A short while ago, I was contacted by a talented drummer by the name of George Sluppick on Instagram. It turns out he had a Ludwig drum from the 1940’s which he wanted to identify and might consider selling. He got the drum from a shop called Lollipop Music in Princeton, WV. They got the drum from a guy who bought it from a pawn shop. So unfortunately, no identity of the original owner. I was still determined to find out more…
Read more1930-32 Ludwig & Ludwig 6.5 x 15” Peacock Pearl Super-Sensitive Snare Drum
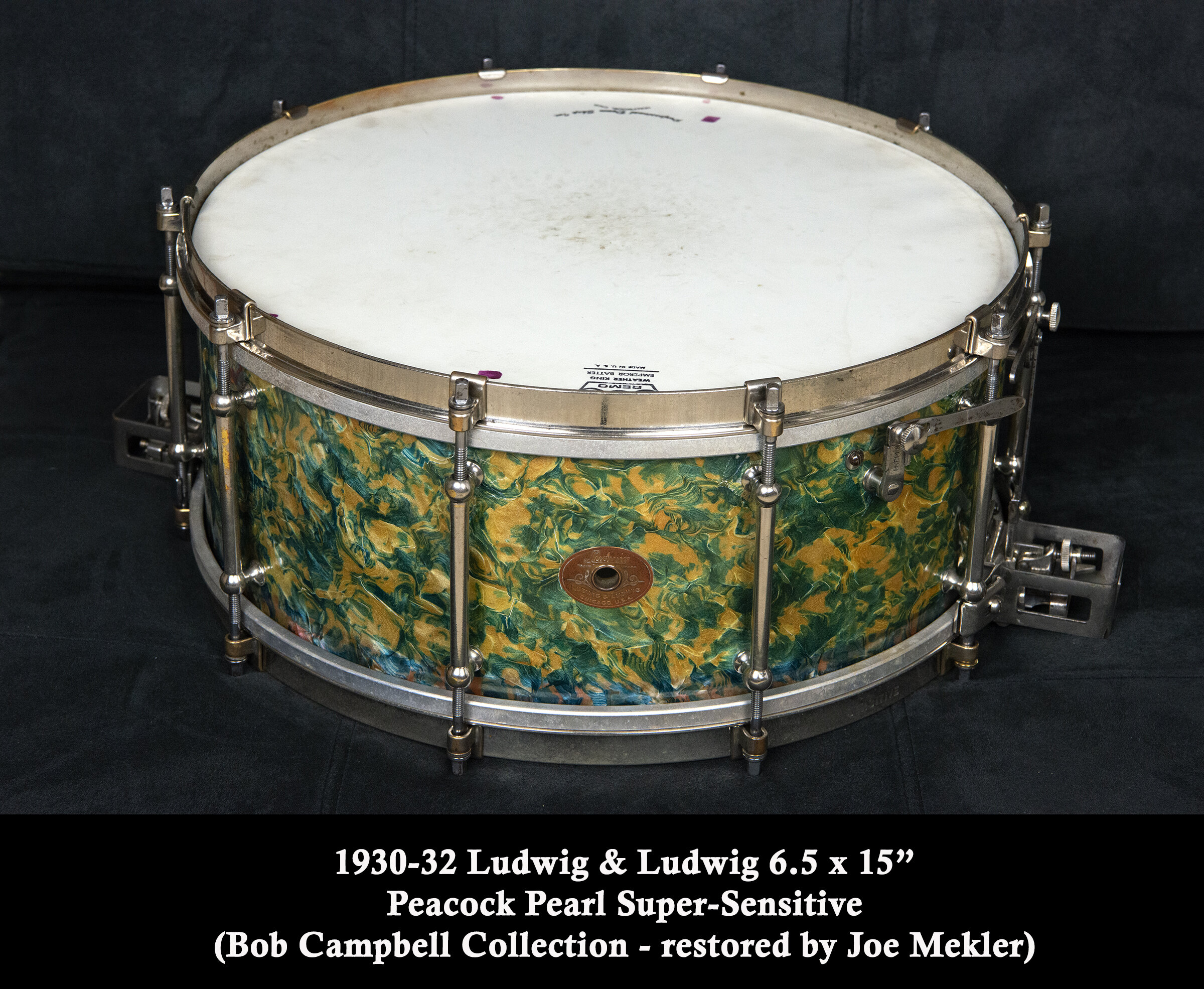
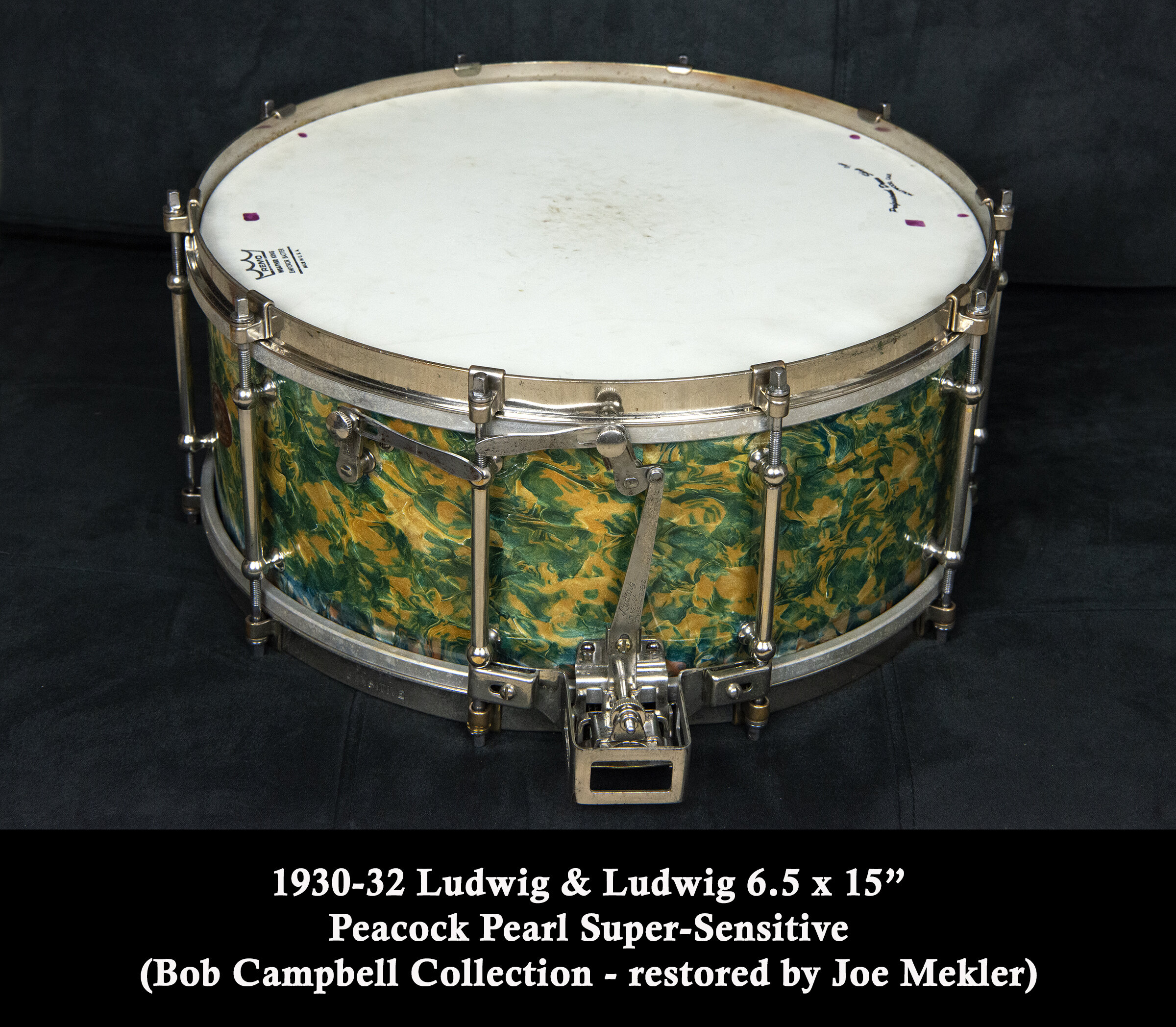
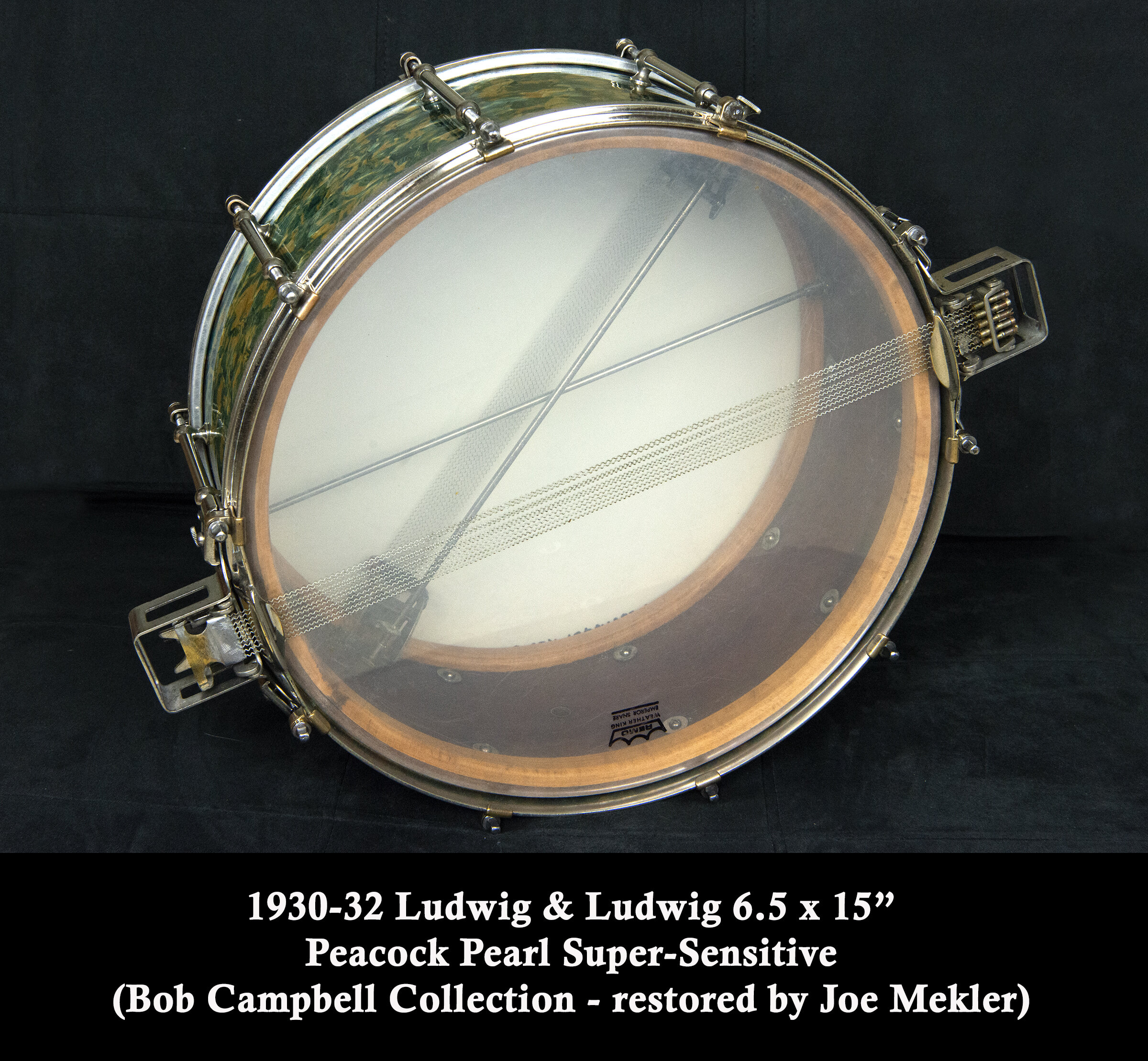
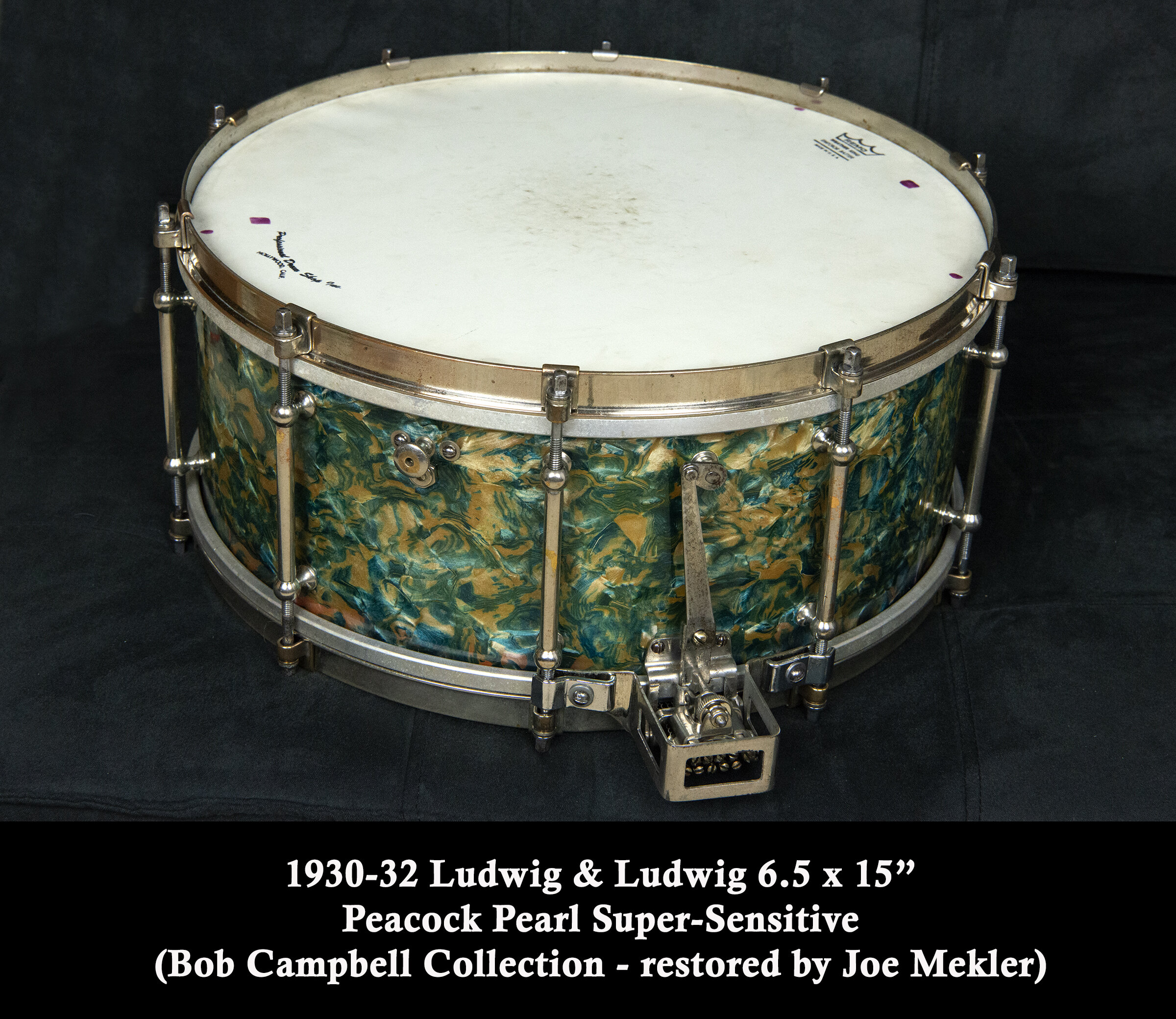
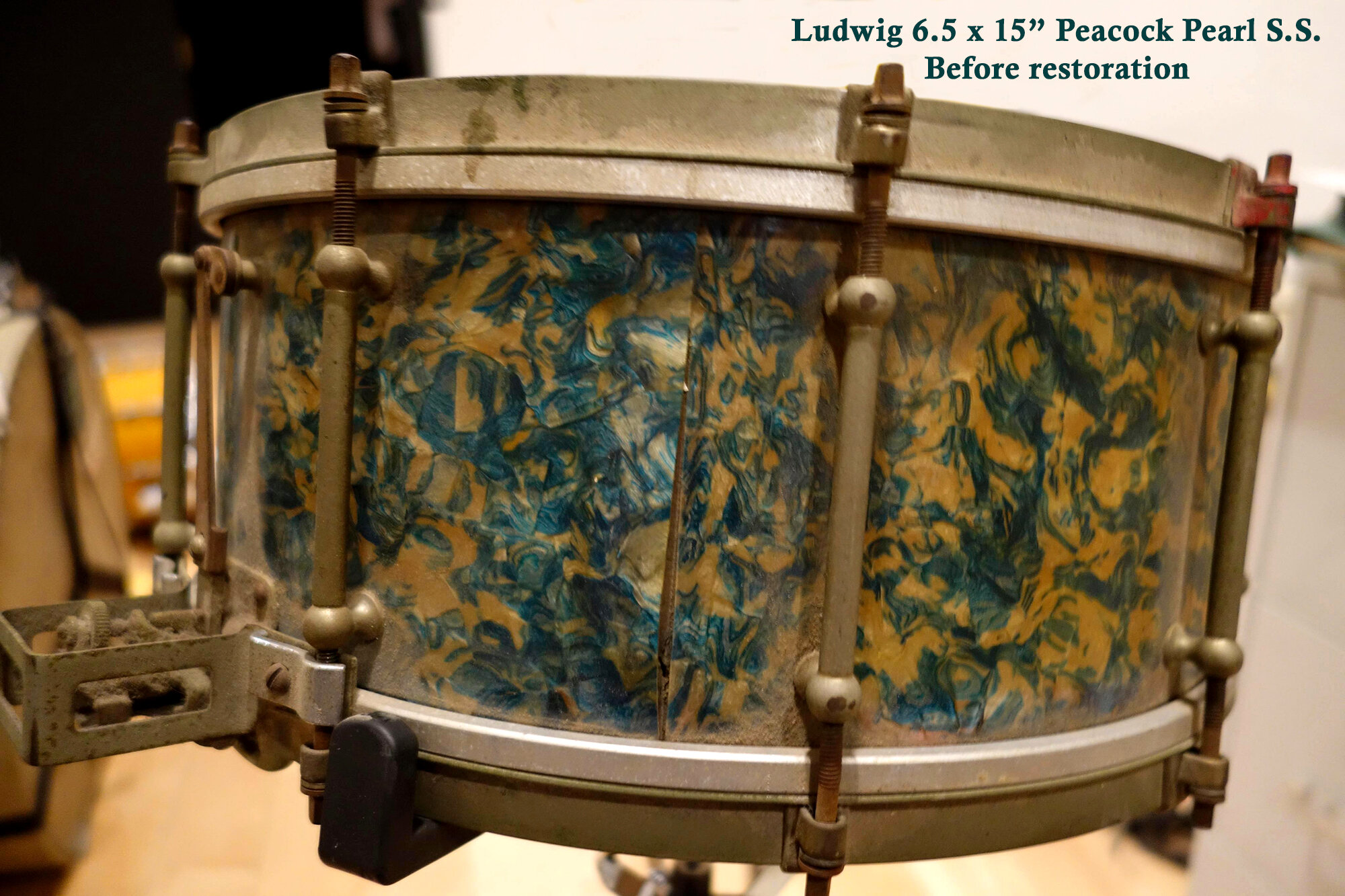
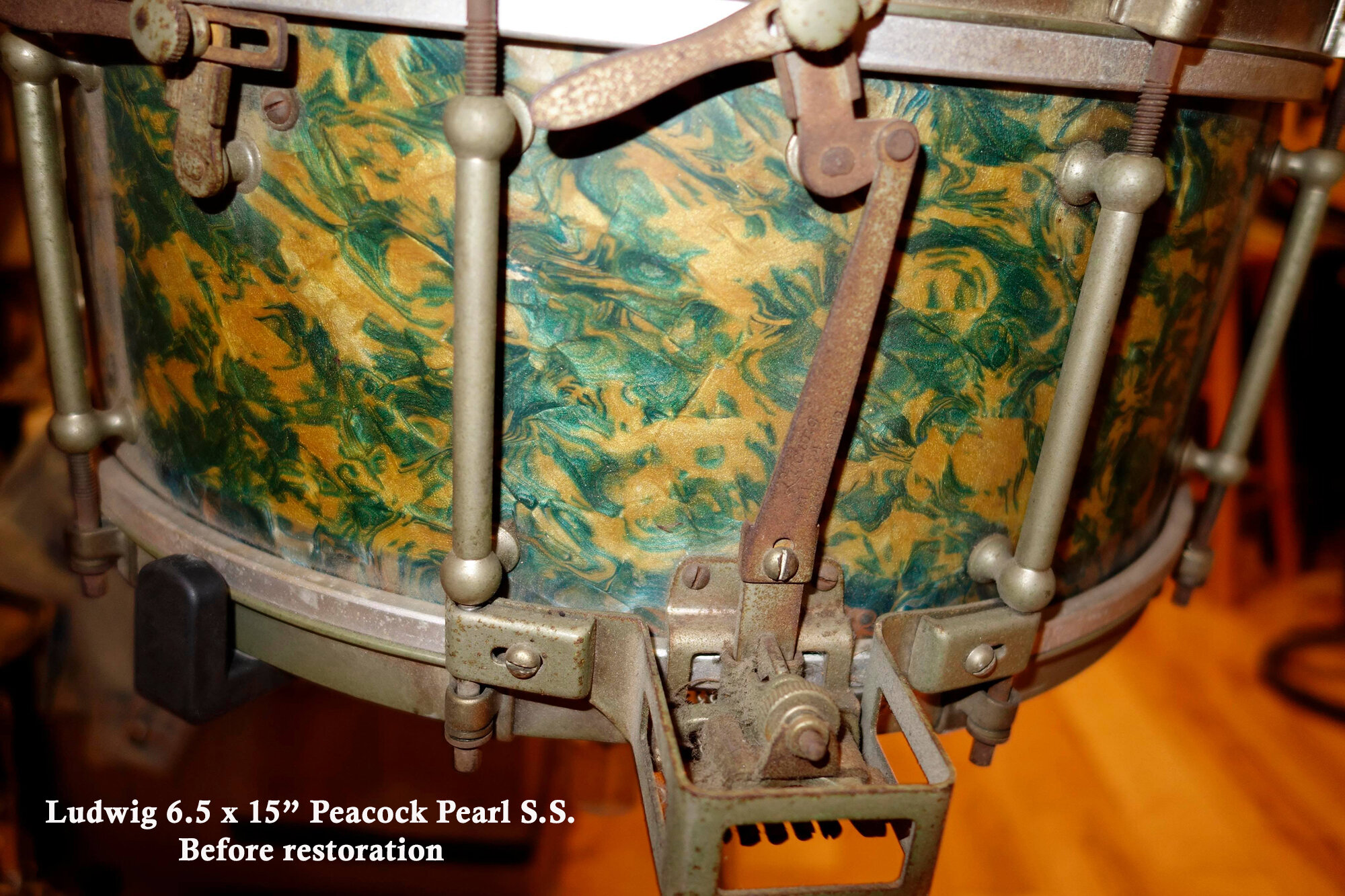
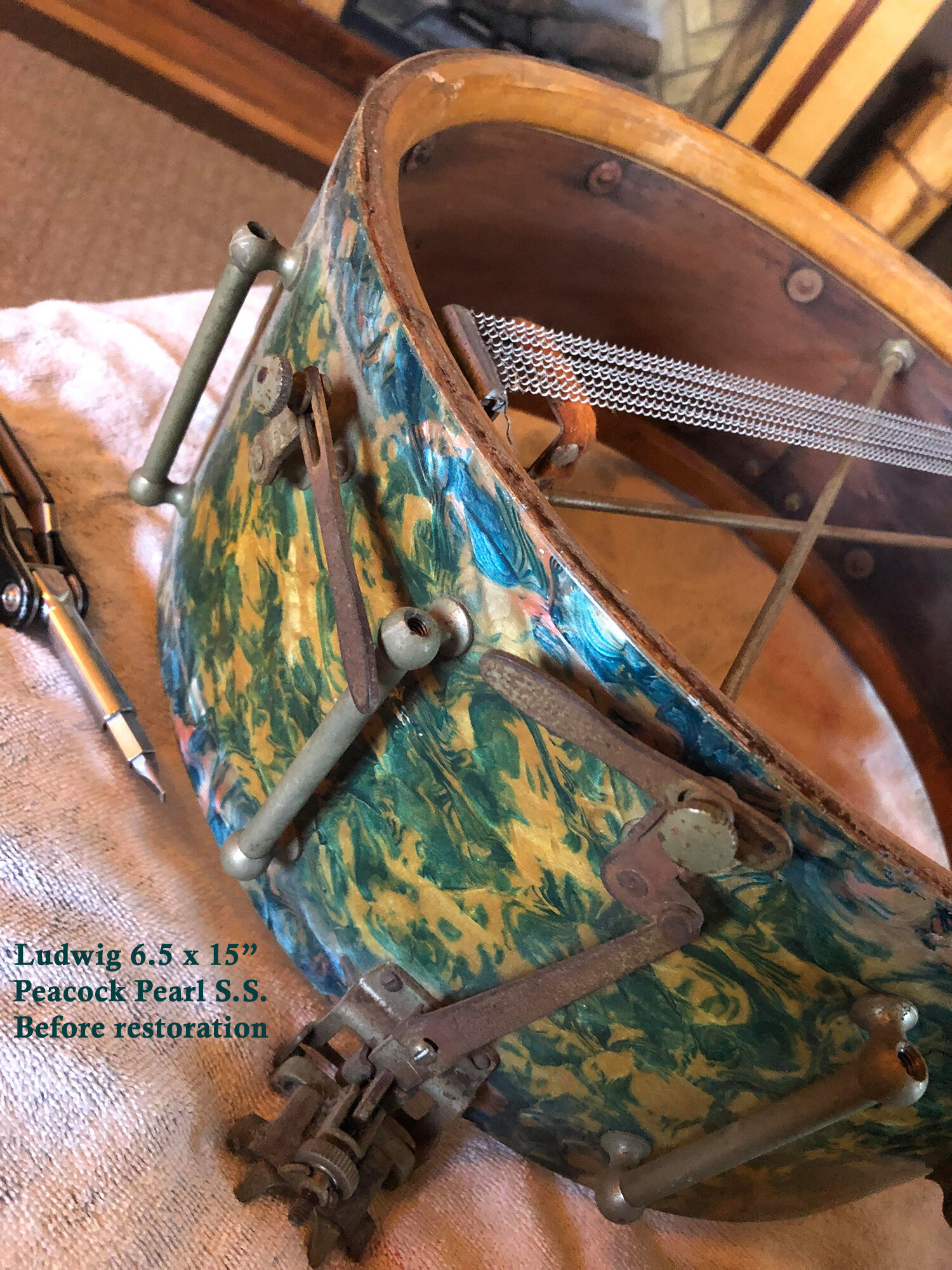
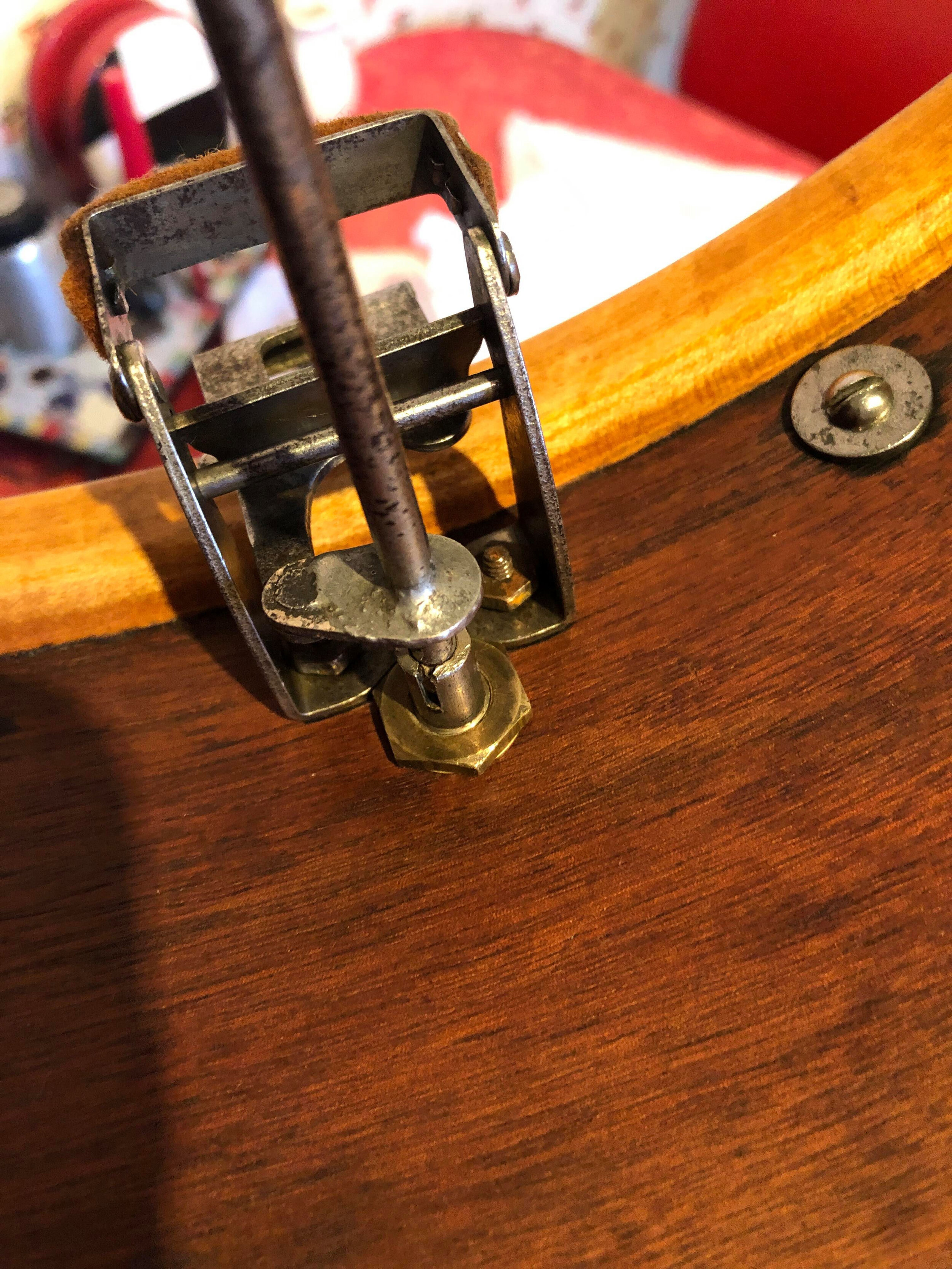
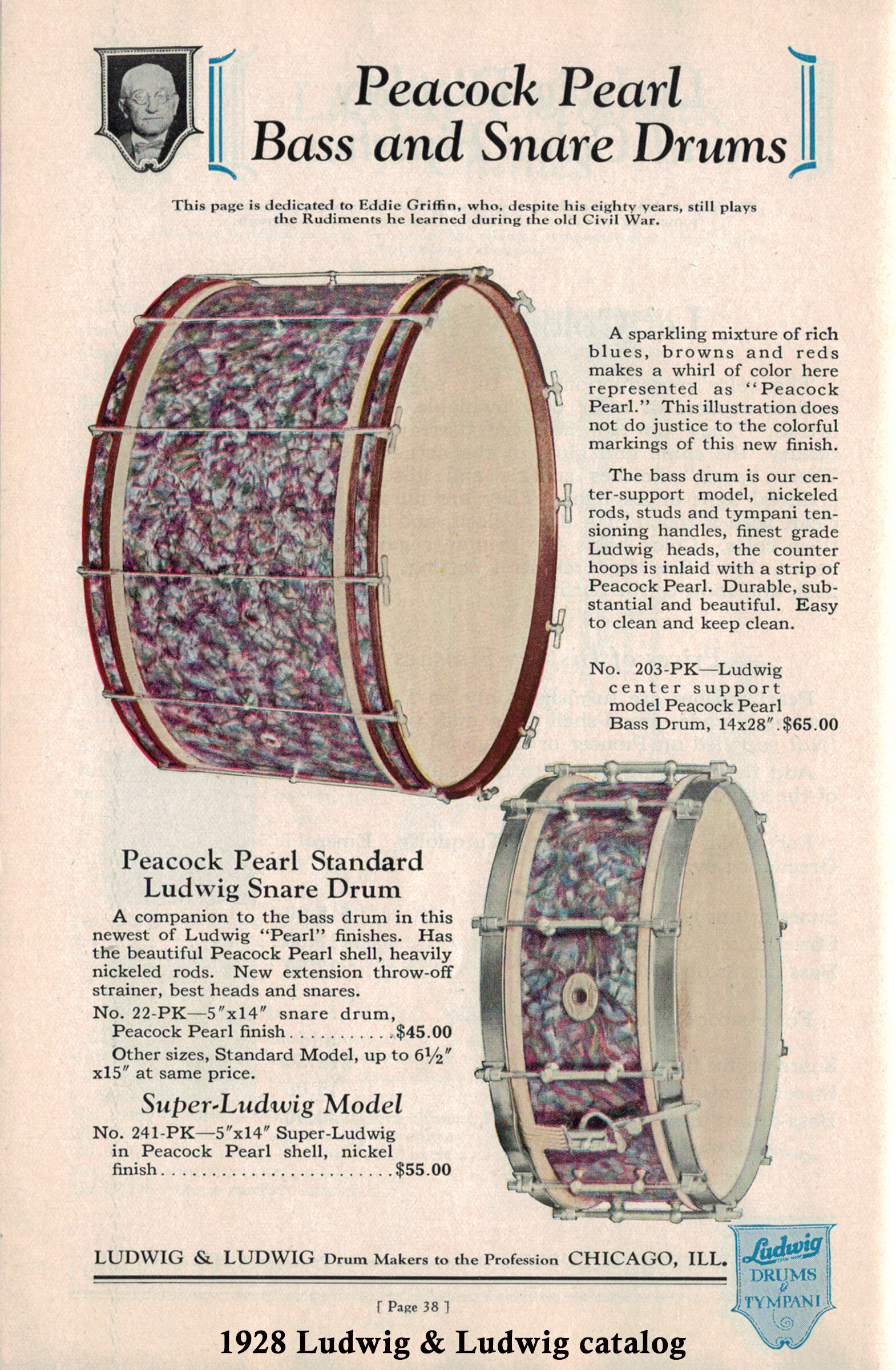
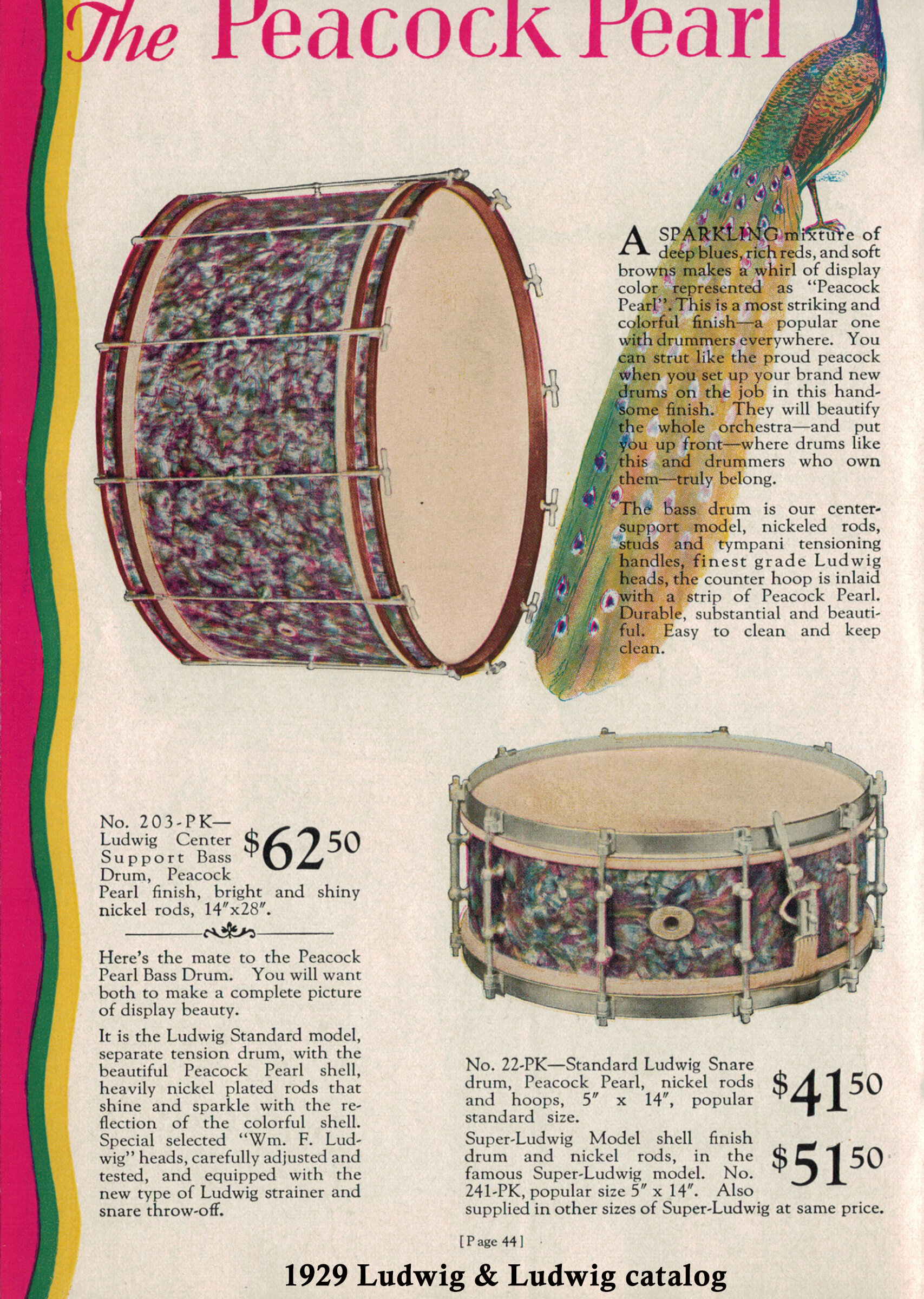
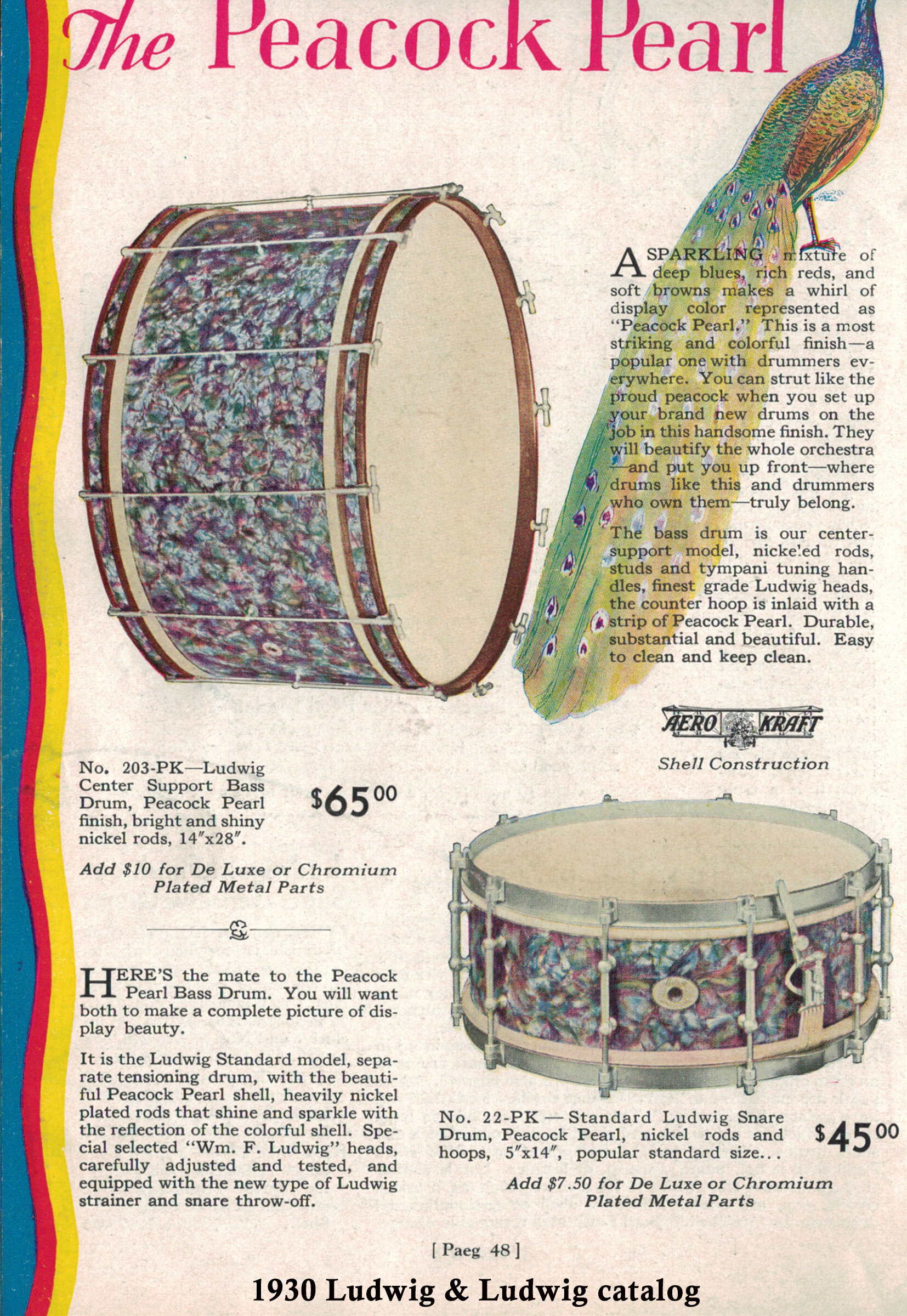
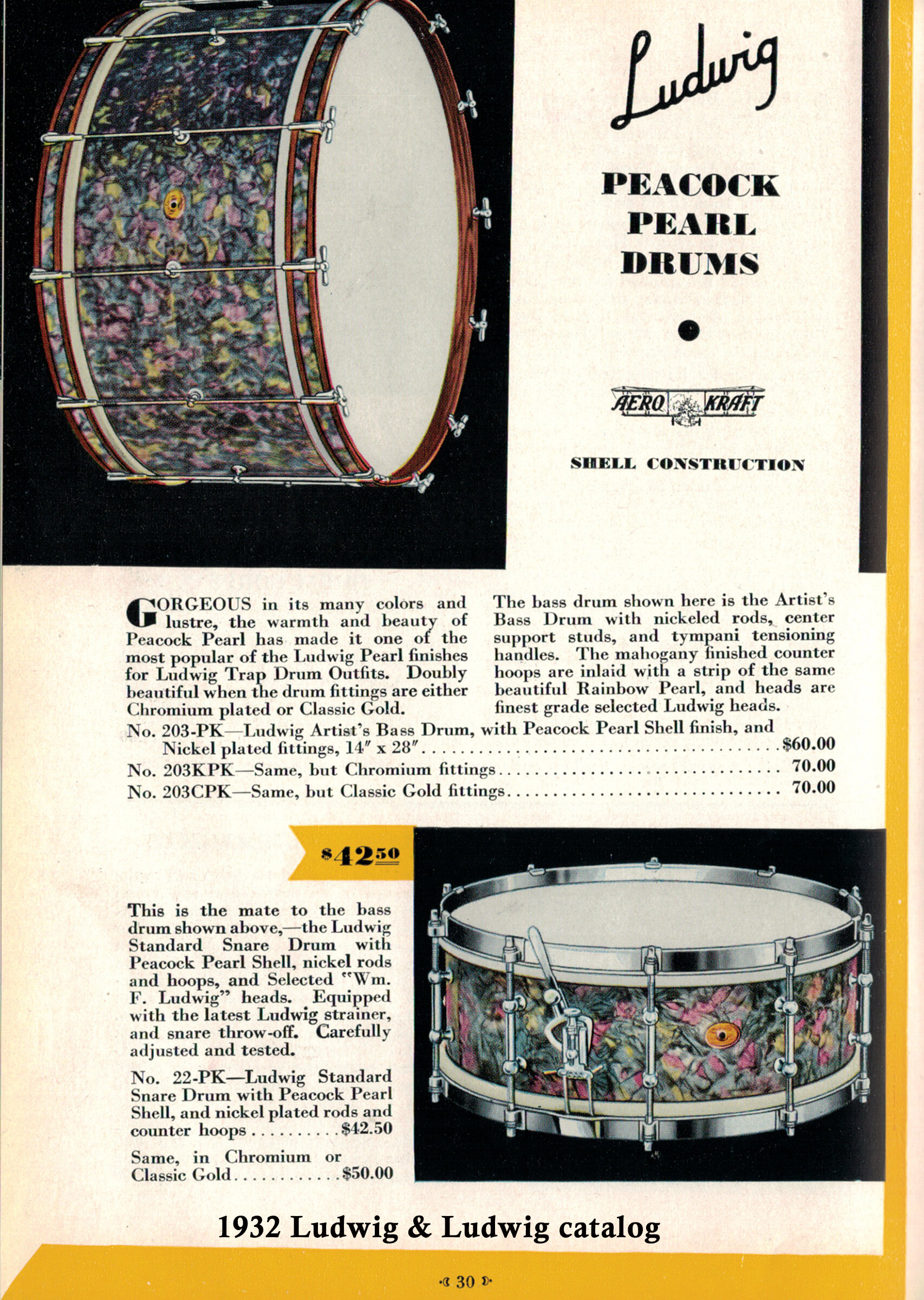
I now own several Ludwig Peacock Pearl snares, but all are 5 x 14”. In late 2020, I found out that Paul “Jamo” Jamieson was thinking of retiring and paring down his drum collection. Jamo is well known for his many contributions to the music industry as a drum tech and cartage/rental businessman. He has worked with some of the biggest names in the music business and accumulated some amazing drums along the way. In one of our many engaging conversations, Jamo mentioned that he had some cool vintage drums that I might be interested in. One of these was a 6.5 x 15” (yes, 15”!) Ludwig Super-Sensitive in Peacock Pearl.
Read moreCirca 1928 Leedy 5x14 Jade Green Pearl Snare Drum
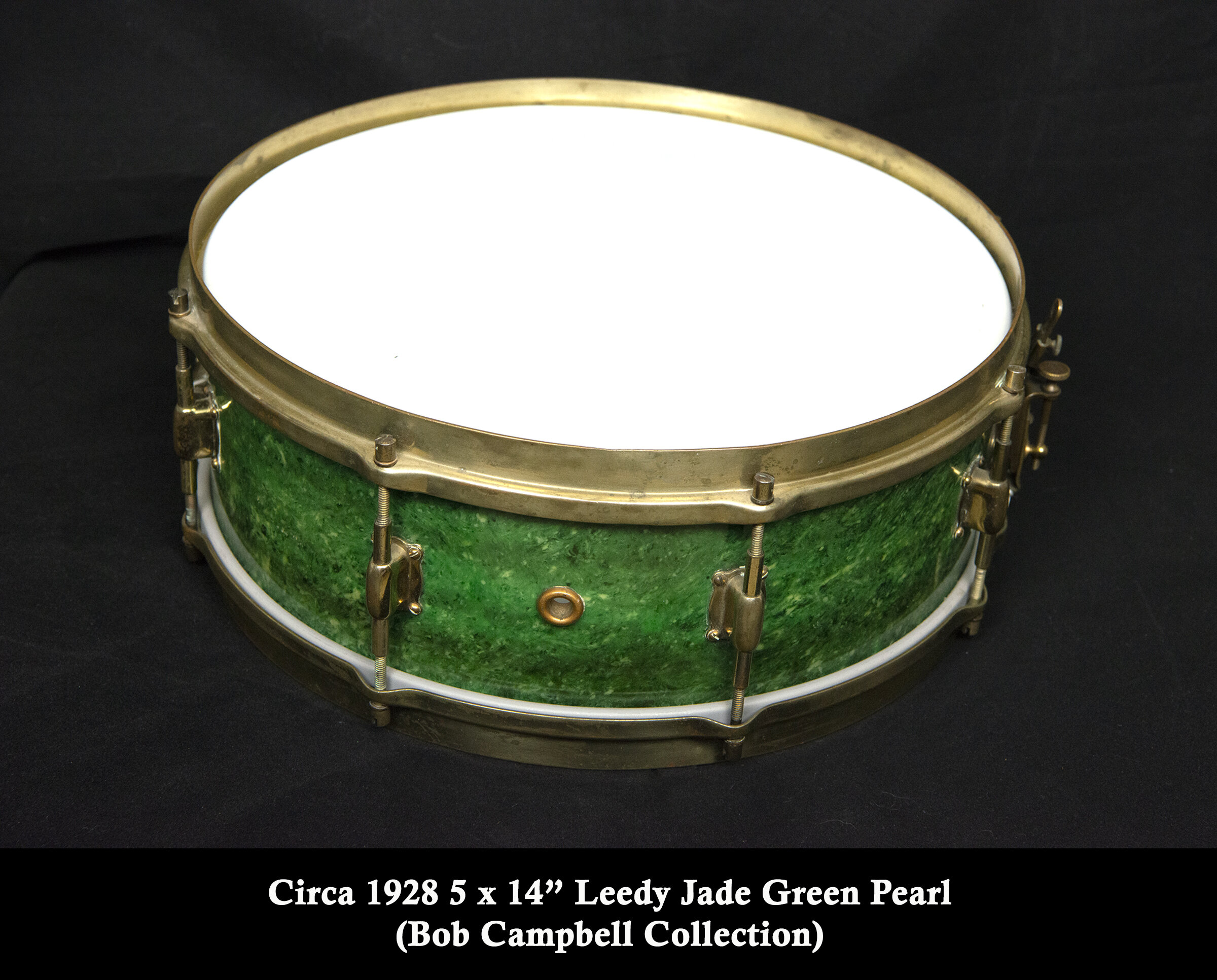
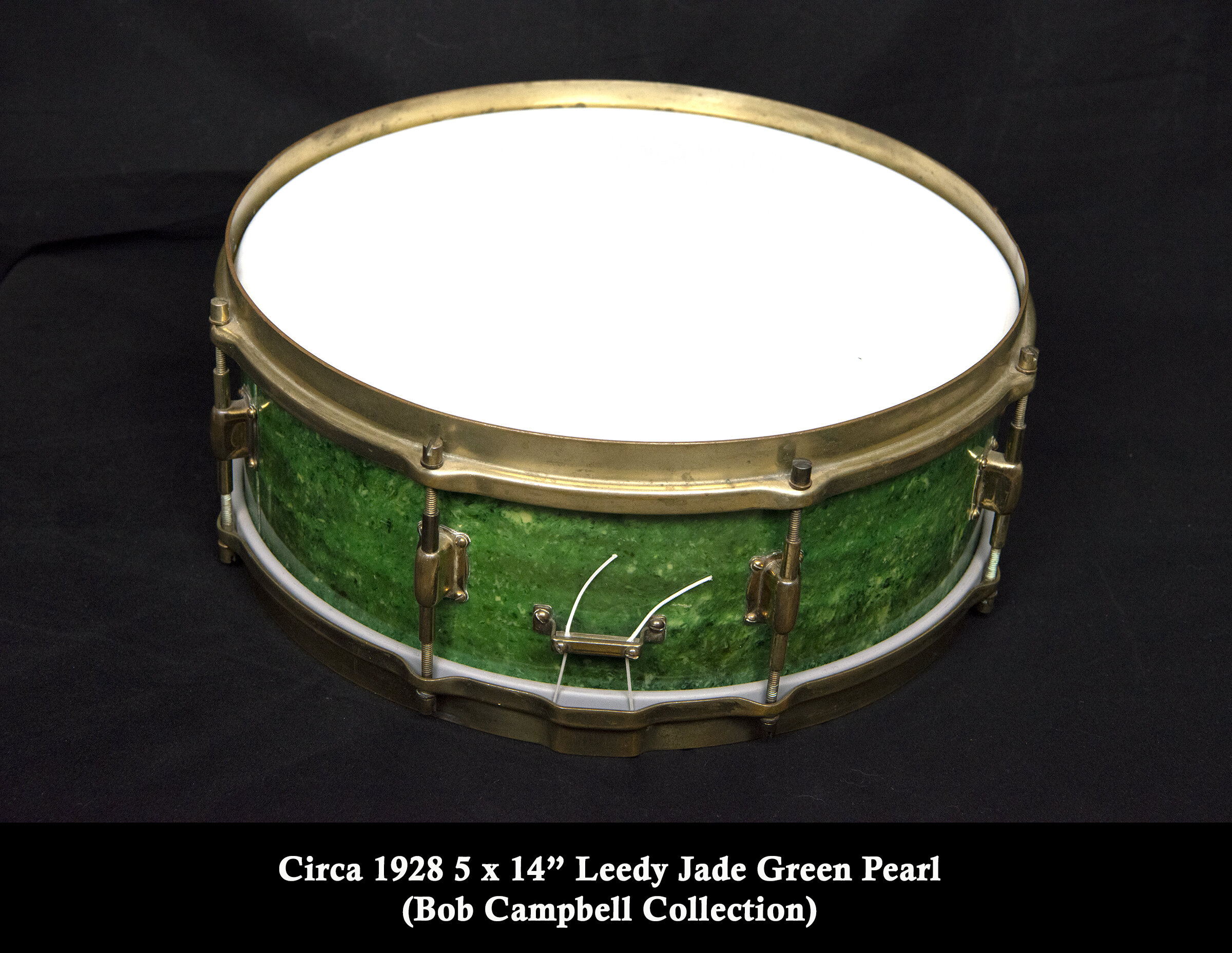
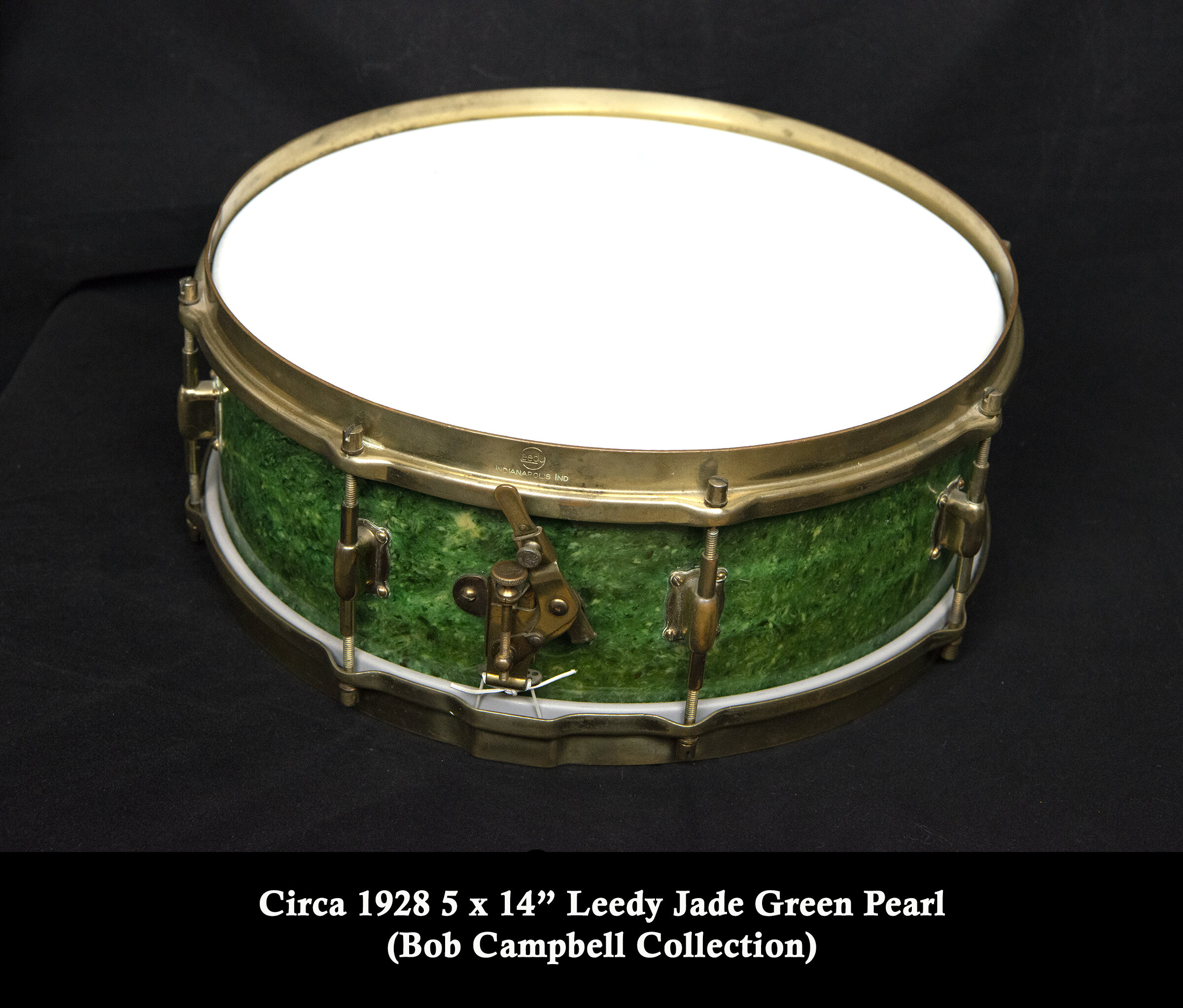
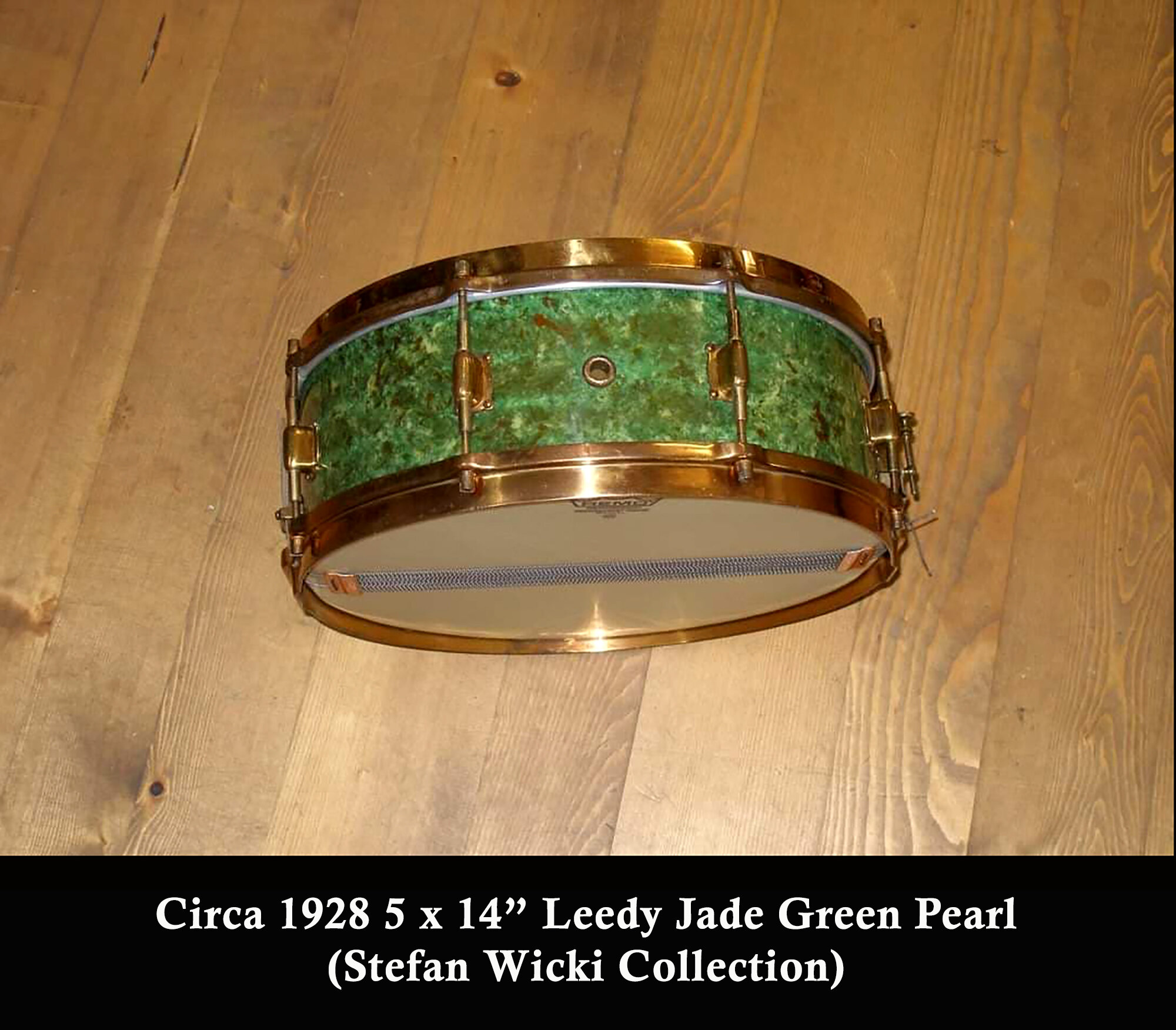
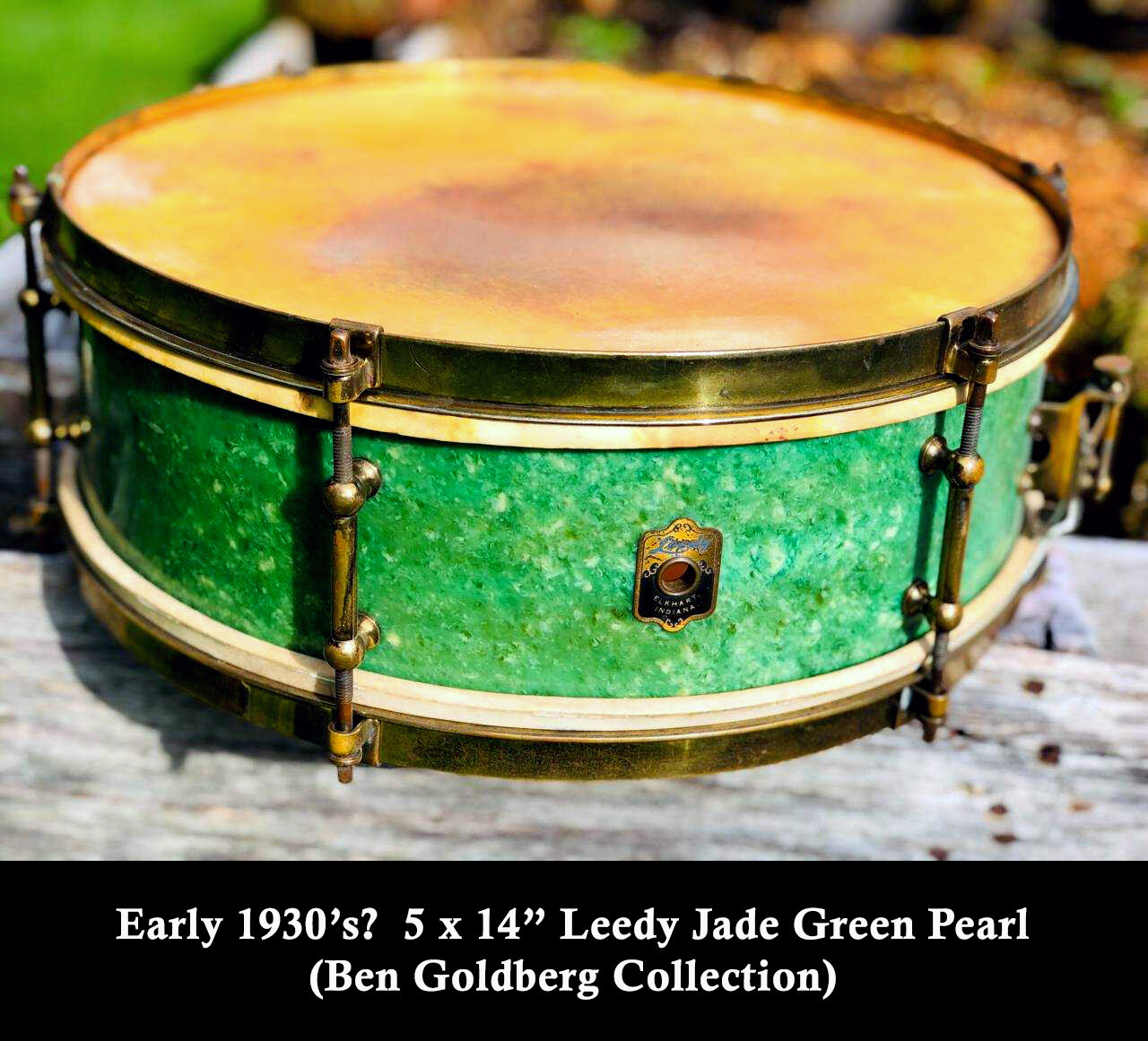
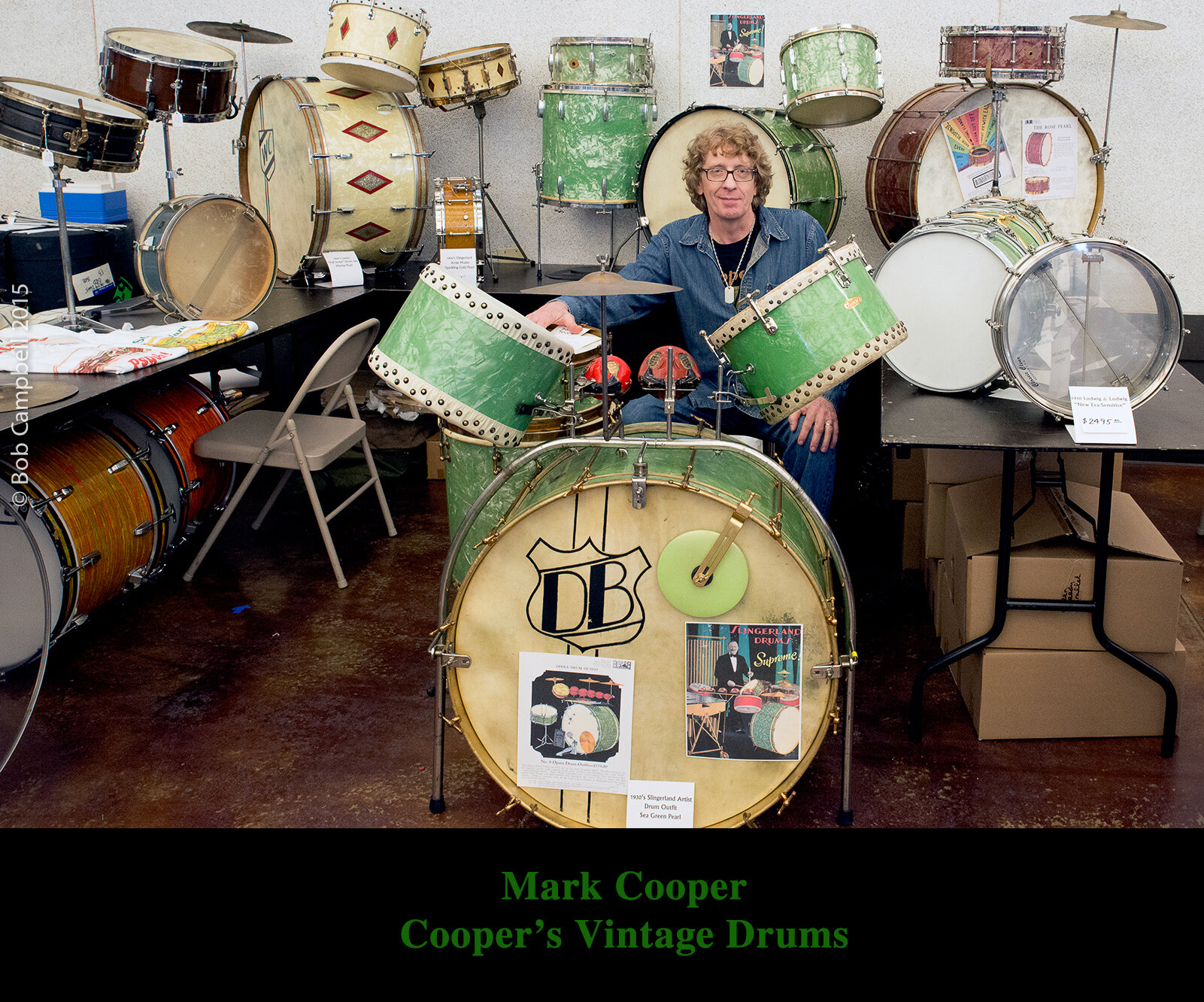
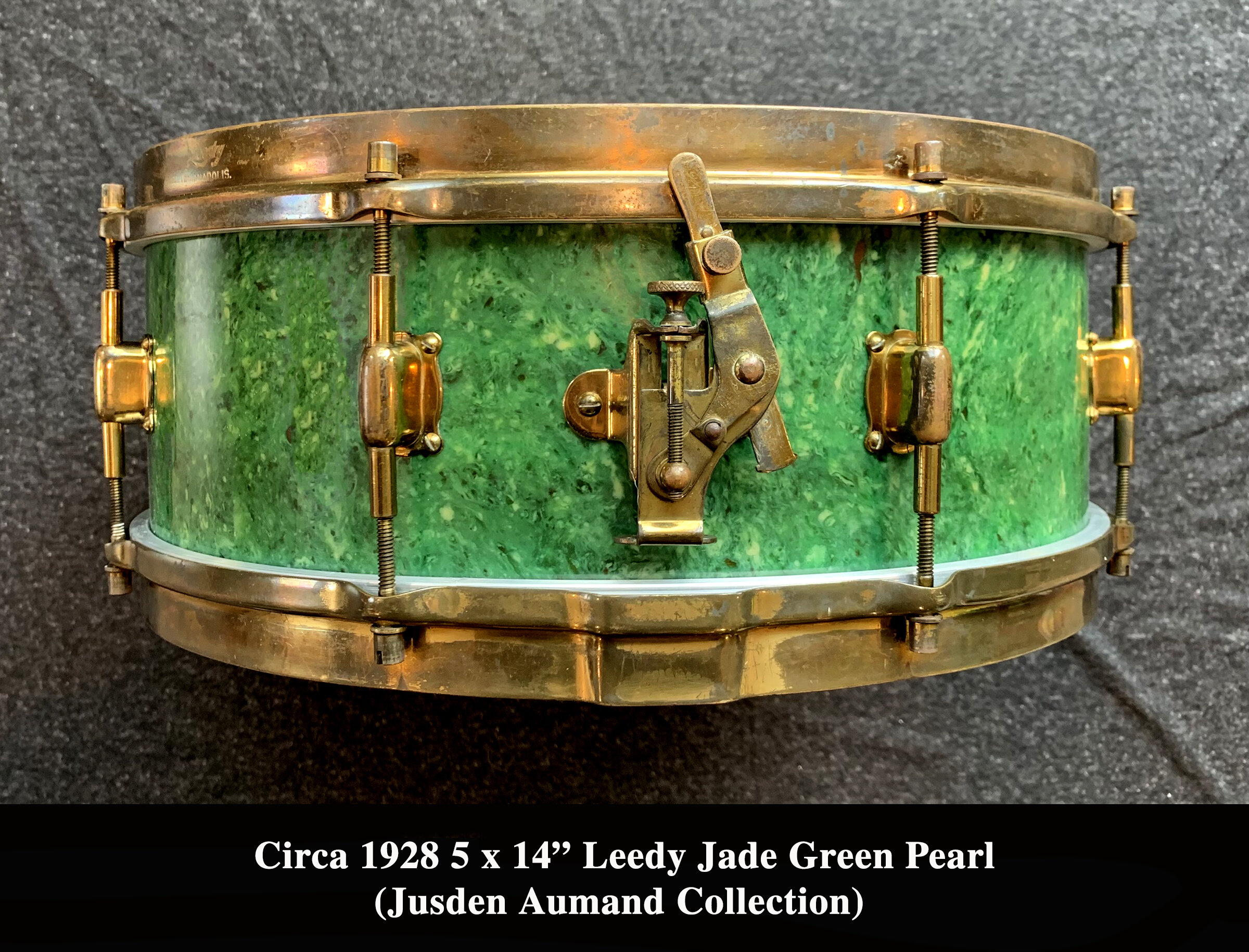
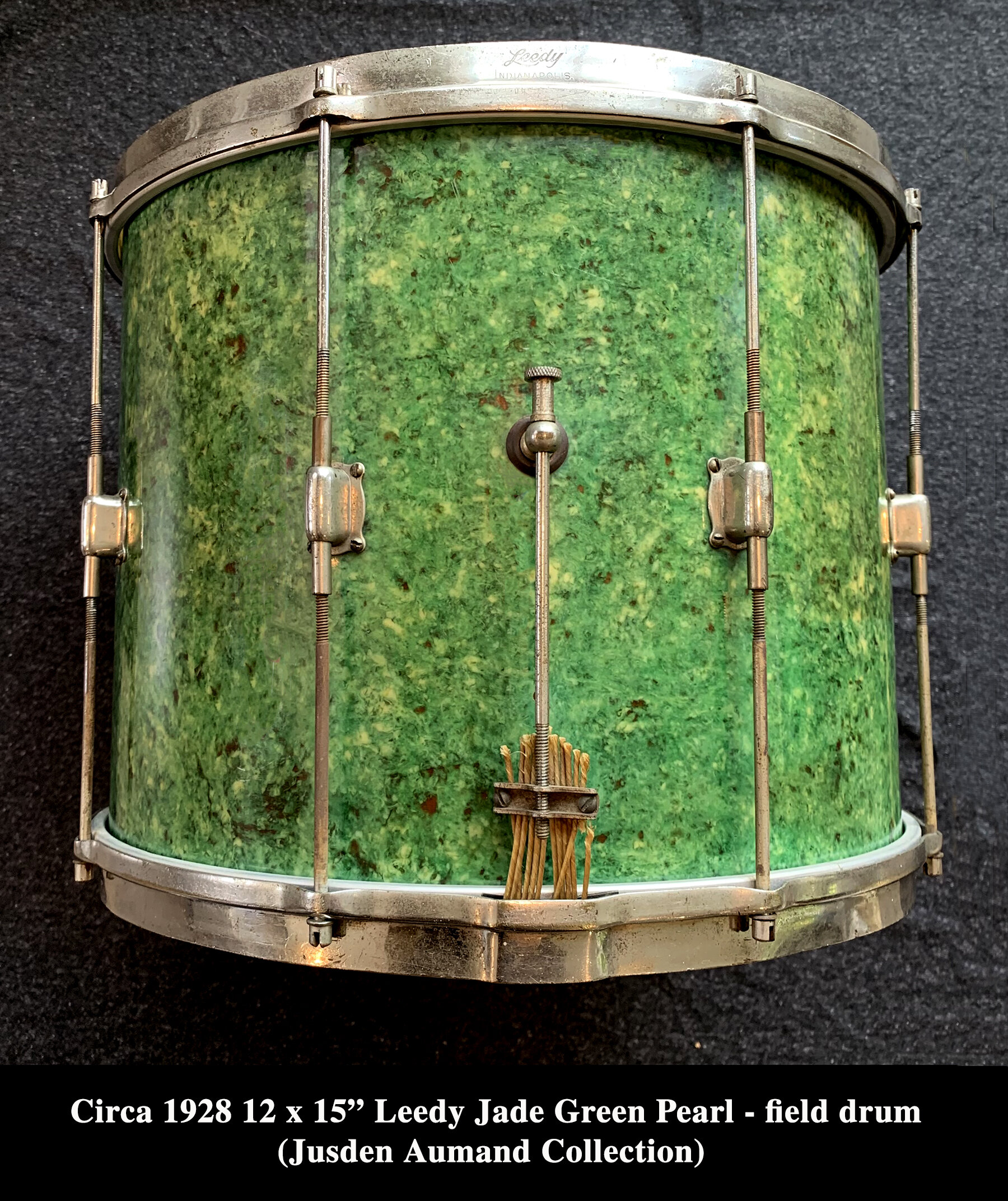
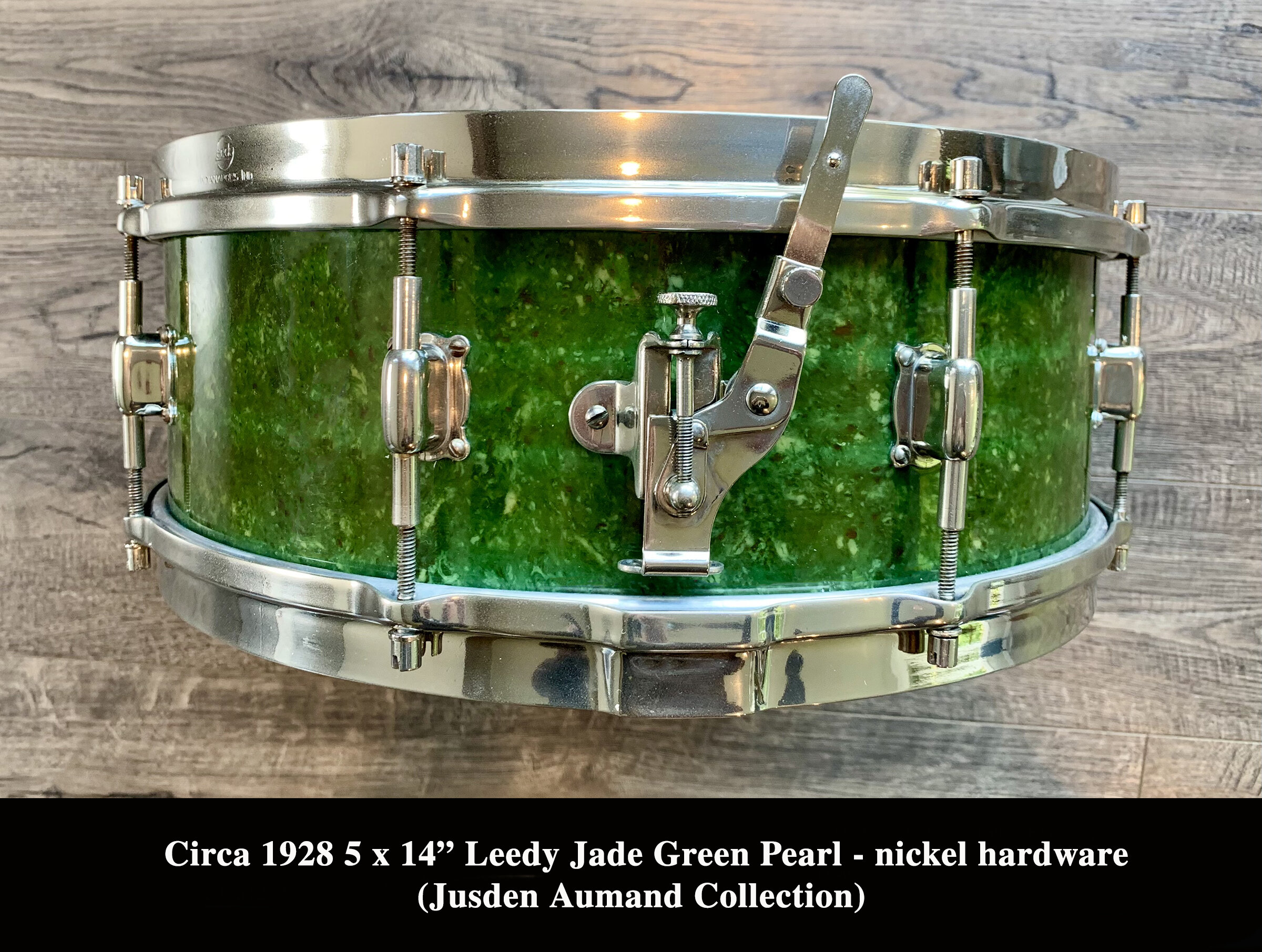
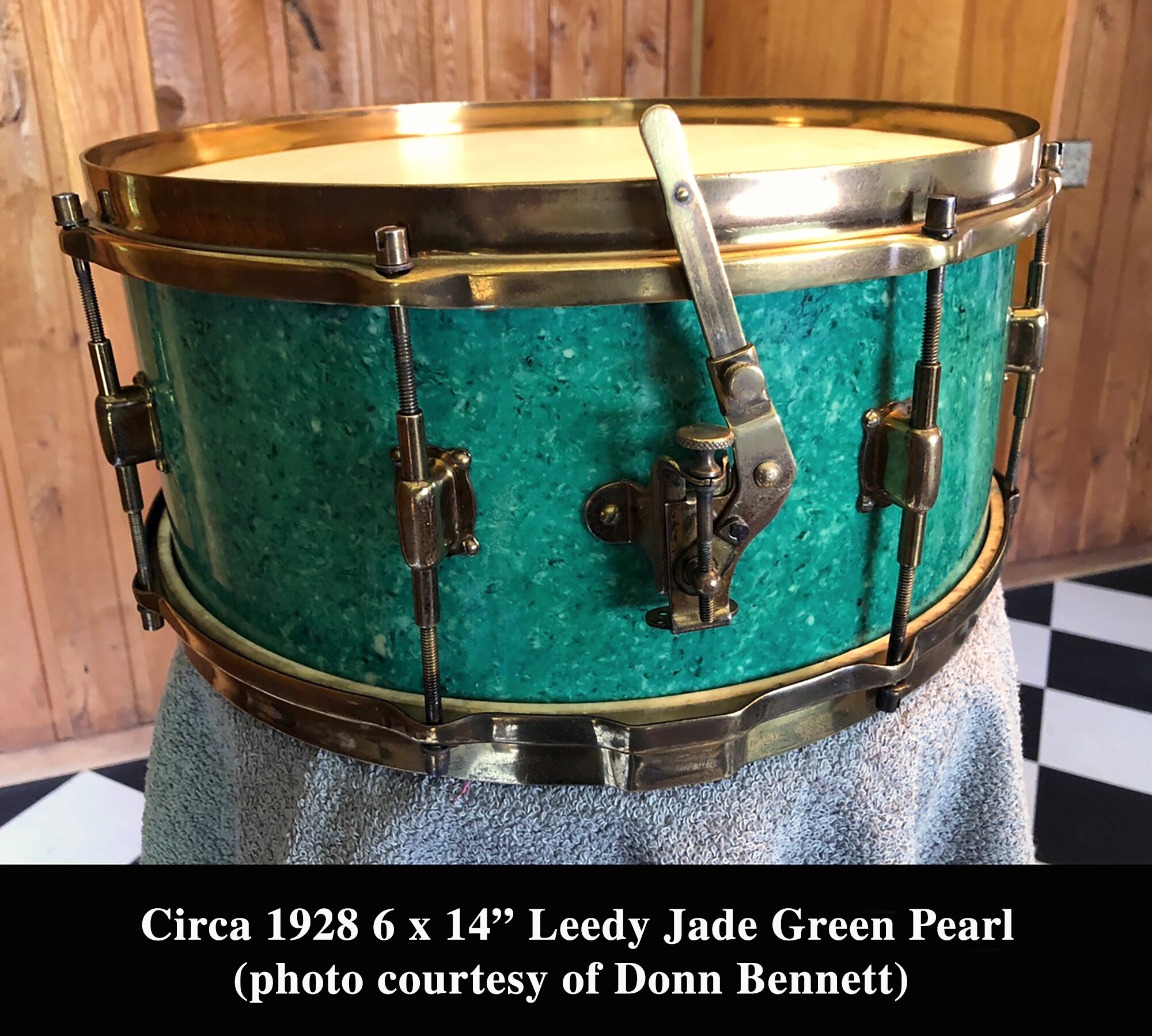
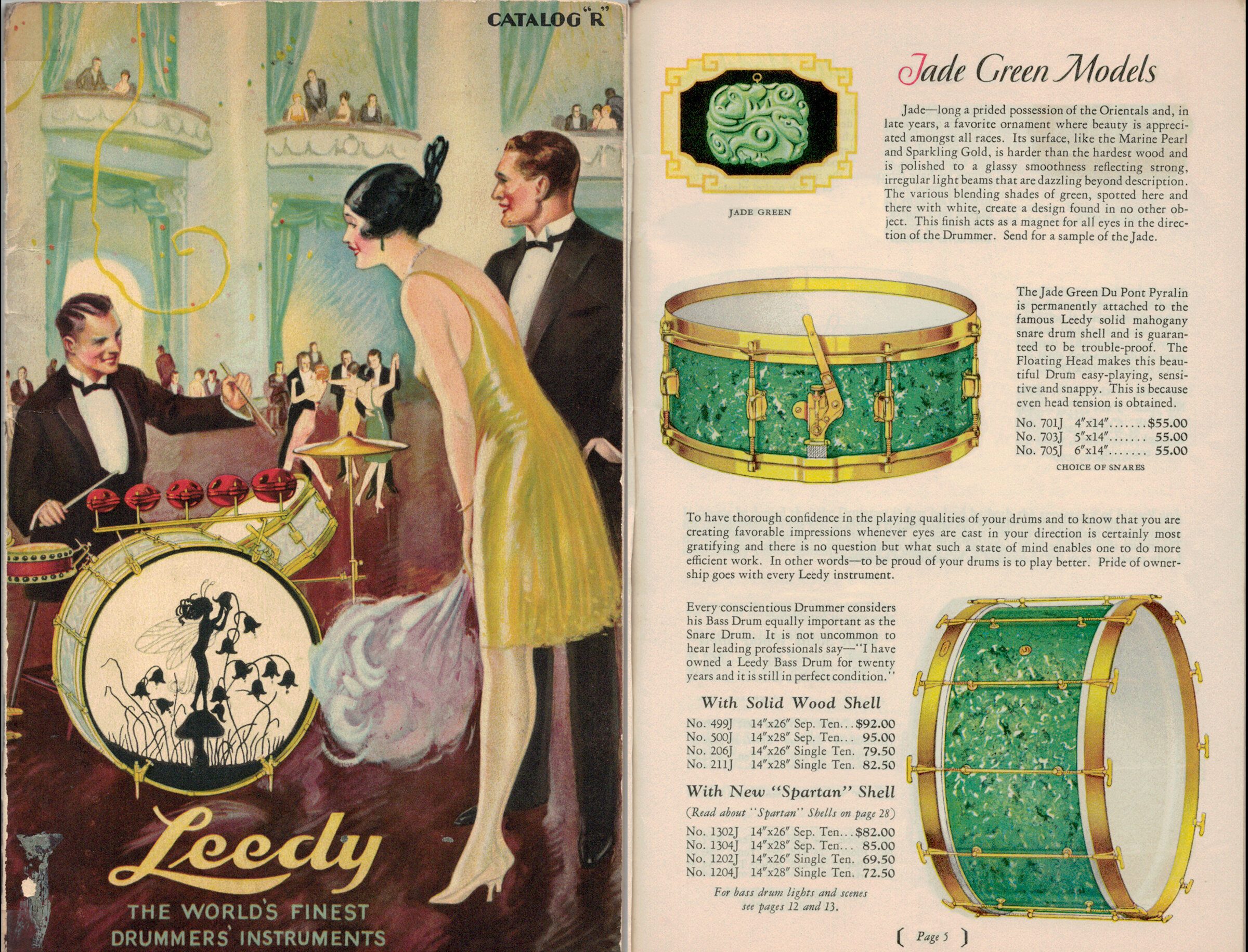
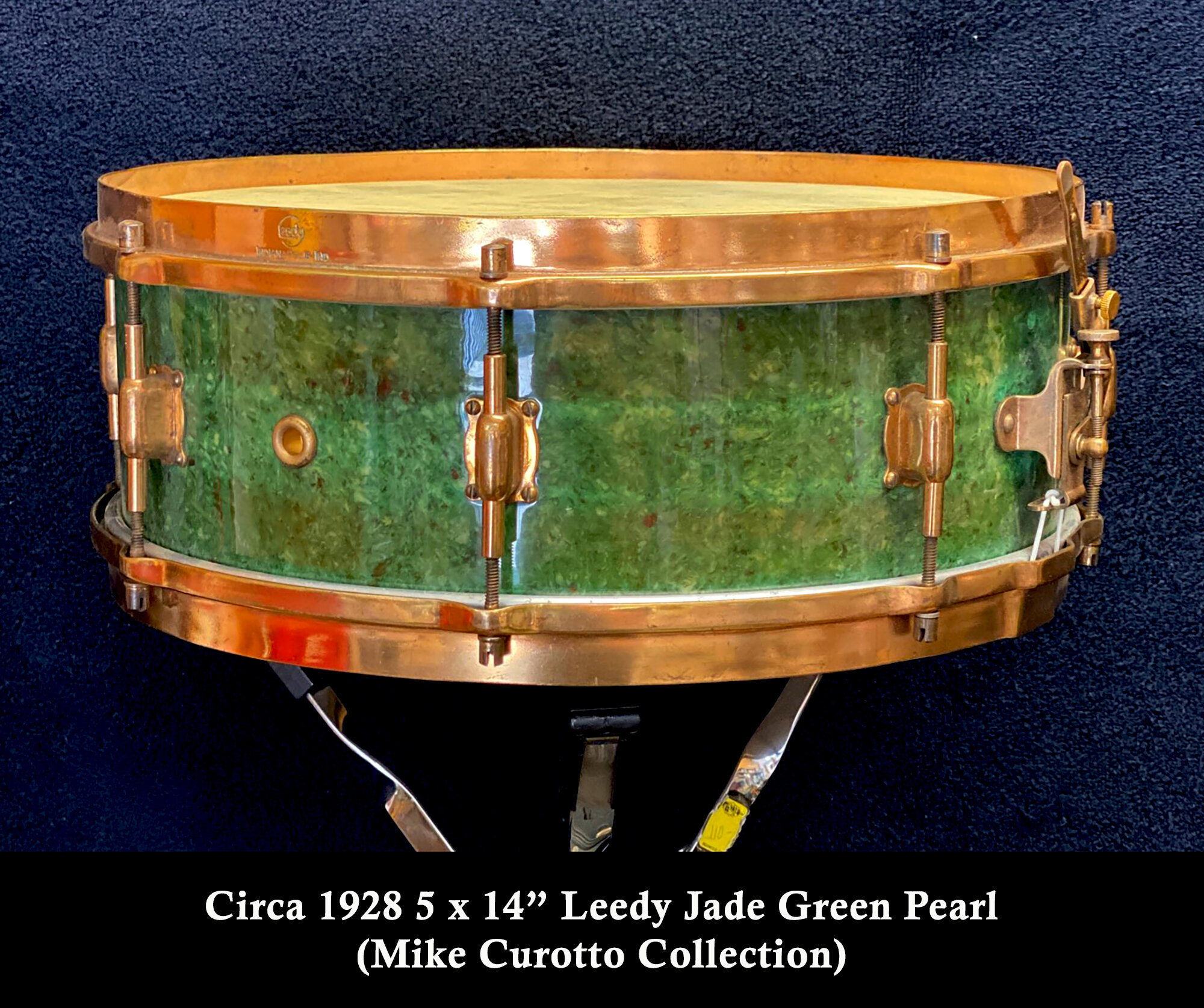
I’d like to start this story by both thanking and blaming Mark Cooper (Coopers Vintage Drums) J. Many years ago, I met Mark at one of the Chicago Drum Shows. He was sharing his fabulous collection of vintage green-wrapped drums from Slingerland and Leedy.
Read moreWFL 7 X 14” Paramount snare drum Circa 1939
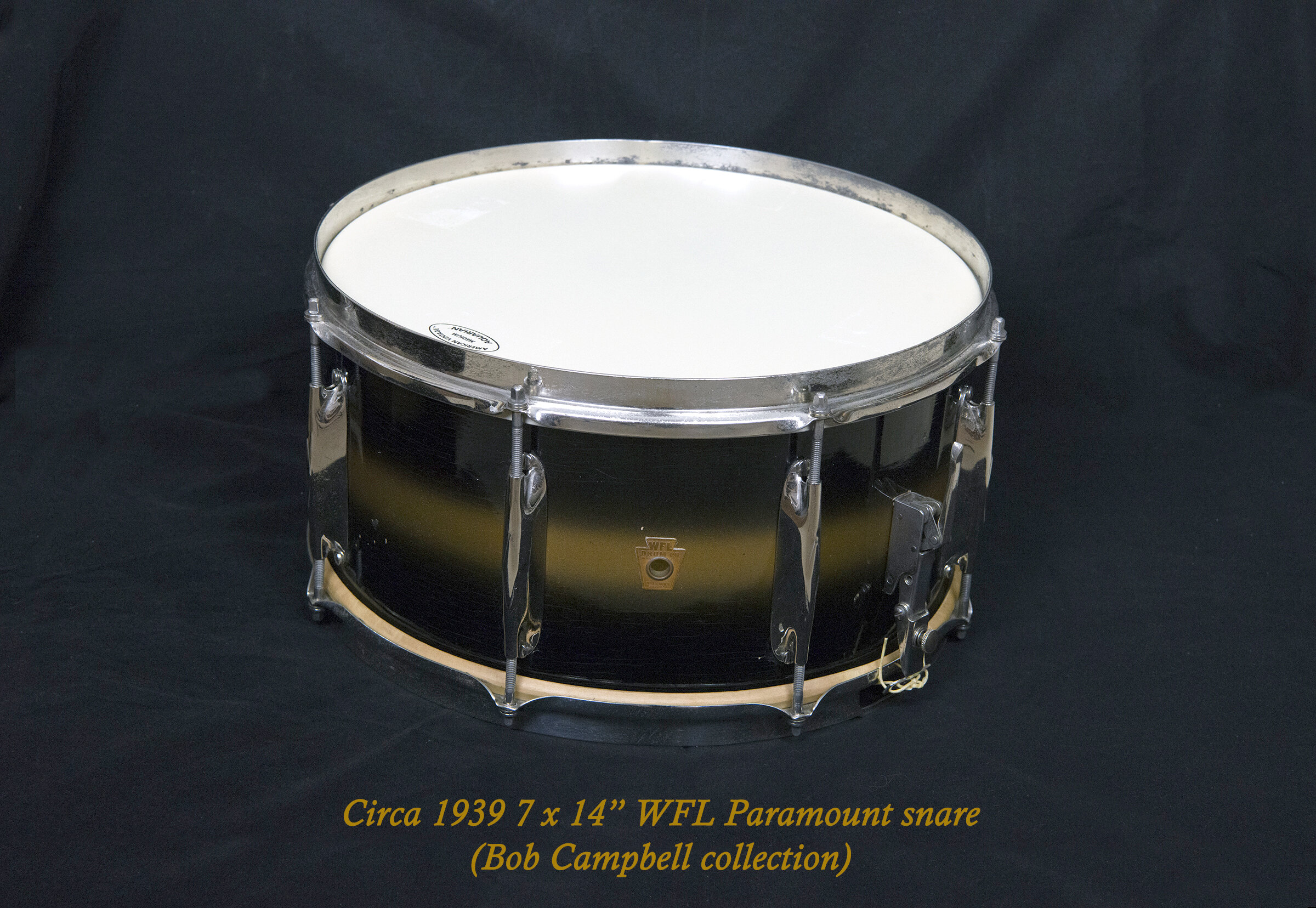
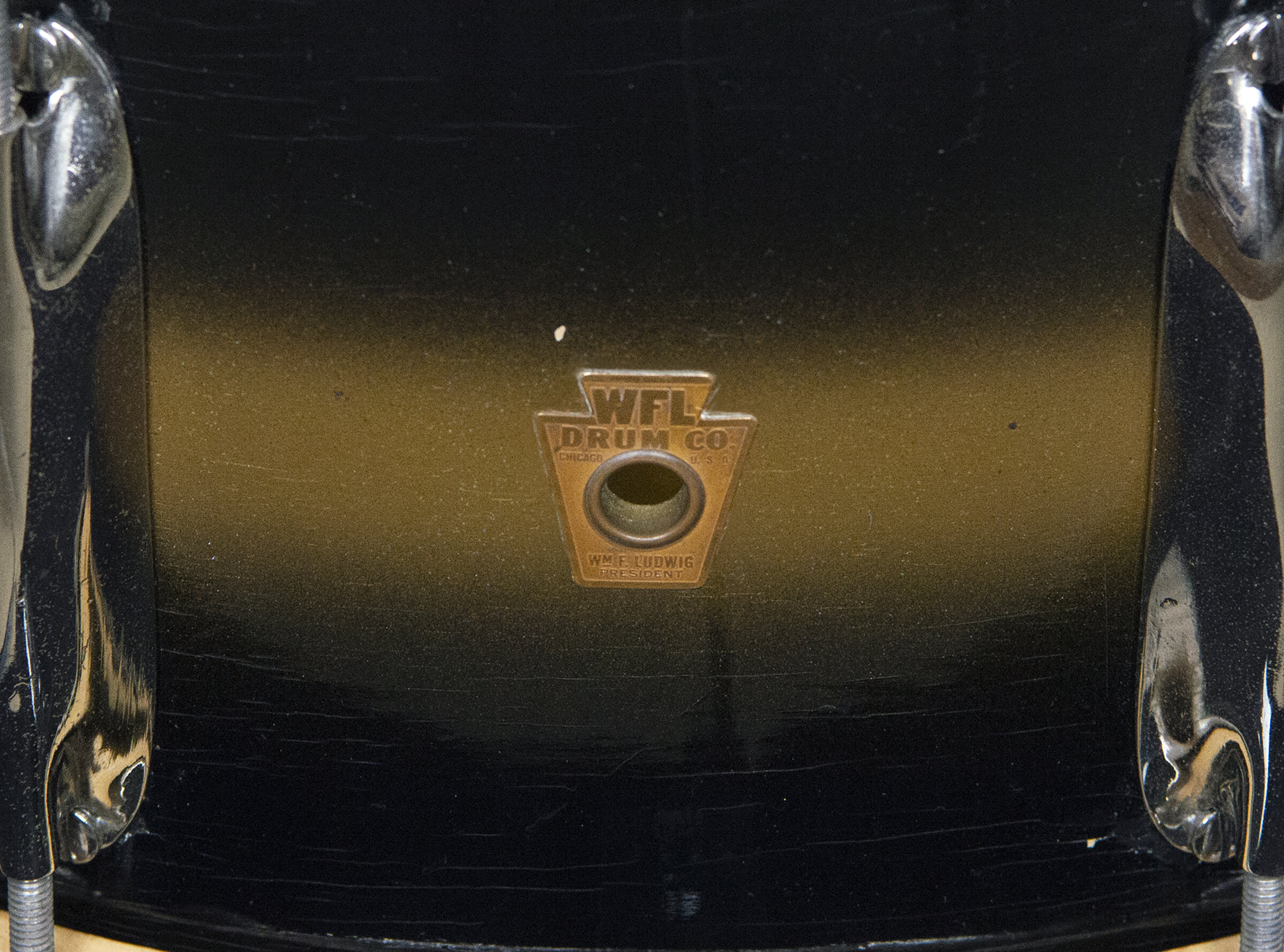
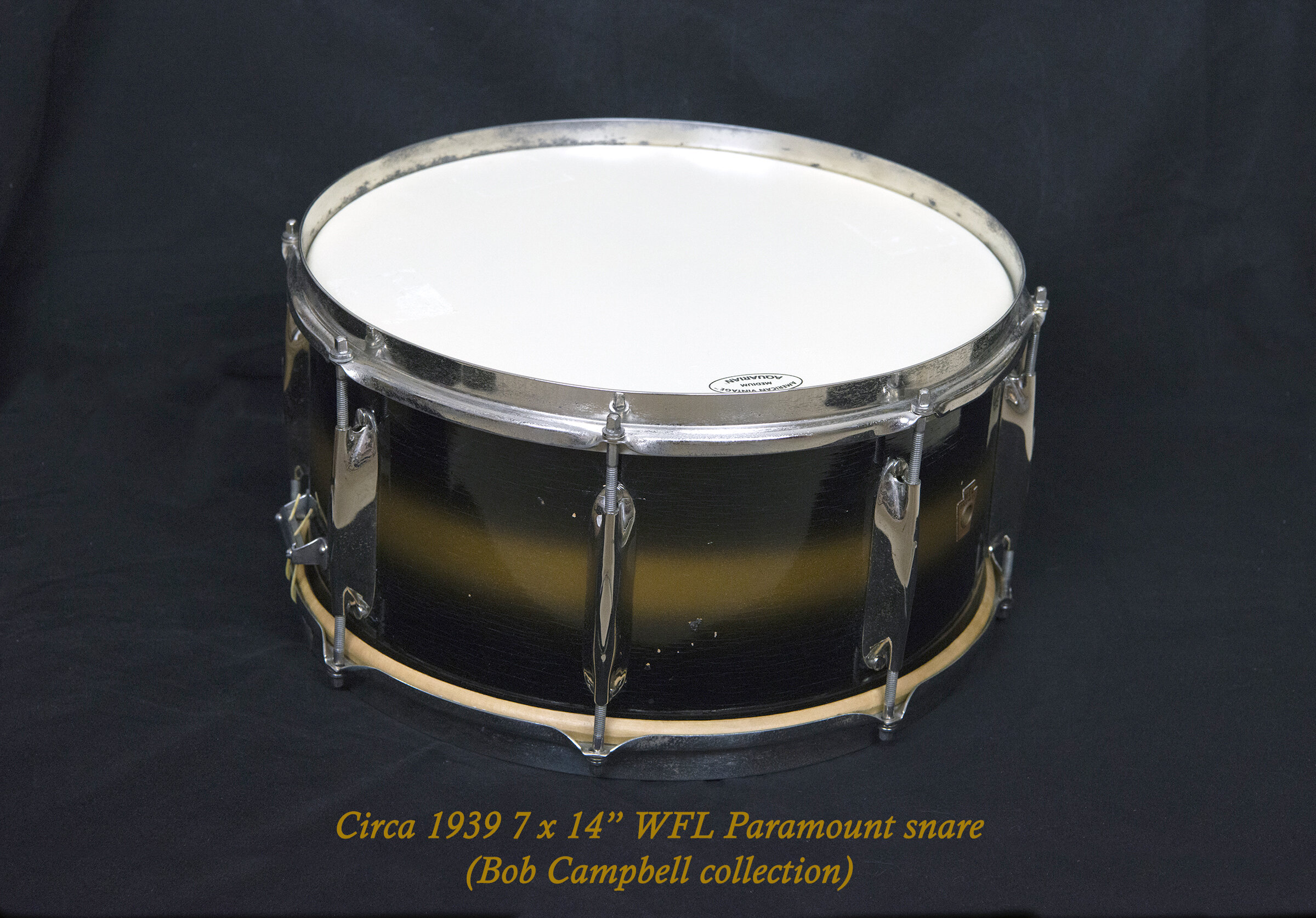
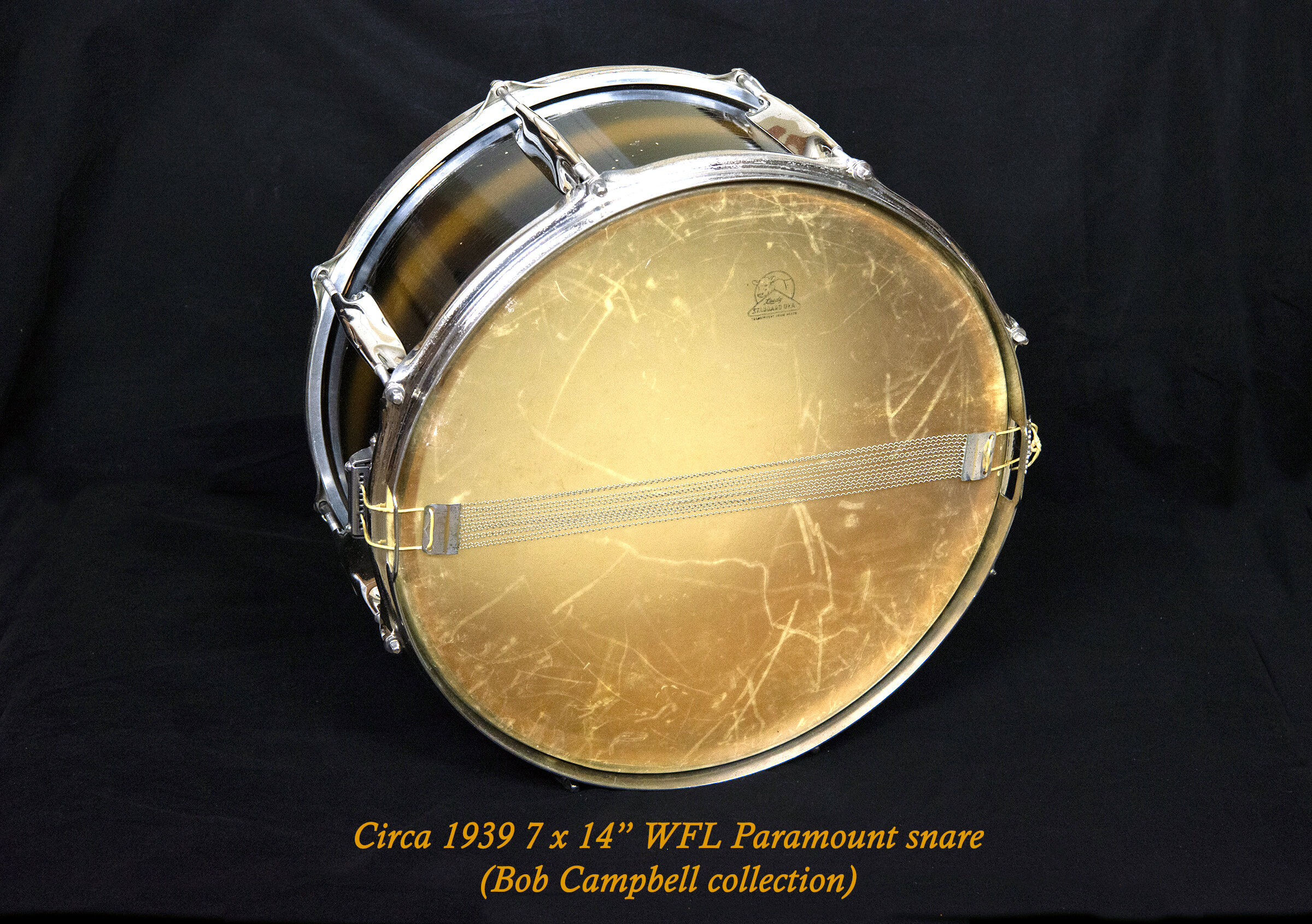
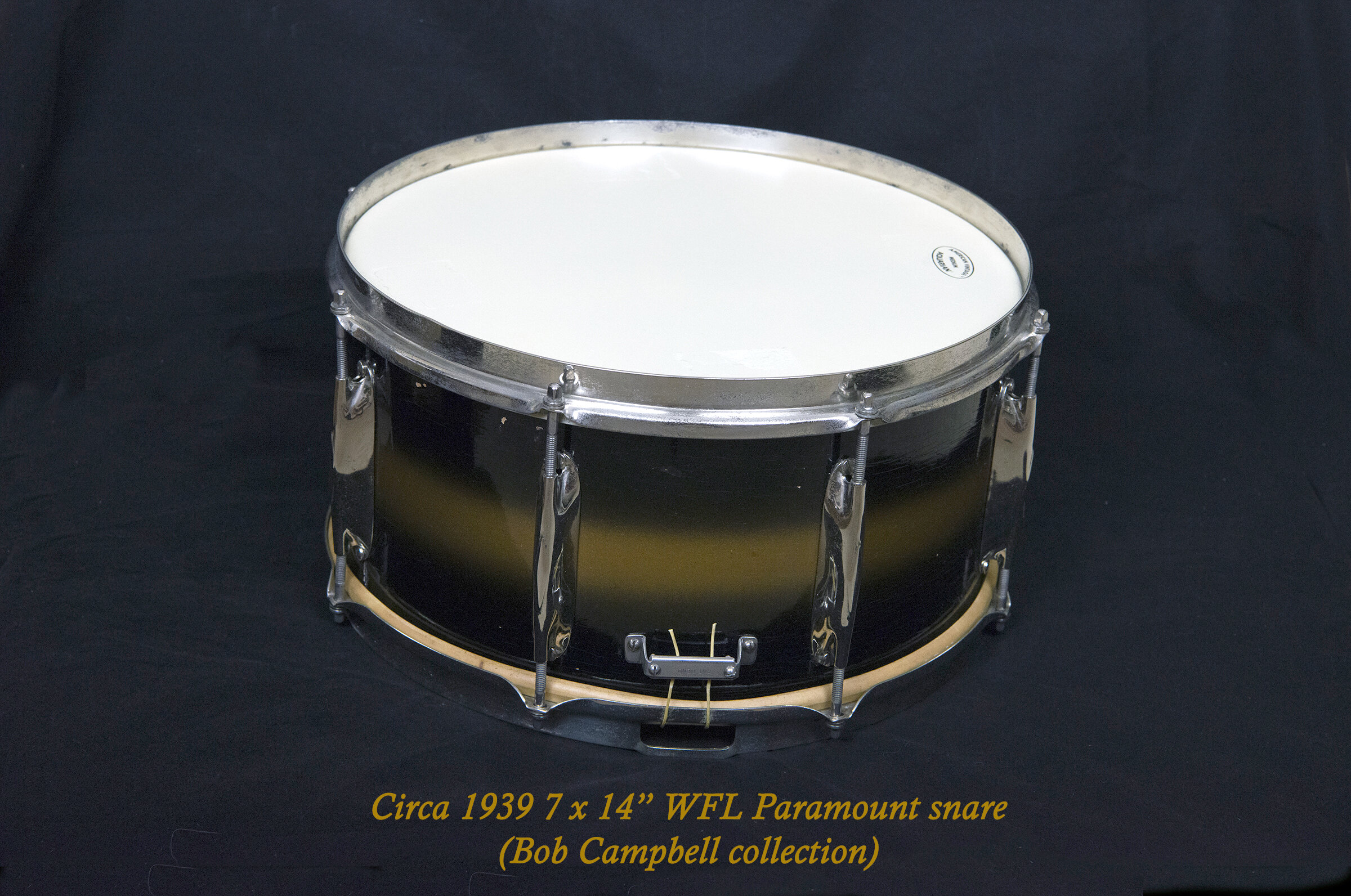
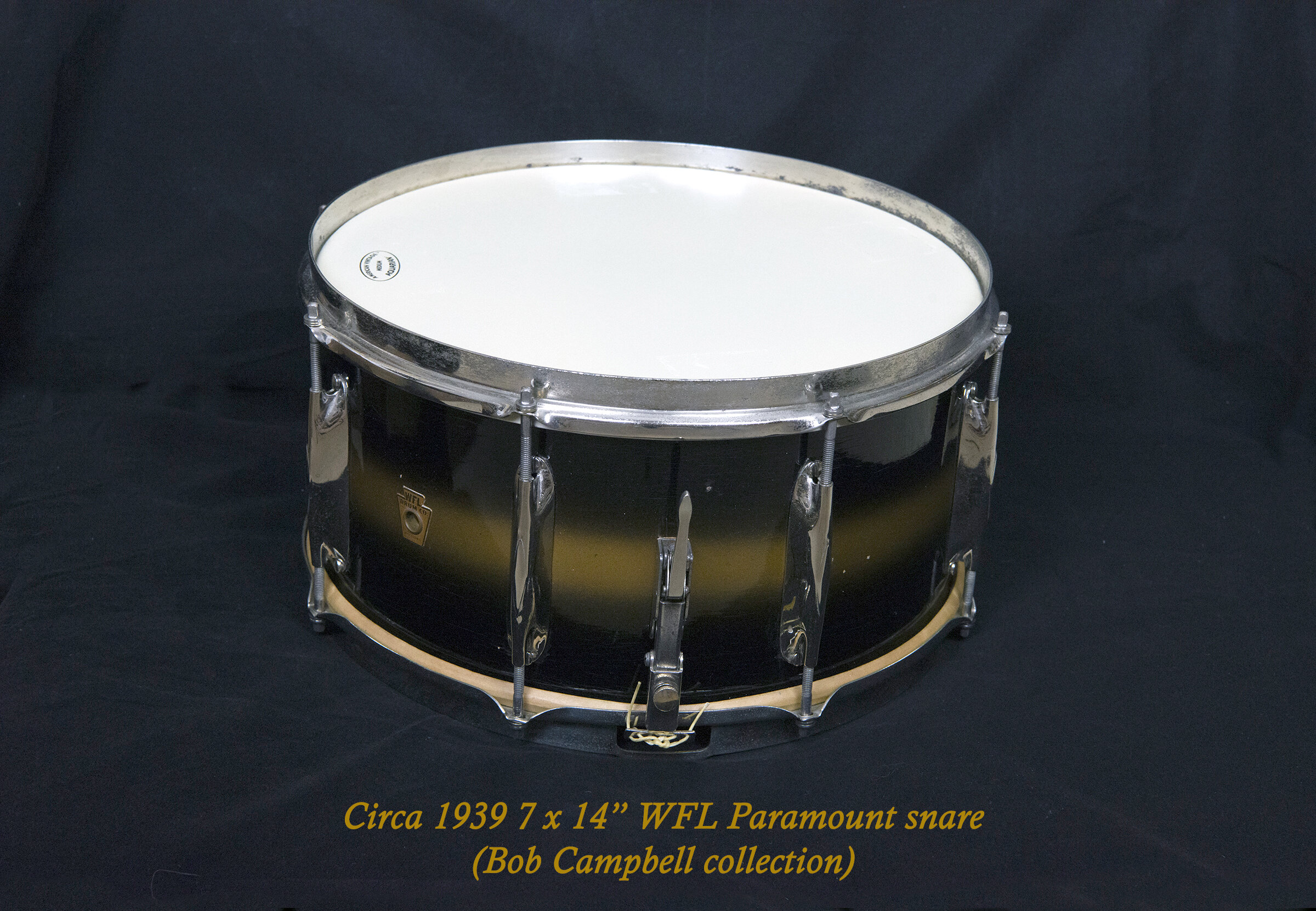
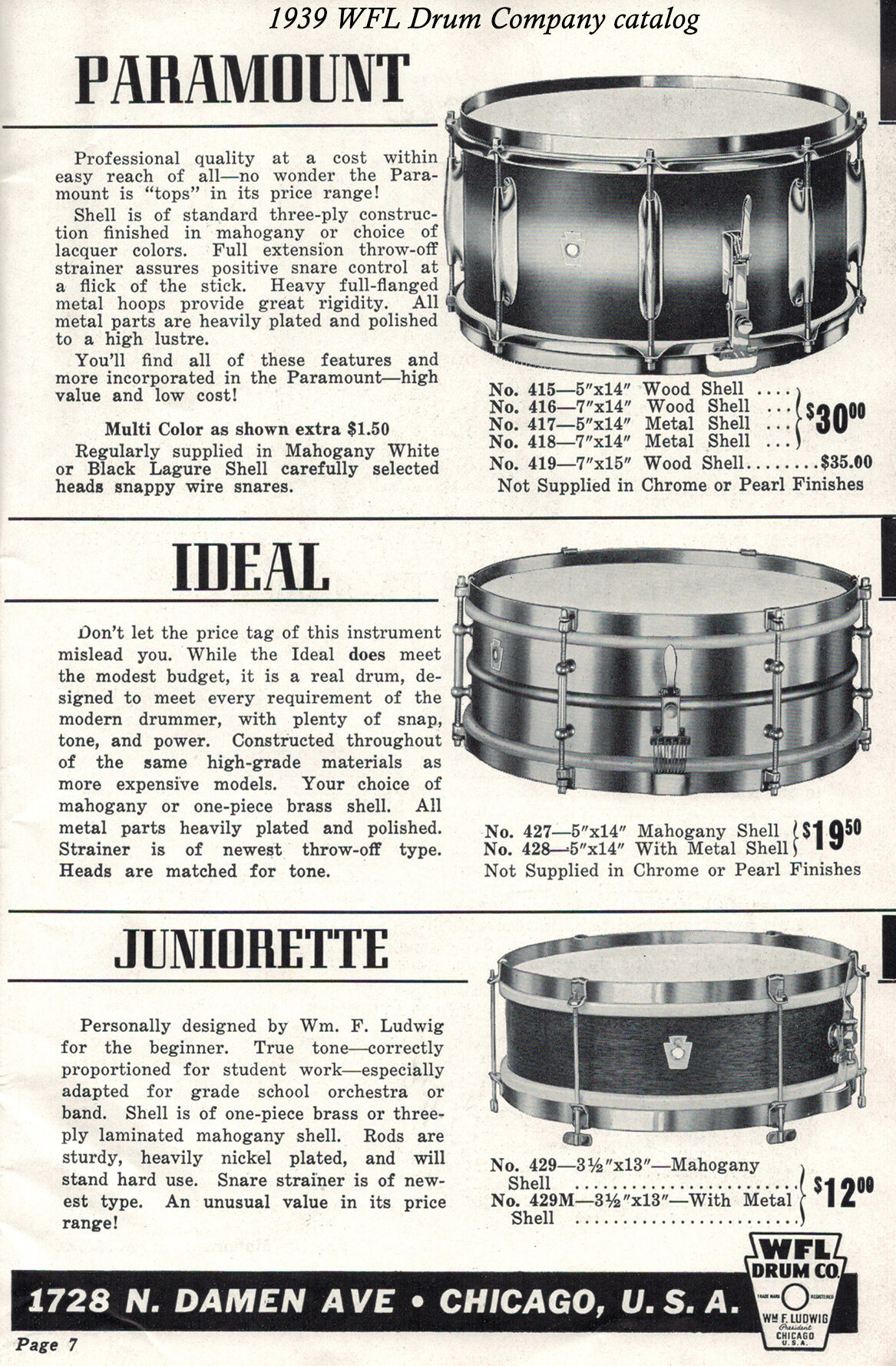
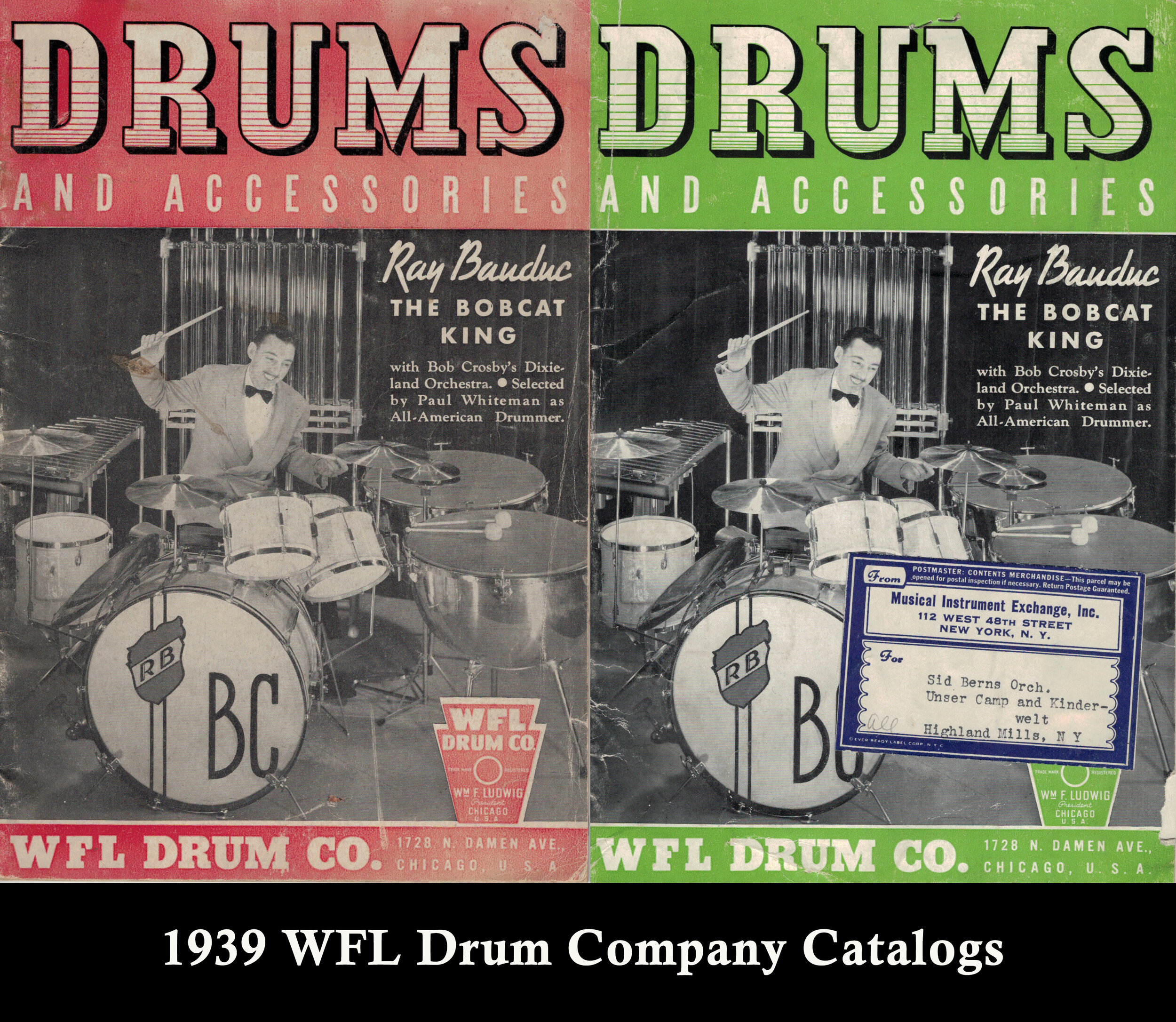
This 1939 WFL Paramount snare was produced in the year that Germany invaded Poland, and just over 2 years later, the U.S. would join the war. Bill Ludwig, Sr. had lost his name, much of his savings, and yet survived both the transition and WWII. In the end, his company thrived, and he regained his name. There is so much to be admired about Bill Sr’s. drive, fortitude, and relentlessness. This 1939 WFL Paramount snare is one representation of his work during this challenging time and embodies all those who appreciated its sound and construction over 8 decades.
Read more1936 Leedy & Strupe (L&S) Drum Kit
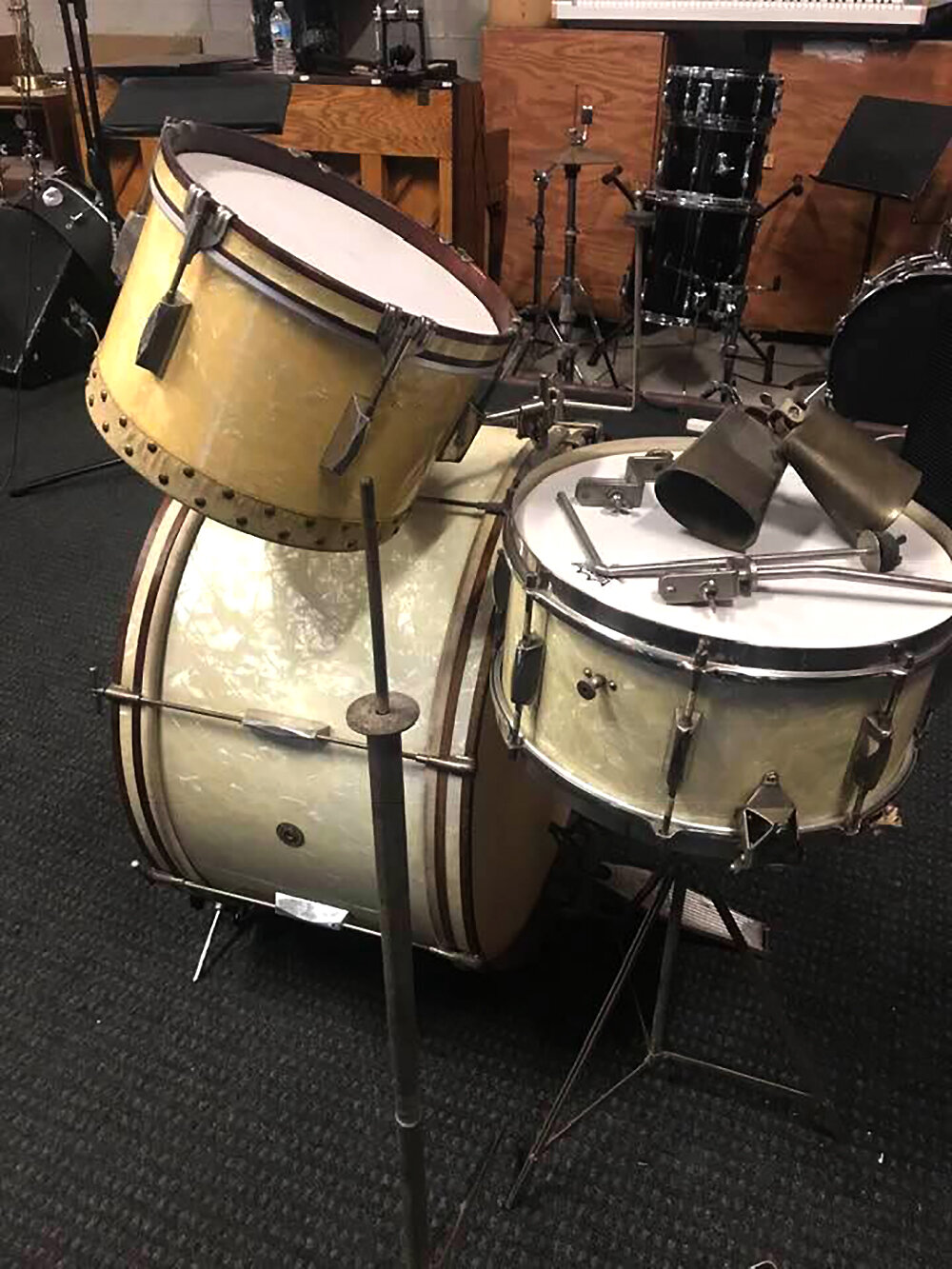
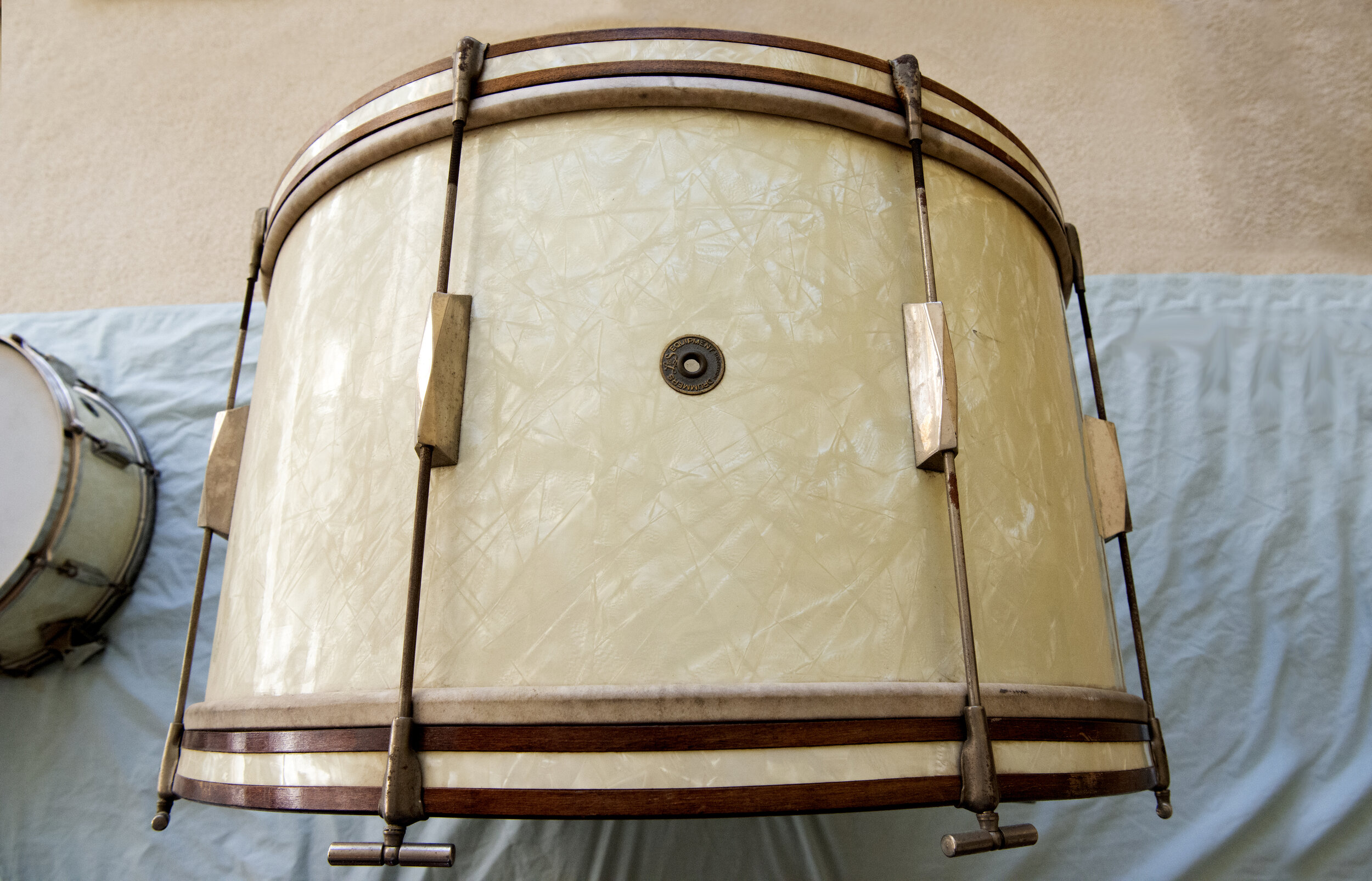
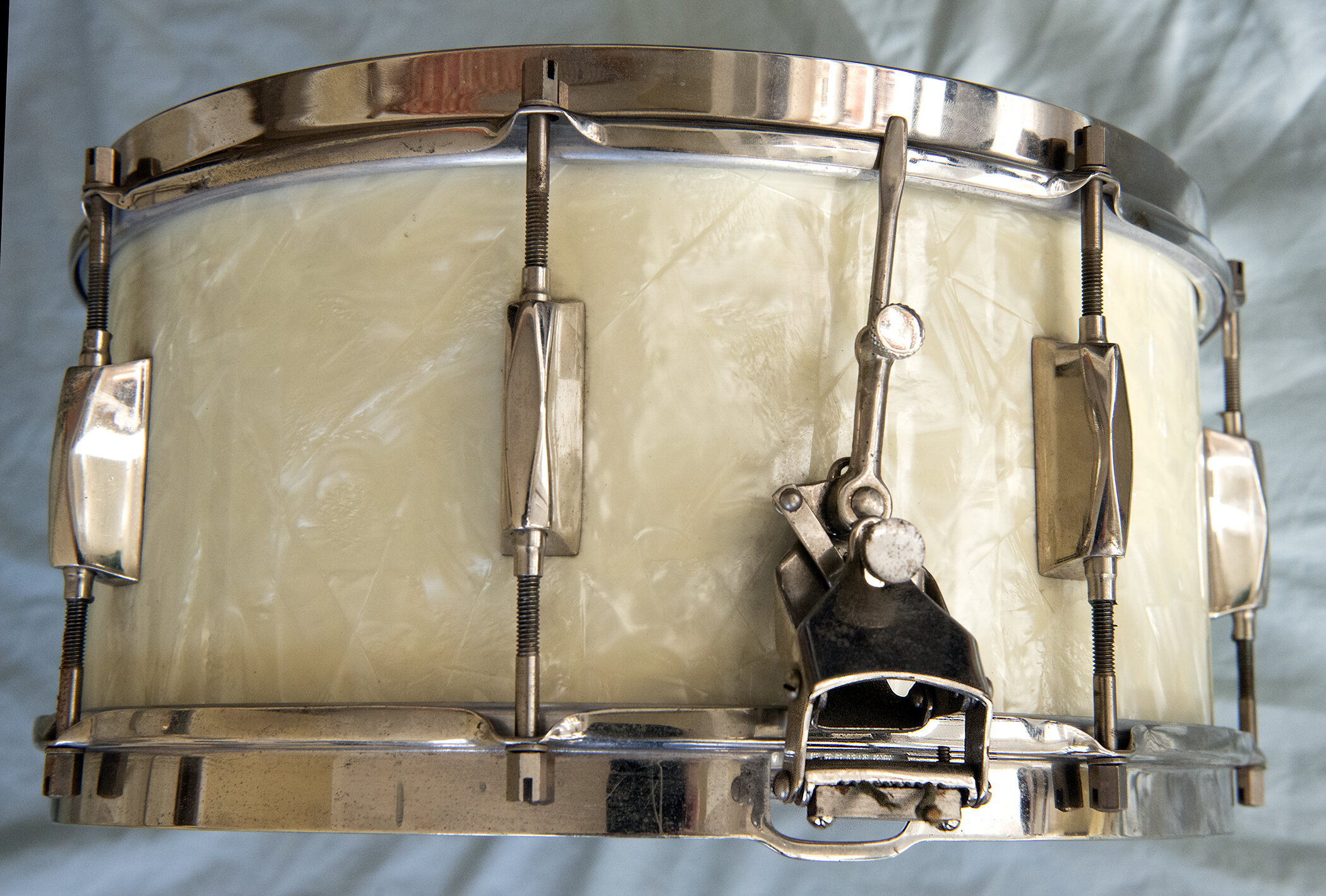

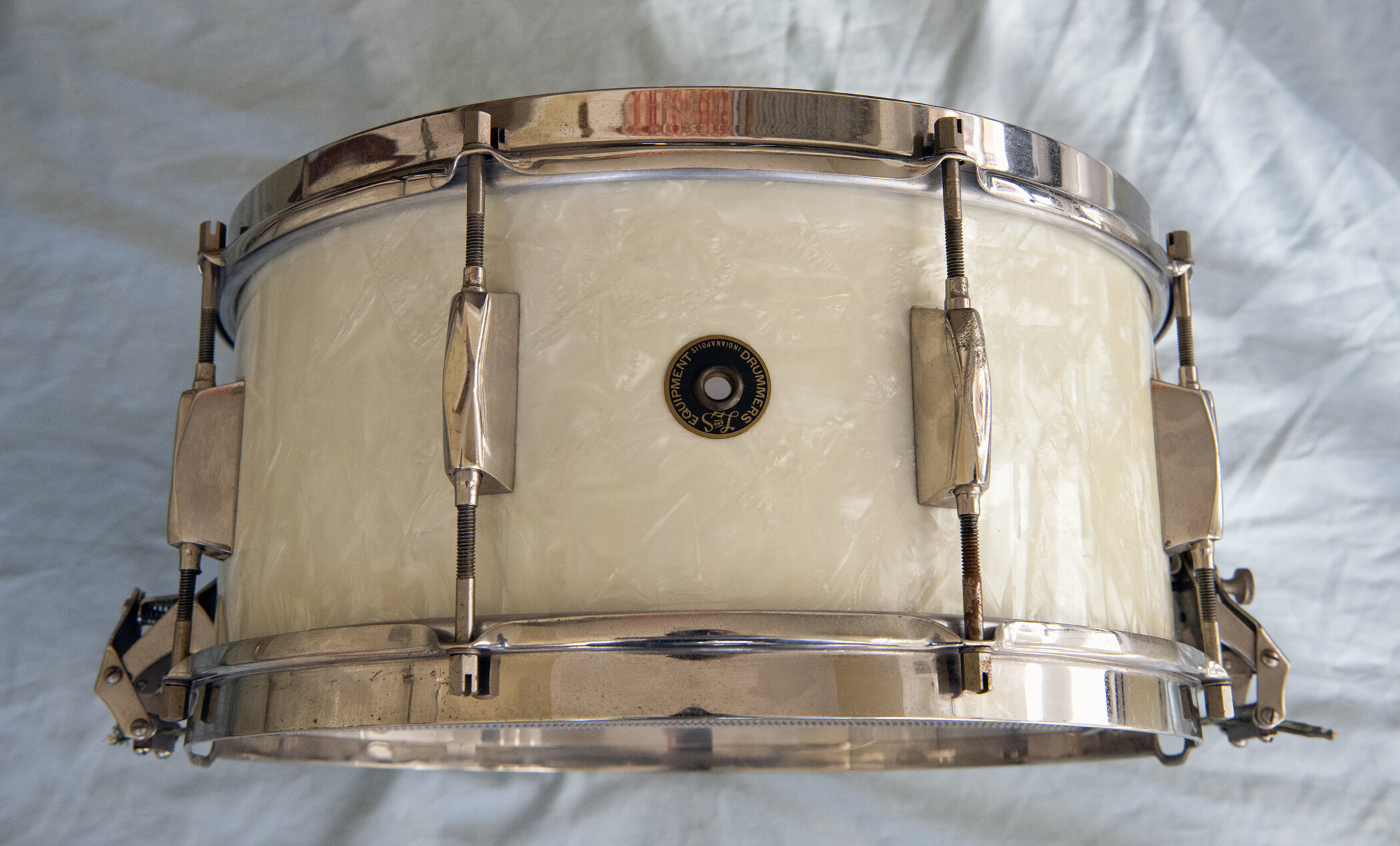
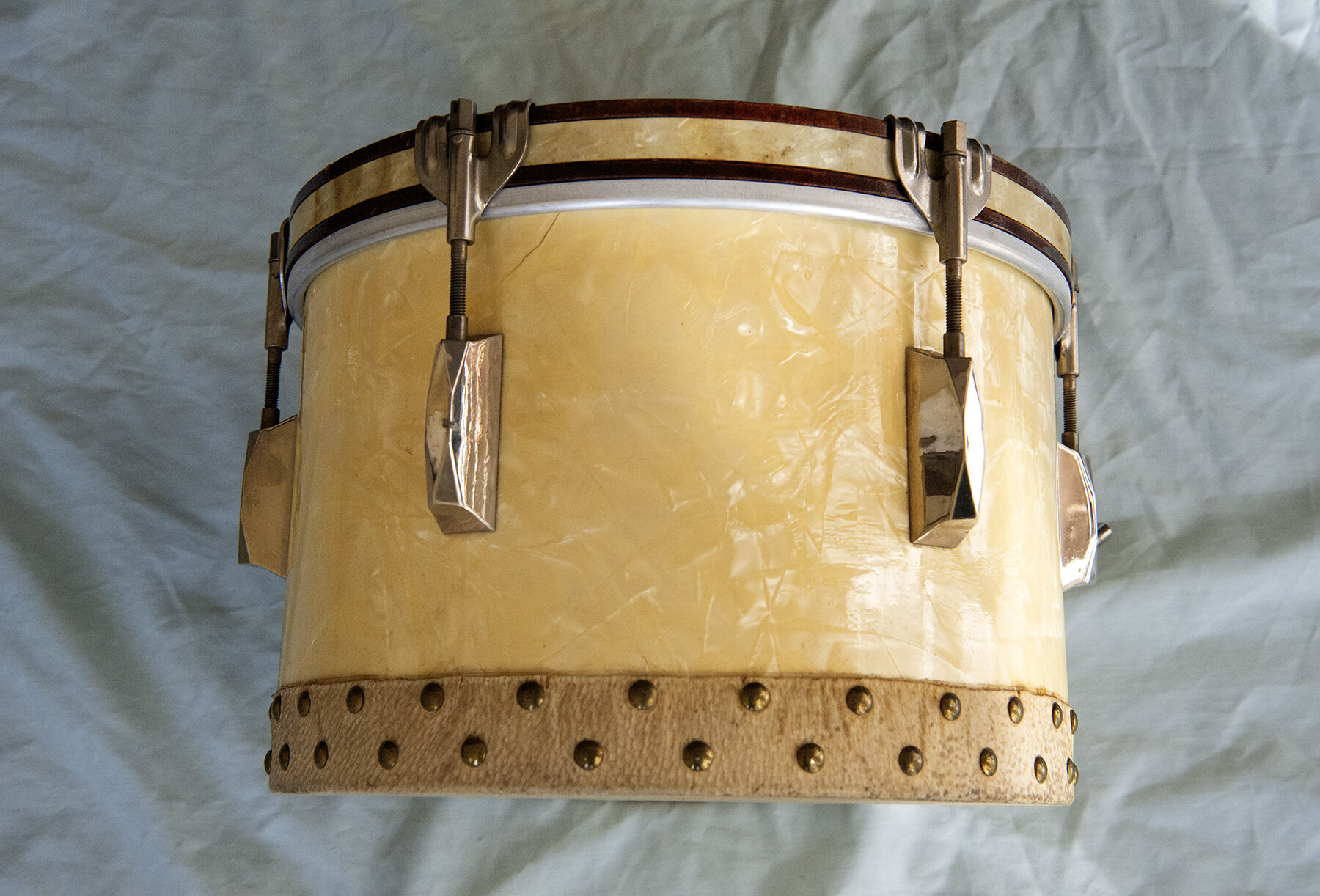
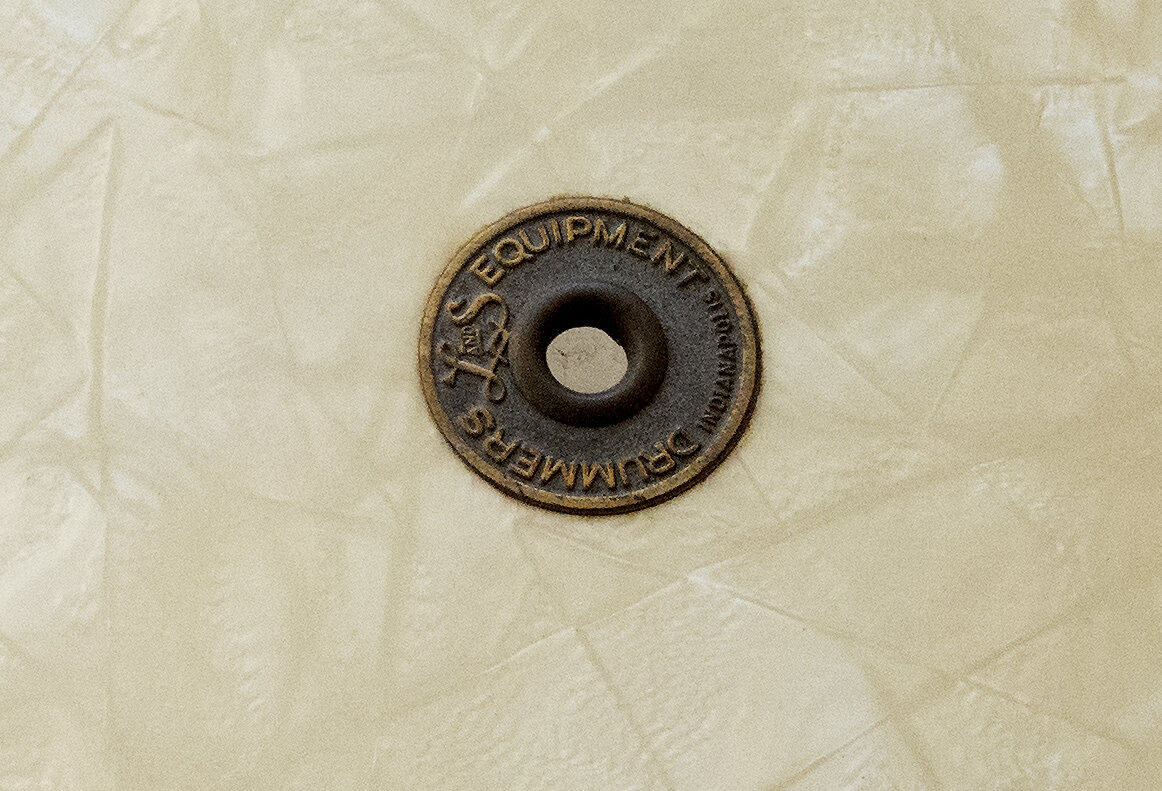
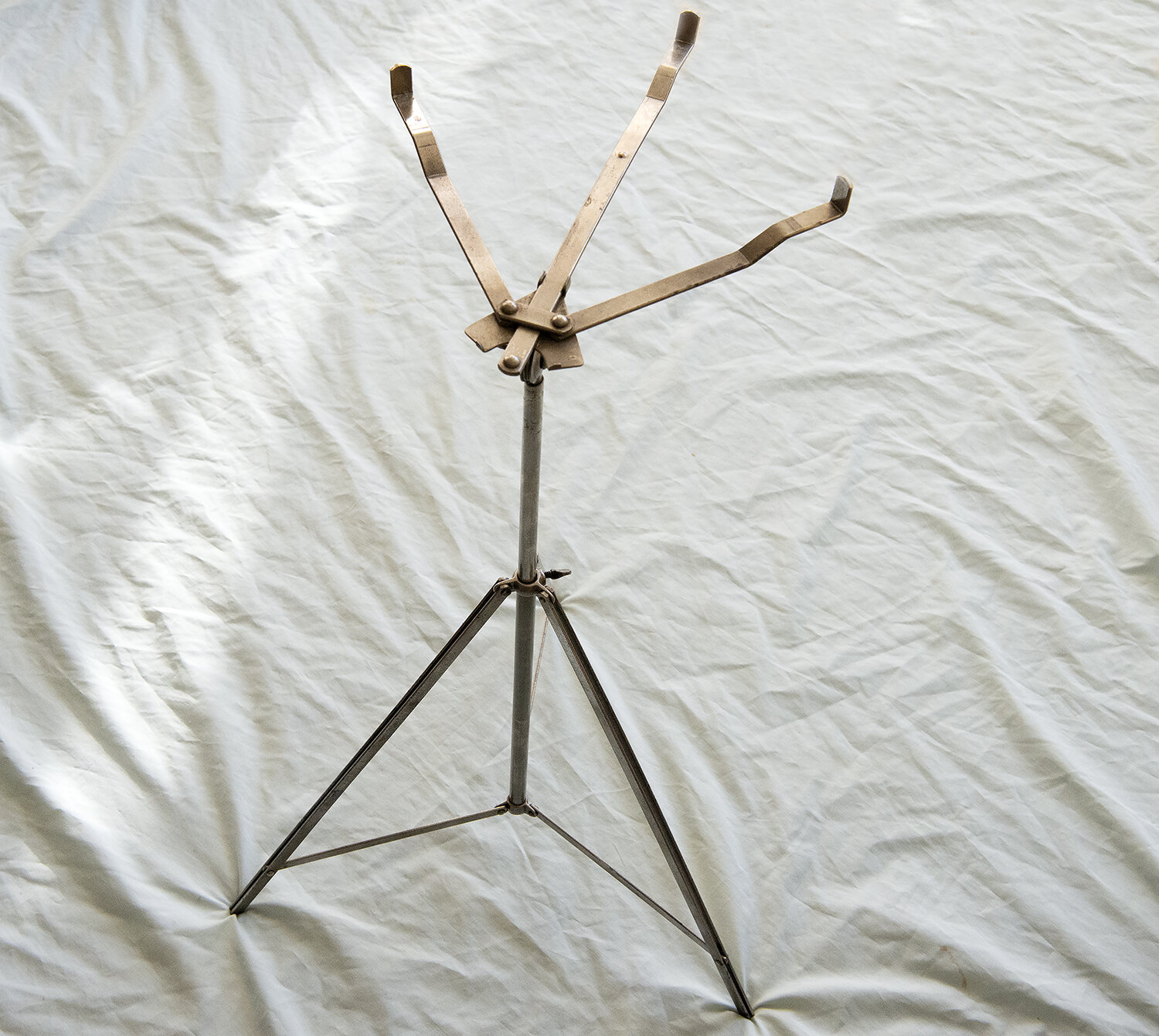
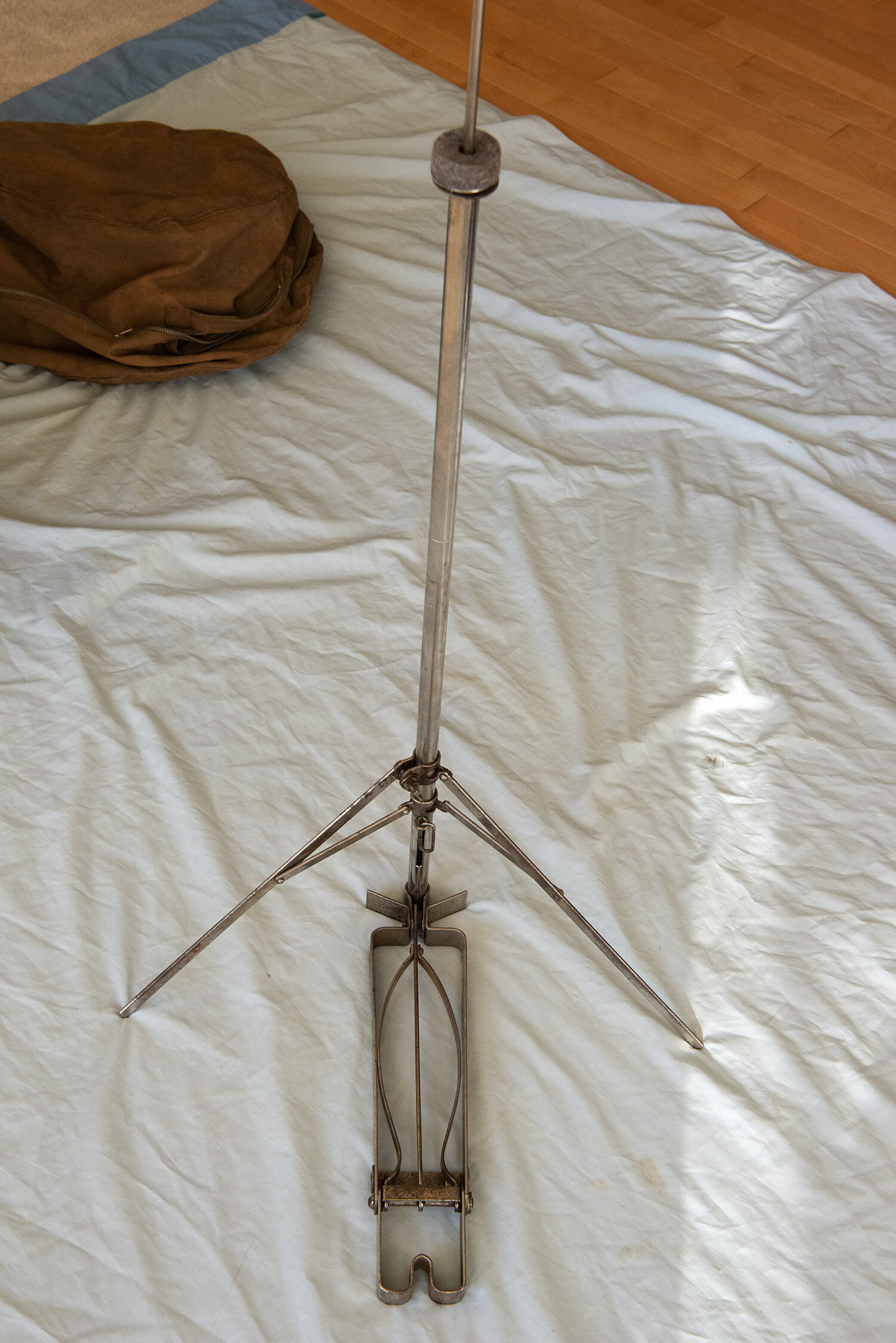
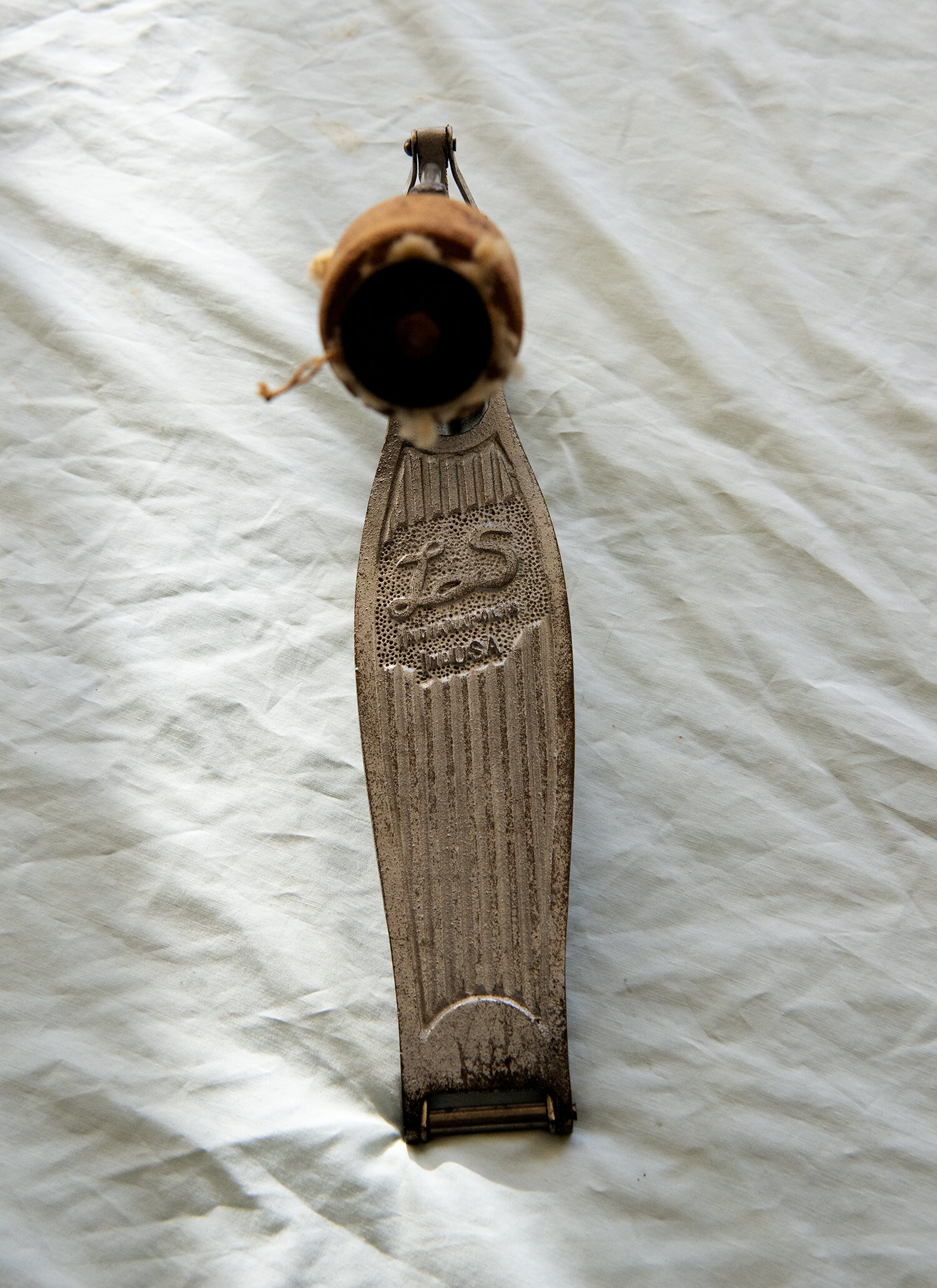
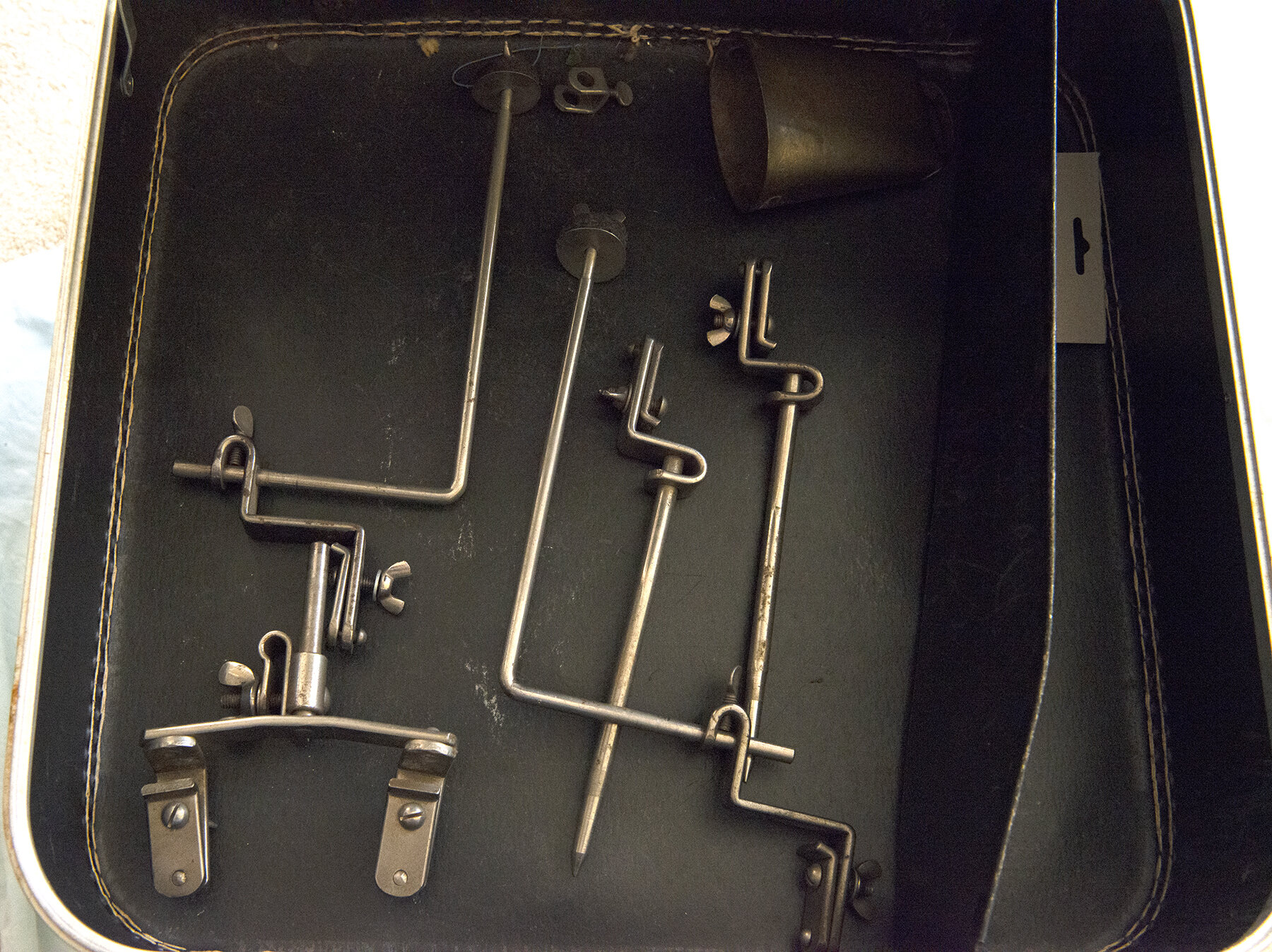
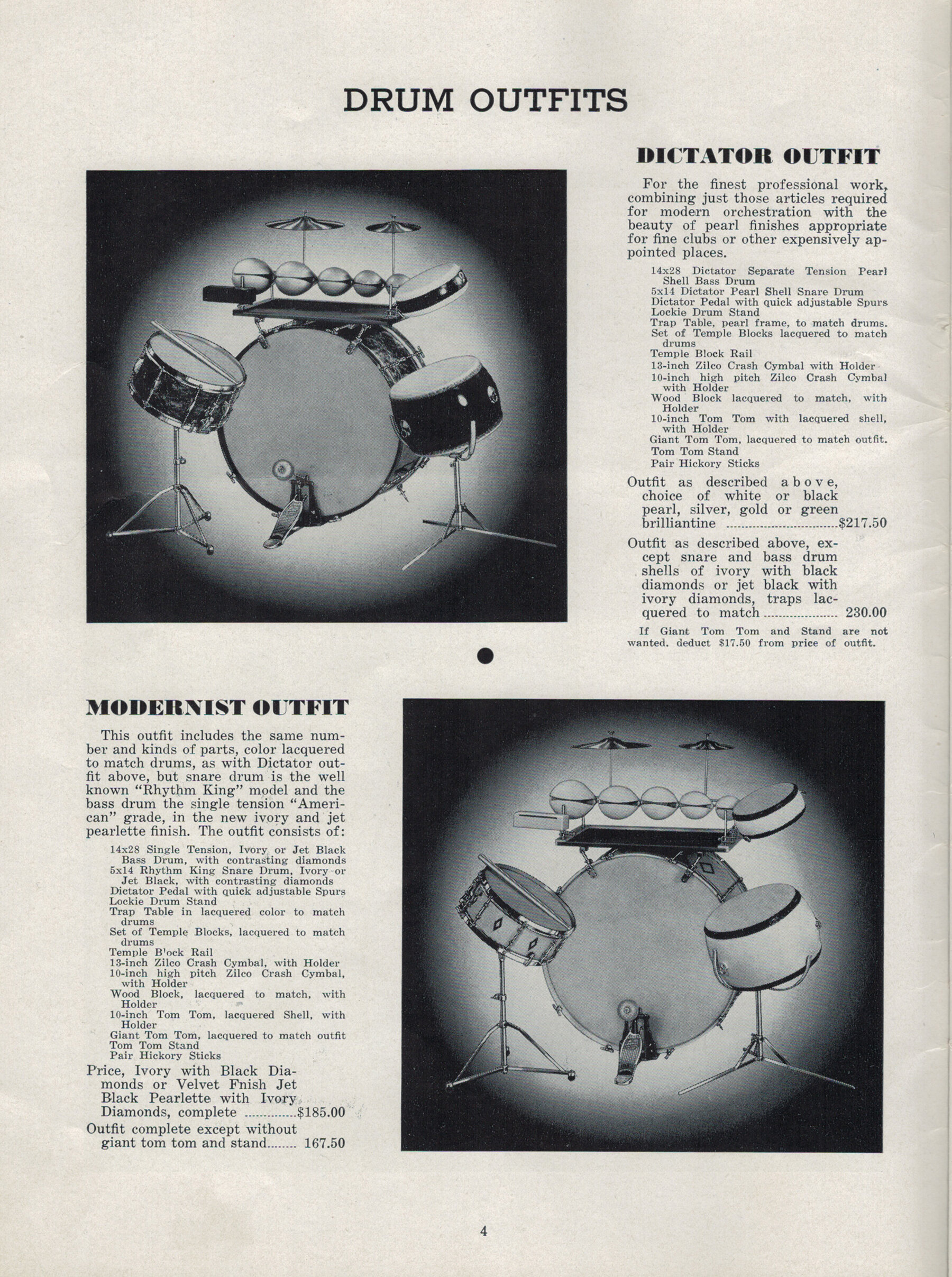
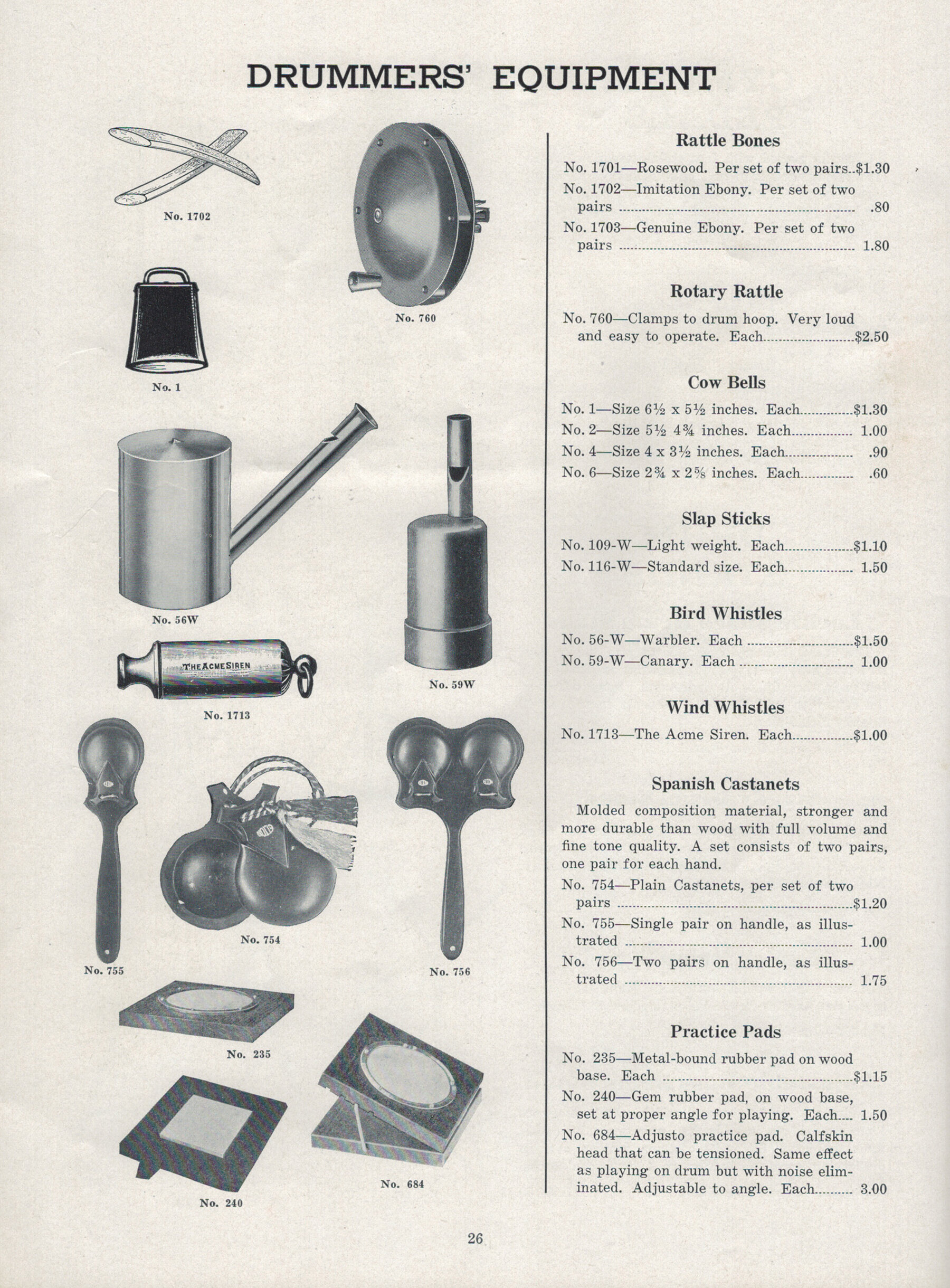
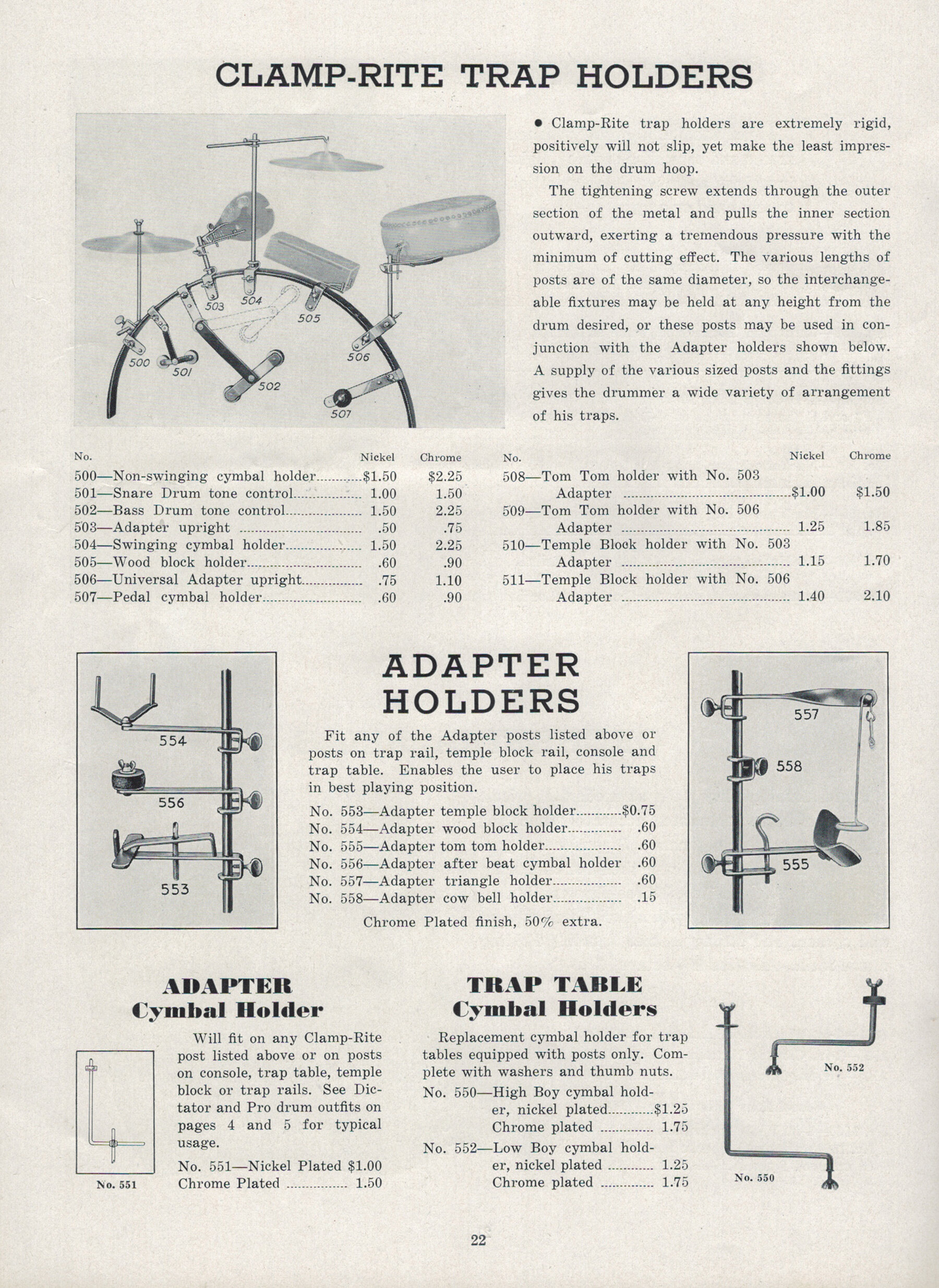
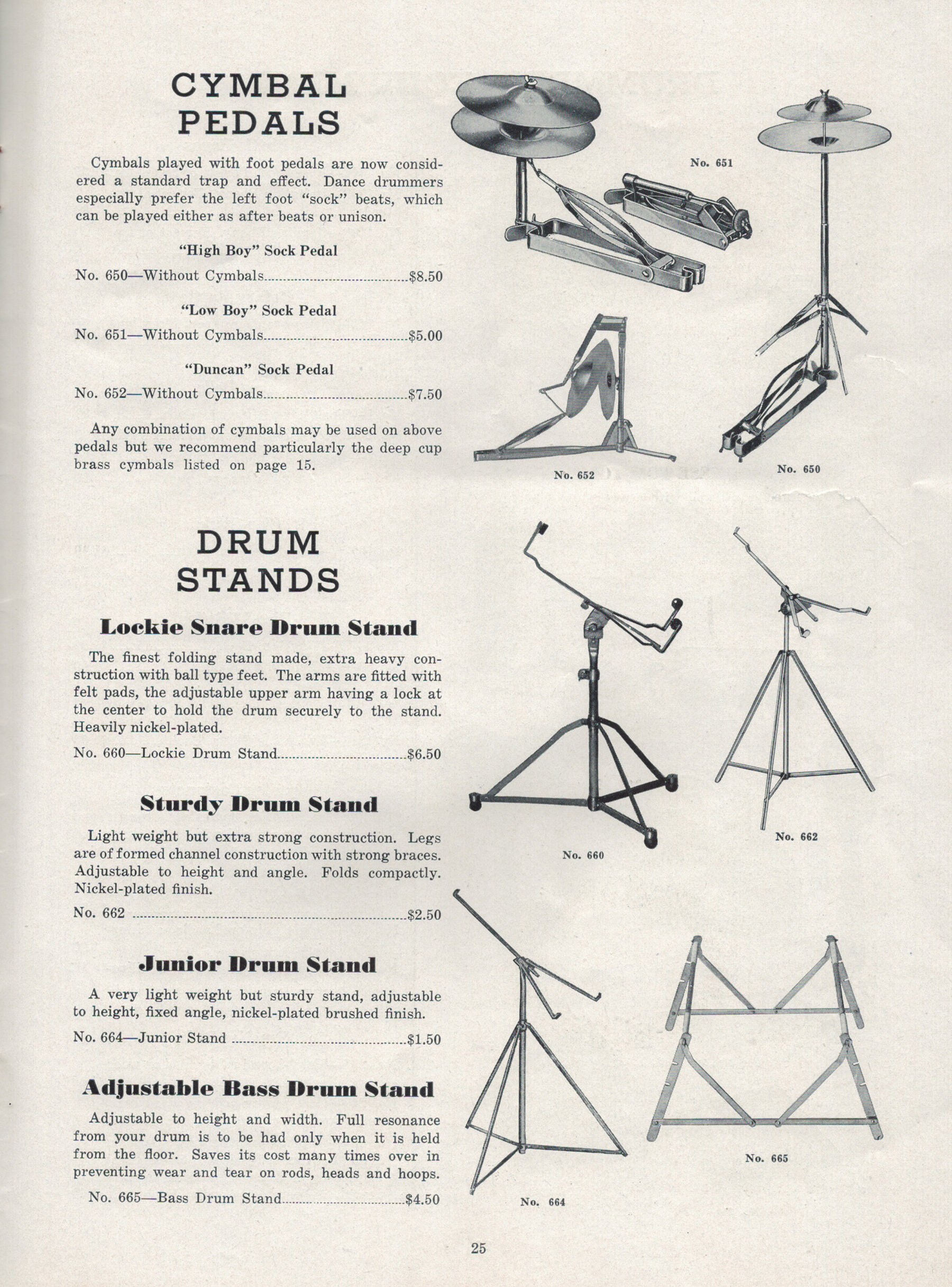
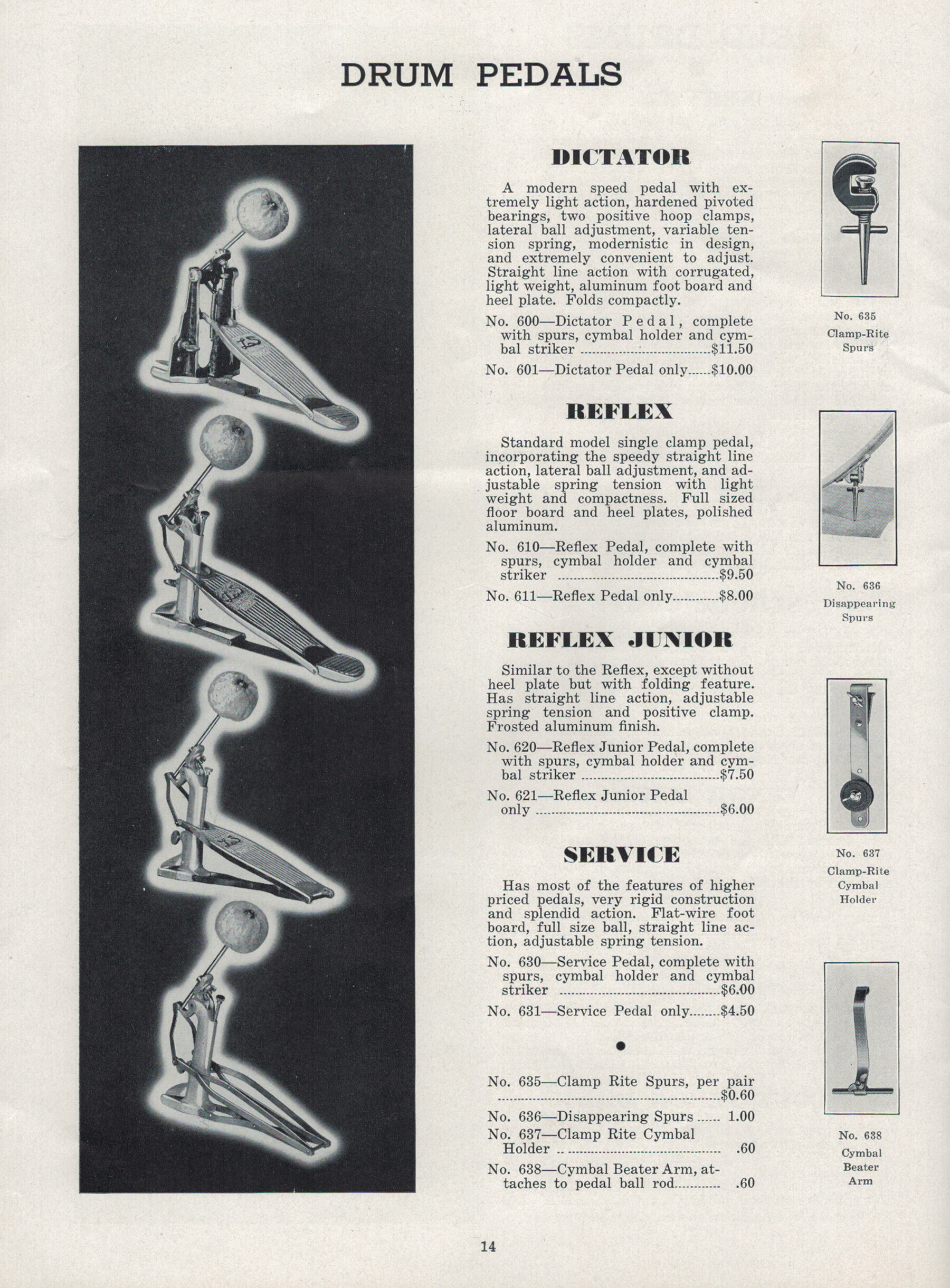
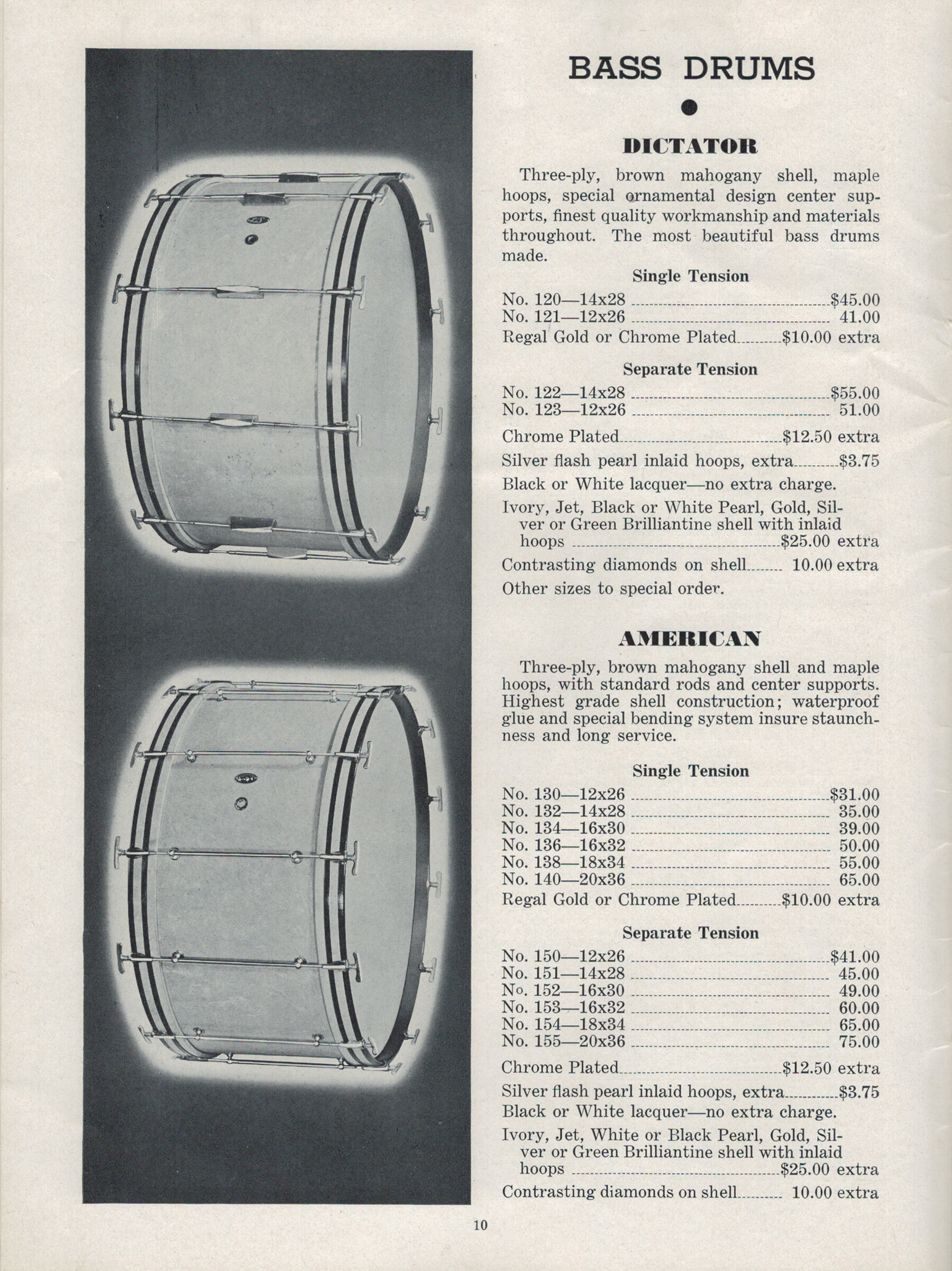

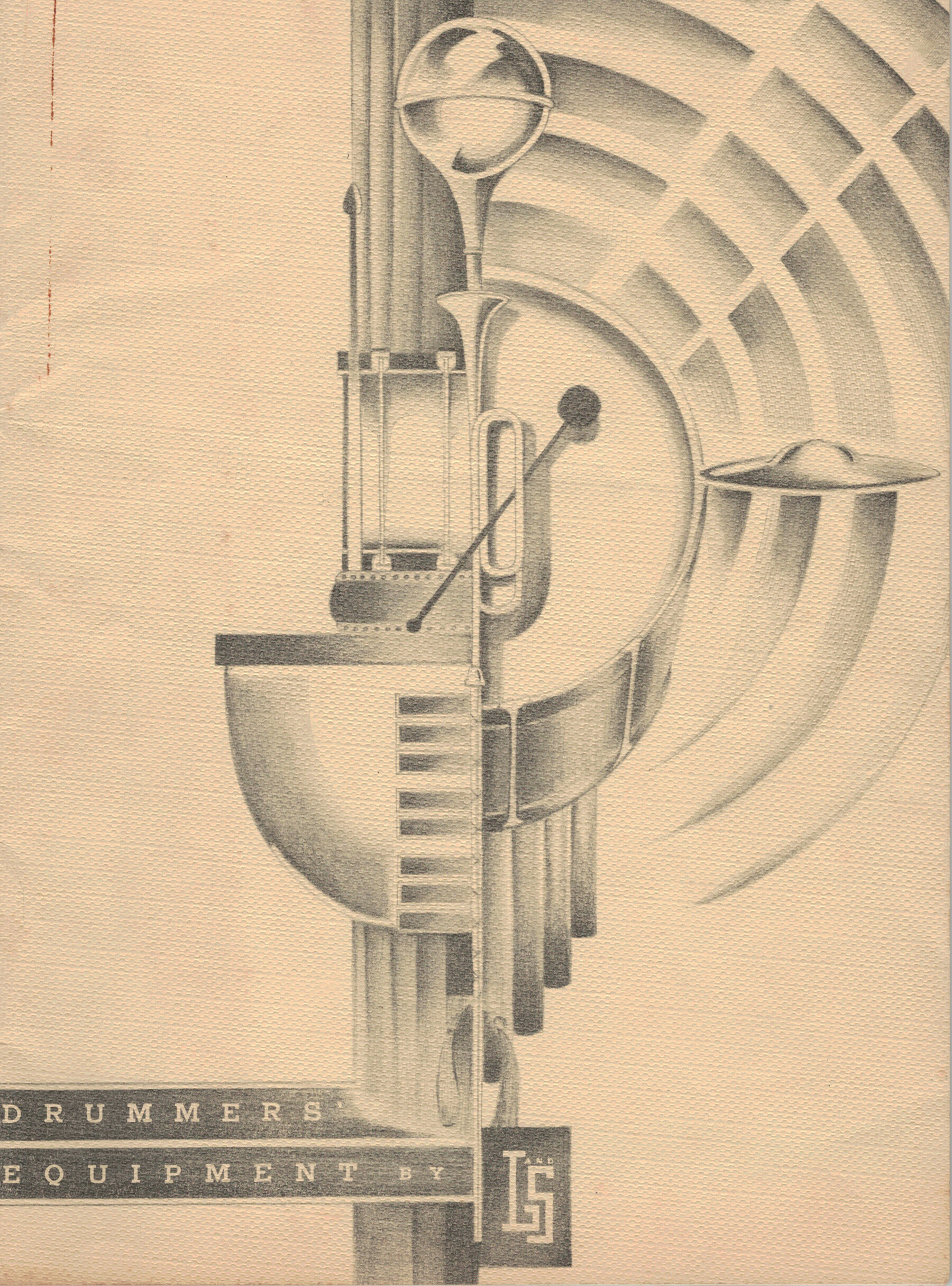
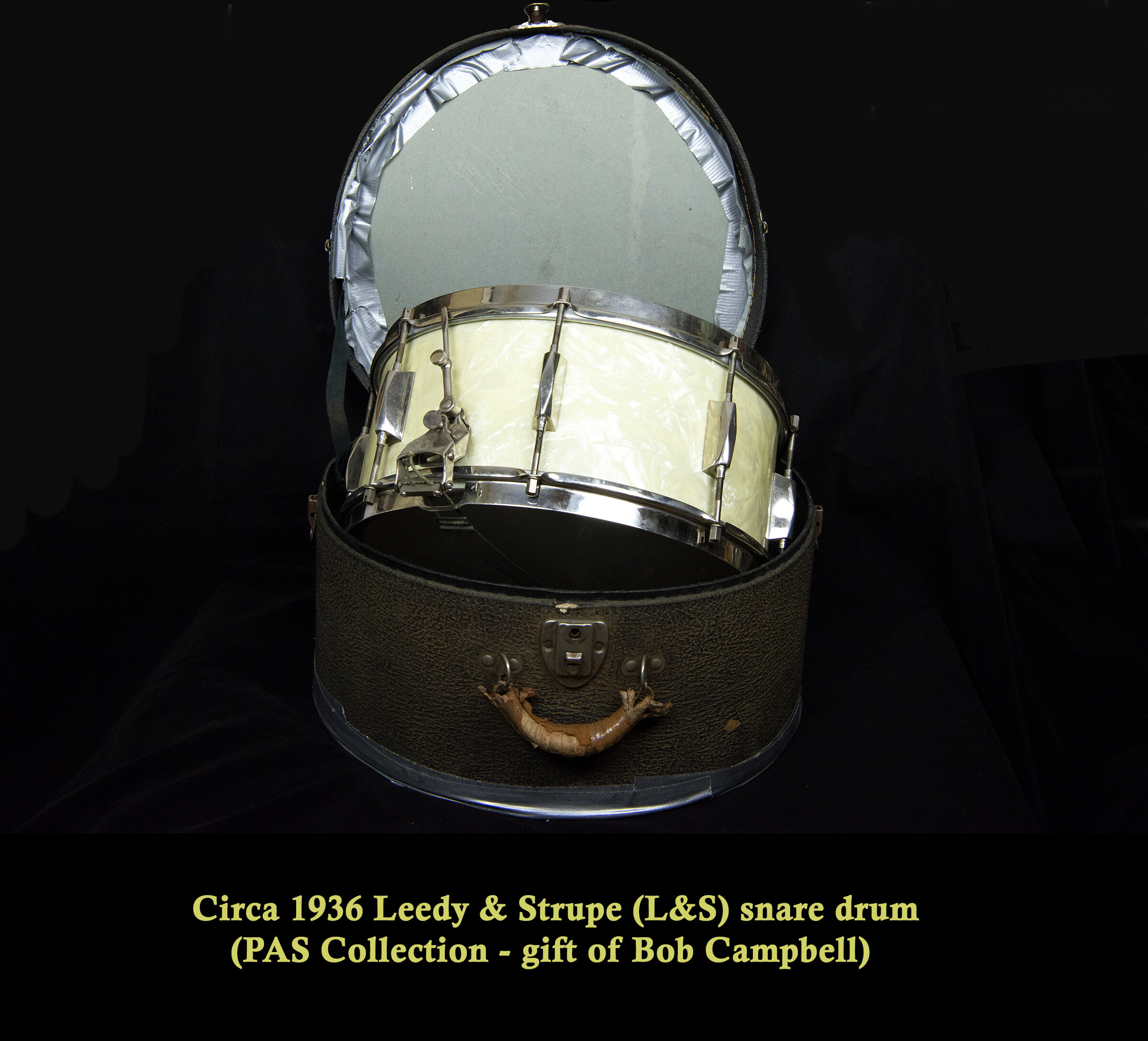
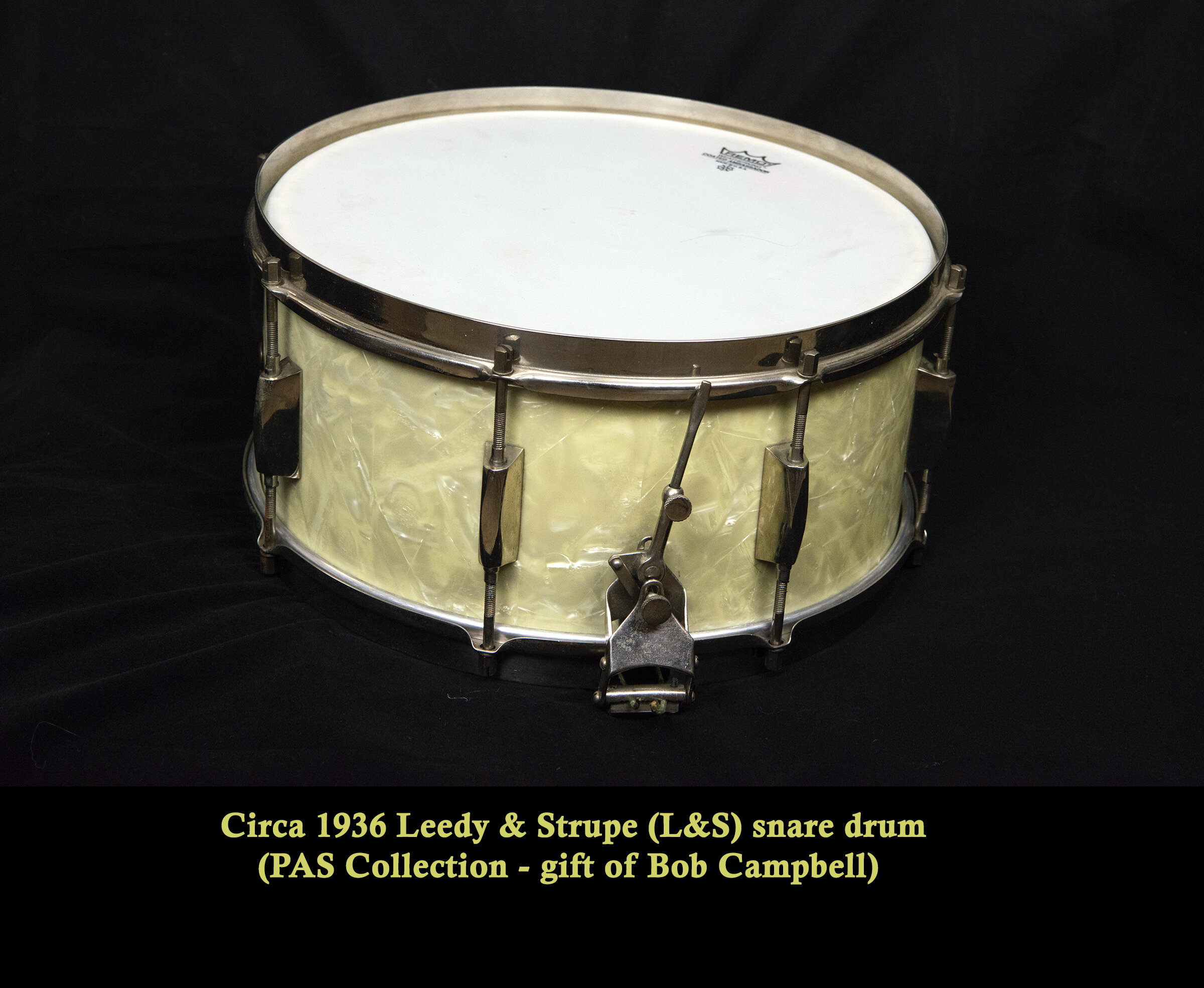
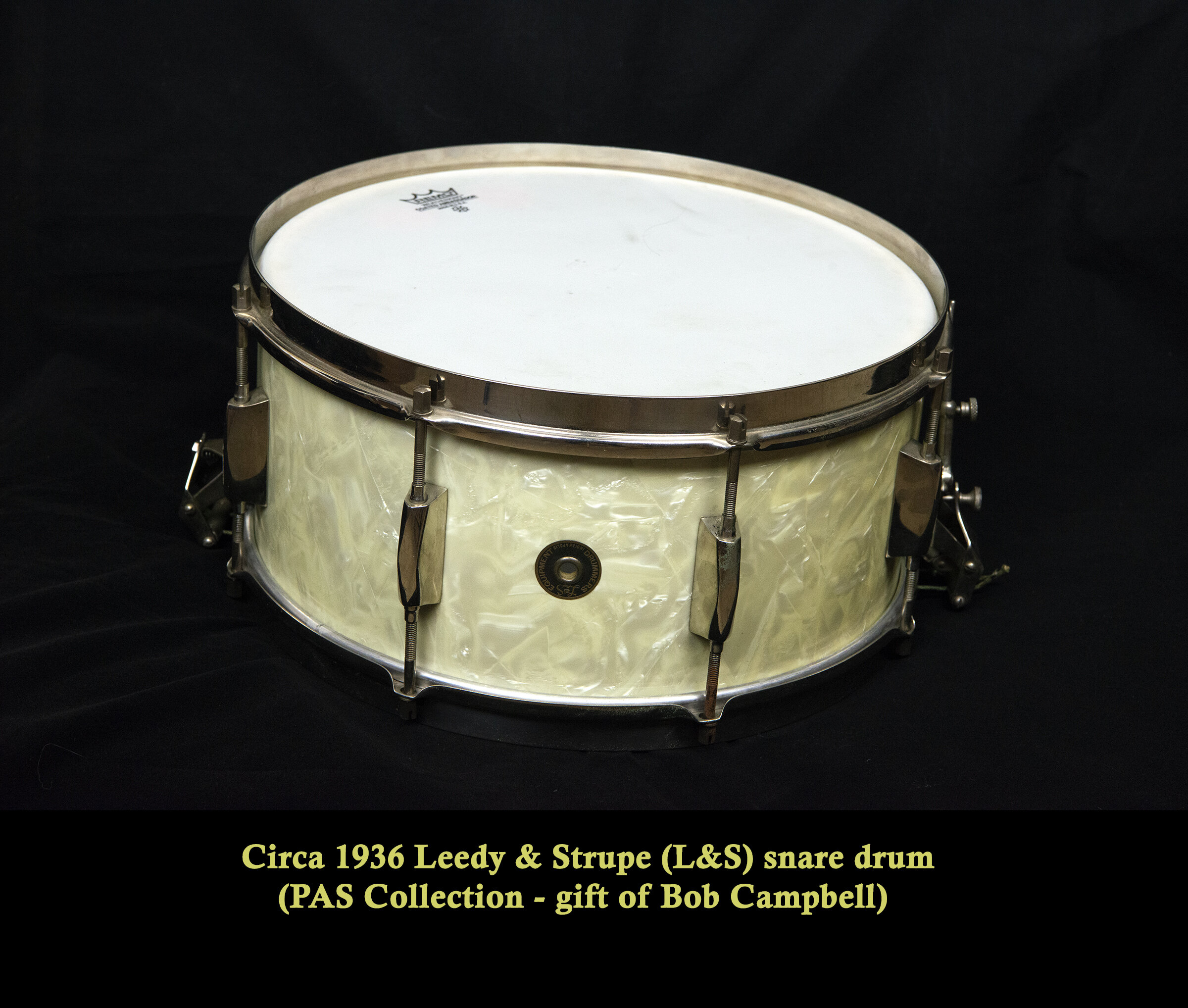
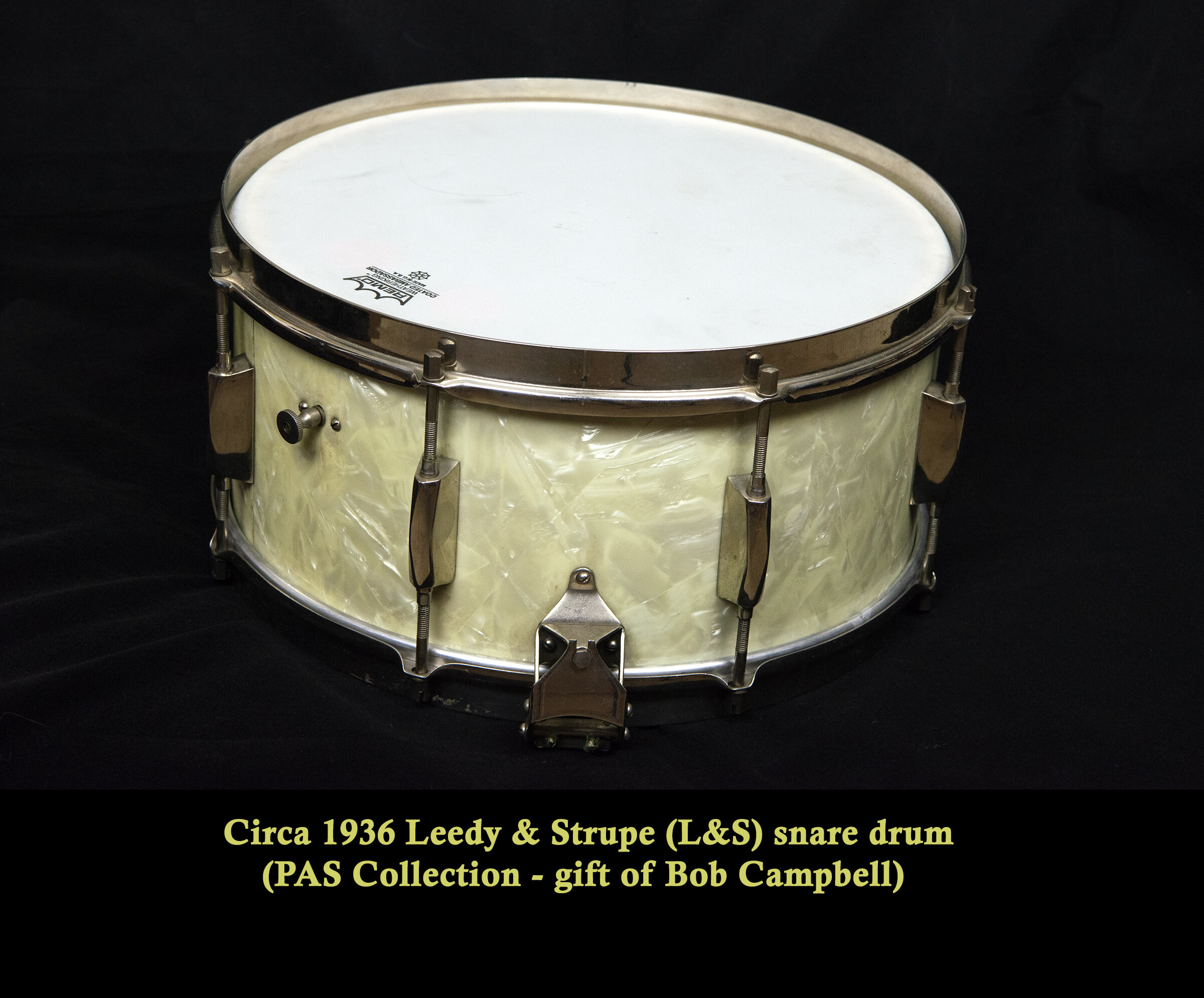
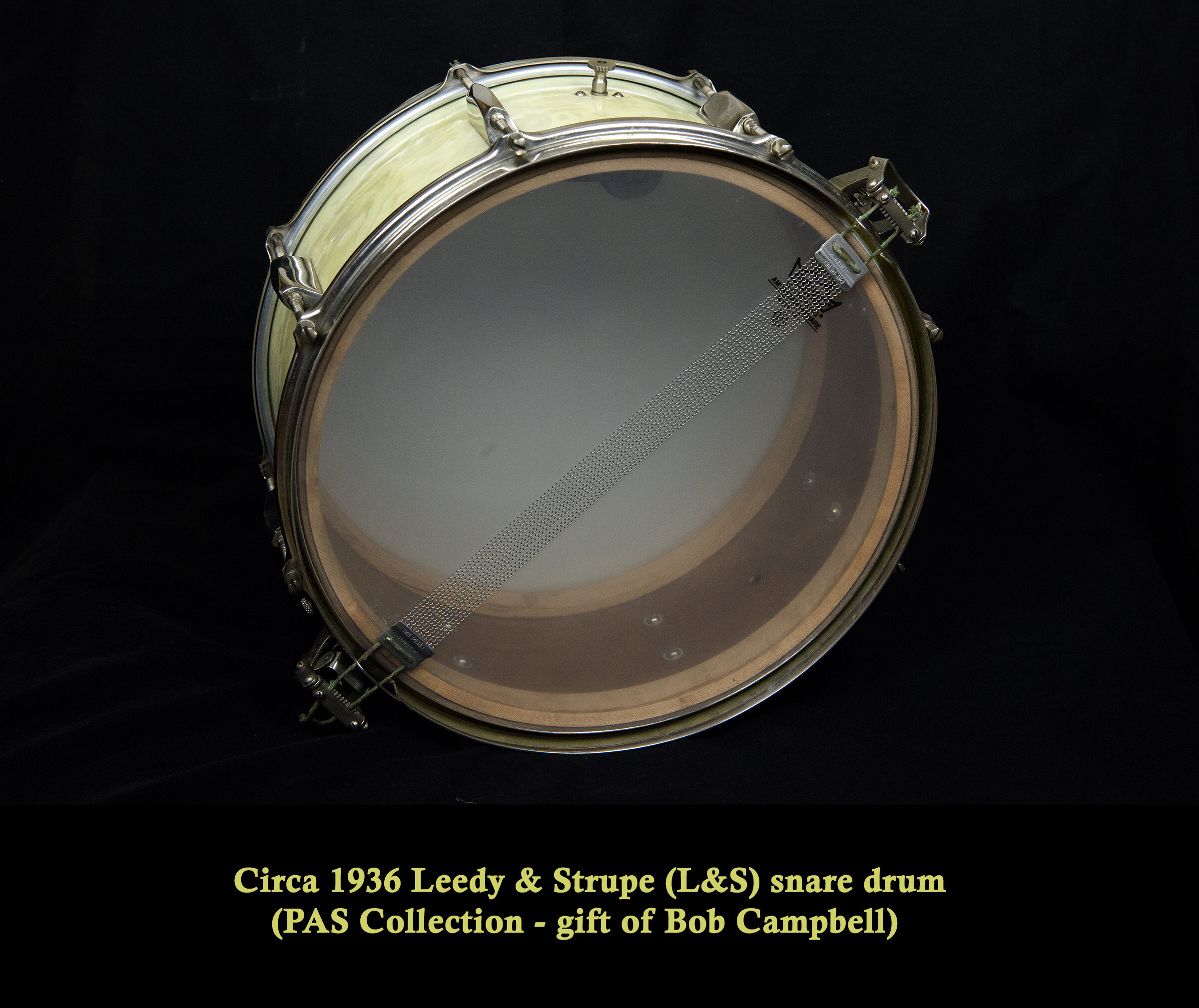
One day in late 2020, I was doing my usual browsing through vintage drum-related social media posts and came across a 1936 Leedy & Strupe (L&S) white marine pearl drum kit for sale. This L&S kit consisted of a white marine pearl 14 x 28” bass drum (with calf heads), 9 x 13” tom (tacked bottom head), 6.5 X 14” snare, cowbell, and various hardware (original L&S bass drum pedal, hi-hat with lamb wool beater, Clamp-Rite trap holders, spurs). According to Harry Cangany (noted author, drum historian), this kit was, “a ‘Dictator’ model in white pearl (L&S name for white marine pearl)…1936 is probably correct.”
Read moreA&F Nickel-plated Hardware: An interview with Ramy Antoun and NSMD Test-drive
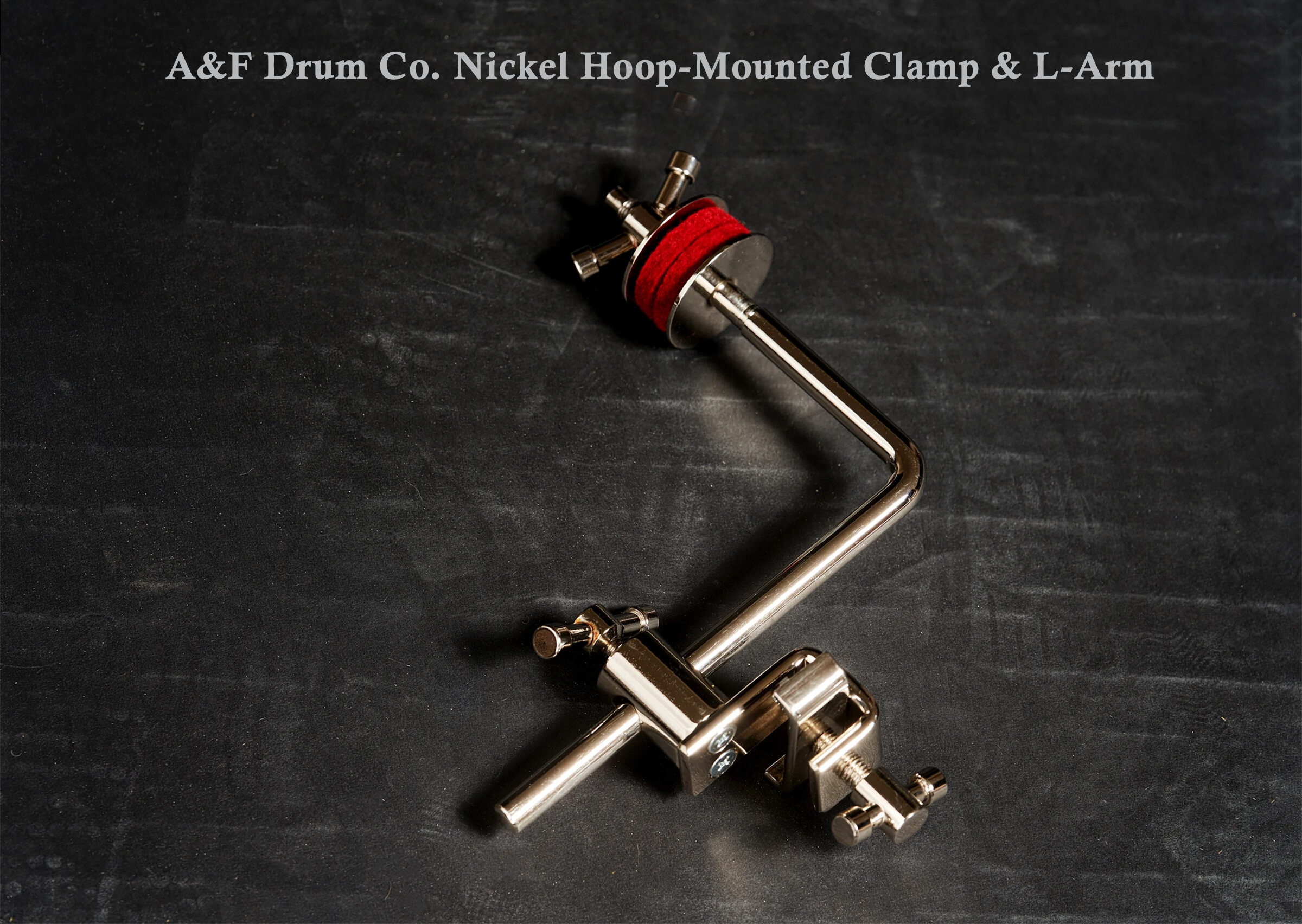
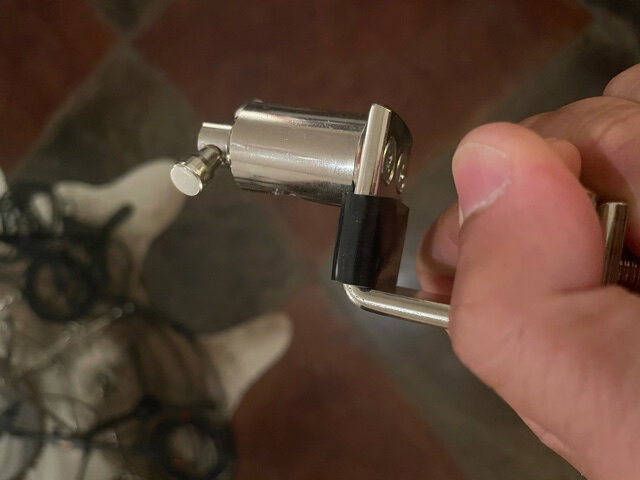
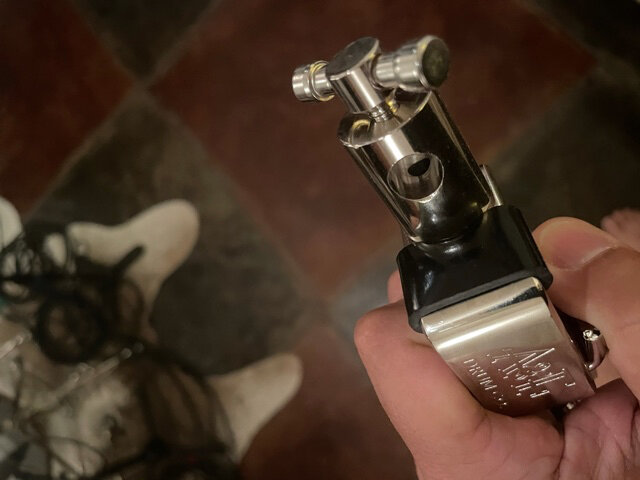
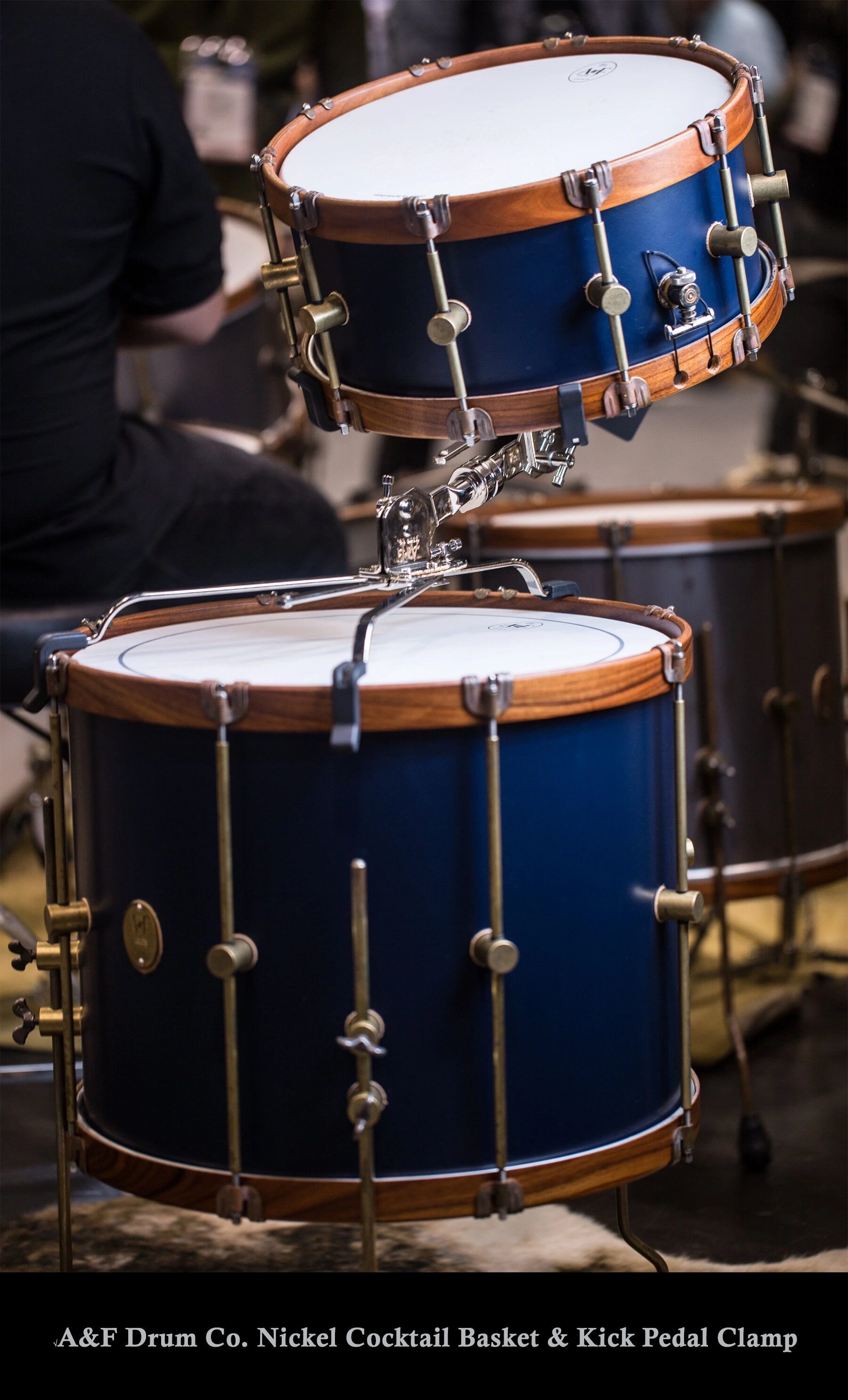
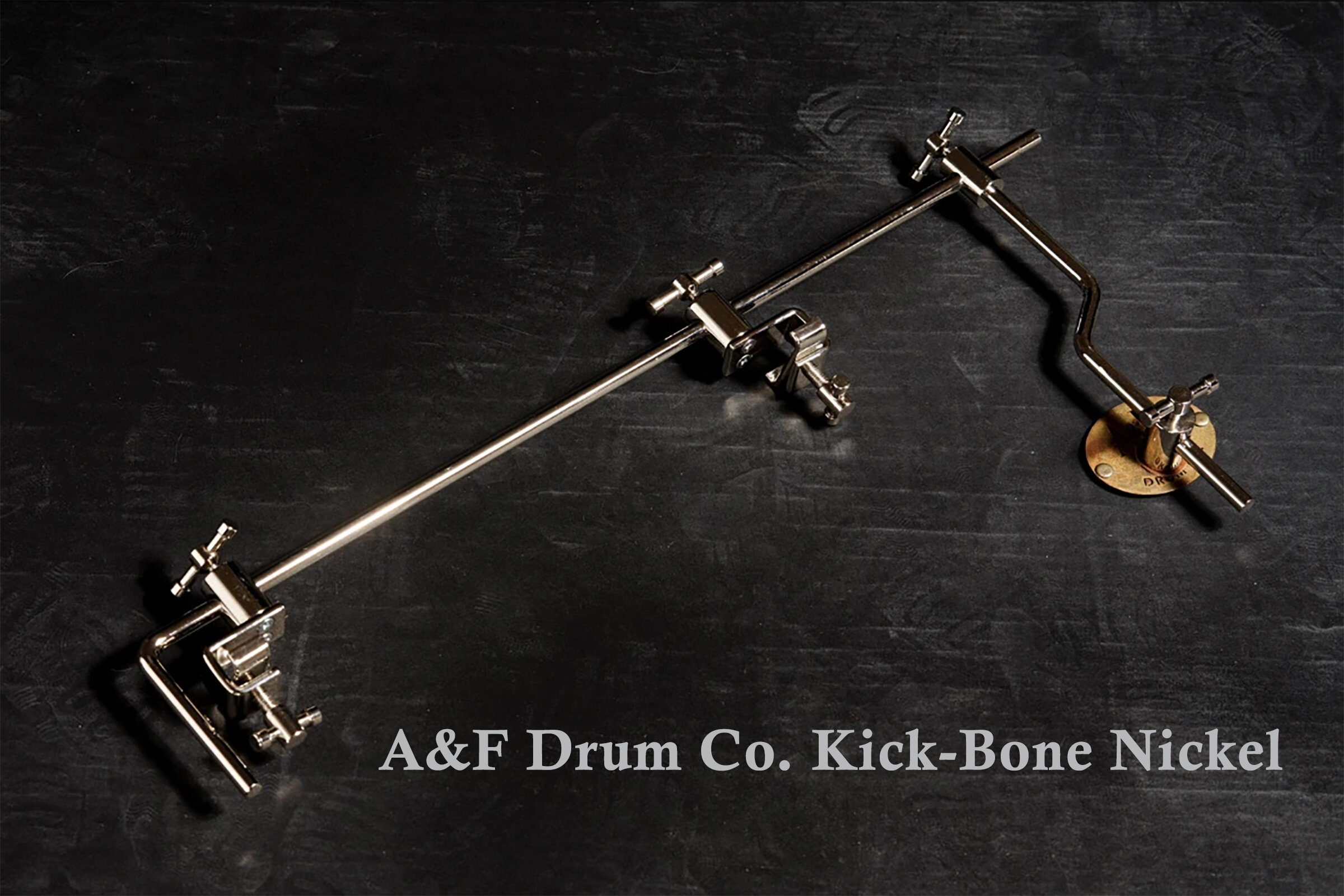
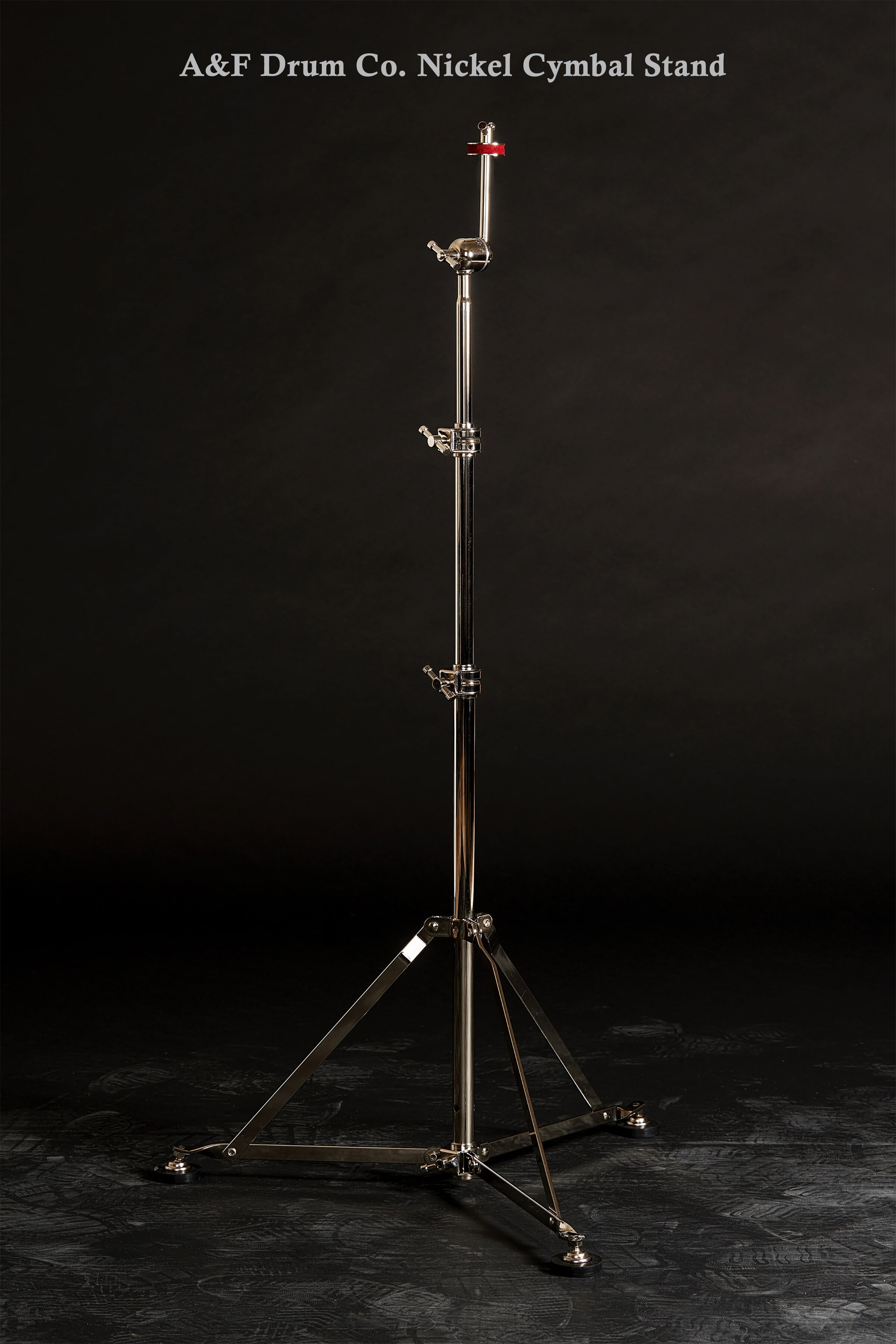
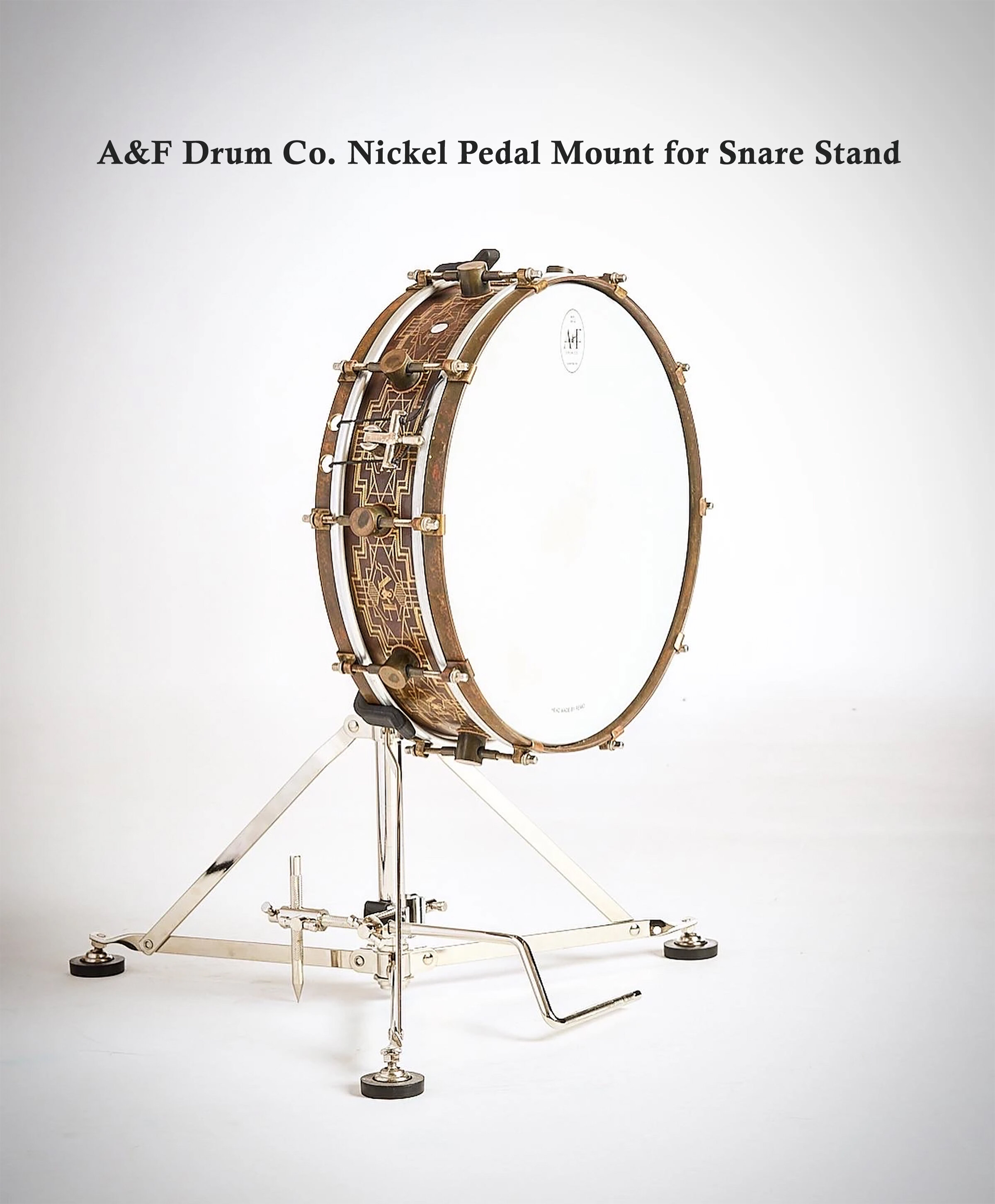
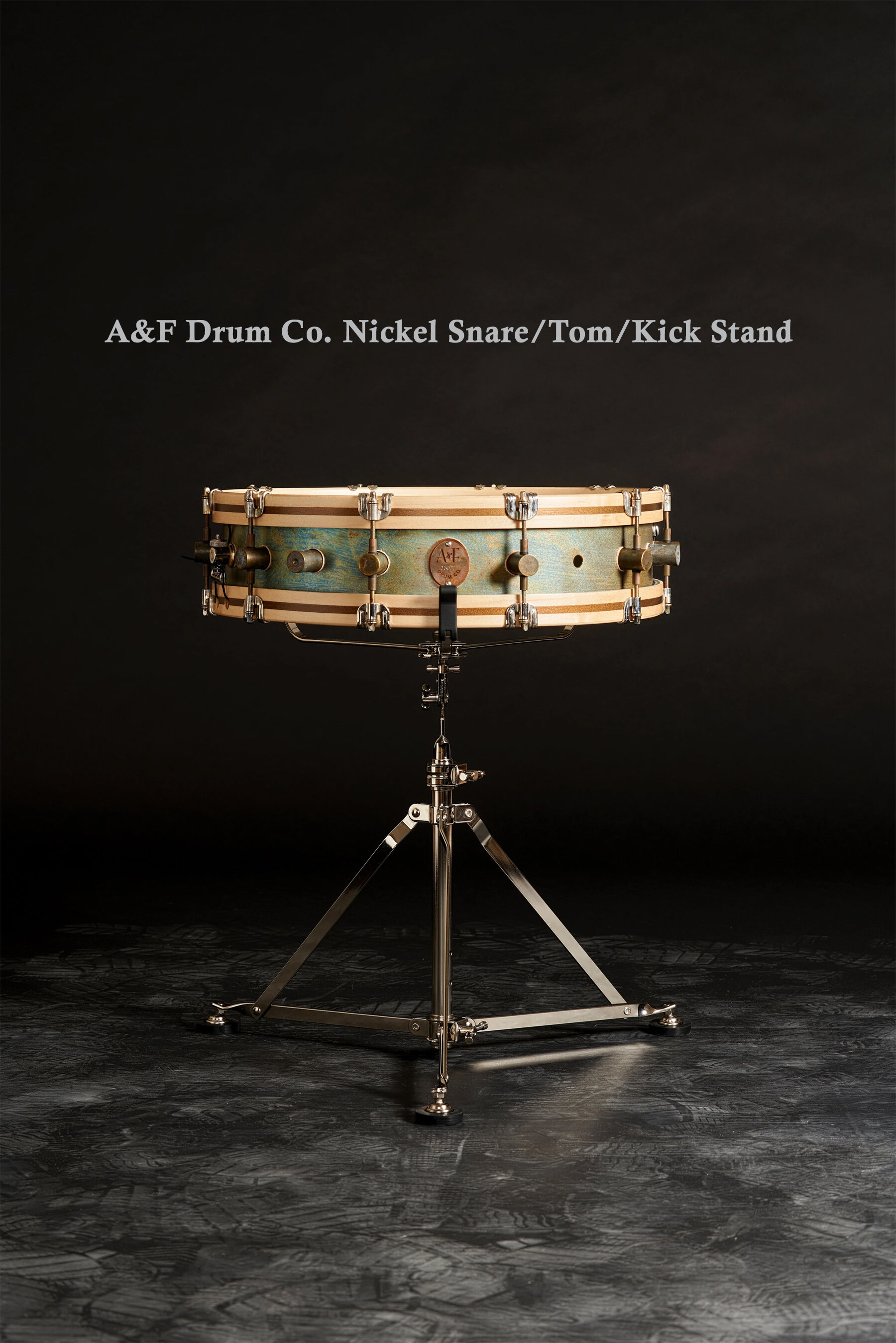
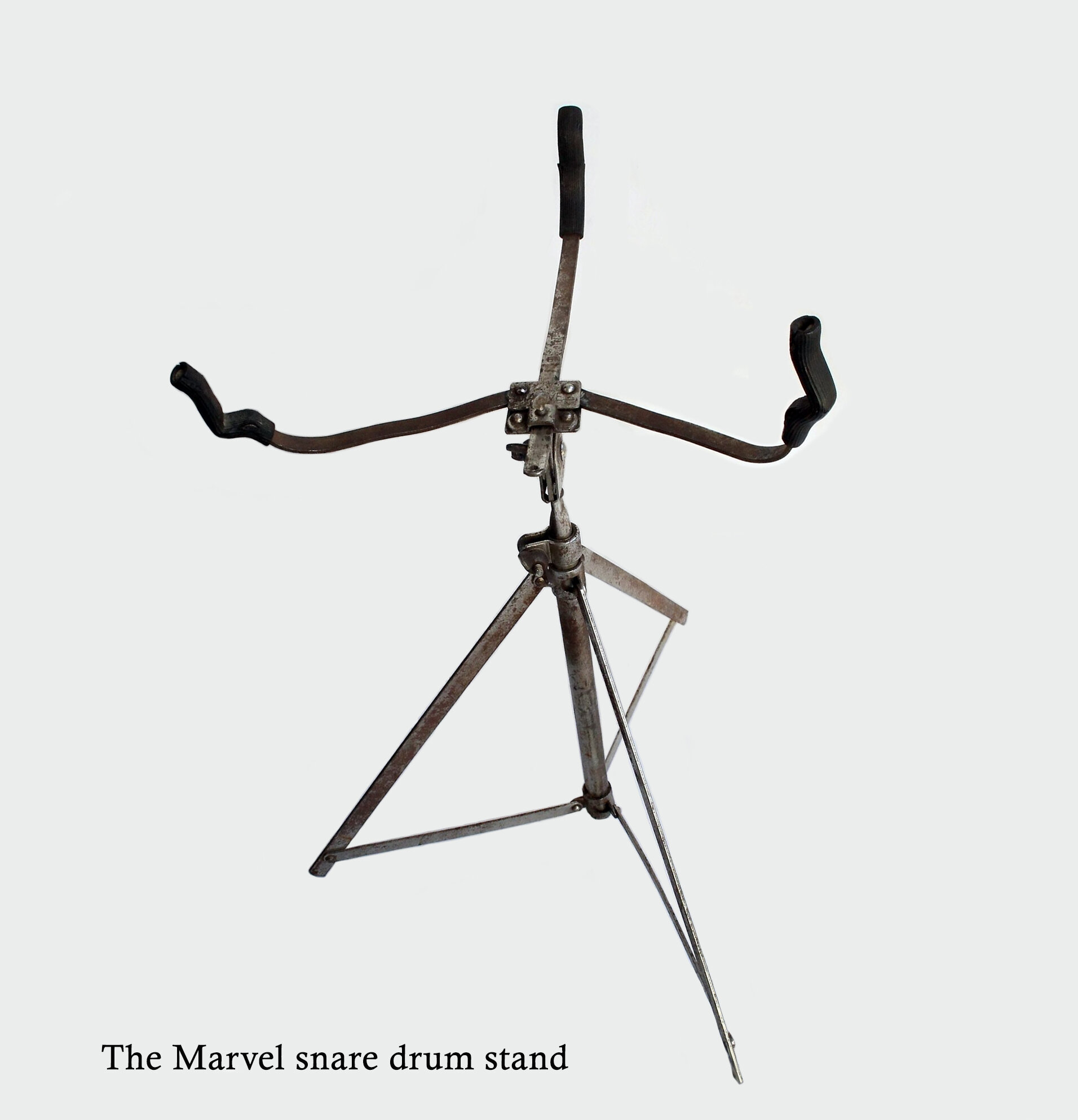
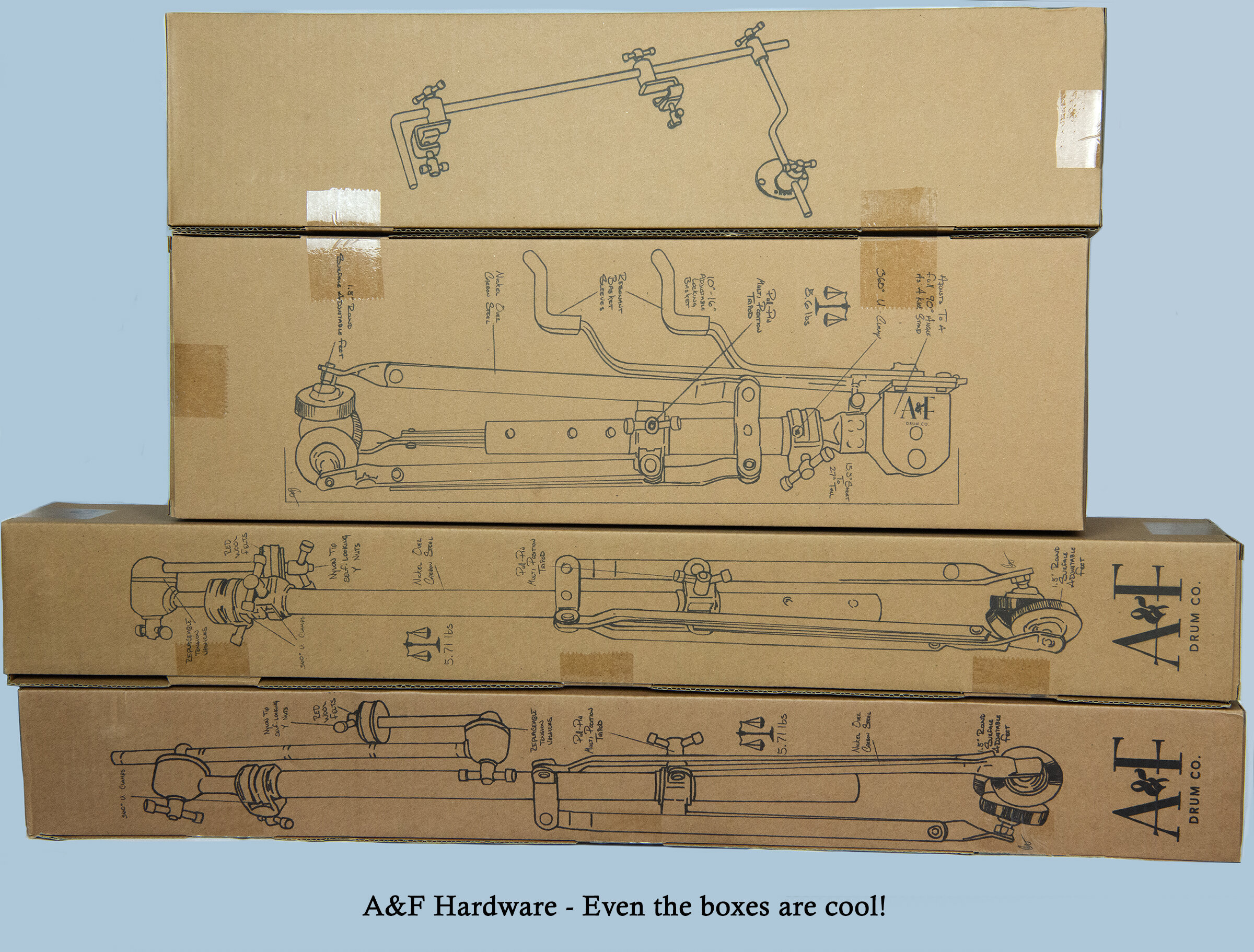
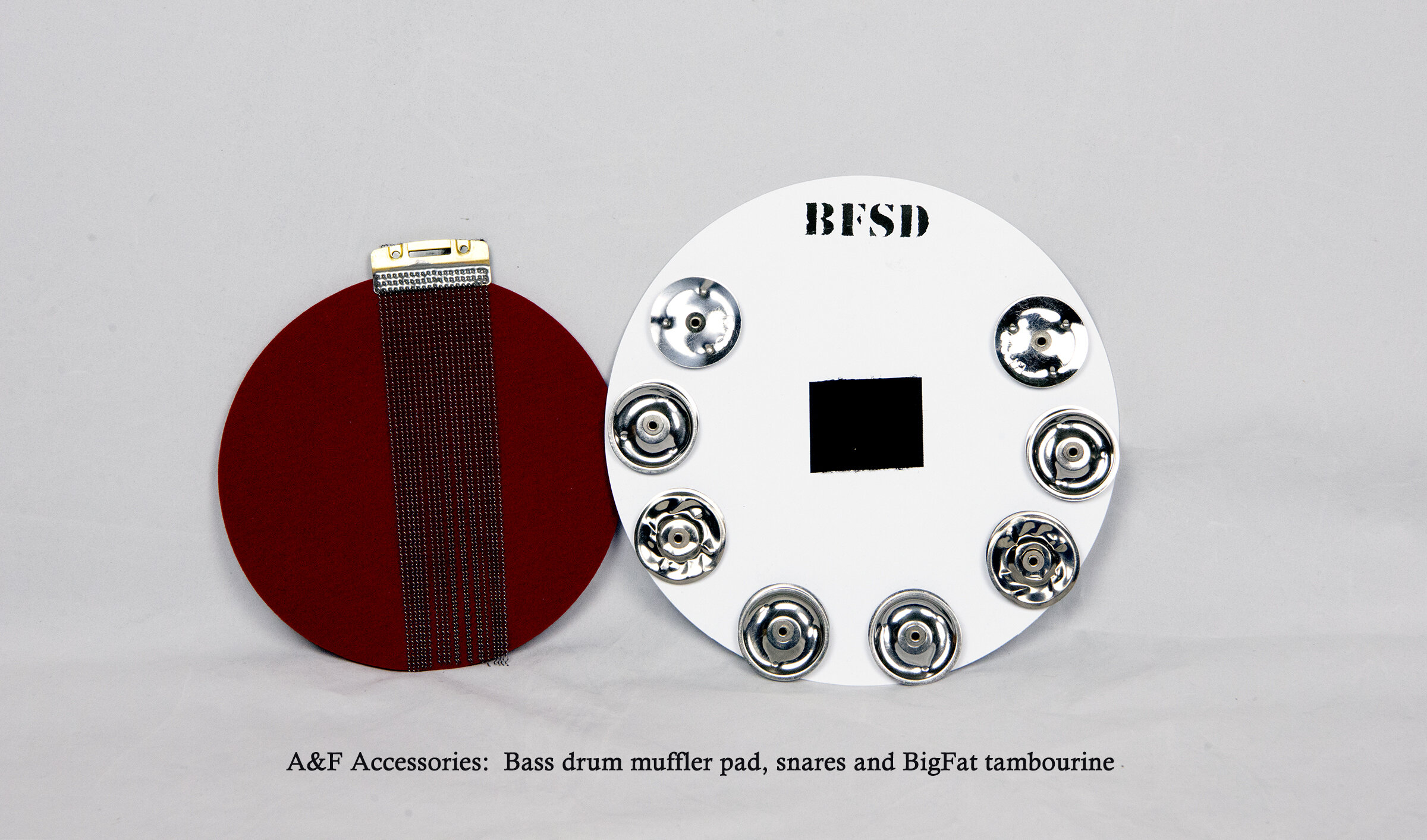
Ramy does not rest on his laurels. Constantly looking to do more and do better, he has recently expanded the A&F line-up to include an array of innovative nickel-plated drum hardware: snare/tom/kick stand, cymbal stand, pedal mount for snare stand, hoop mounted clamp and L-arm, kick-bone, cocktail basket and kick pedal clamp.
Read moreReview and video: No Nuts Cymbal Sleeves, CymRings & SizzleNut
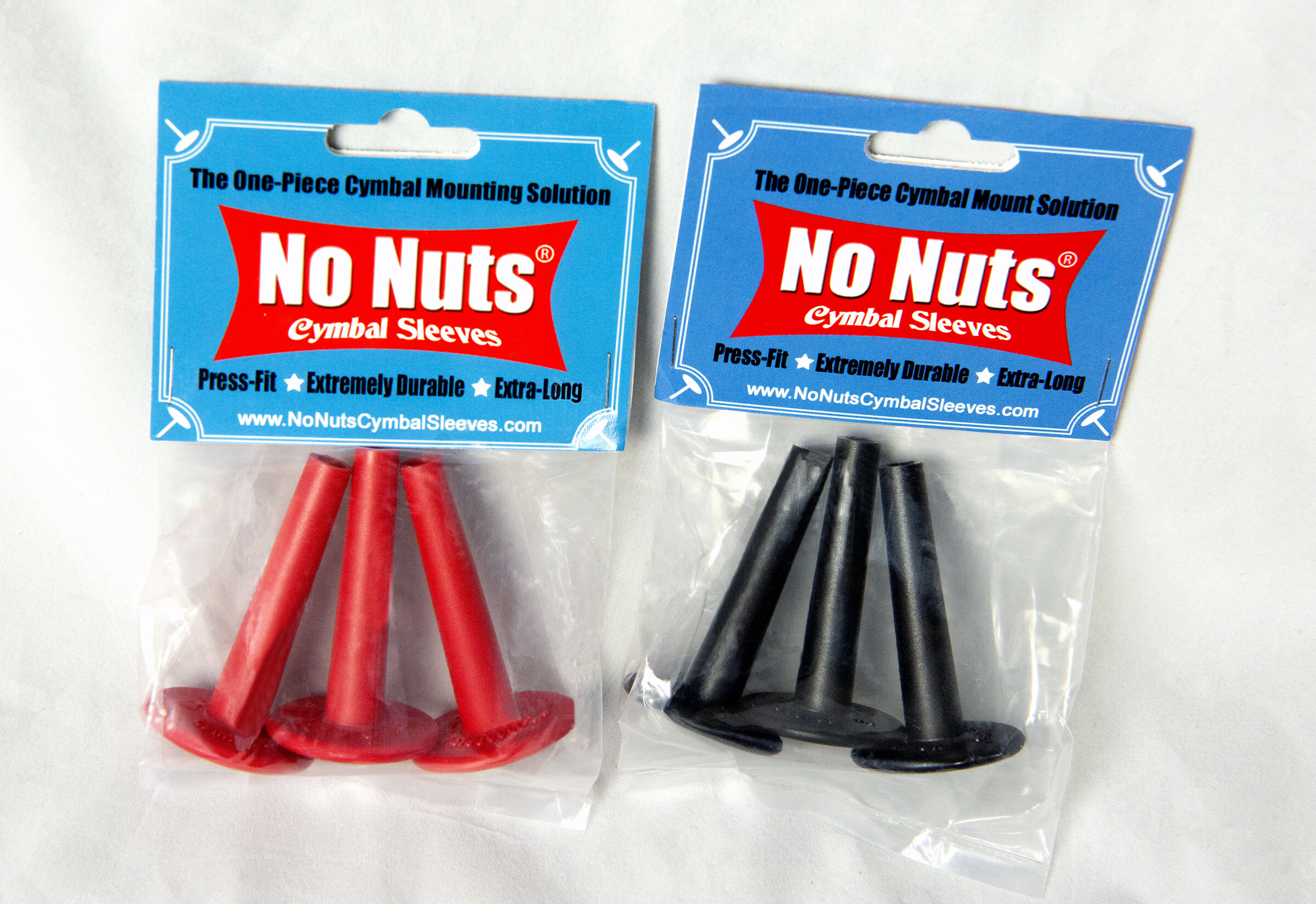
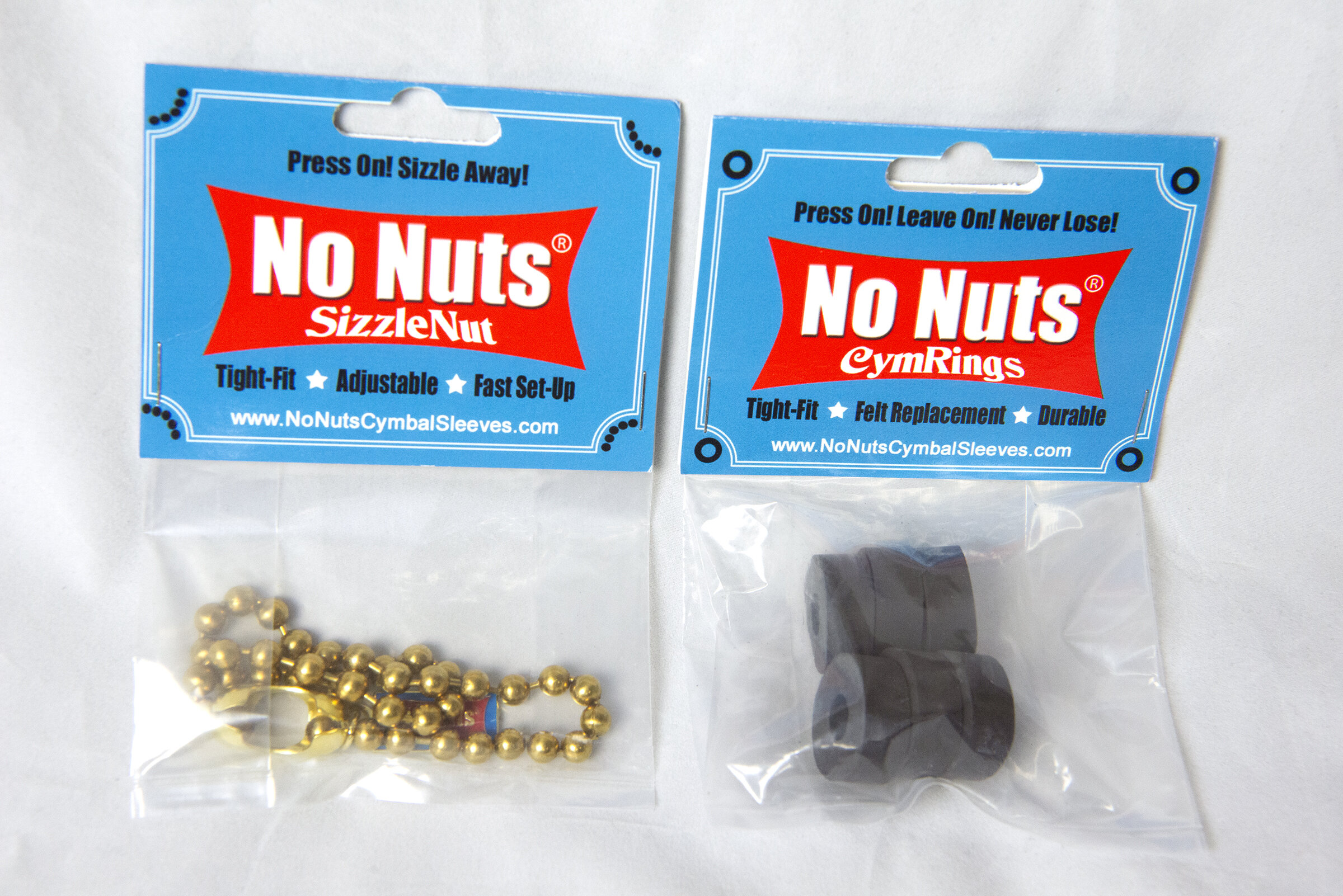
So overall, I would definitely recommend trying out the No Nuts products, especially the Cymbal Sleeves, as they really do make mounting and dismounting cymbals so much easier and quicker. The convenience factor is well worth the money in my mind. I like having alternatives to felt pads so the CymRings are a much better substitute. I don’t use a sizzle cymbal enough to justify the cost. Having a little ‘doodad’ like the SizzleNut that I can stick in my bag and pull out as needed is more practical. Think of it this way, for the price of 1-2 pairs of drumsticks, you could buy a set of Cymbal Sleeves, CymRings, or SizzleNut. Music is about experimentation. Try things out!
Read moreThe Drum Engravers, Part 3: Mike Morgan
I’d like to share some of our conversations in order for you to get to know Mike as I did, describe a few examples of his work, and also explain how his approach differs from that of other gifted hand engravers, like John Aldridge and Adrian Kirchler.
Read moreThe Drum Engravers, Part 2: John Aldridge Custom Works
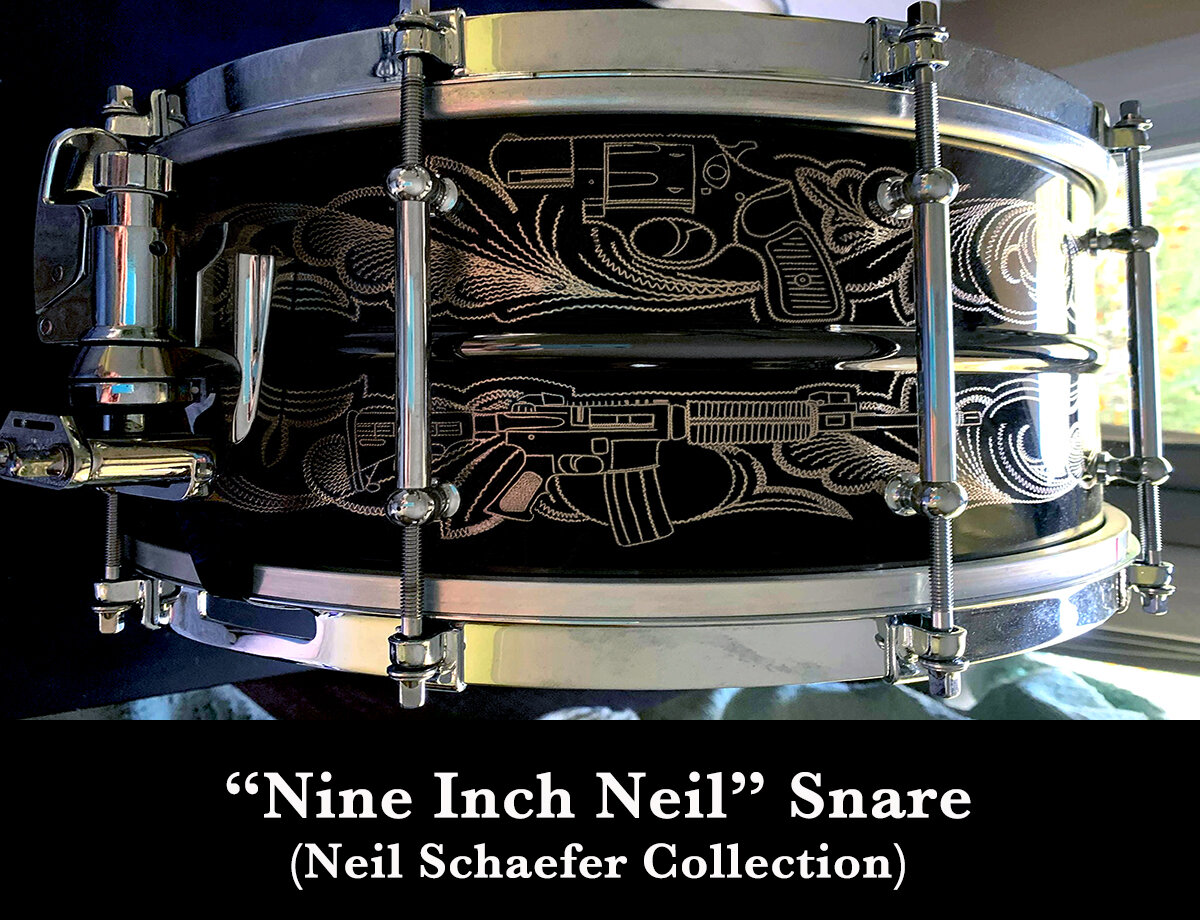
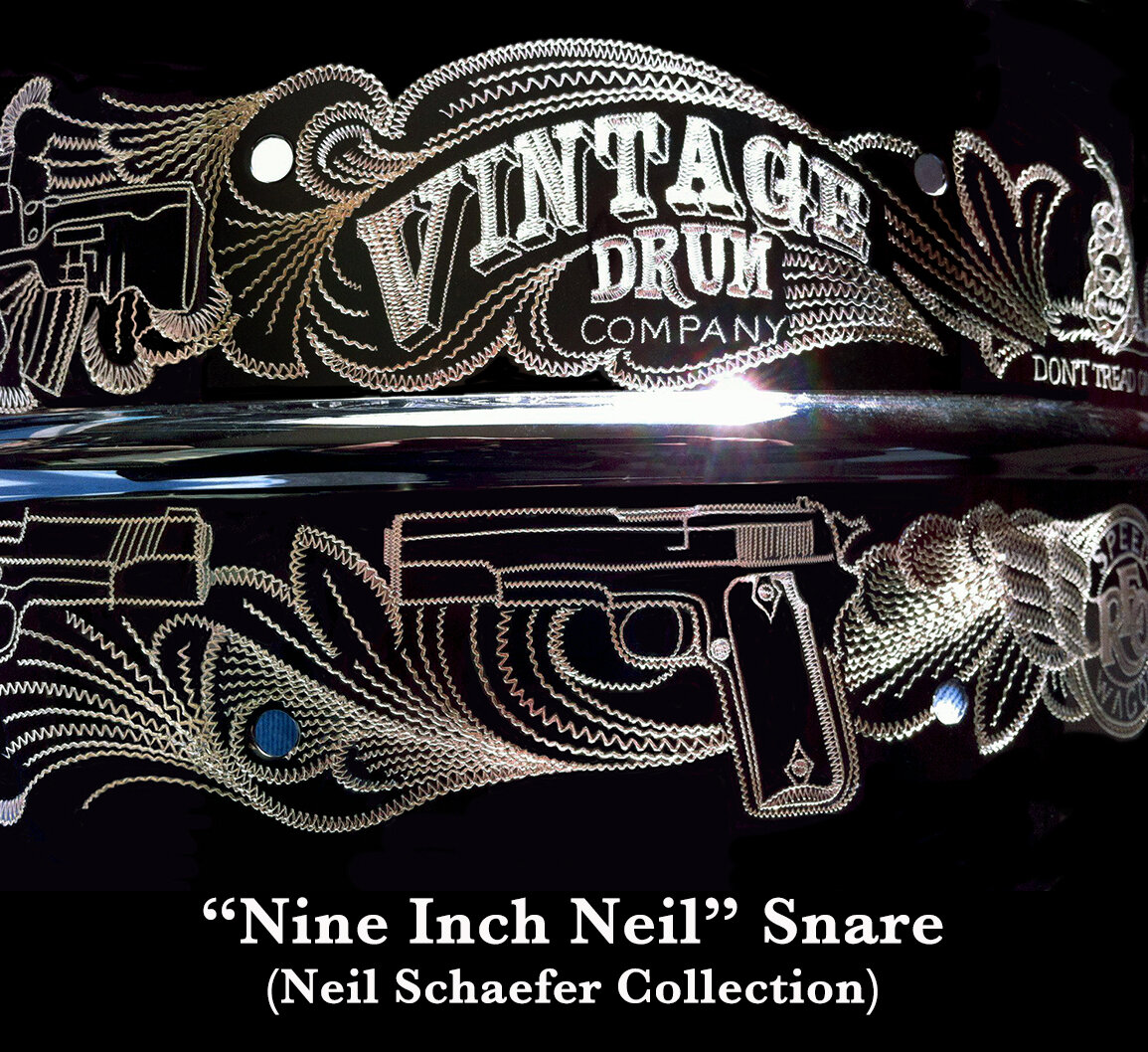
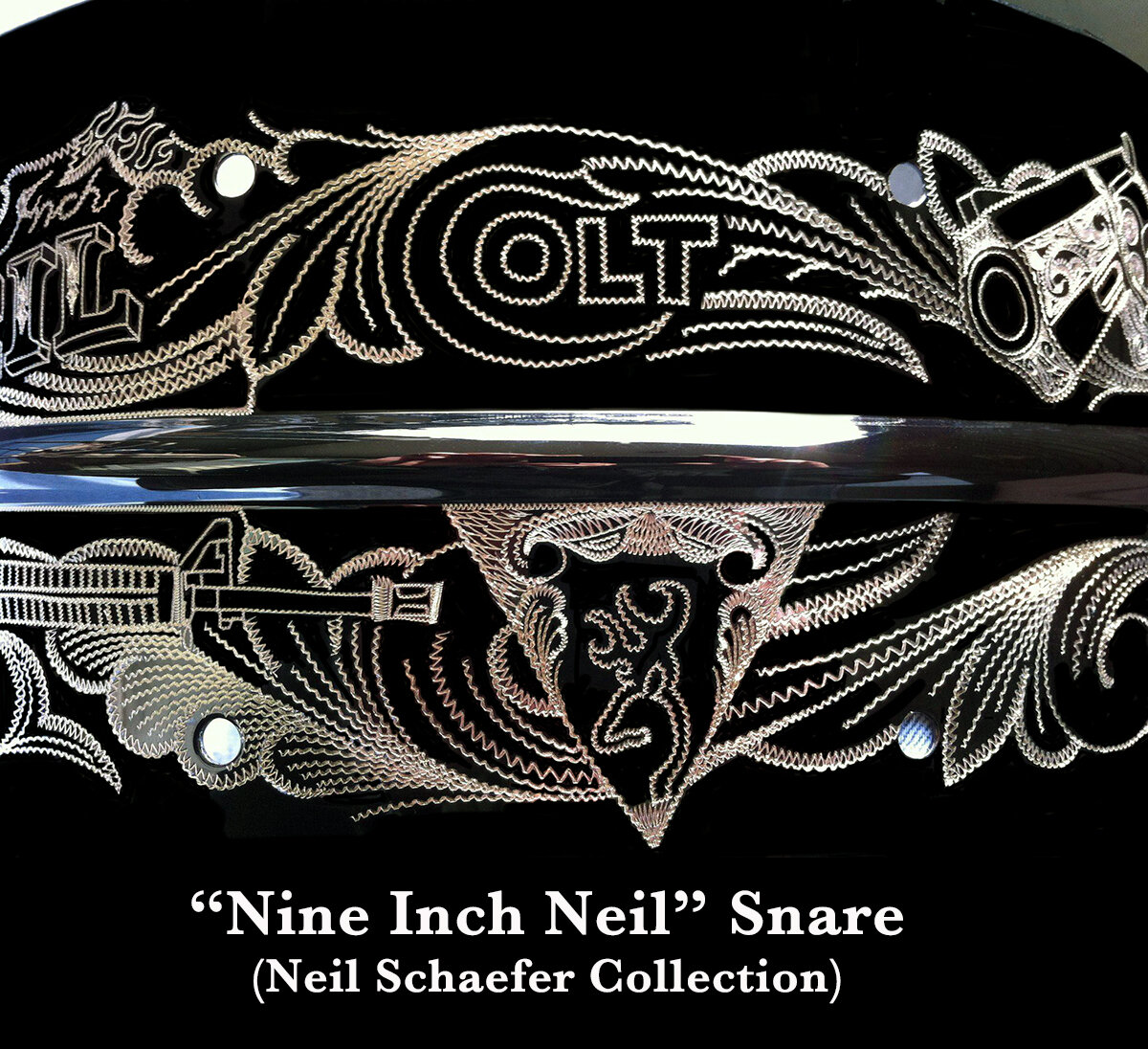
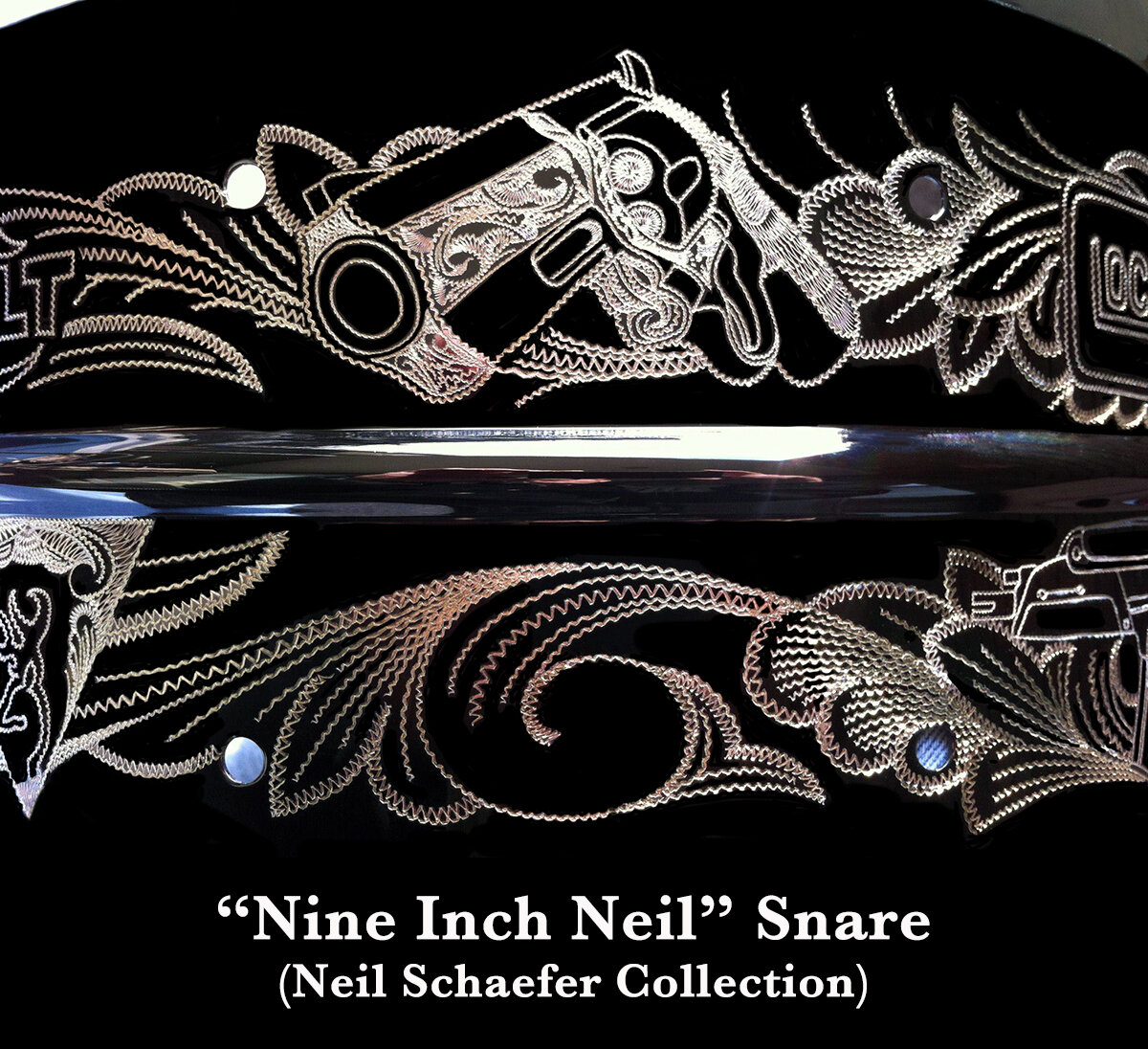
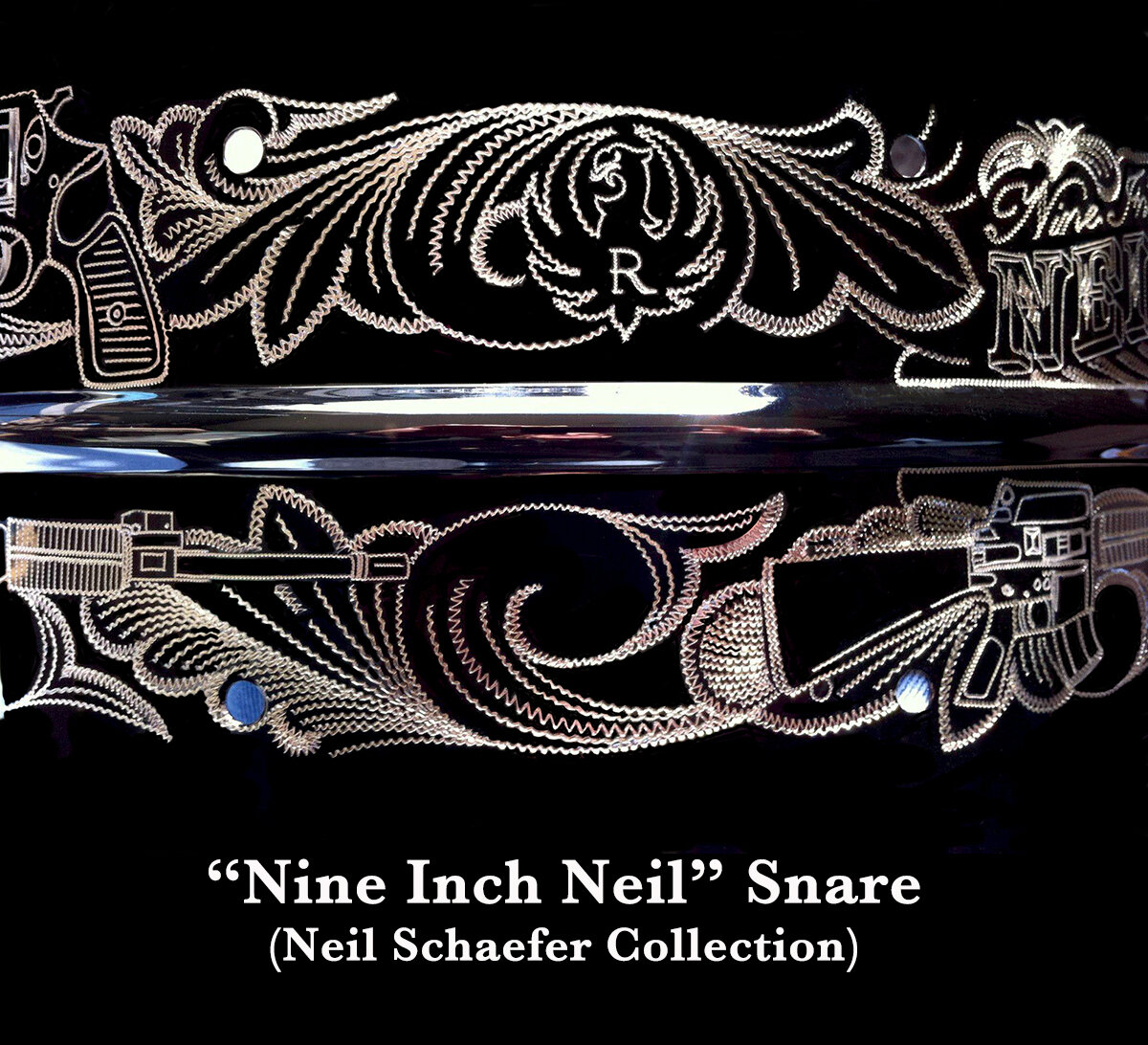
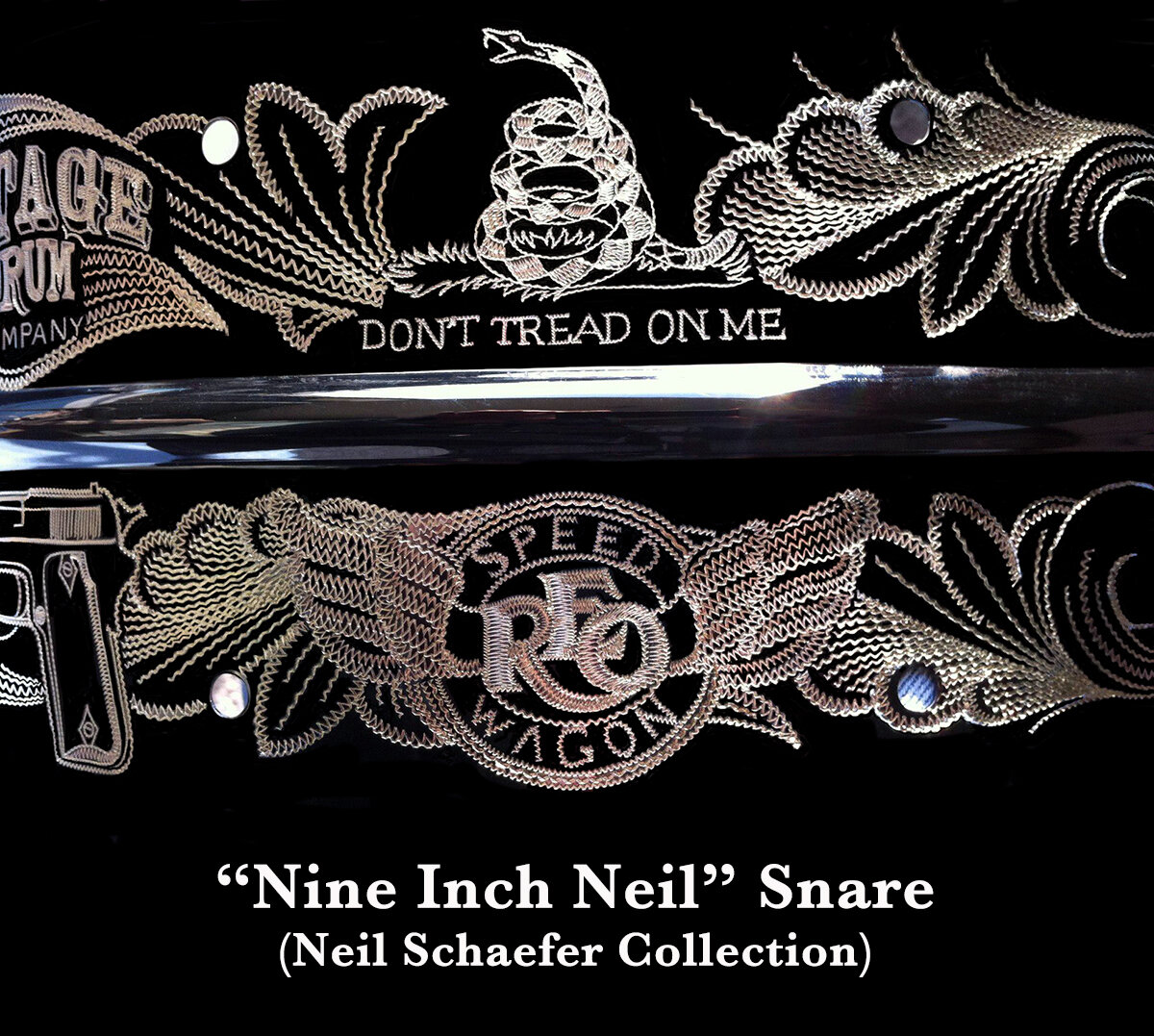
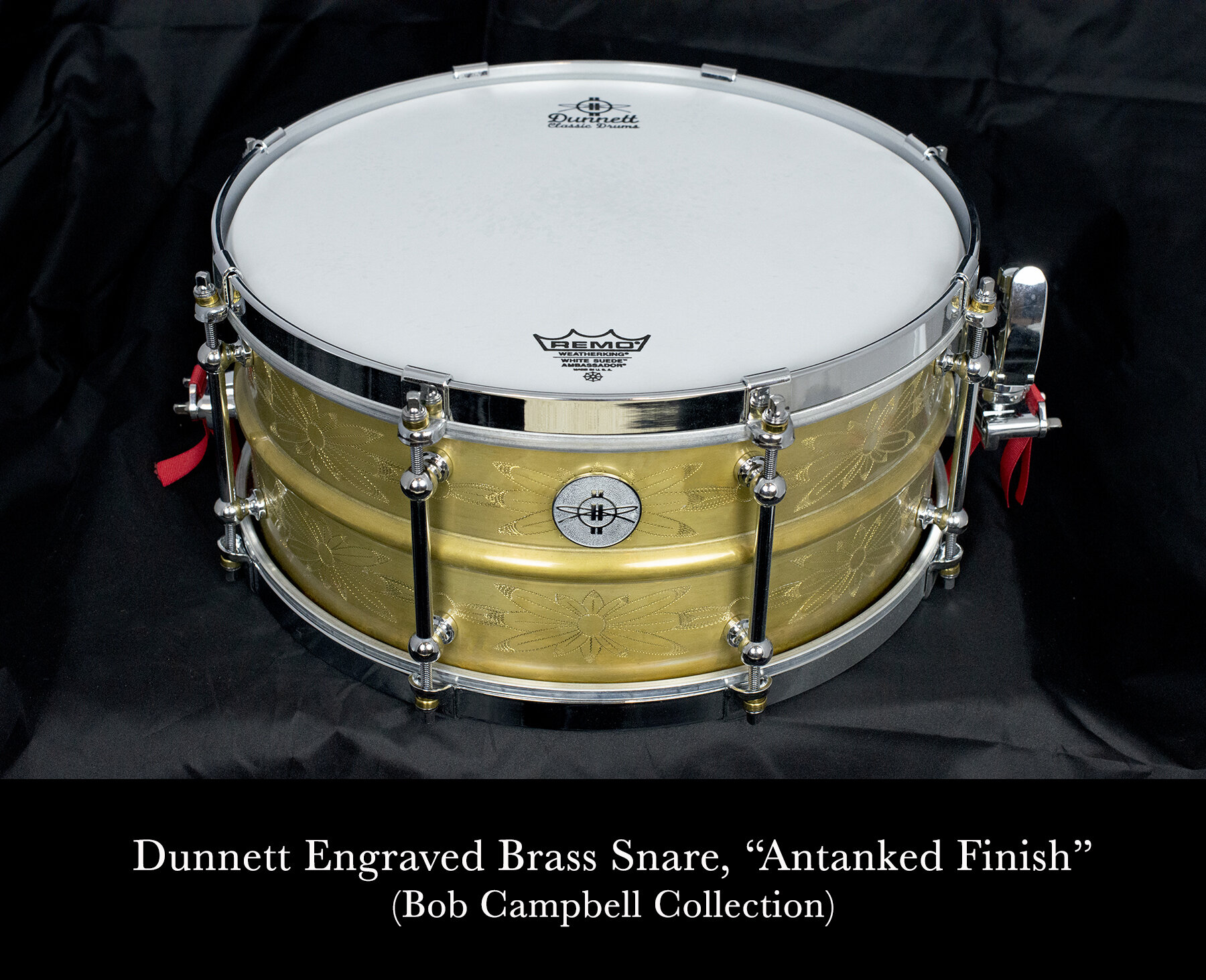
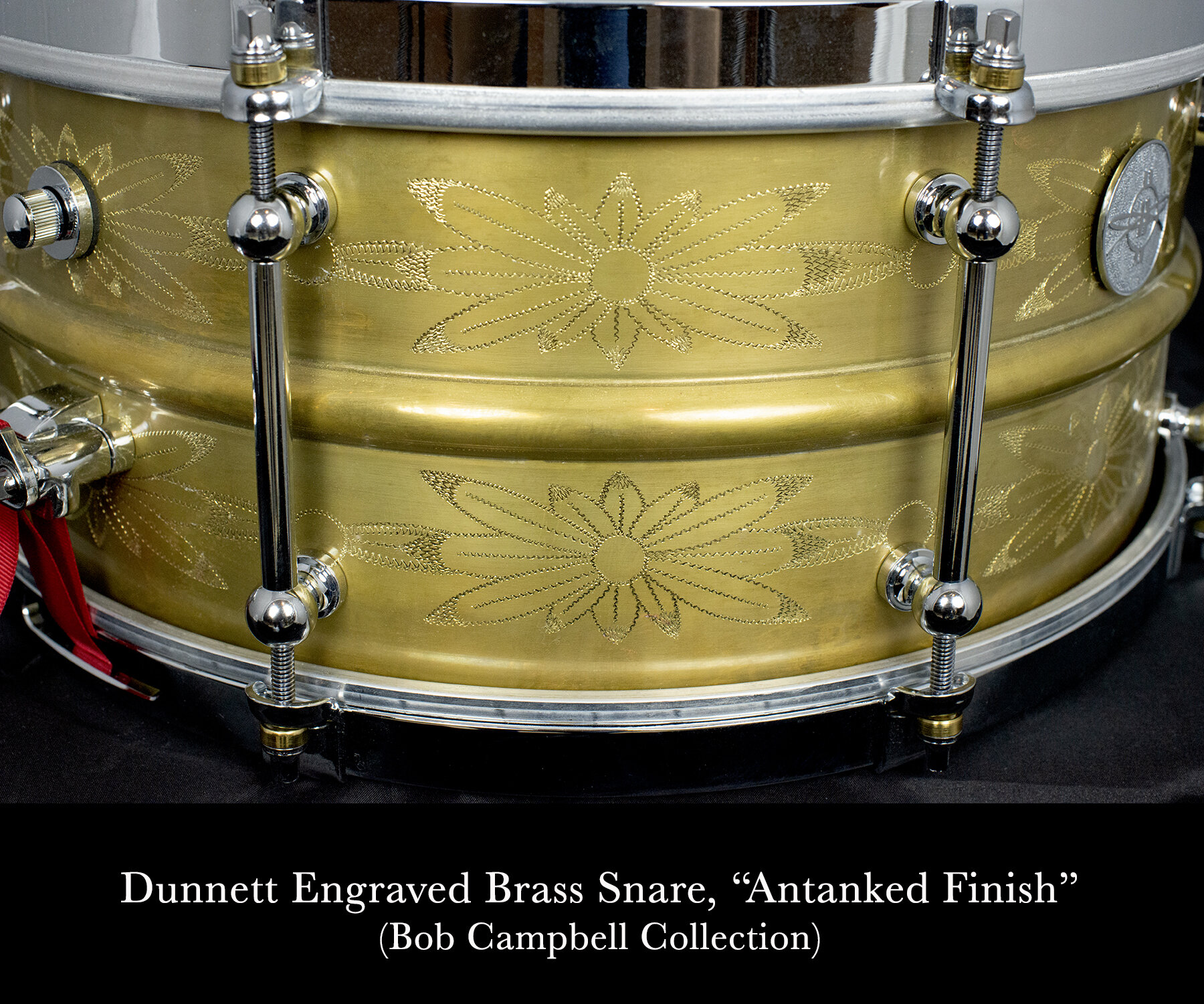
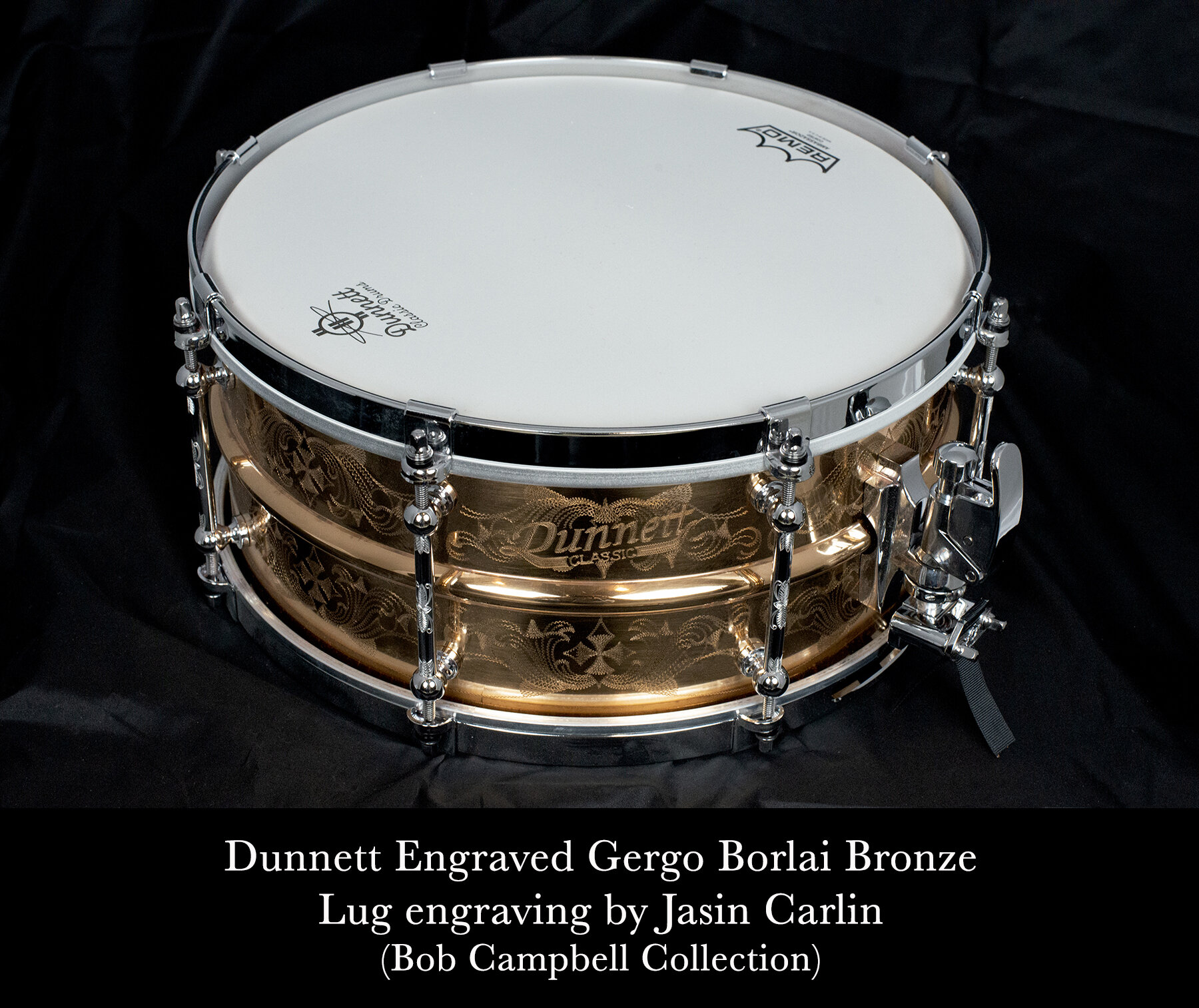
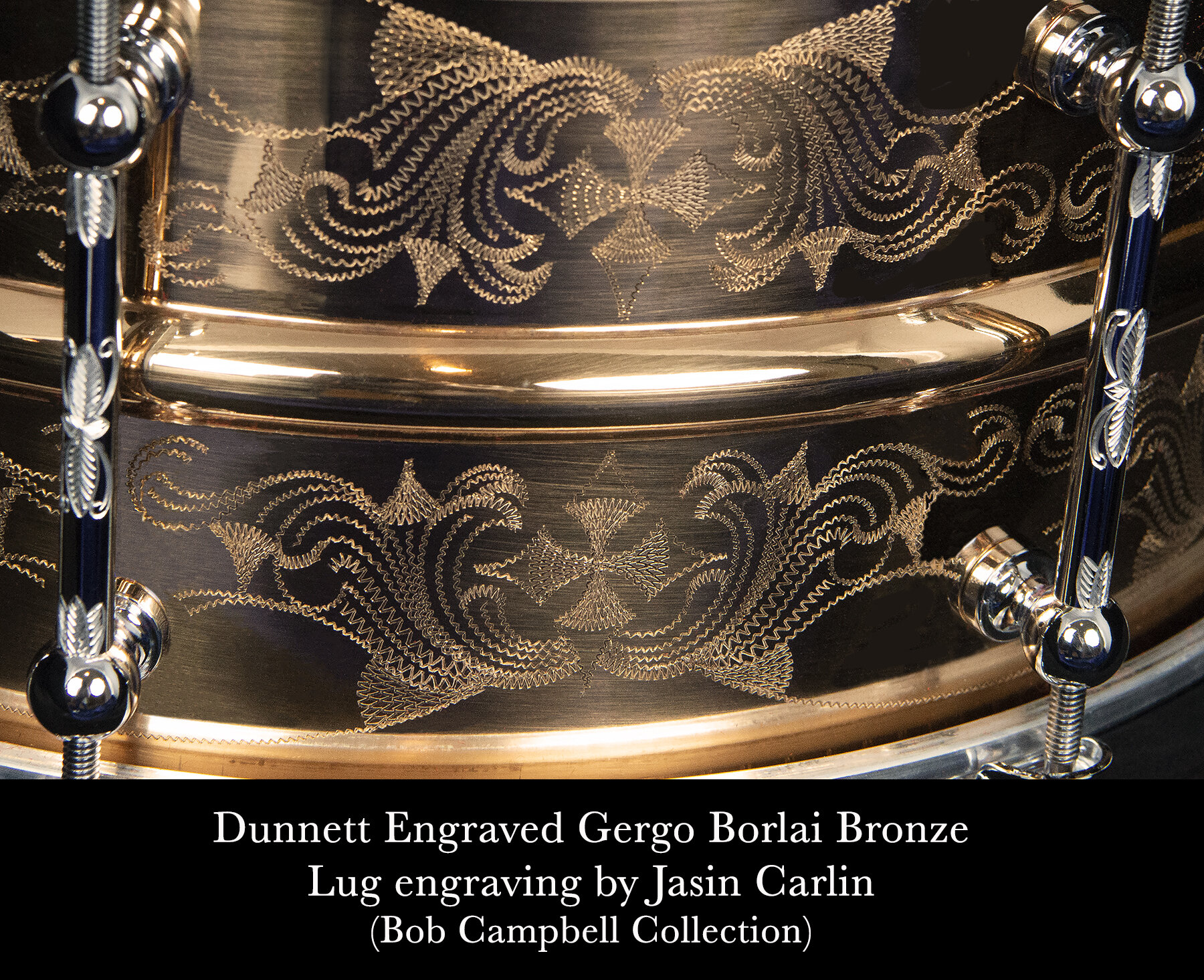
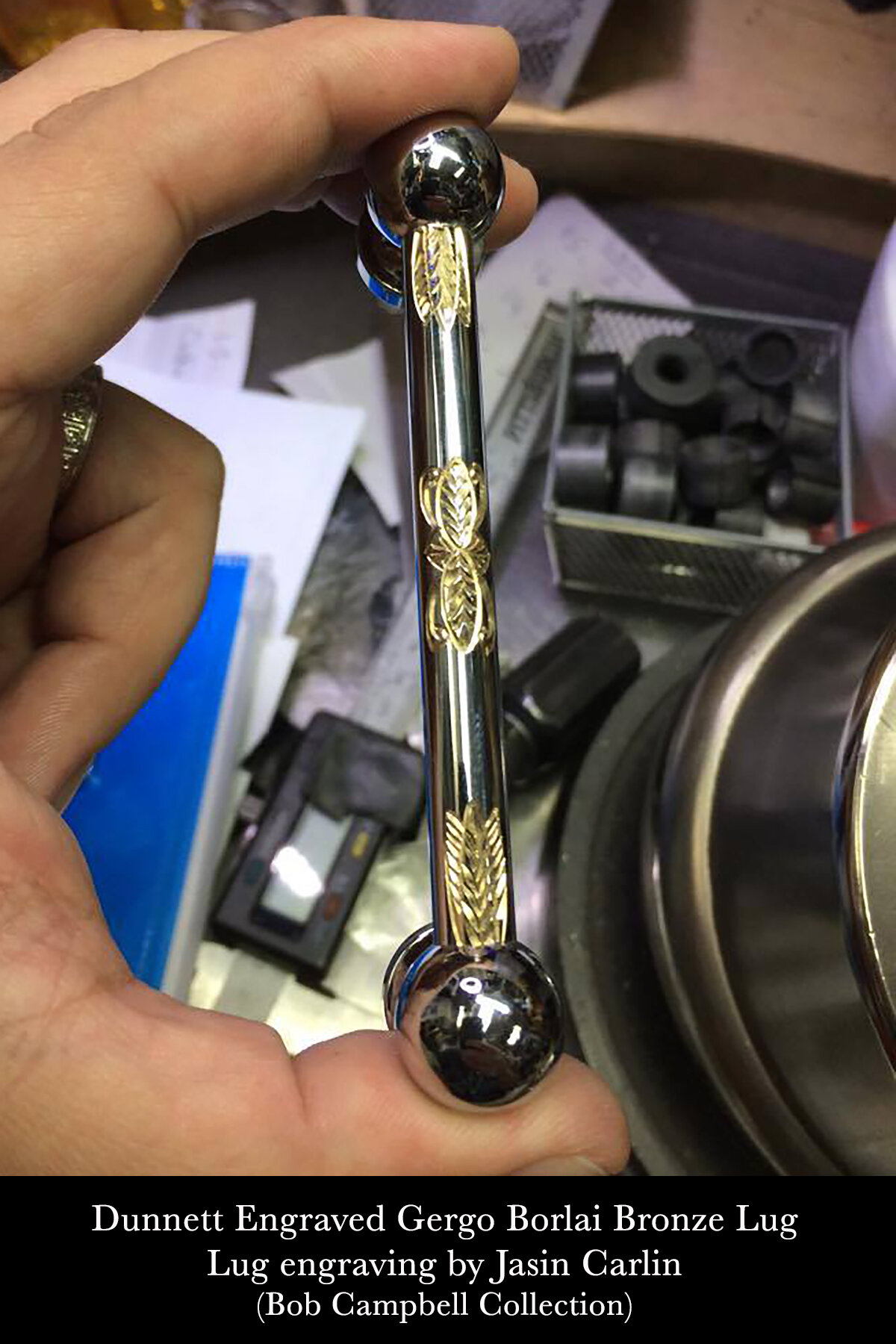
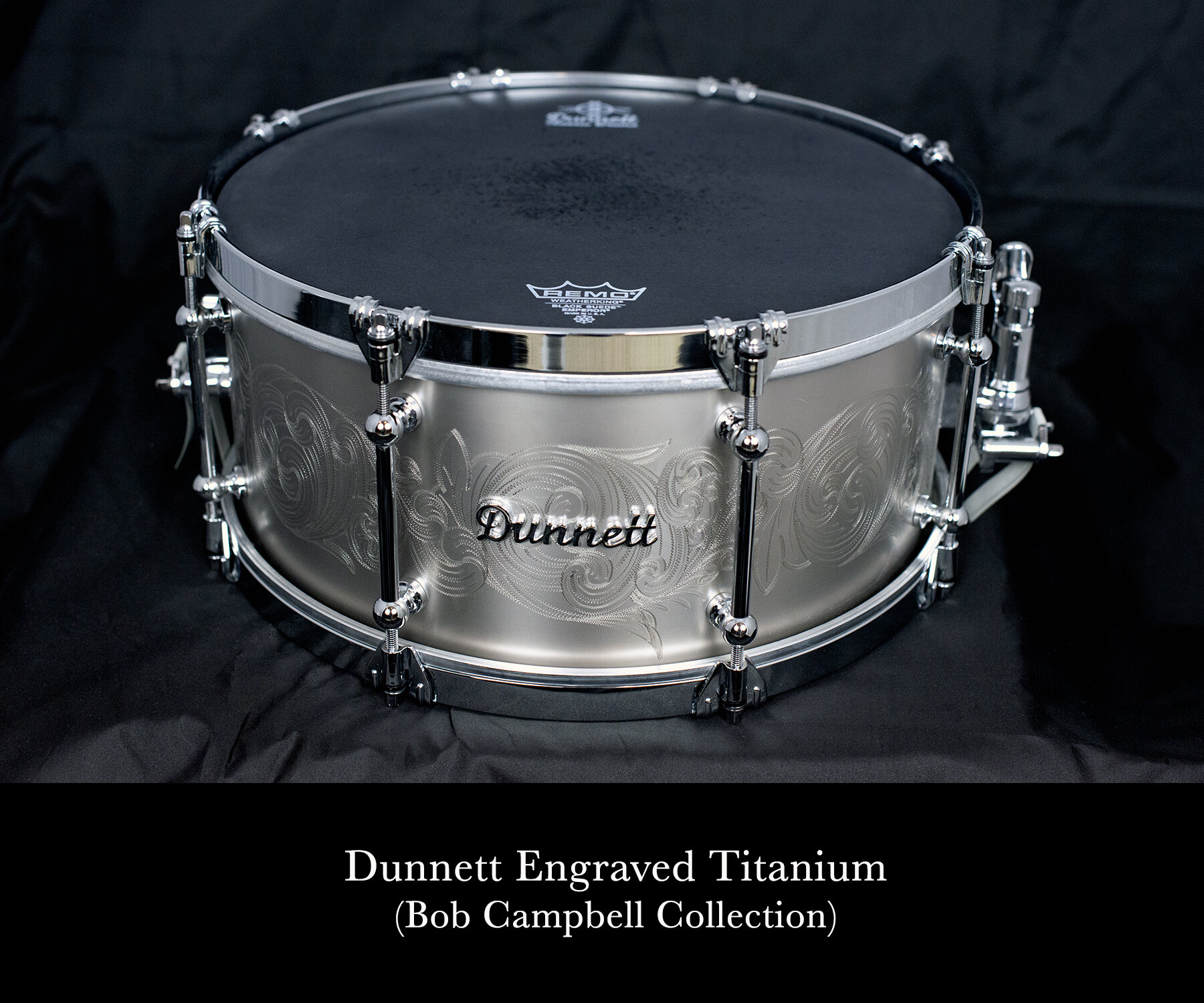
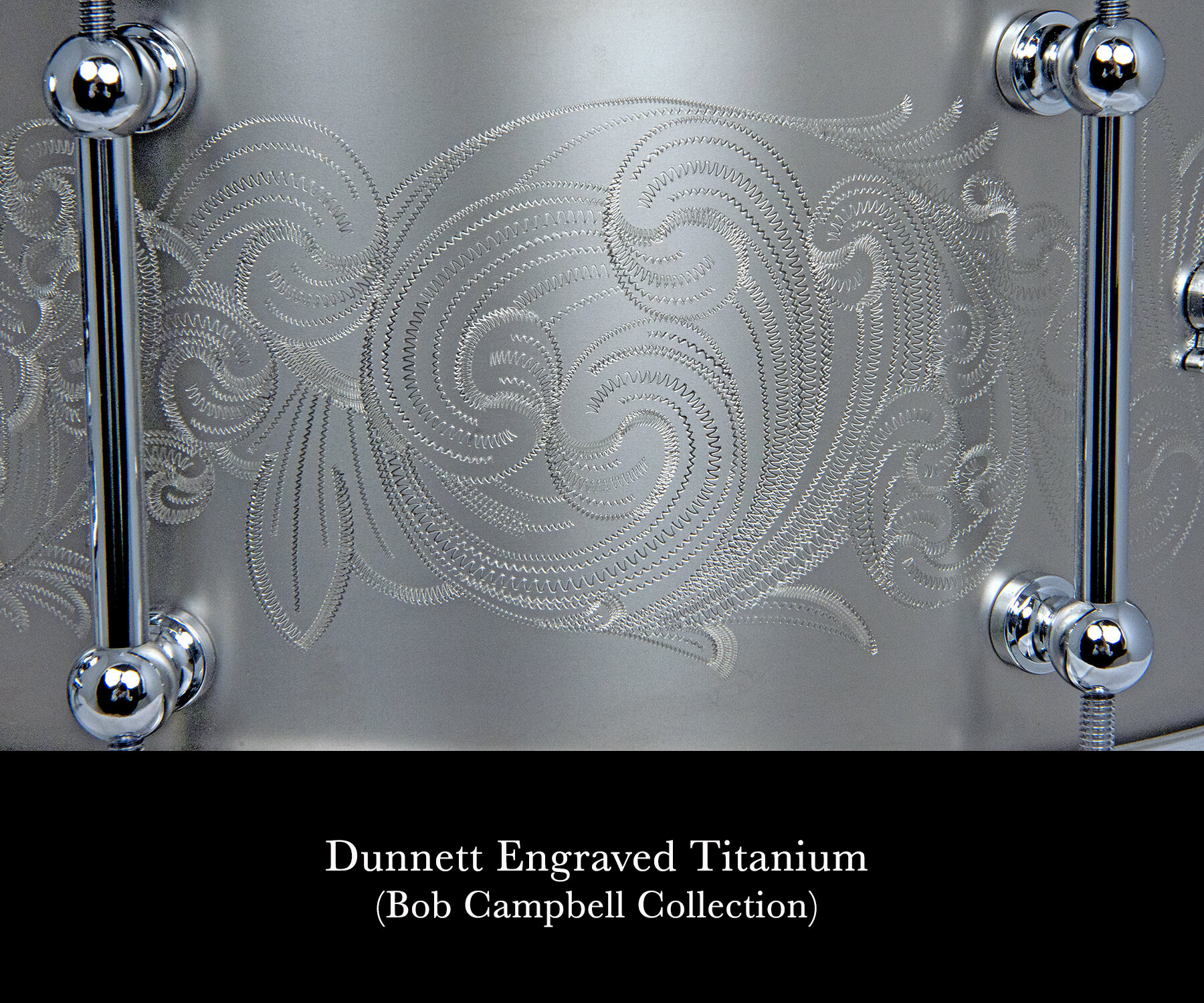
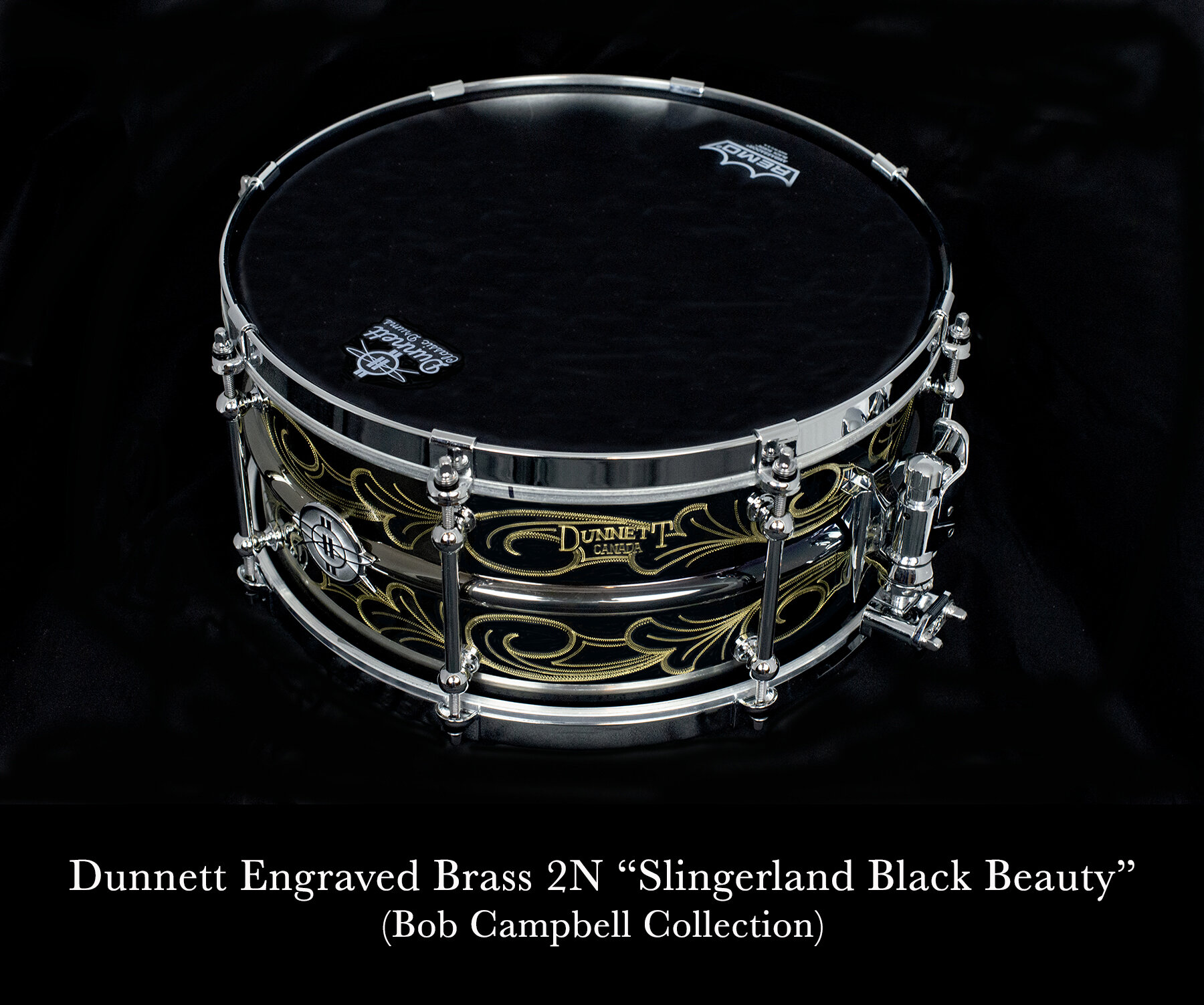
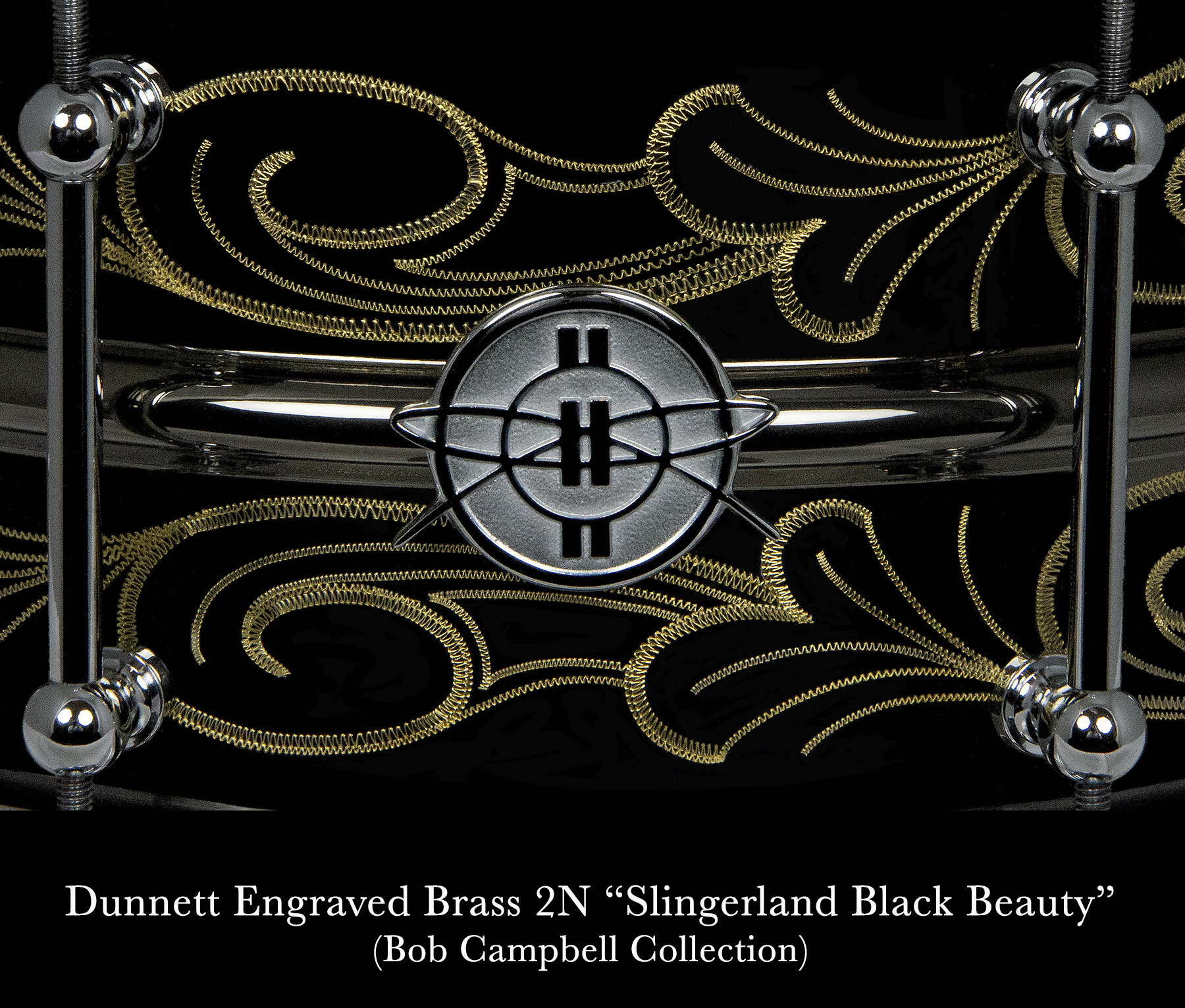
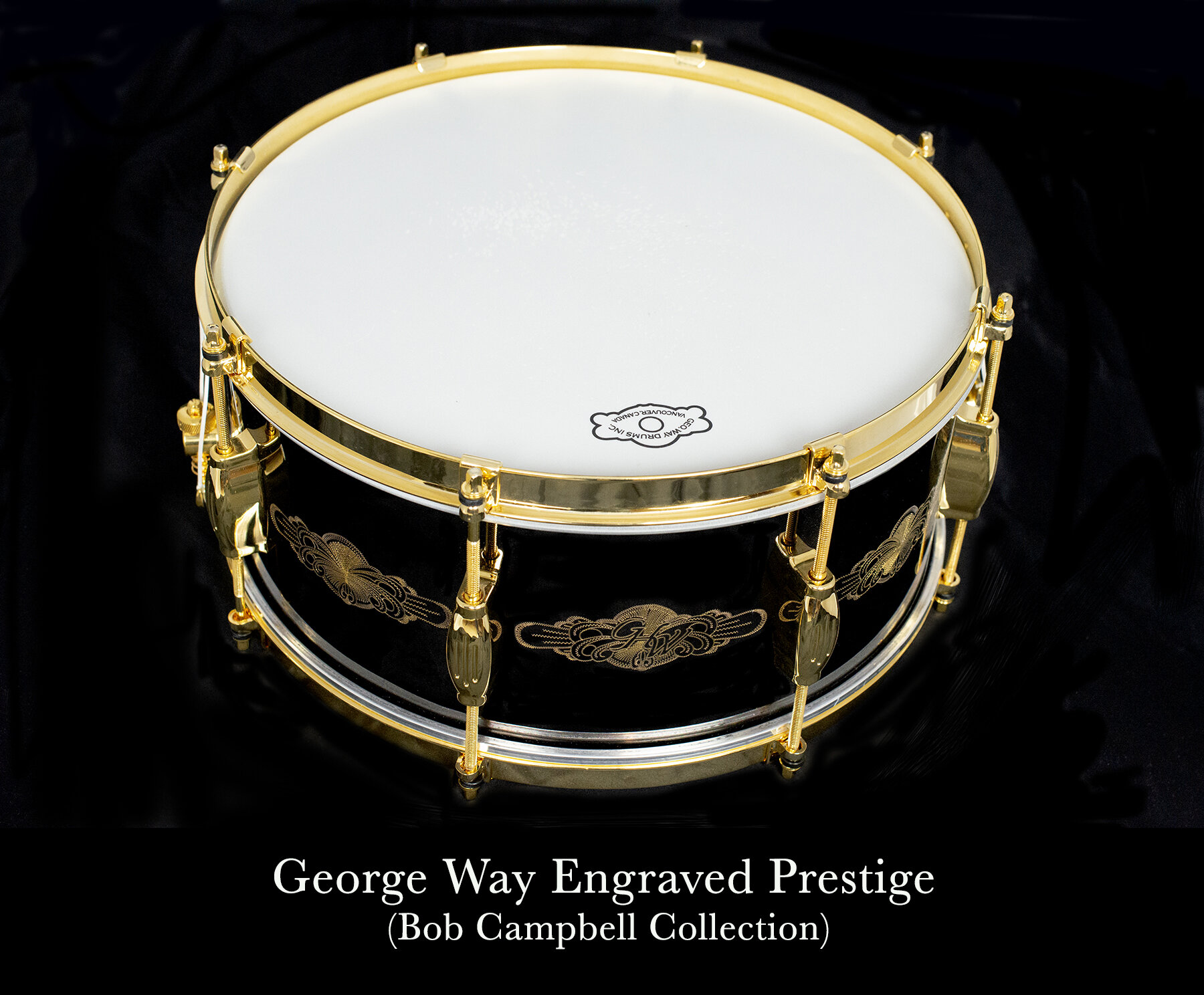
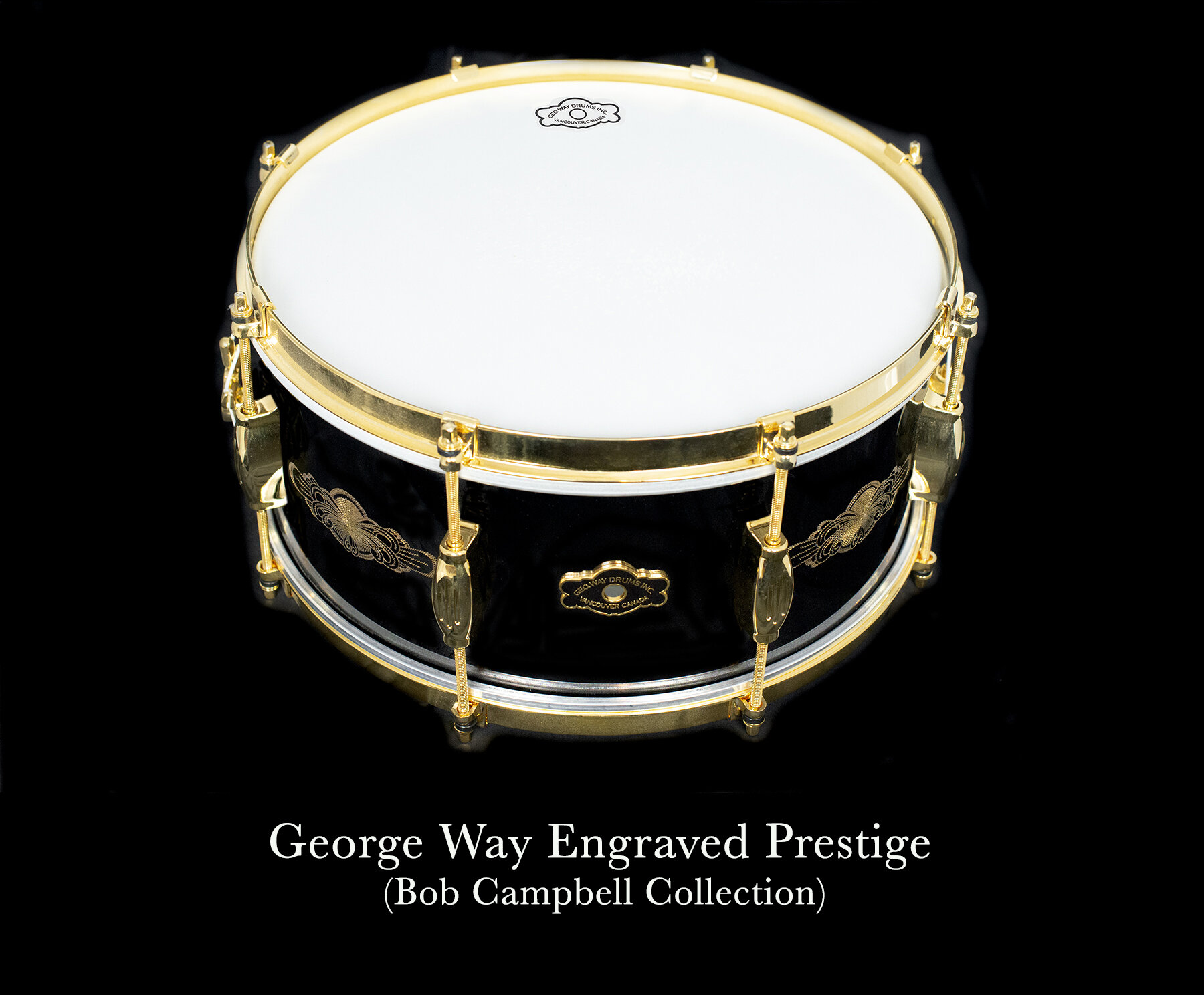
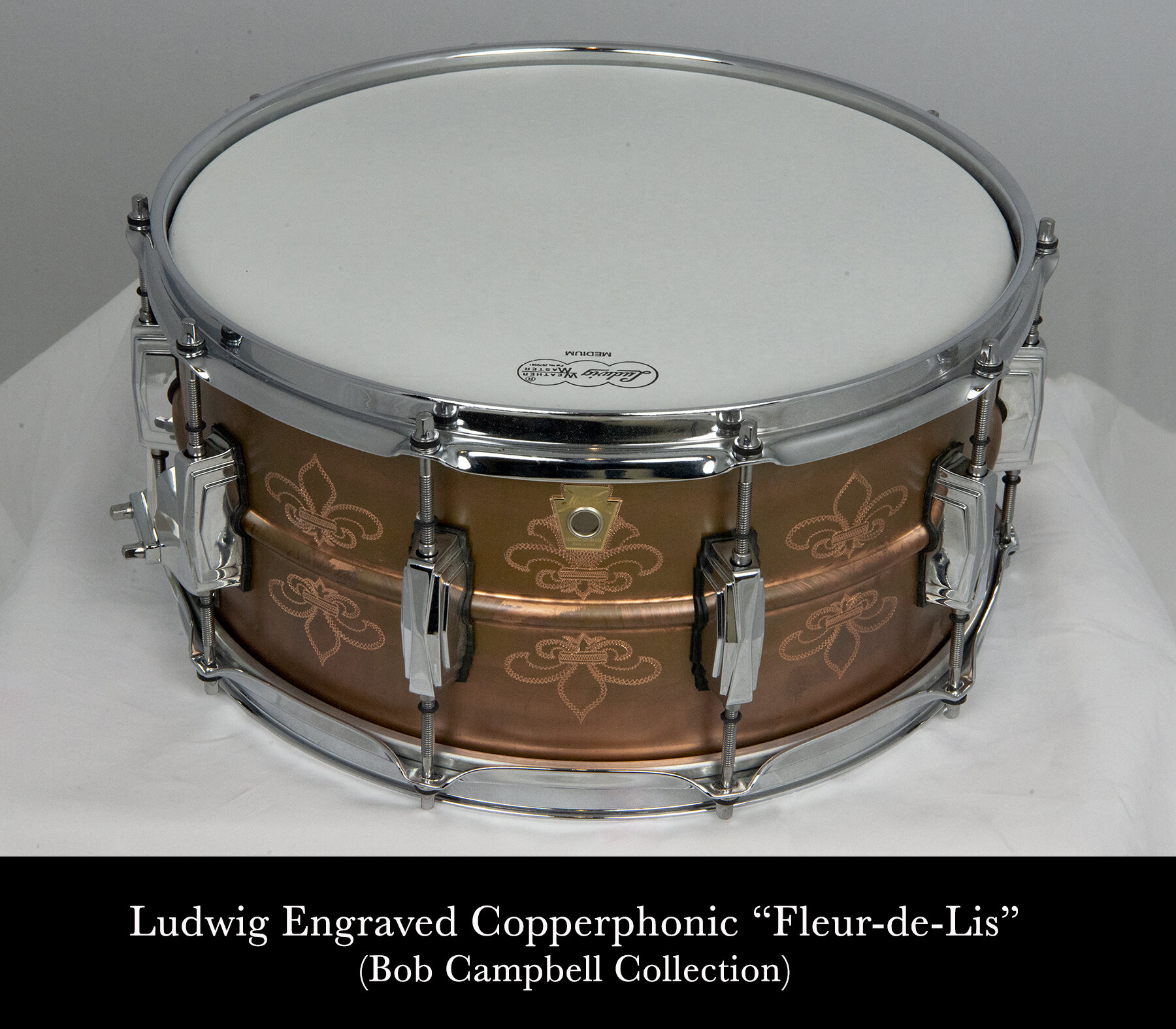
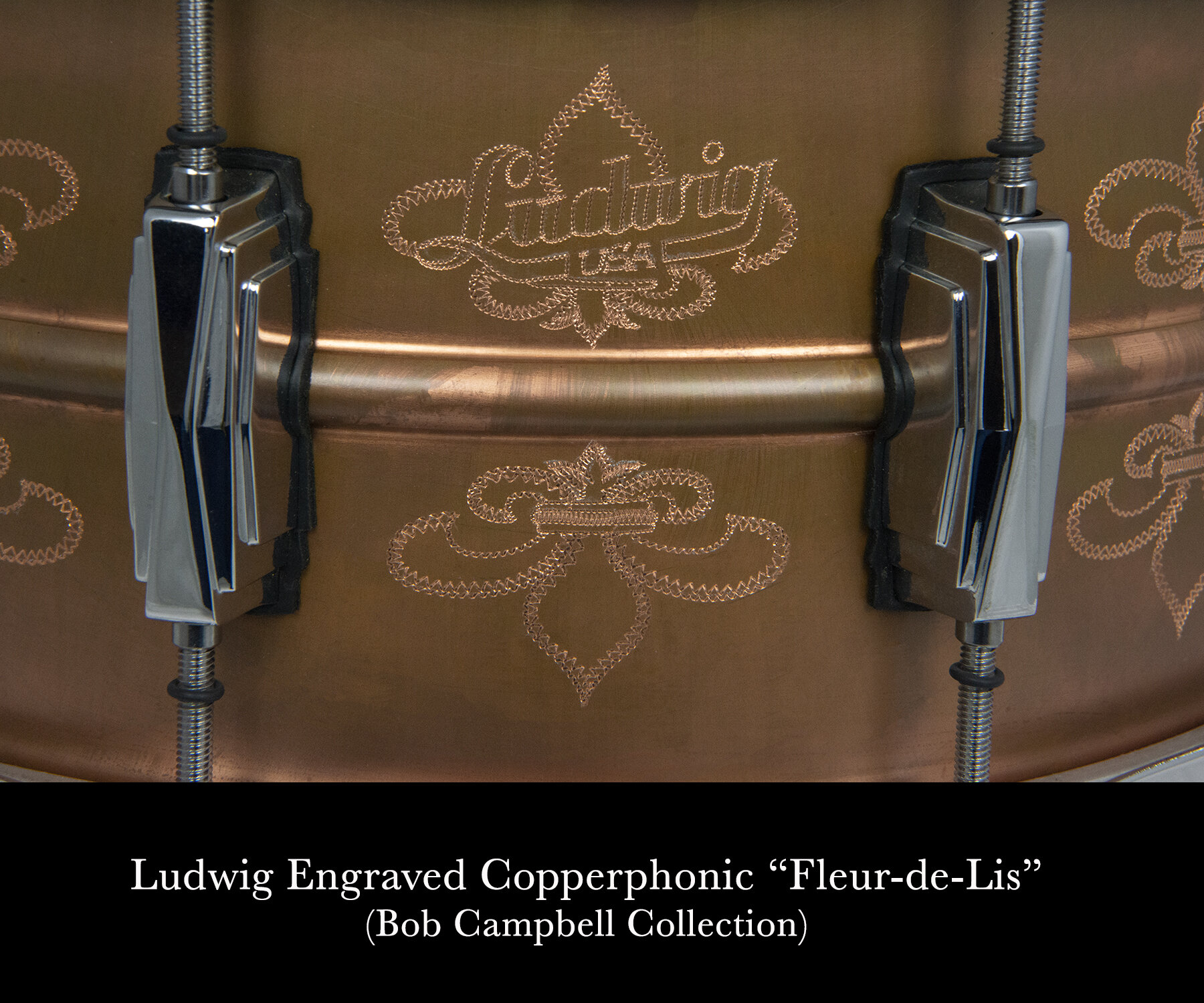
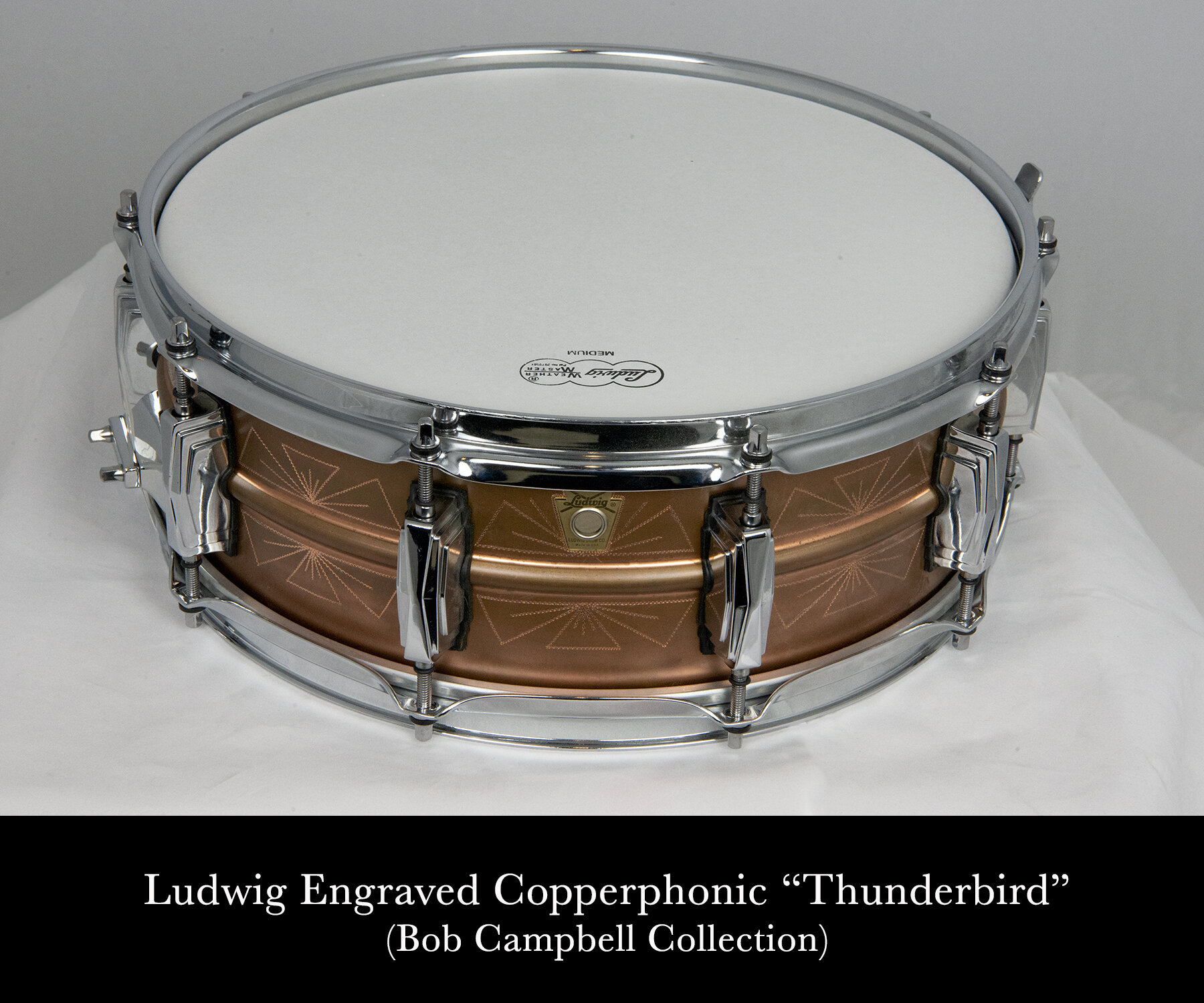
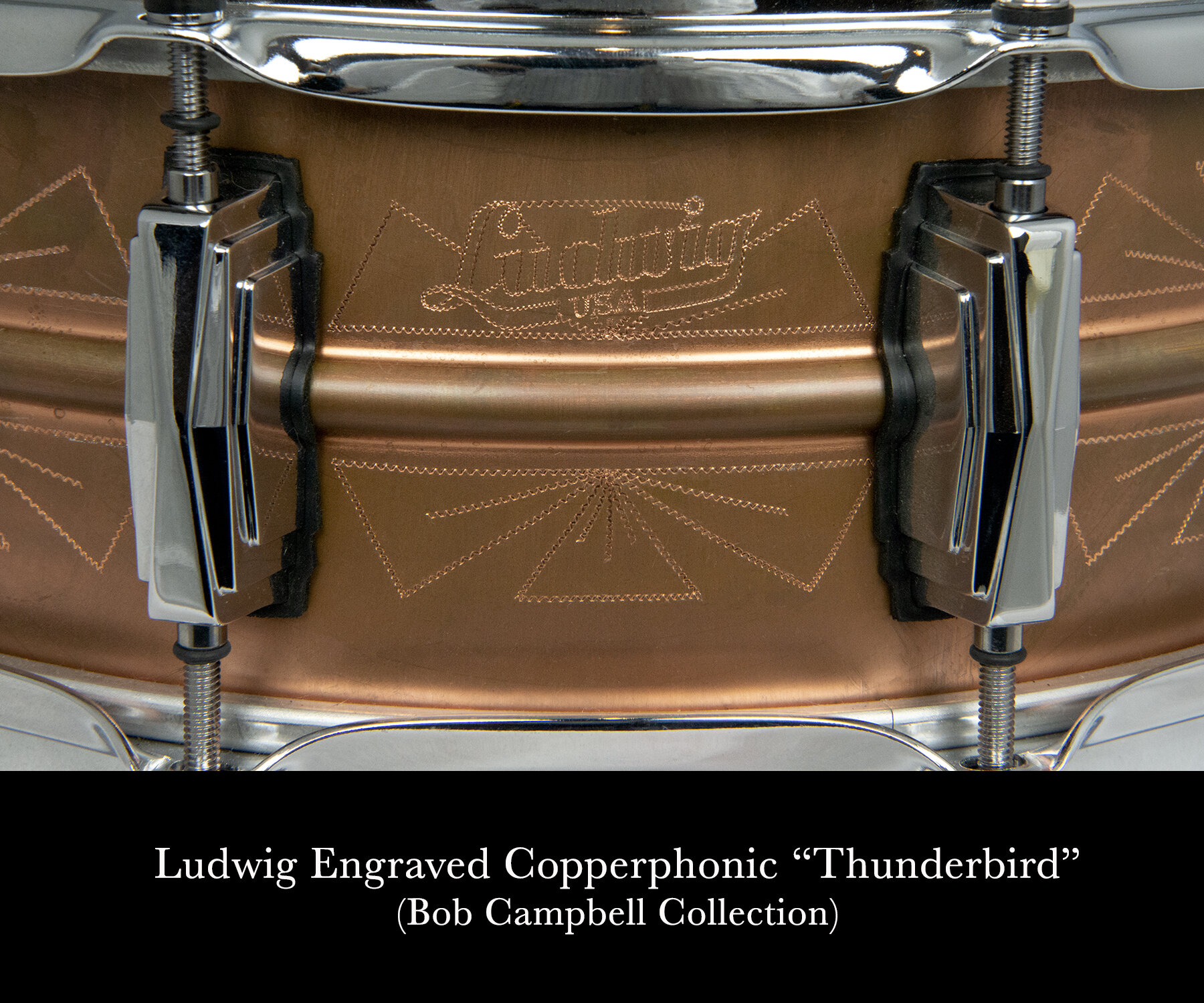
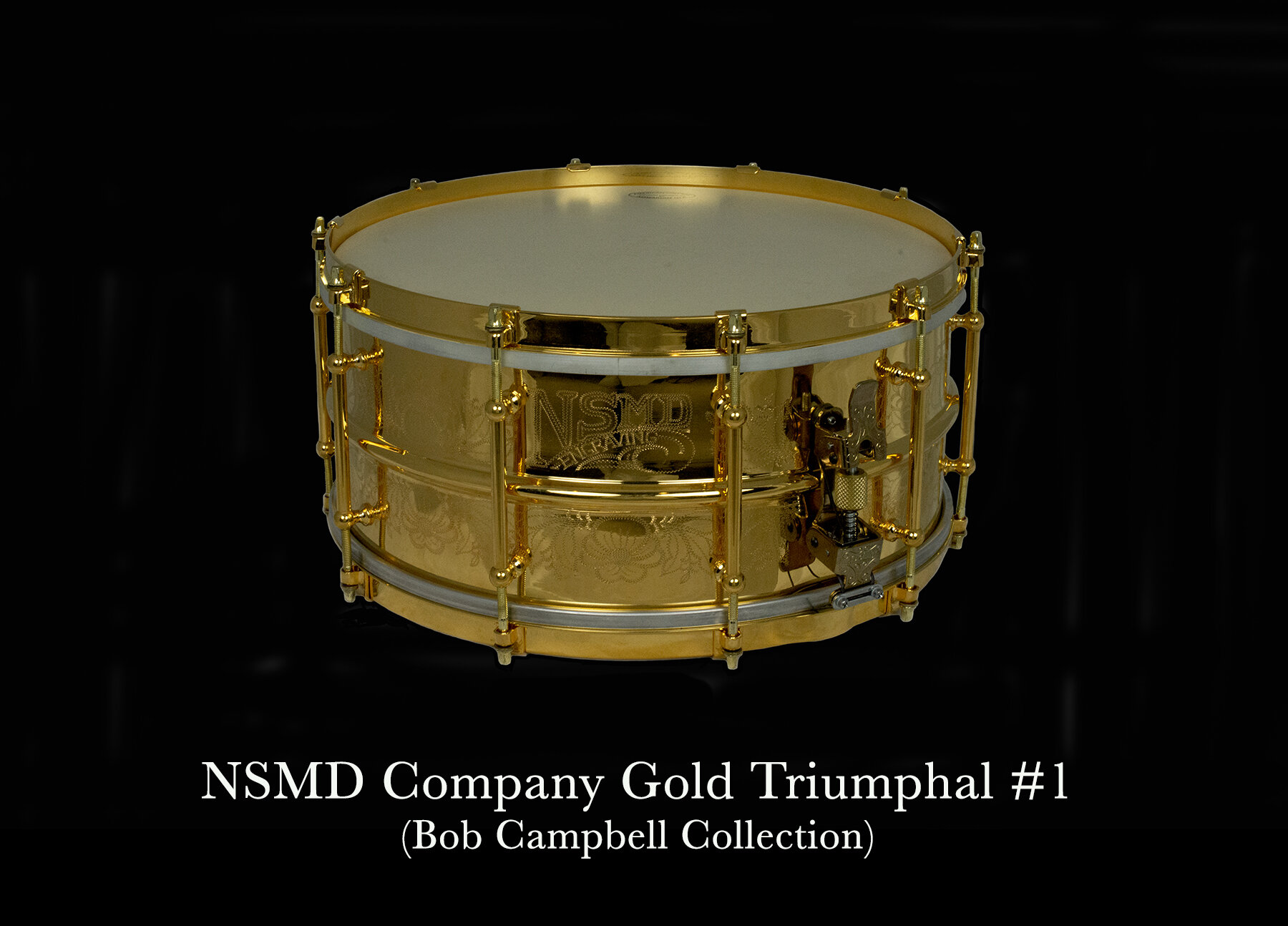
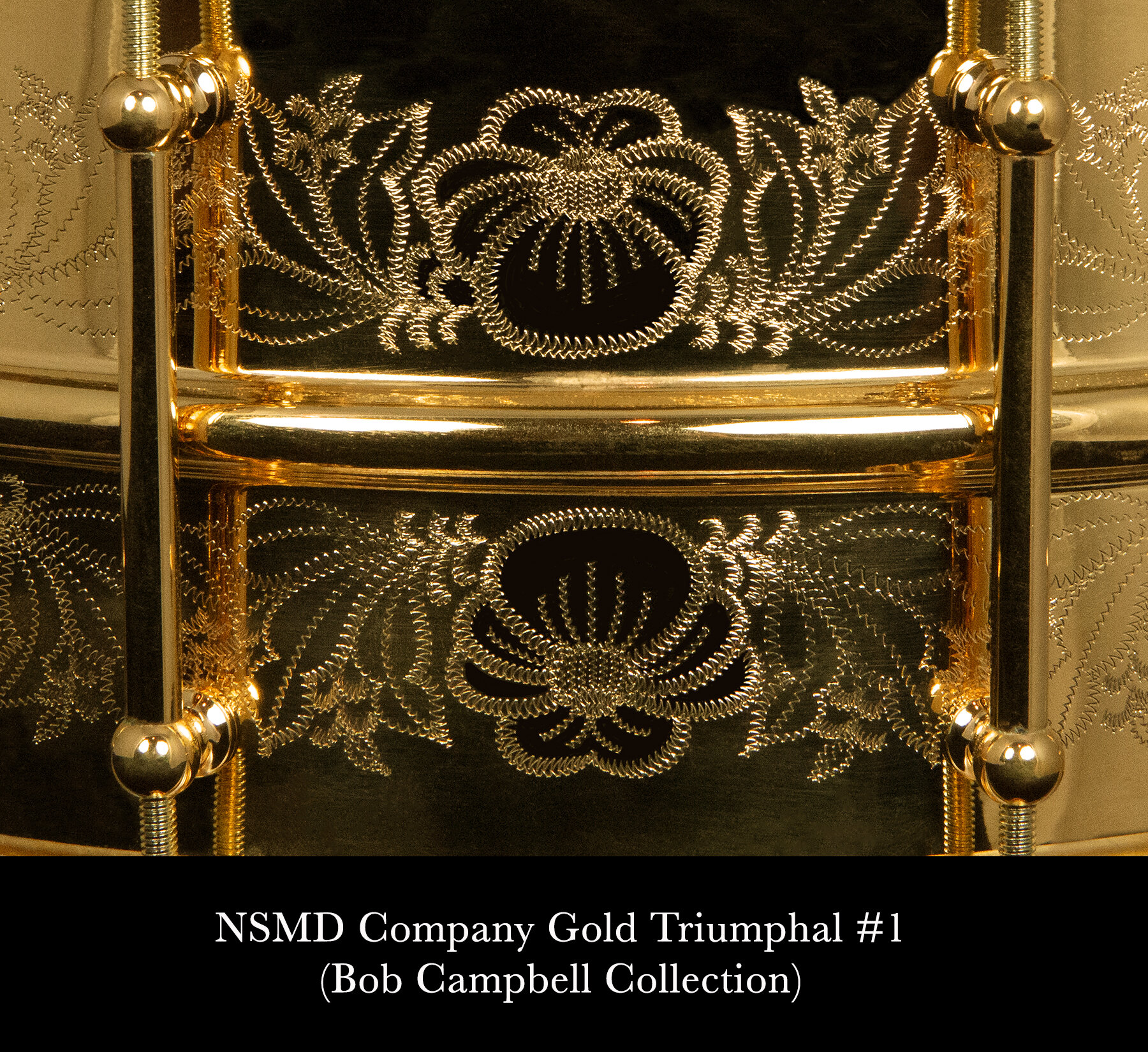
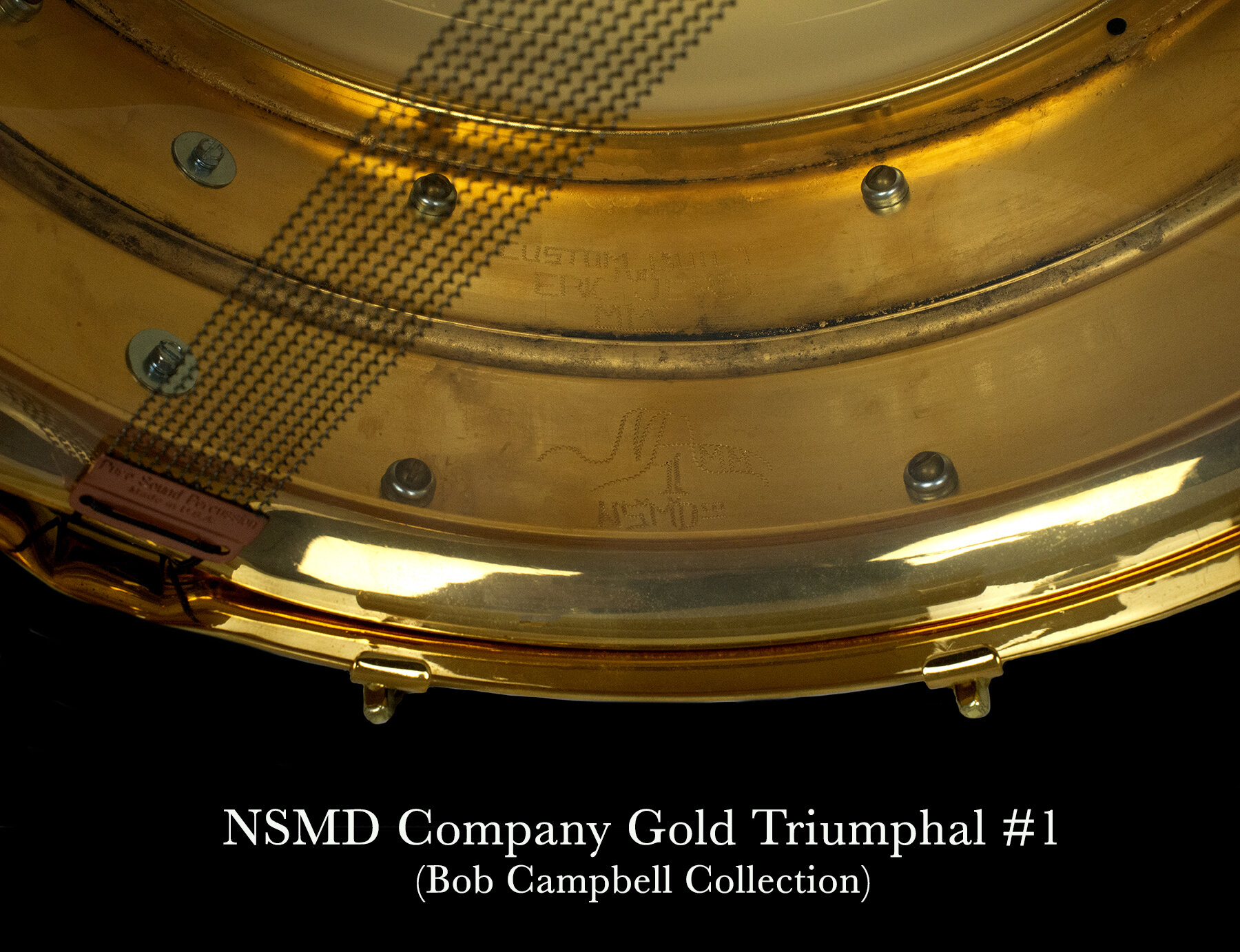
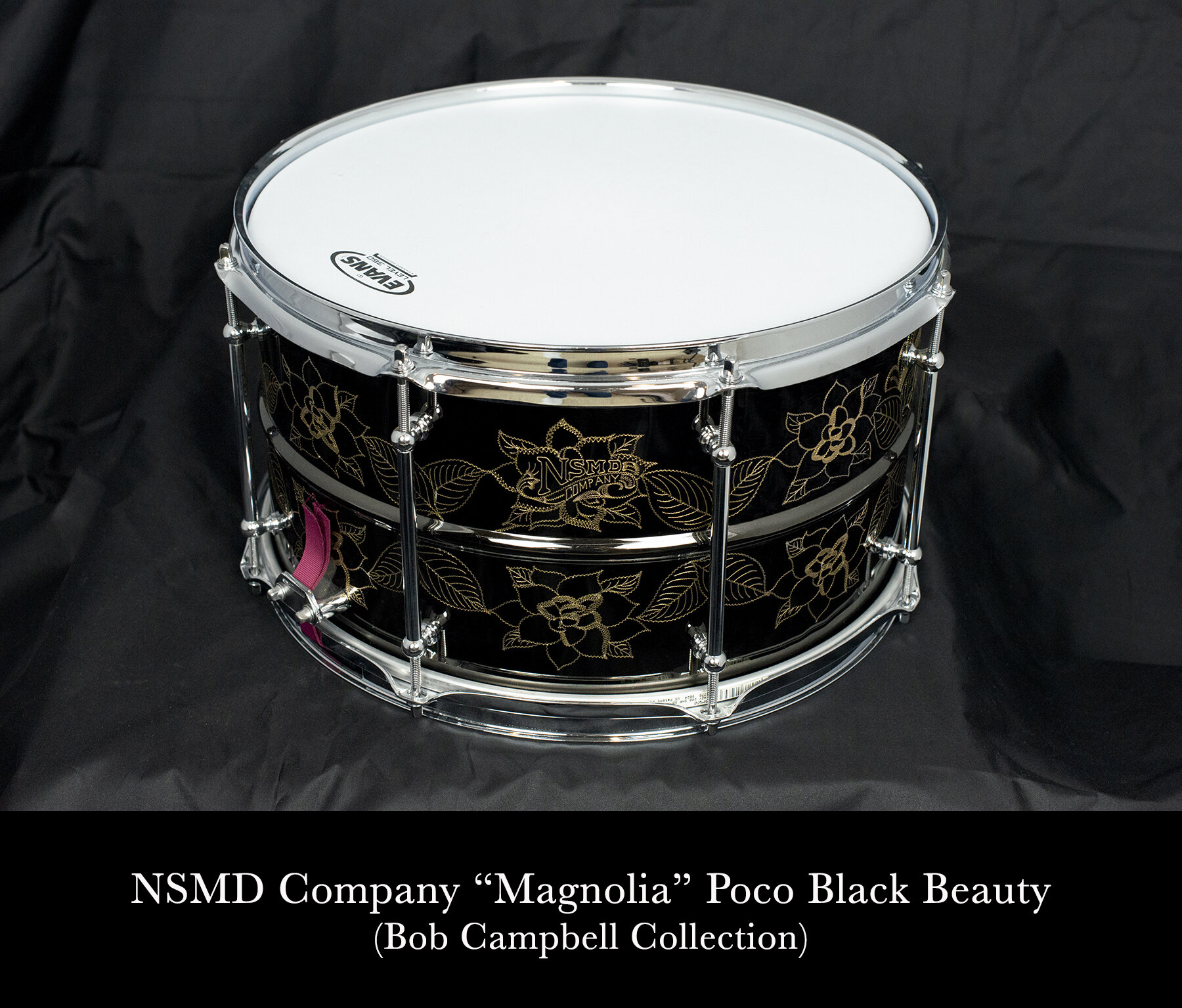
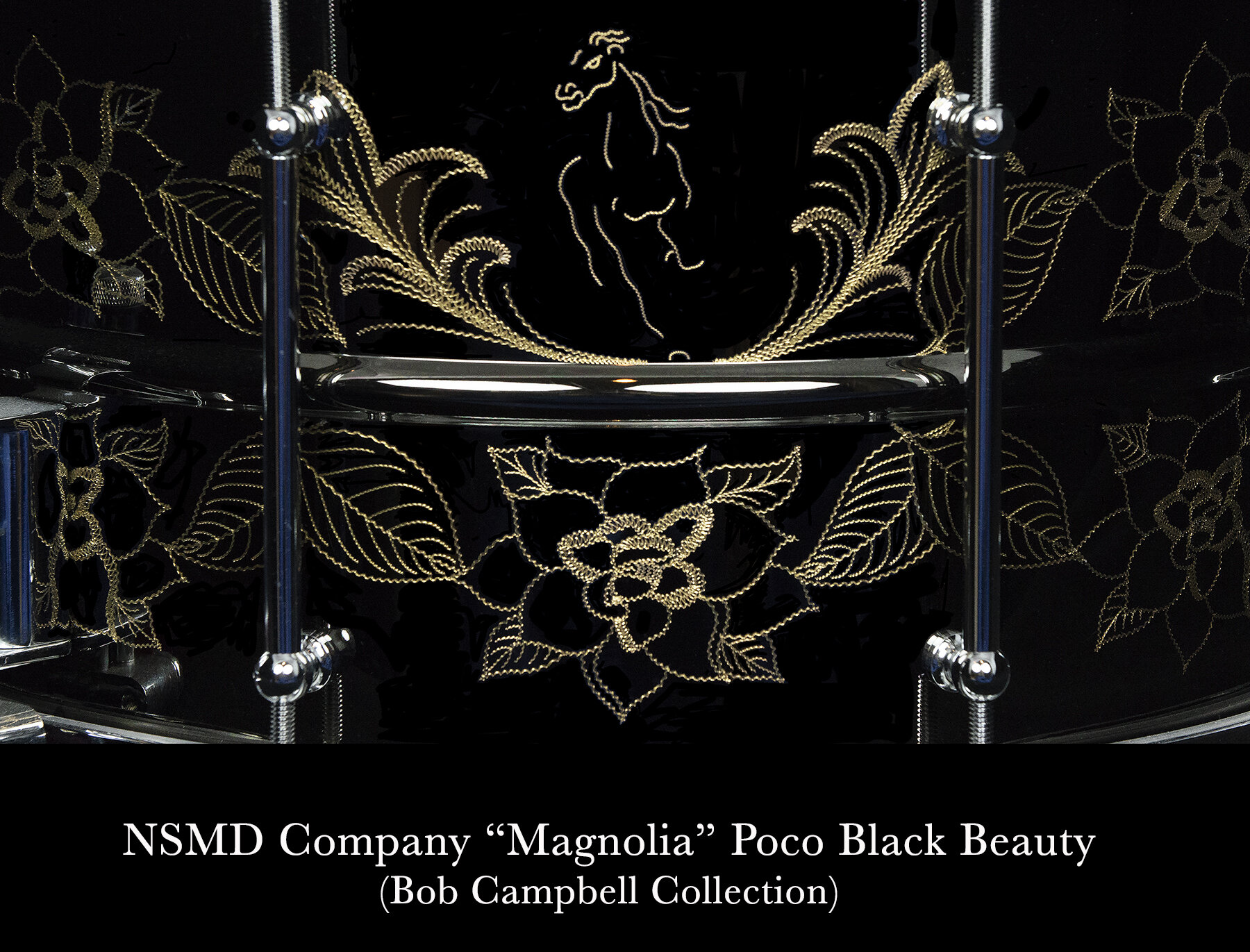
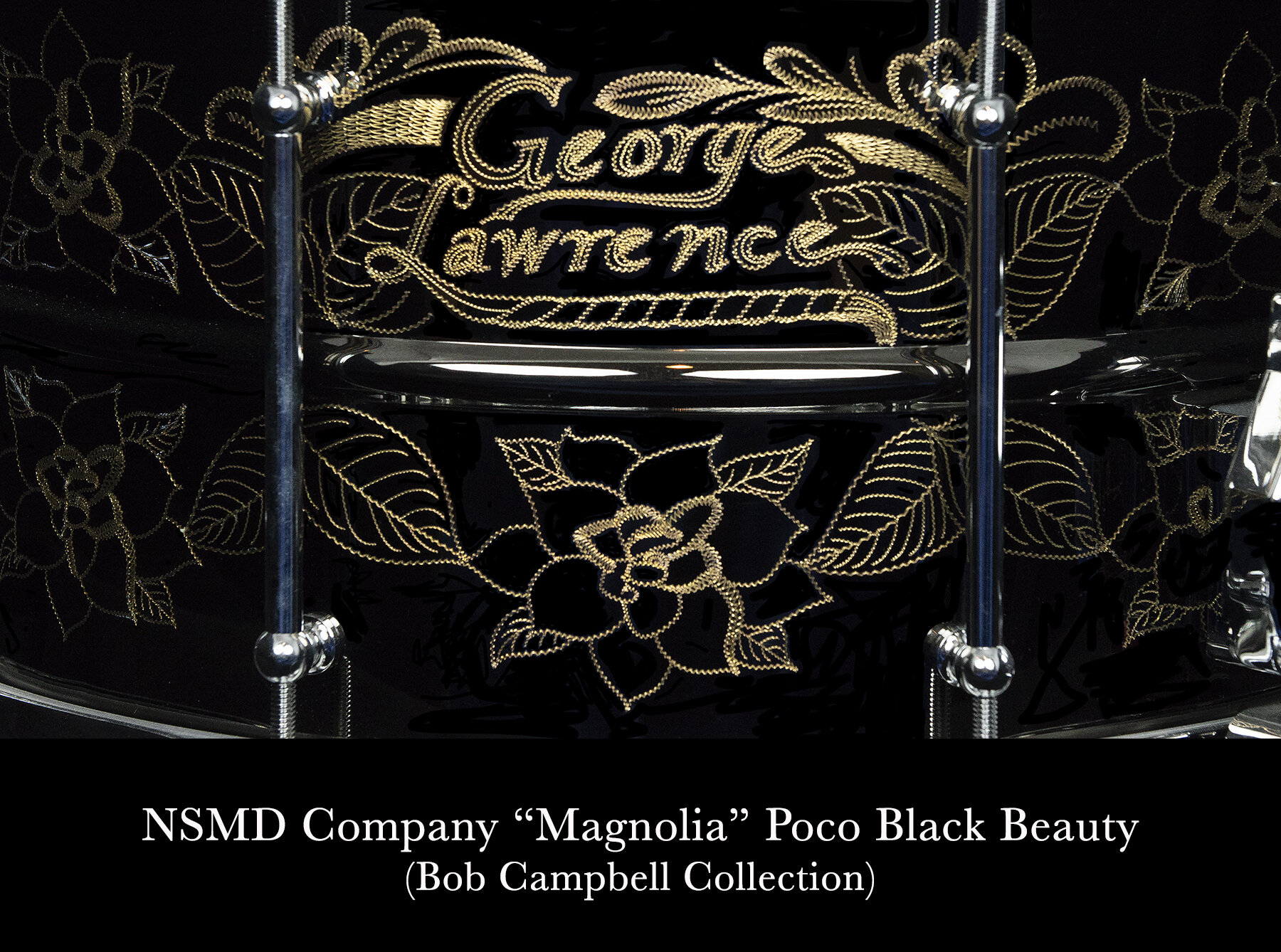
I like to think of John Aldridge as a “Drum Jedi Master”. He is an endless wellspring of drum history, wisdom, experience and creativity. In this sequel to Part 1, I wanted to share some examples of John’s unique custom works with personal insights from John about their design. Many of these drums are from my personal collection and are greatly treasured. It is my hope that drummers will not only appreciate John’s incredible versatility, but also realize that “drum art” can be truly personal. Drum engraving is not restricted to scrolls and florets!
Read moreThe Drum Engravers, Part 1: John Aldridge
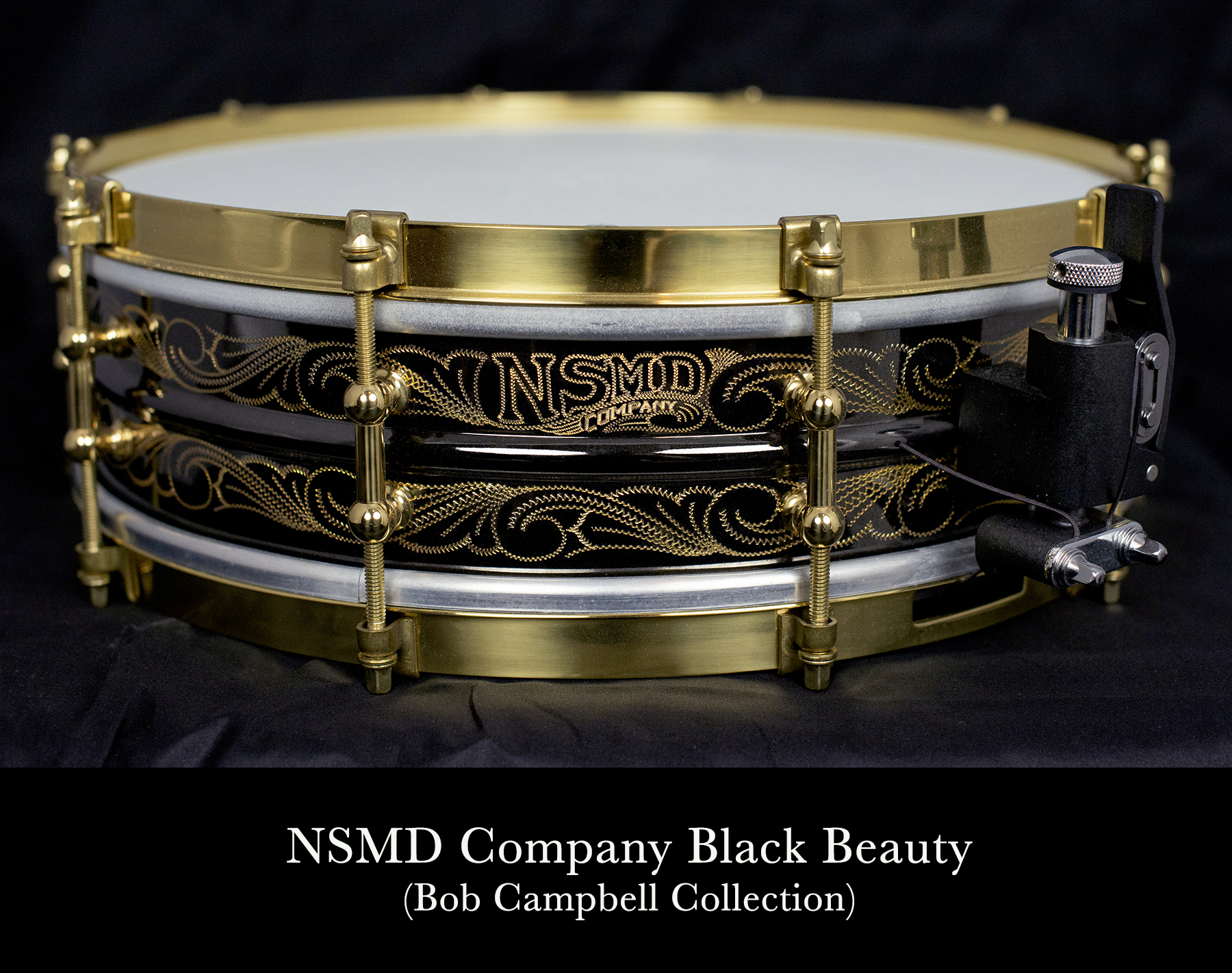
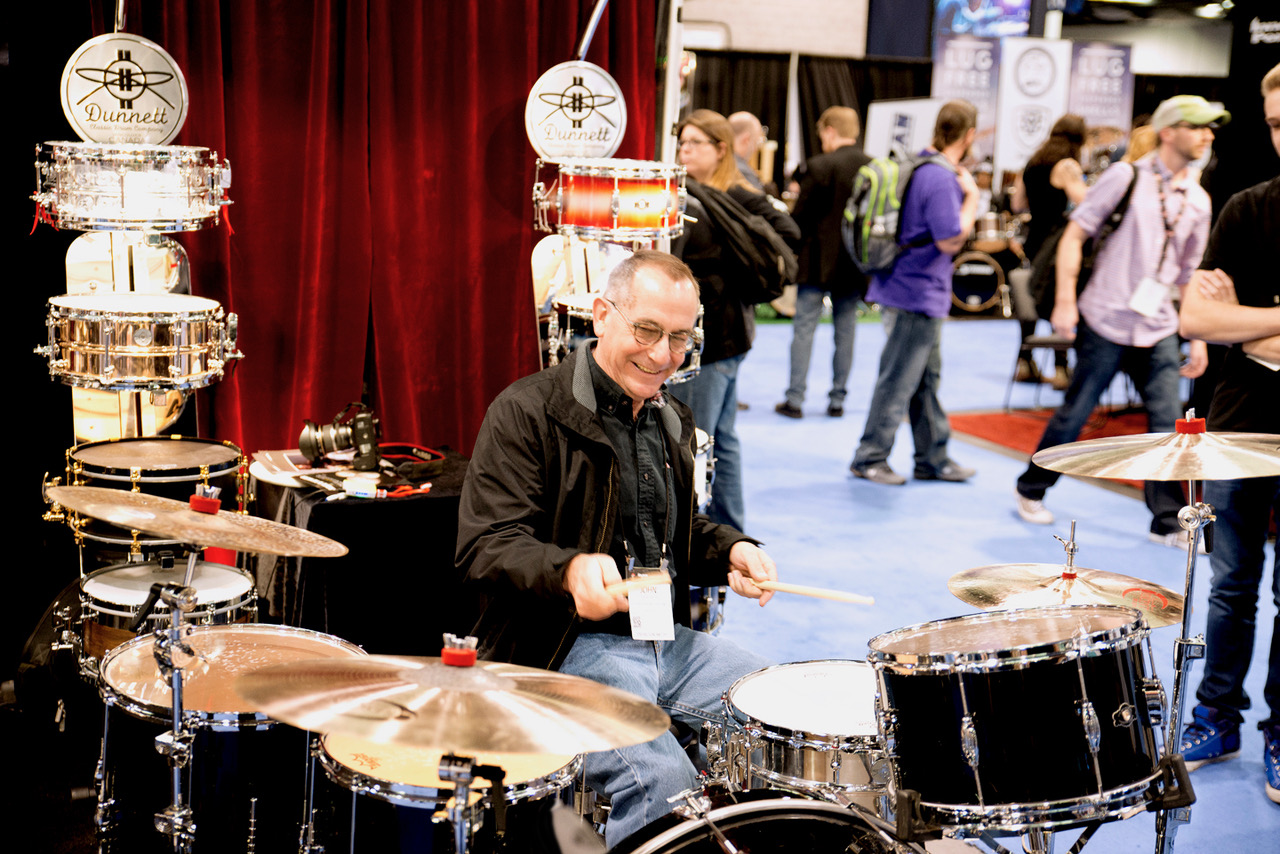
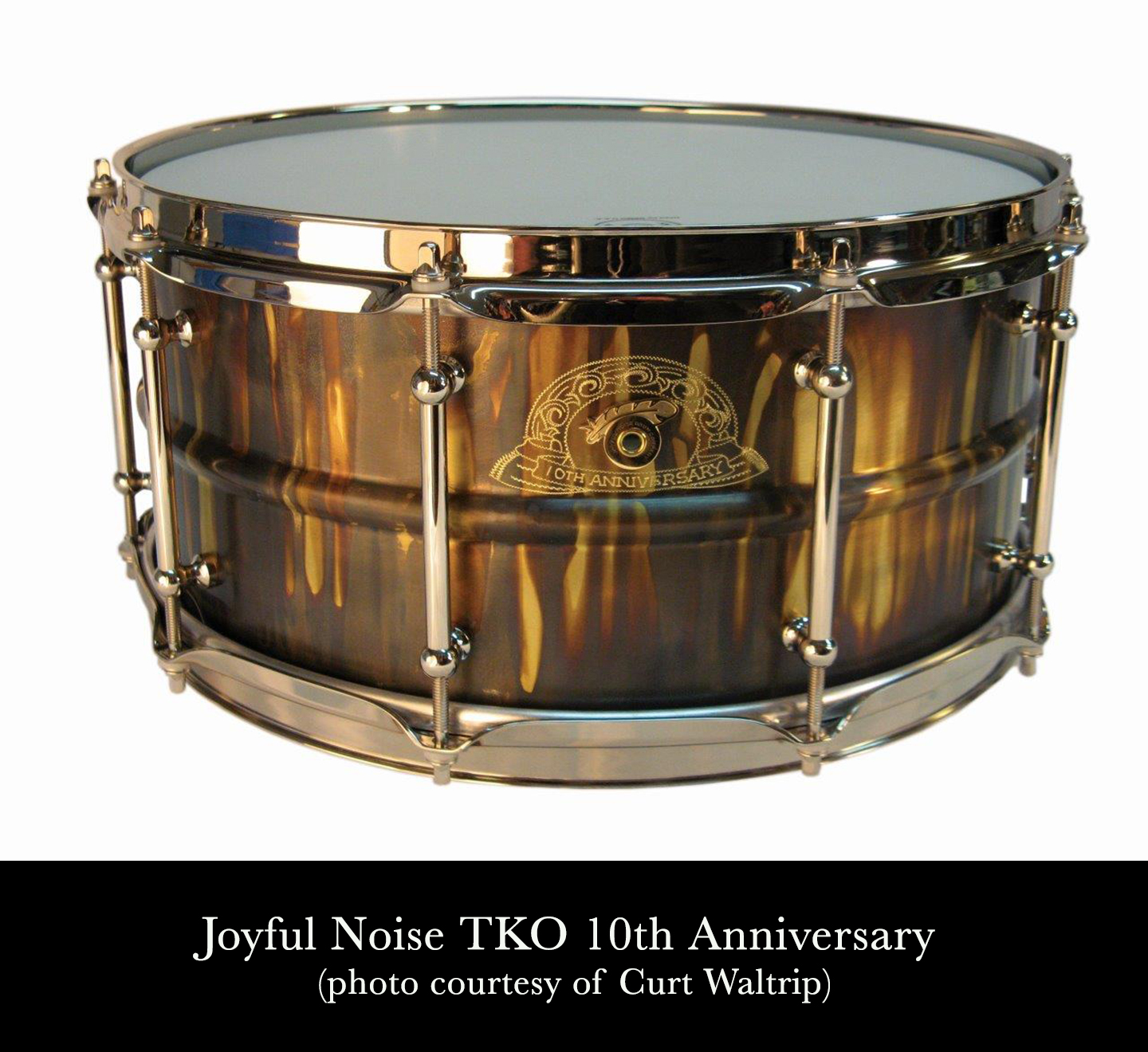
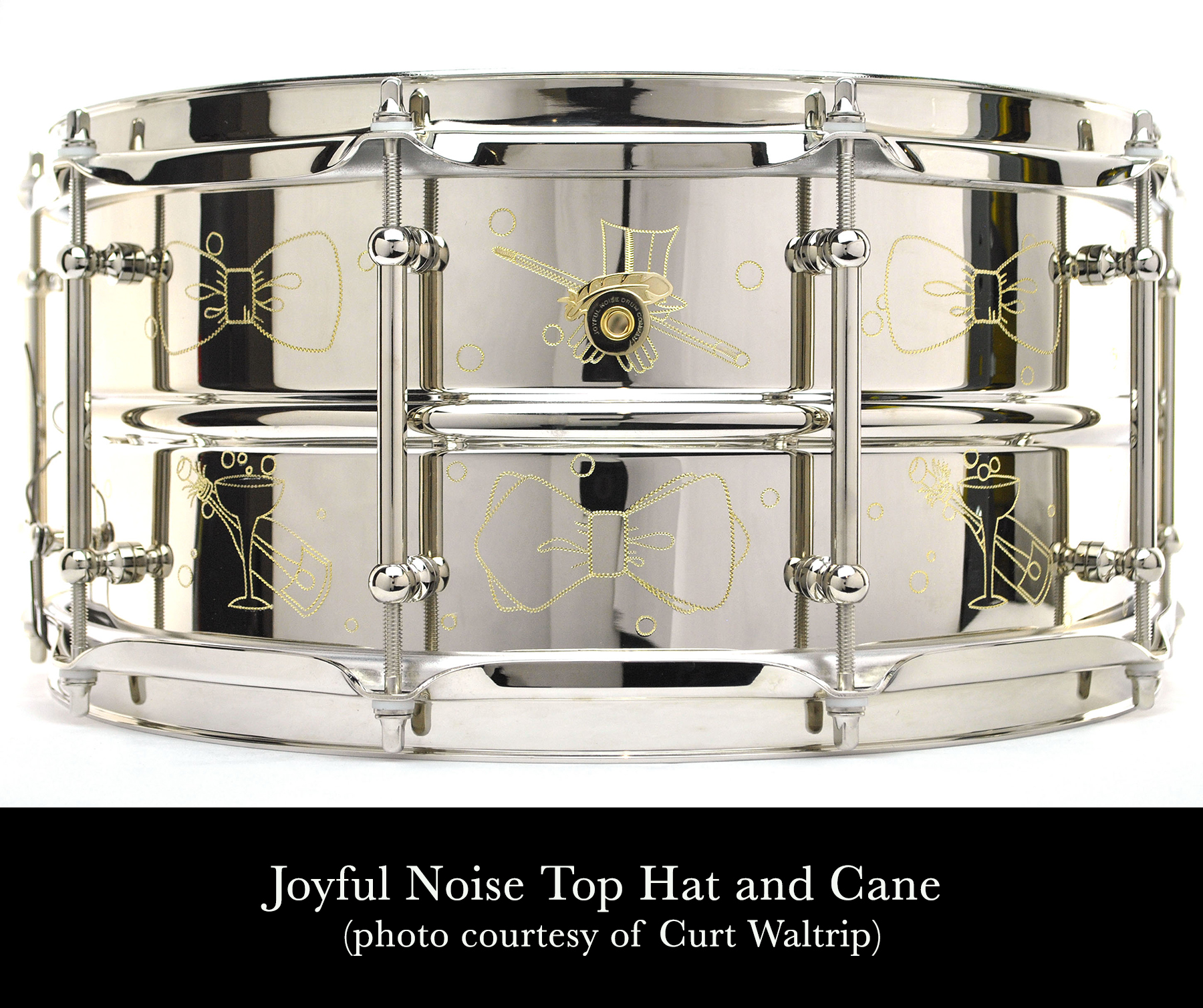
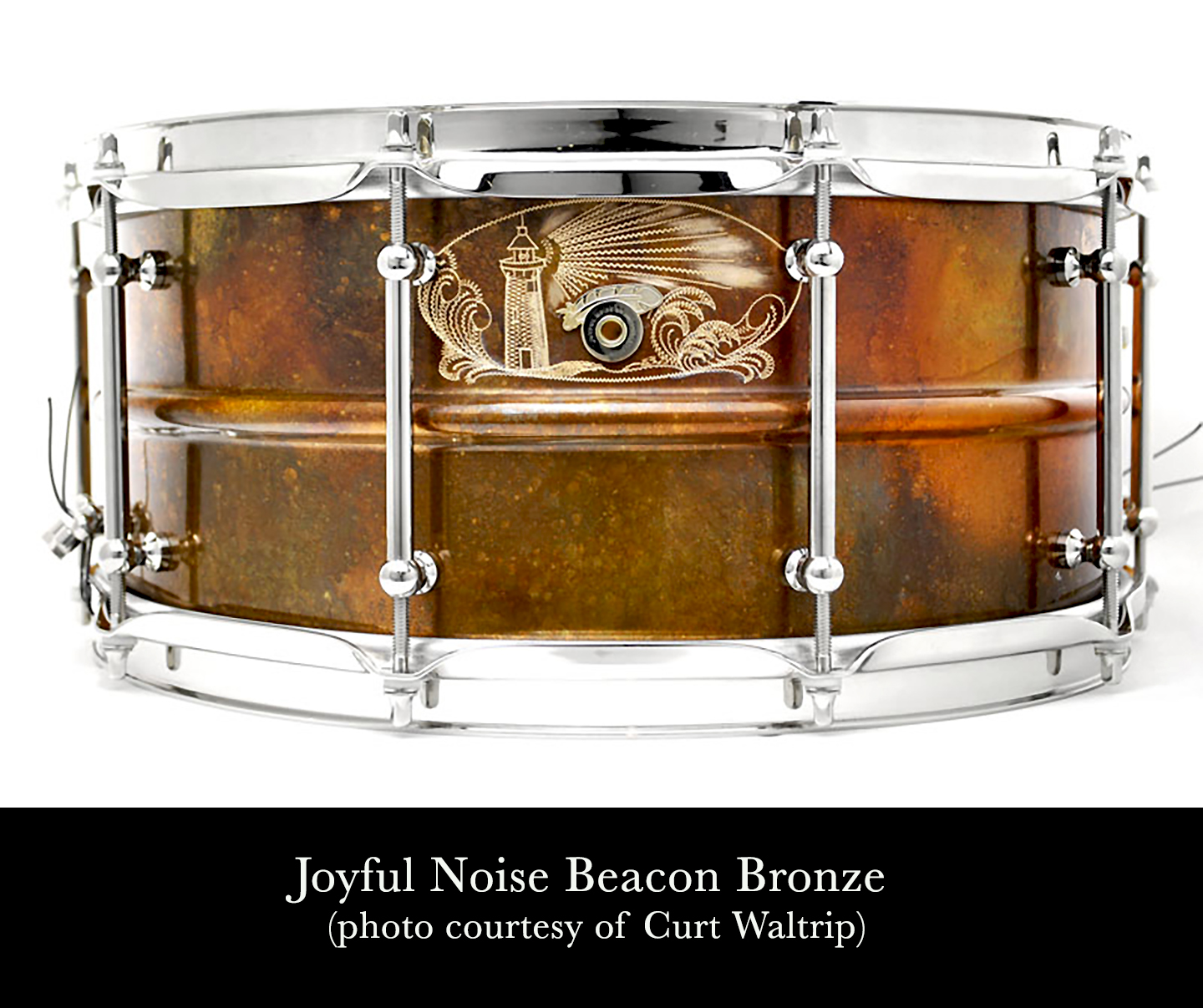
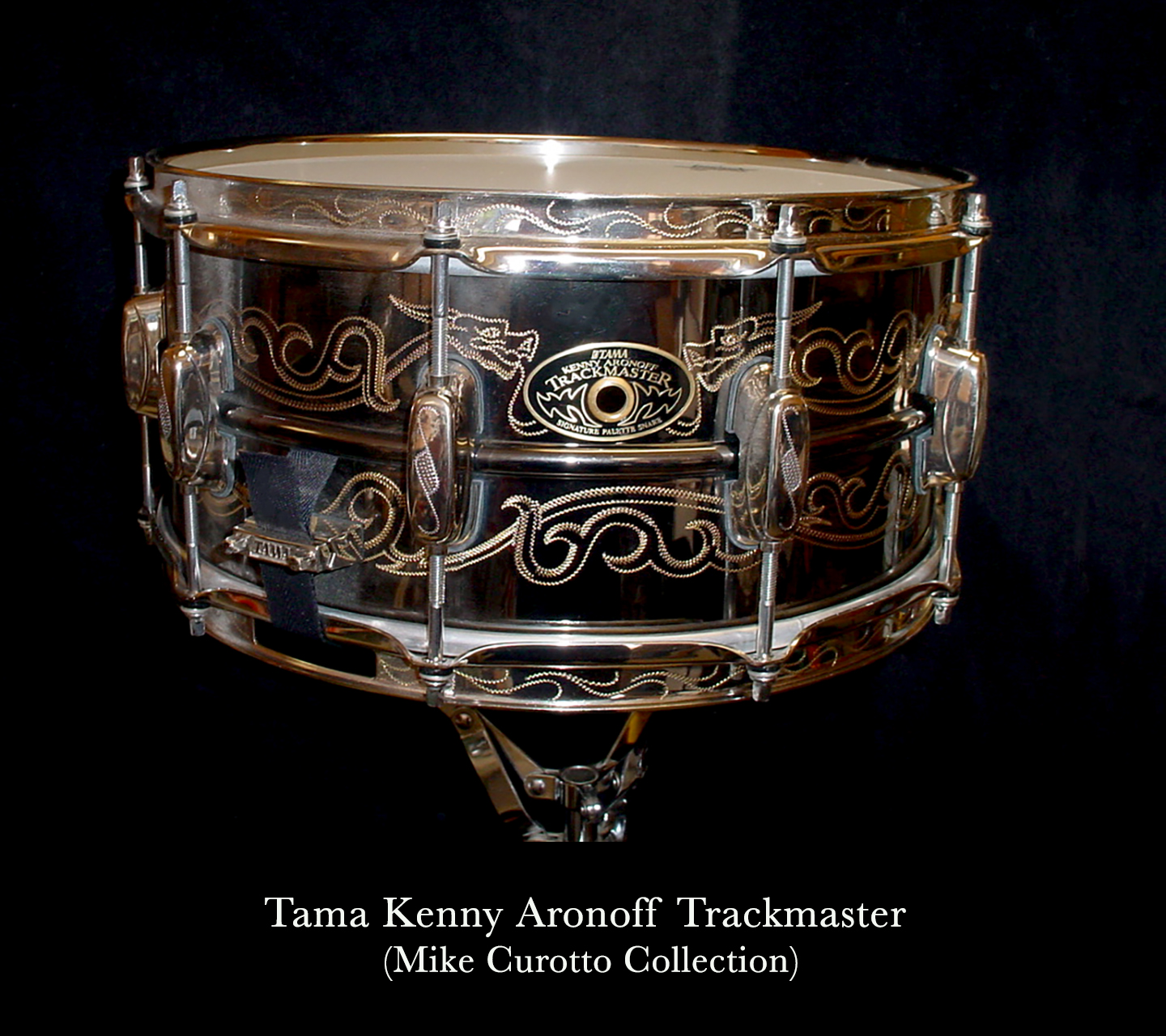
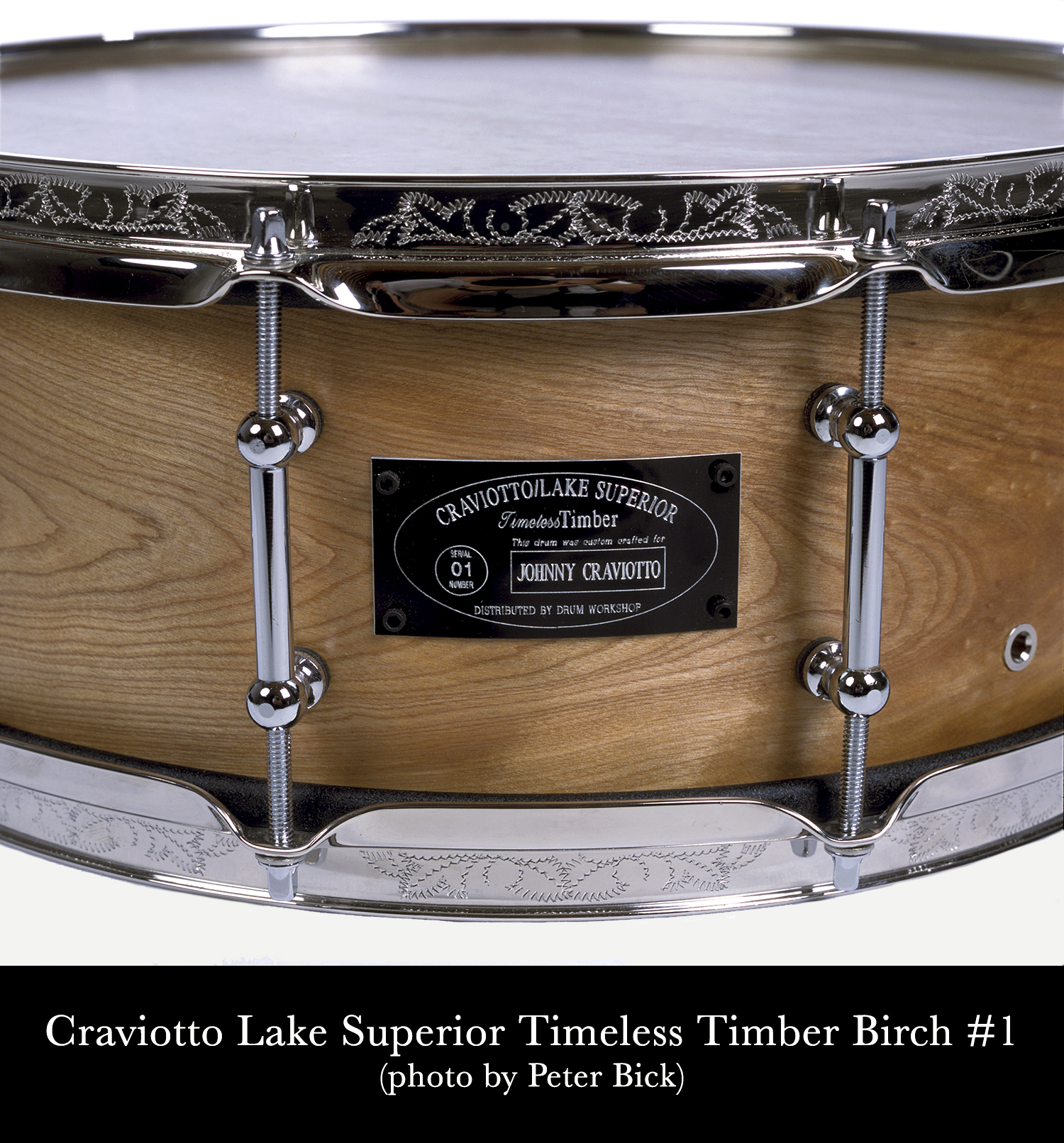
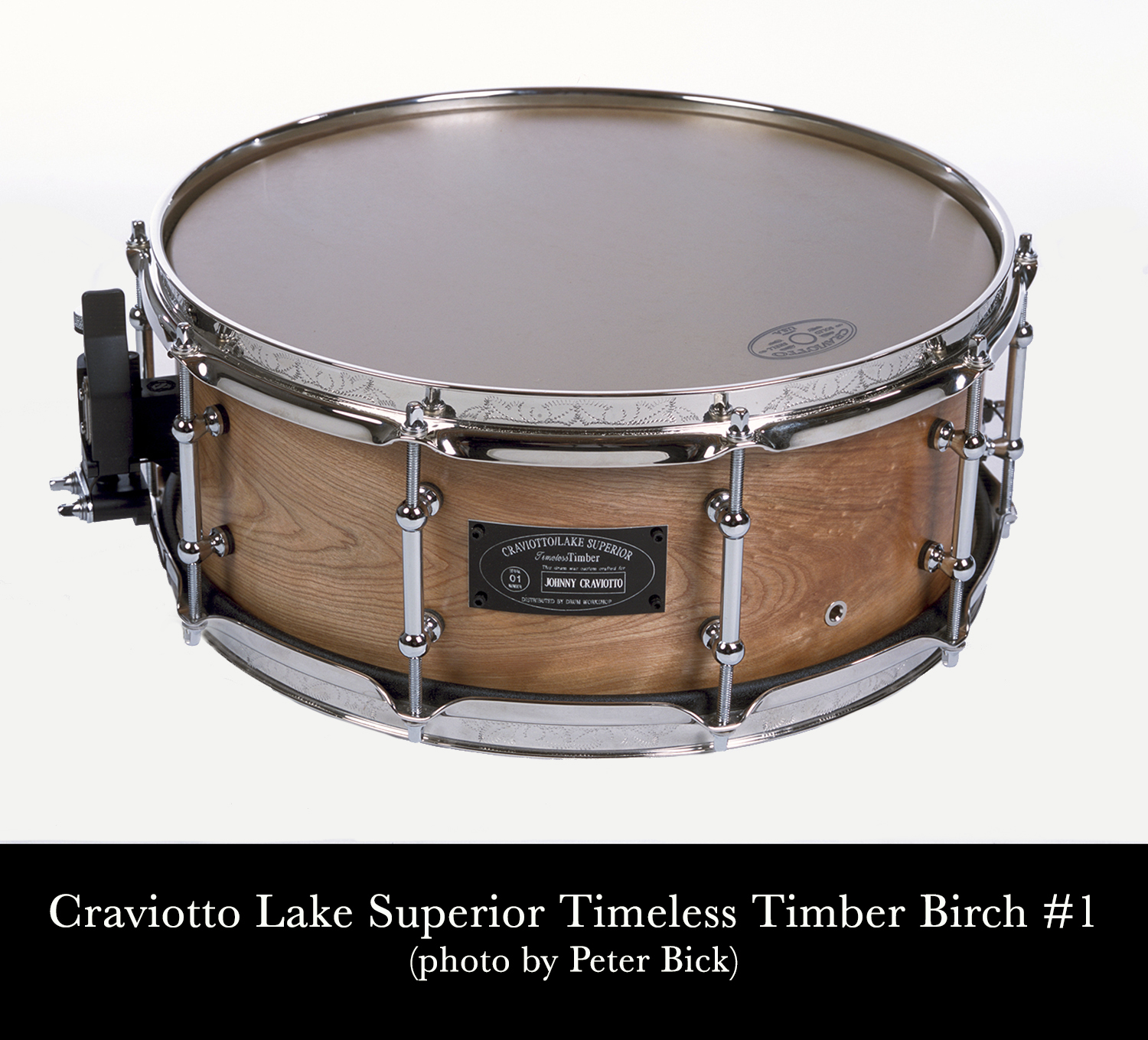
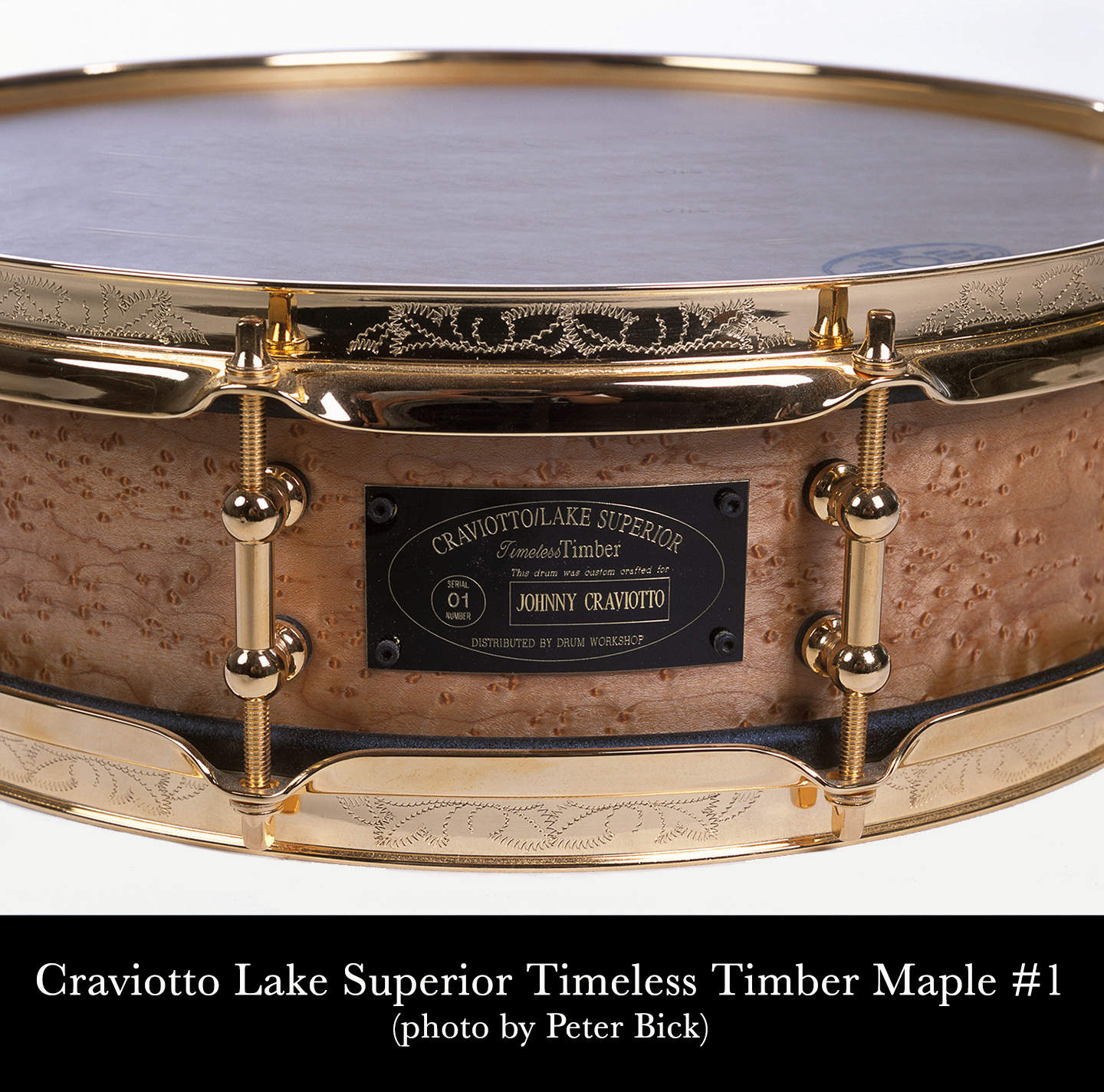
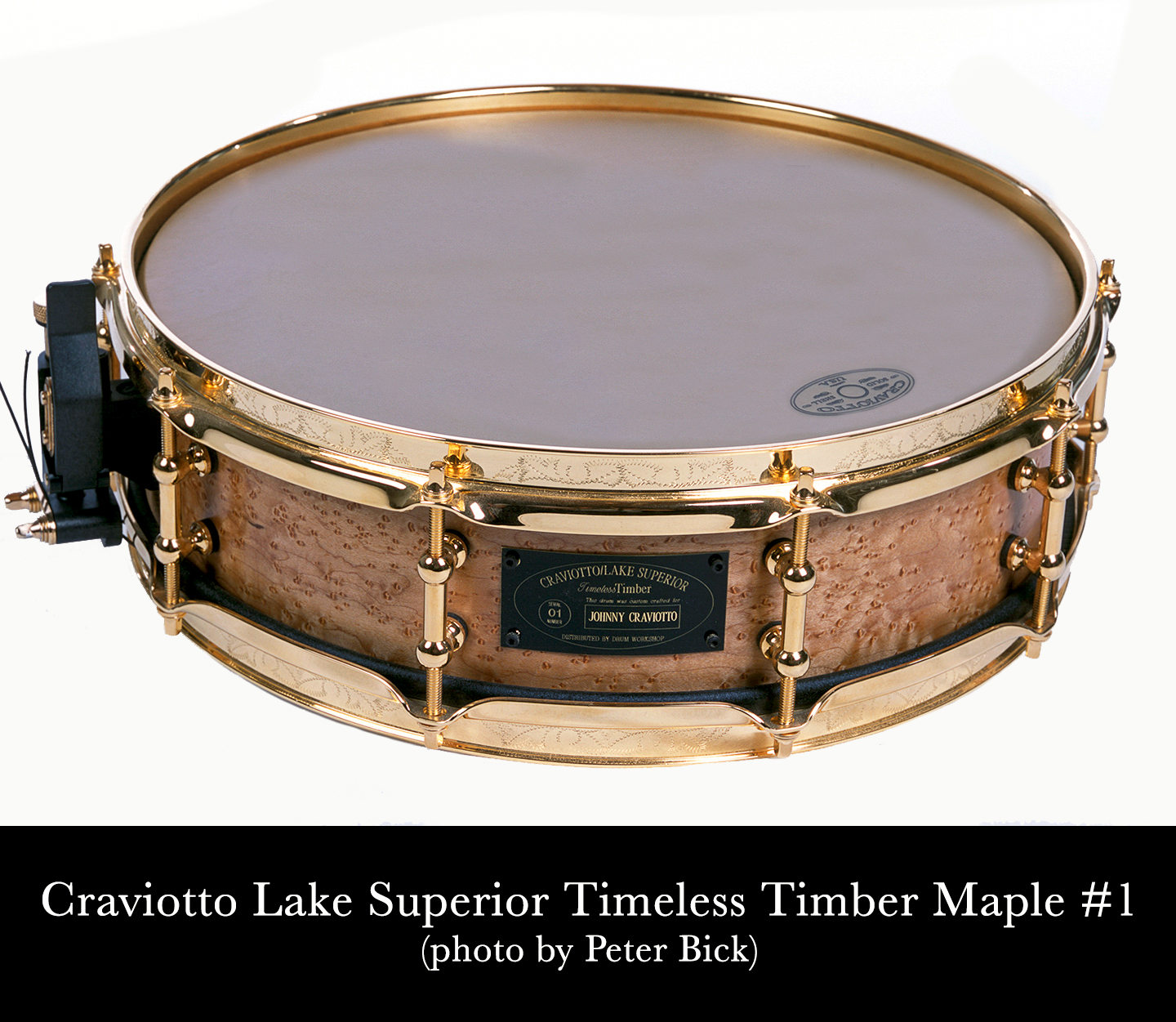
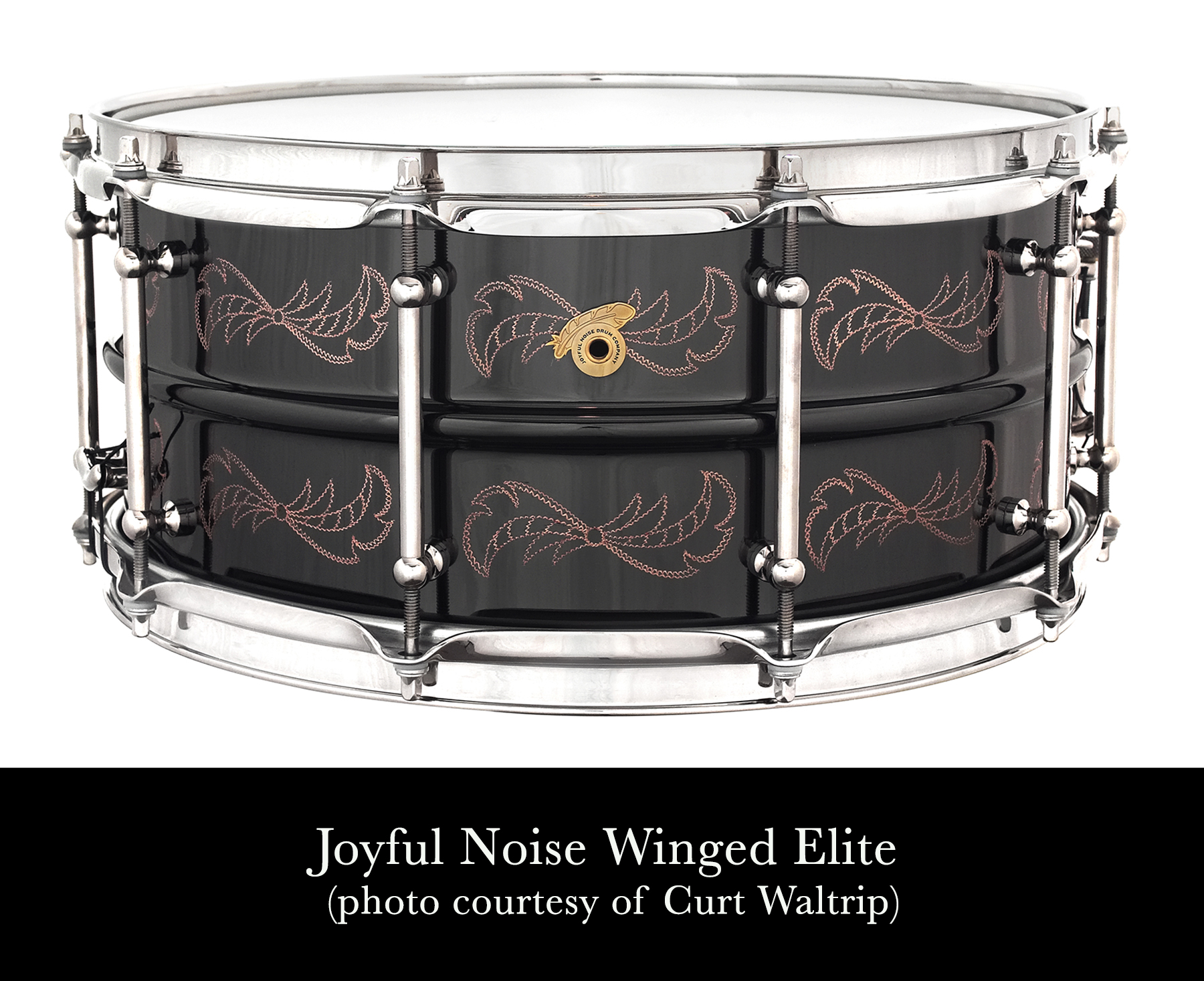
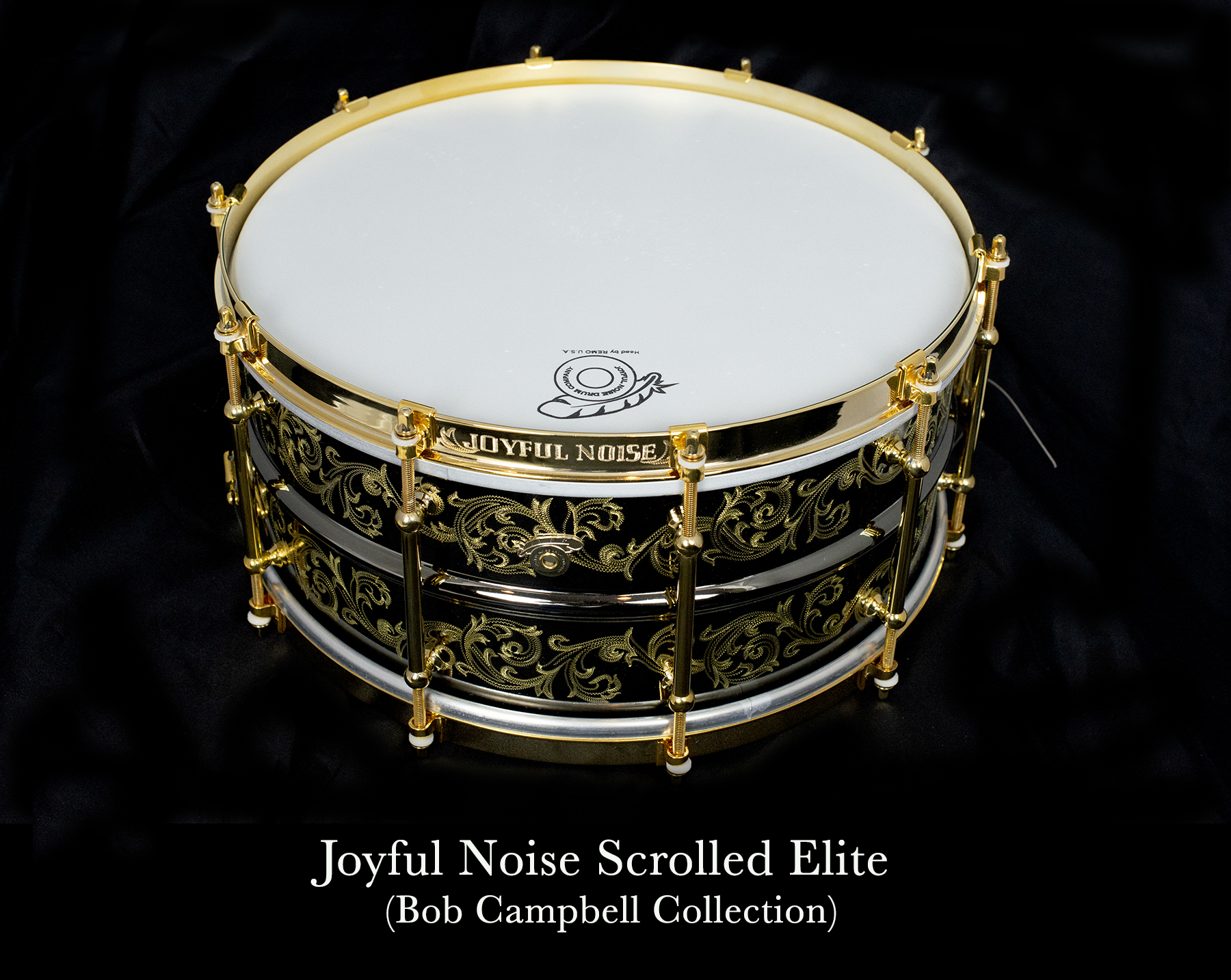
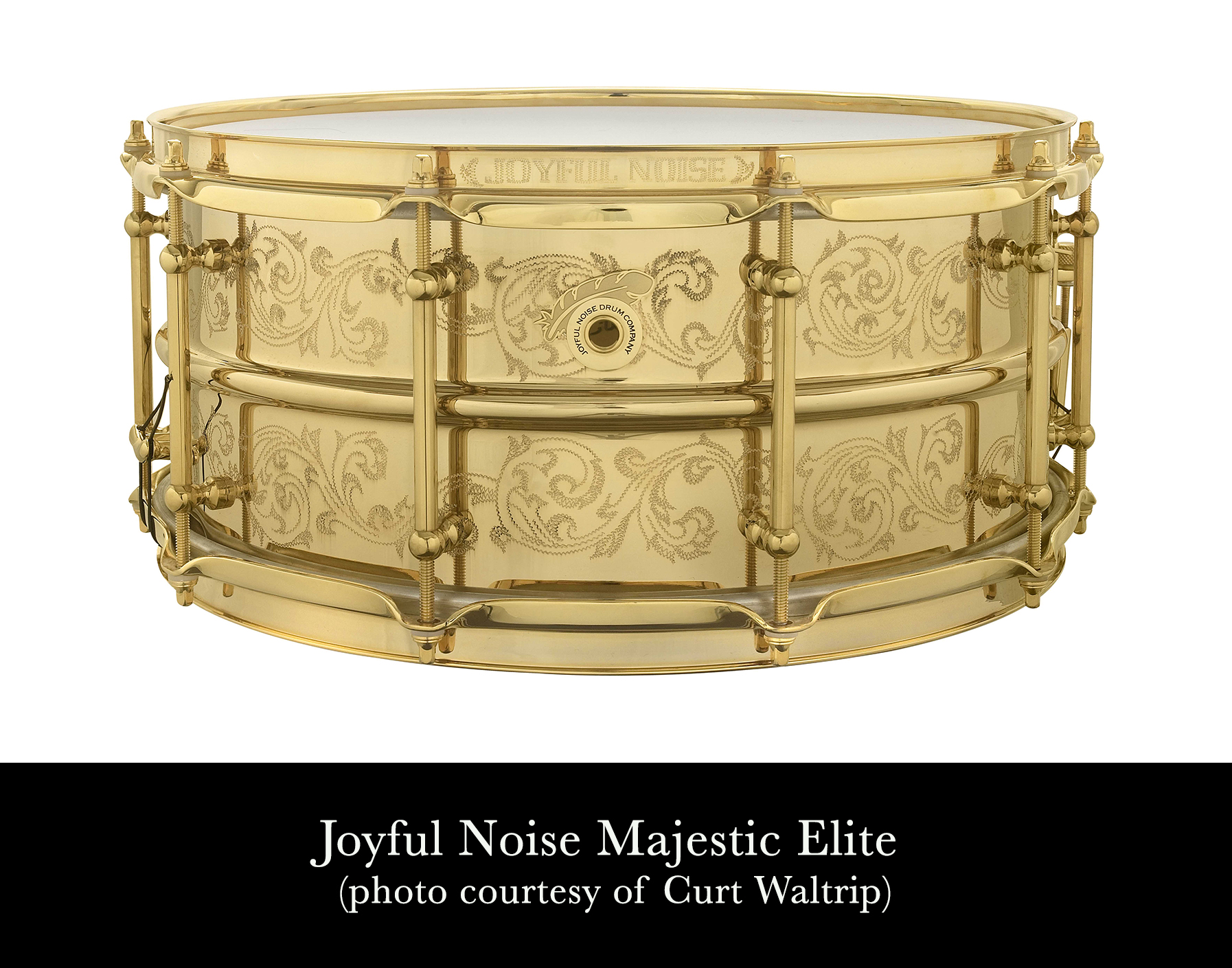
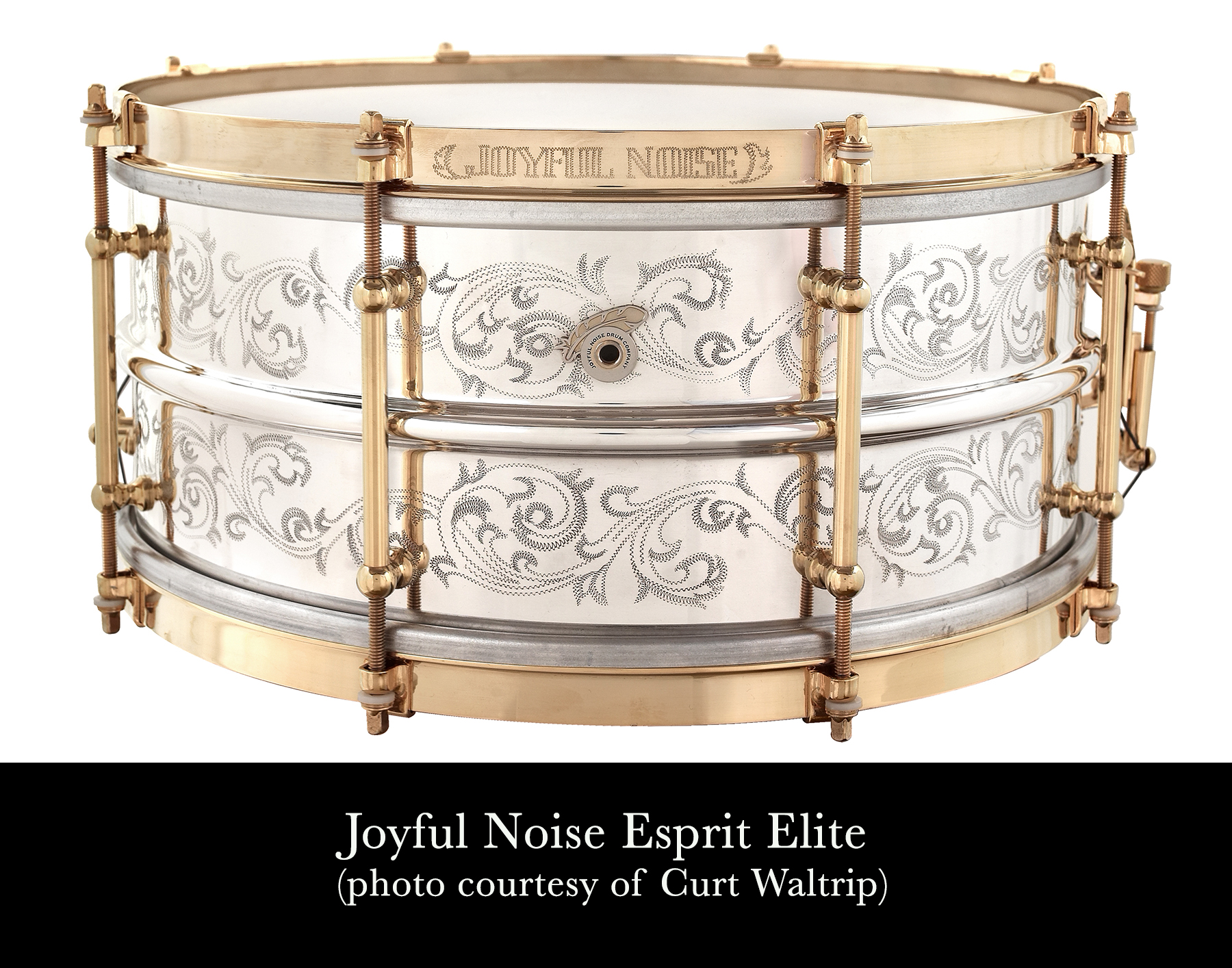
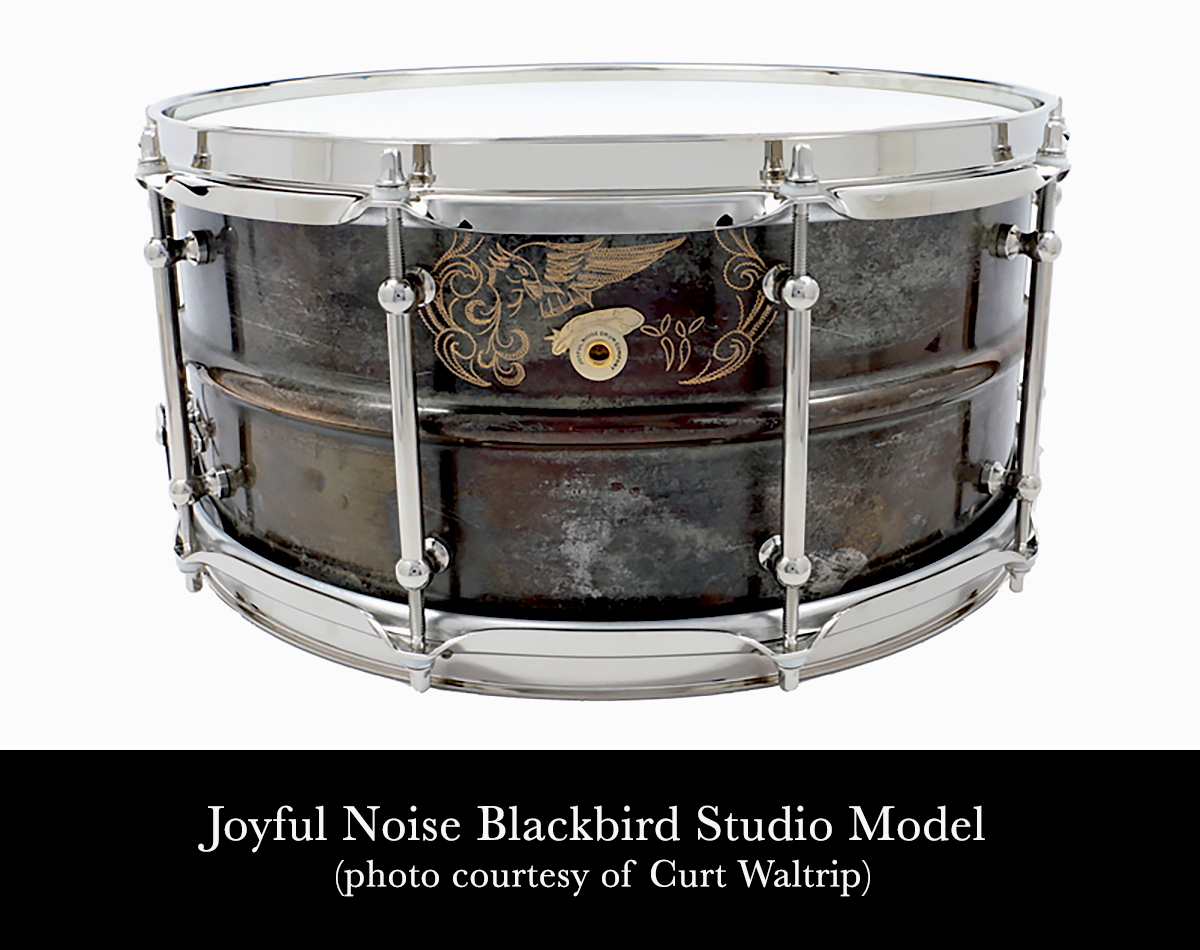
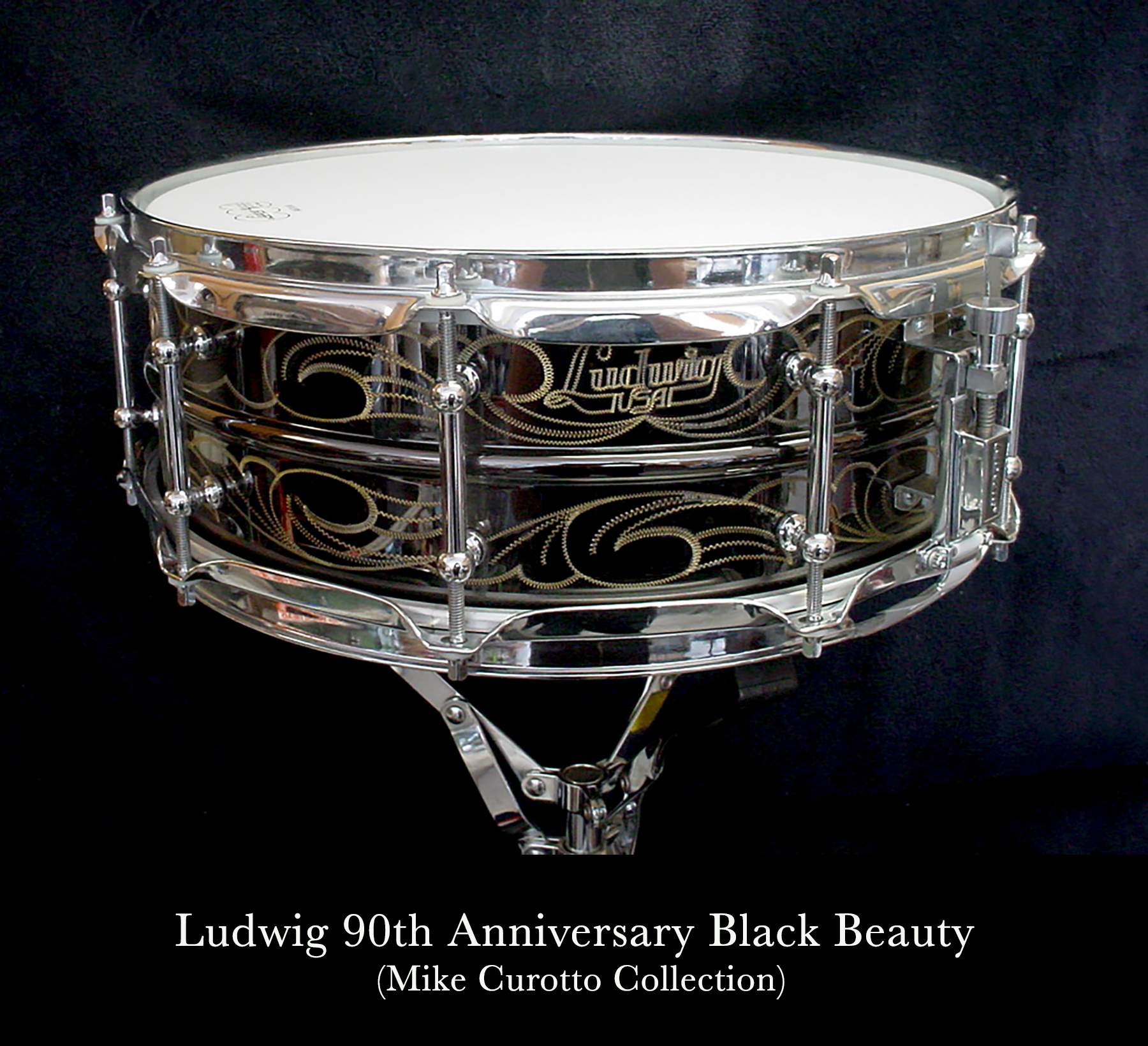
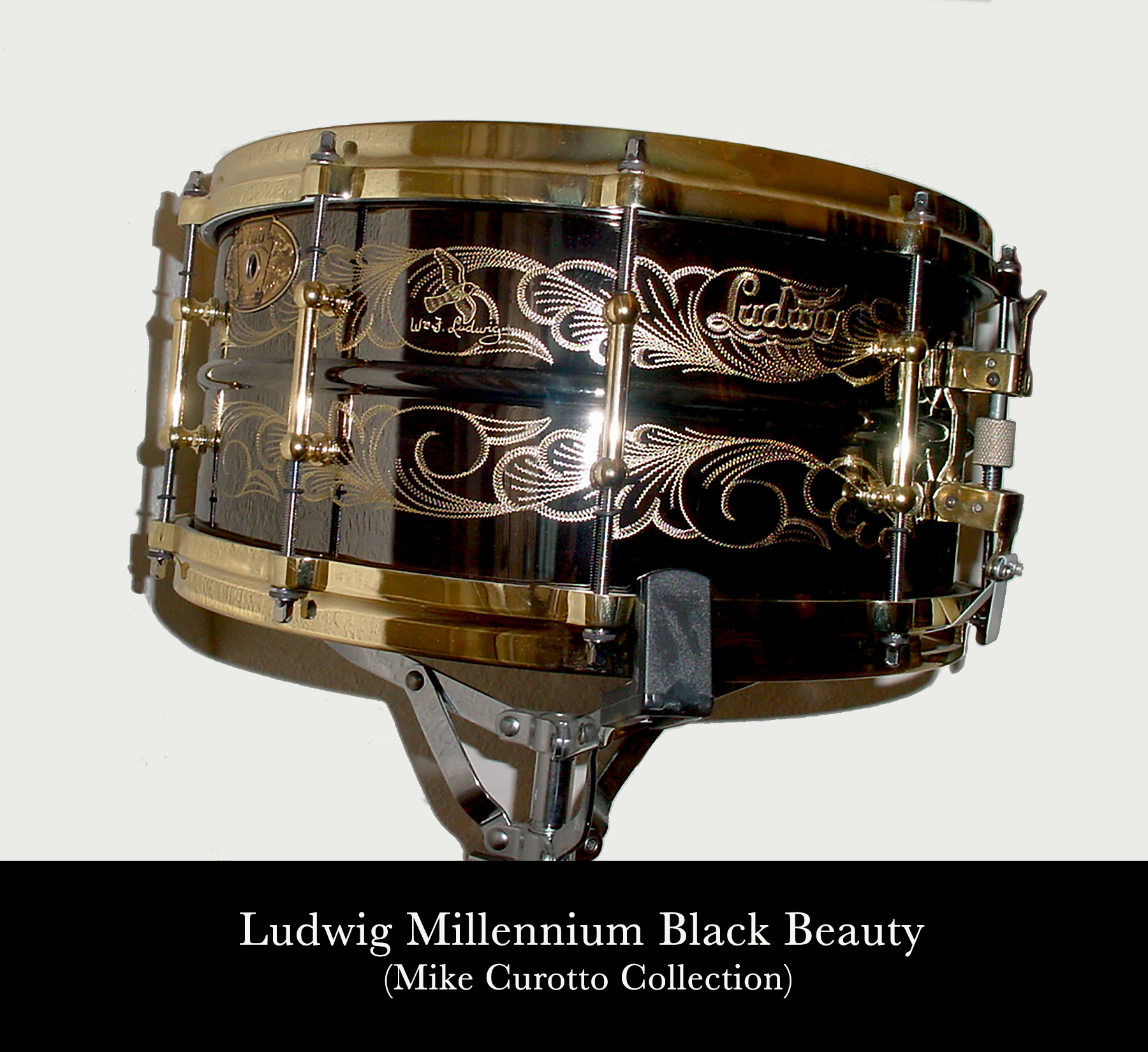
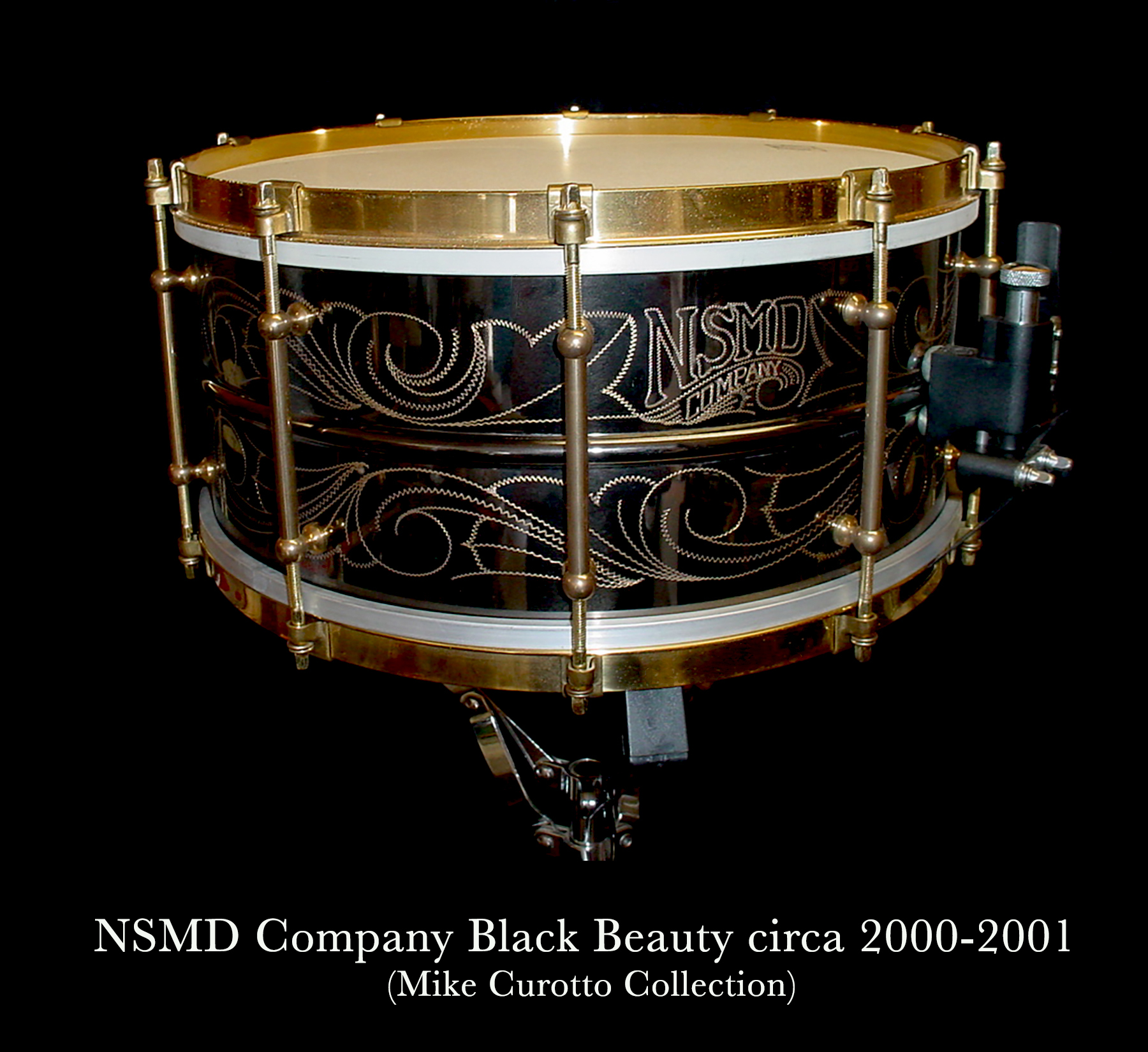
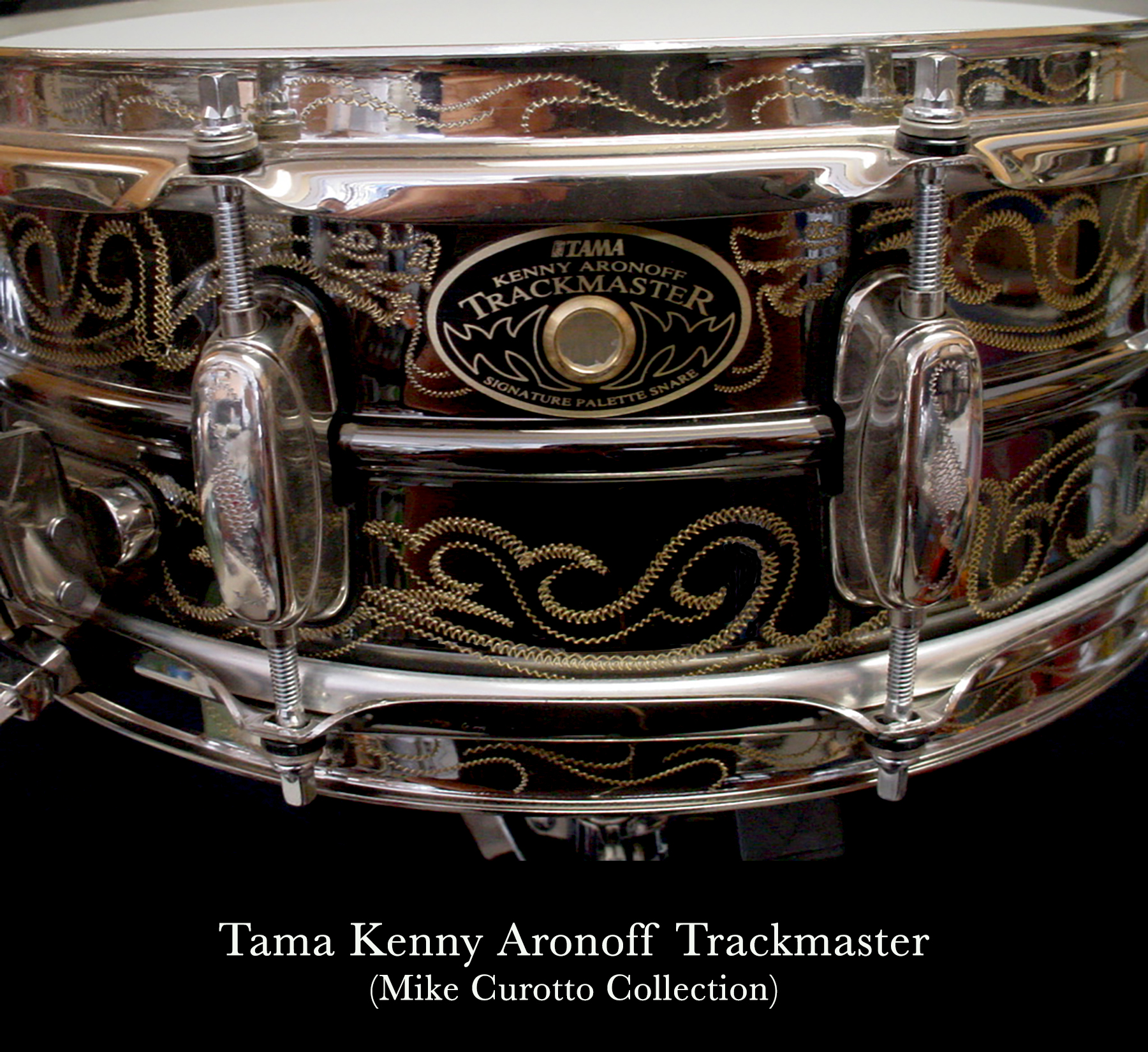
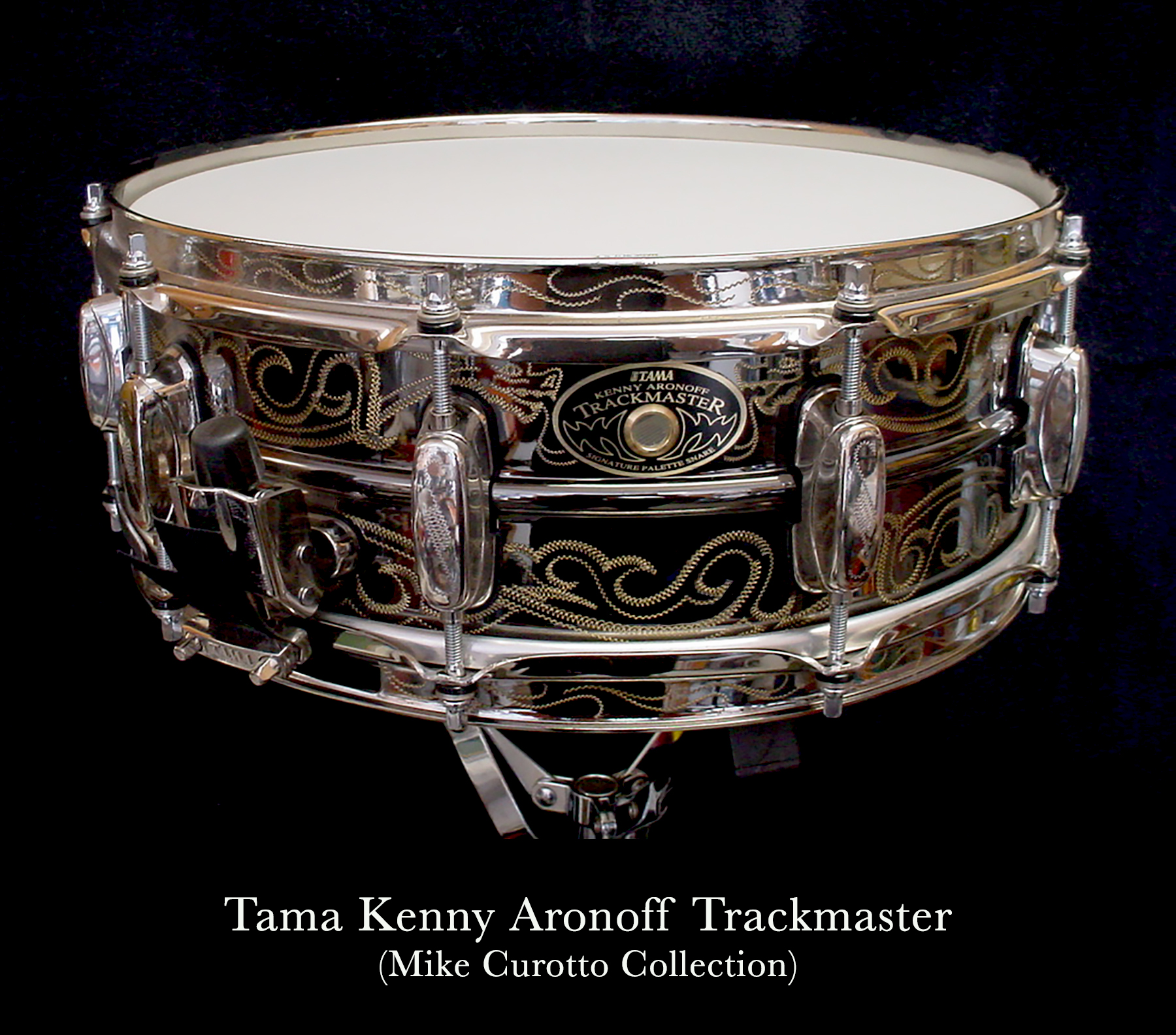
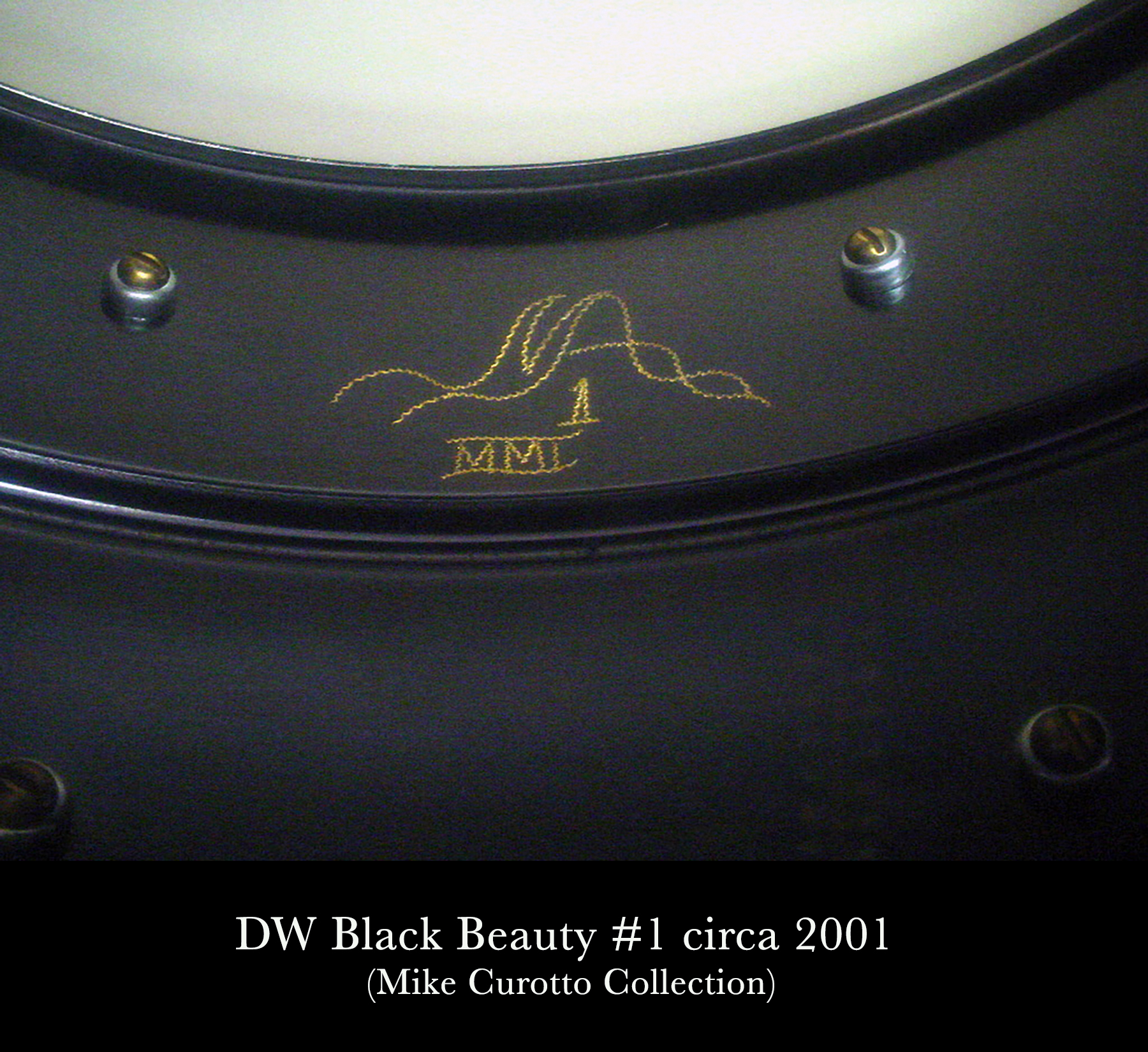
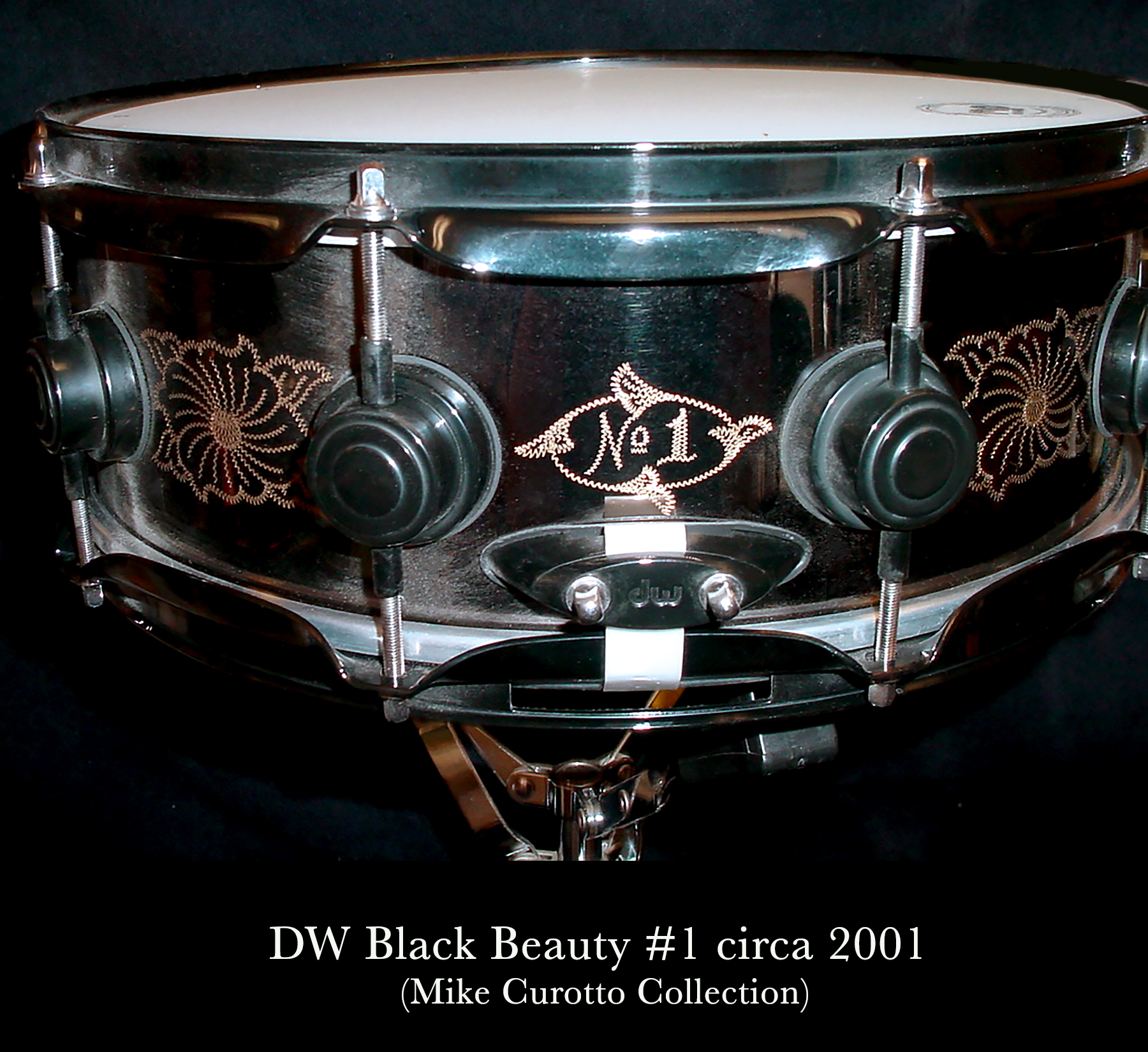
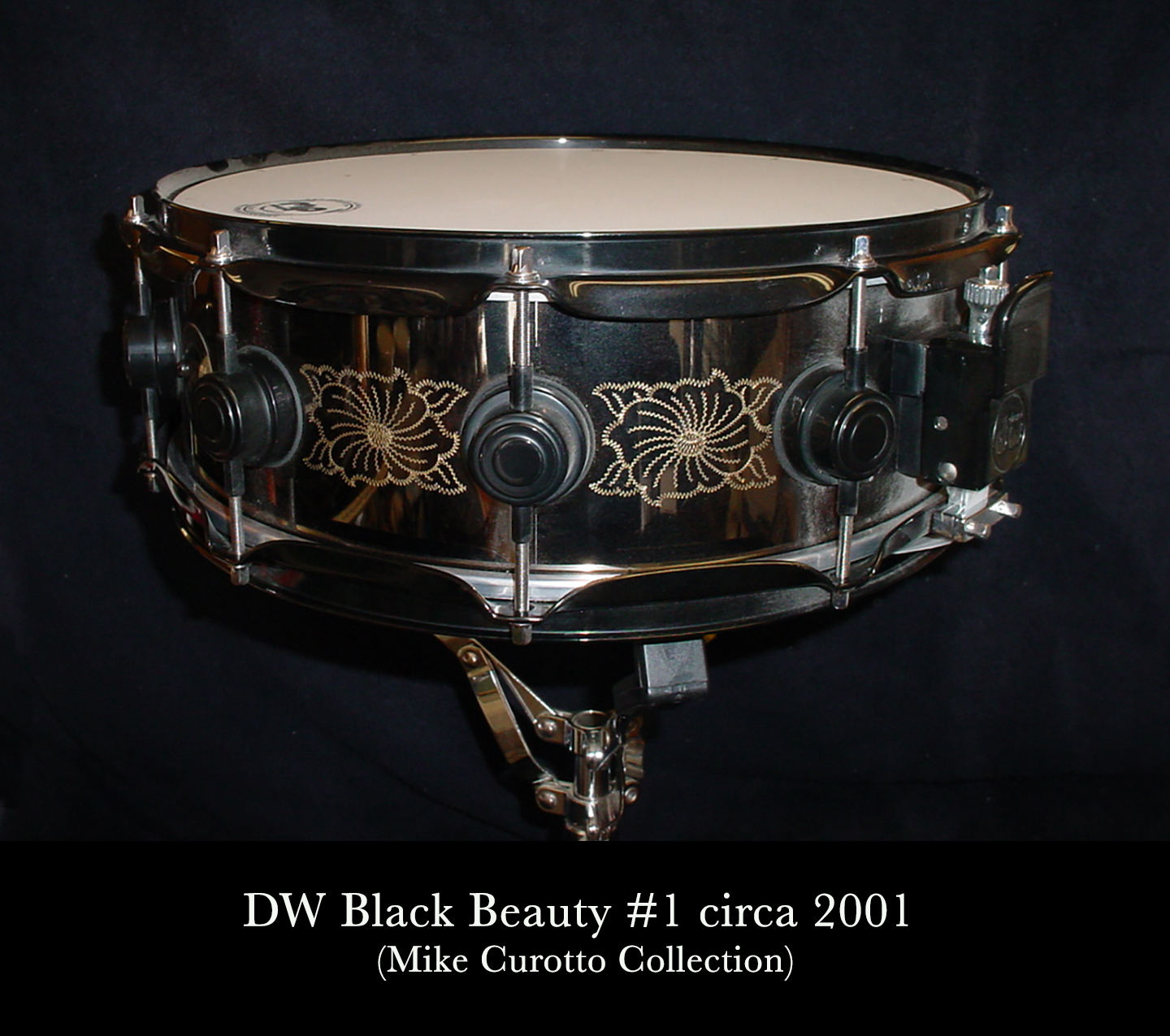
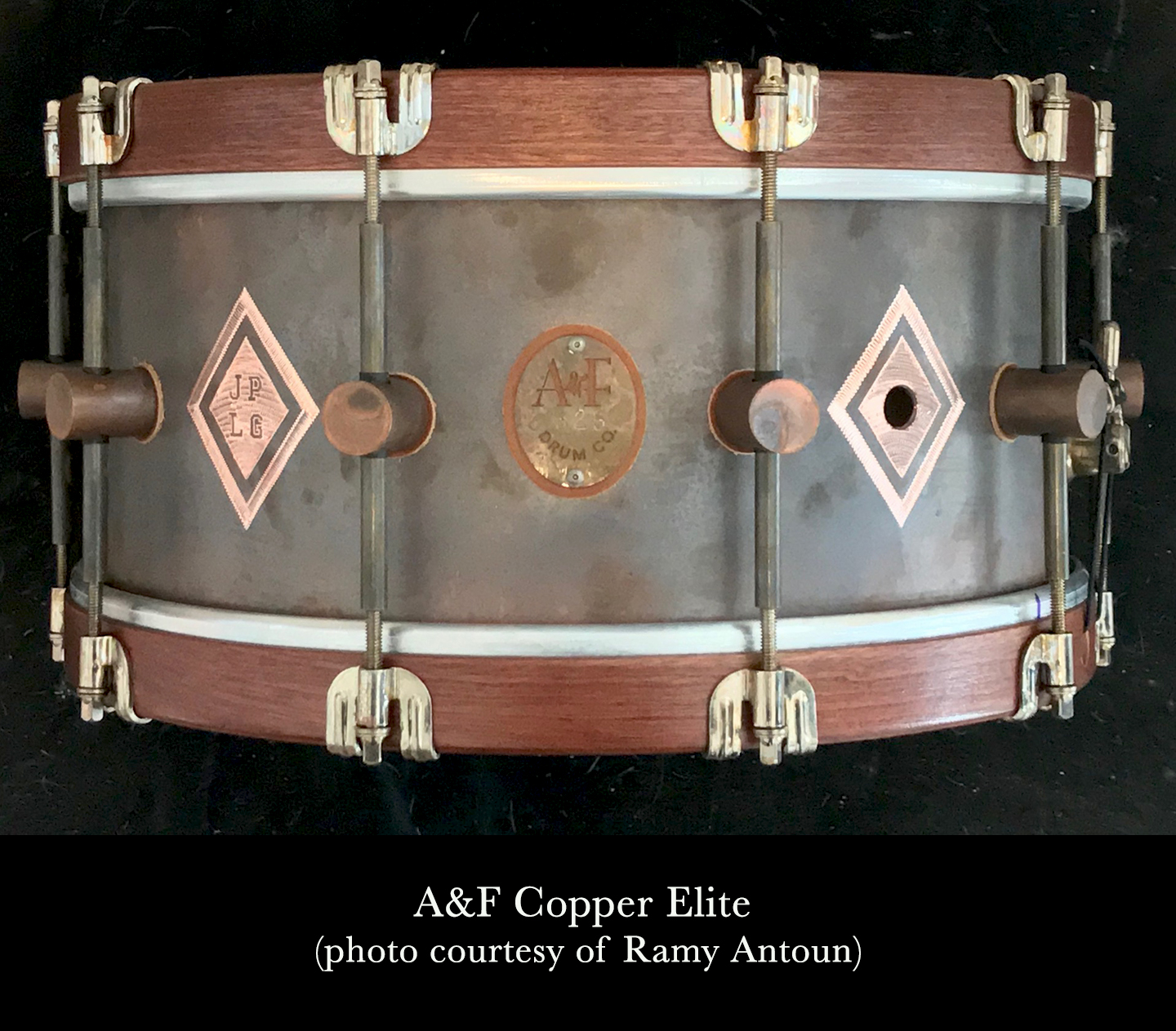
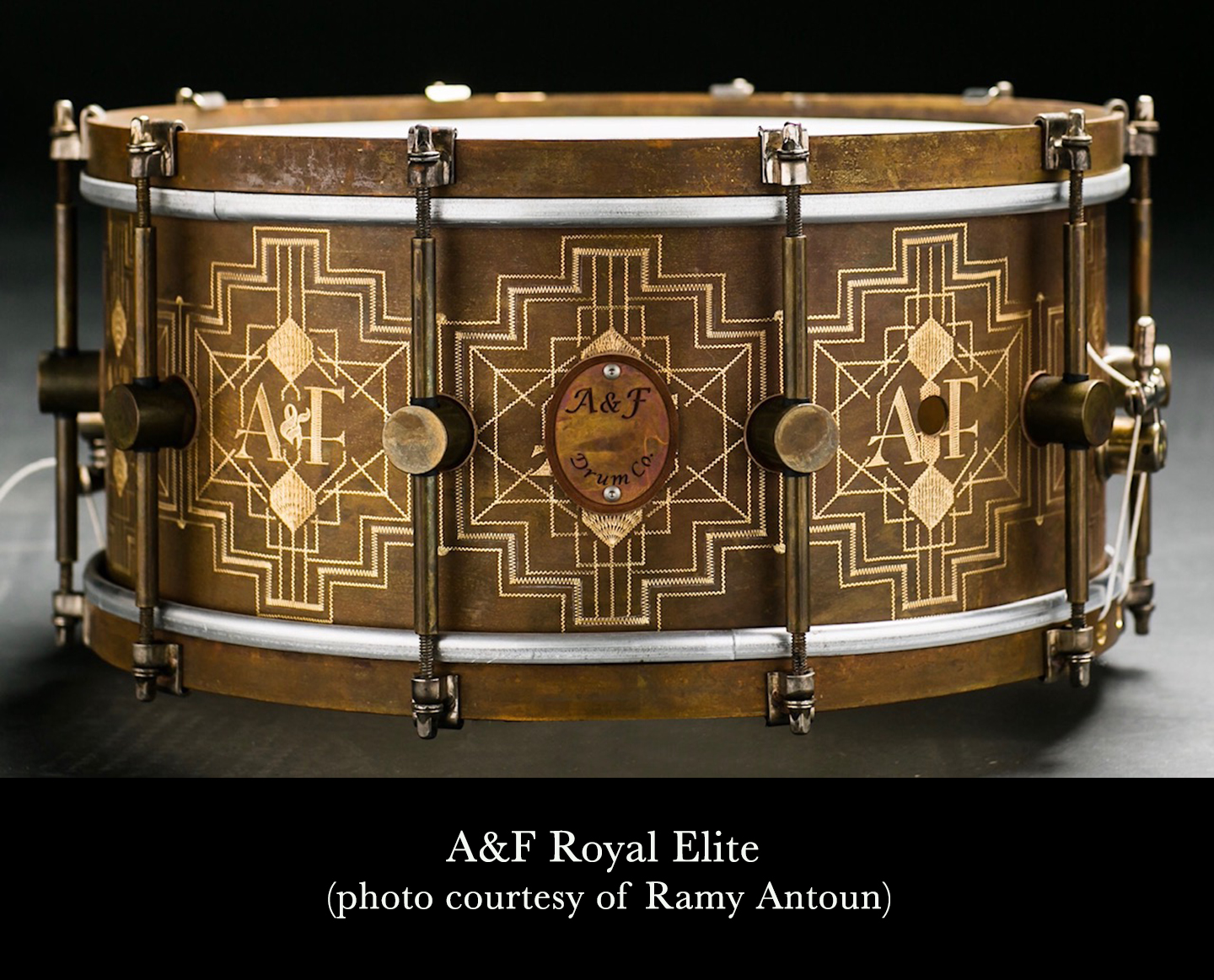
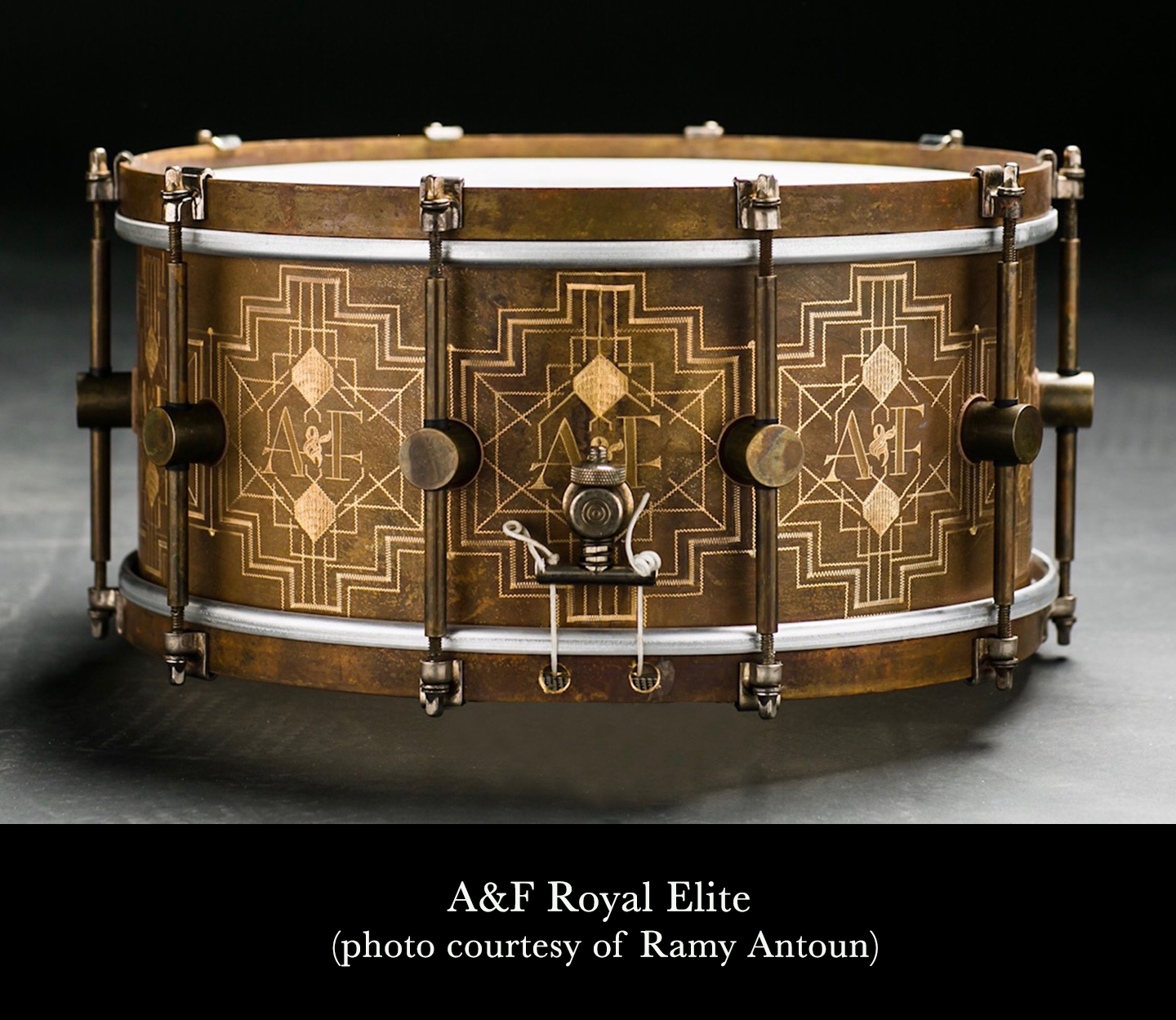
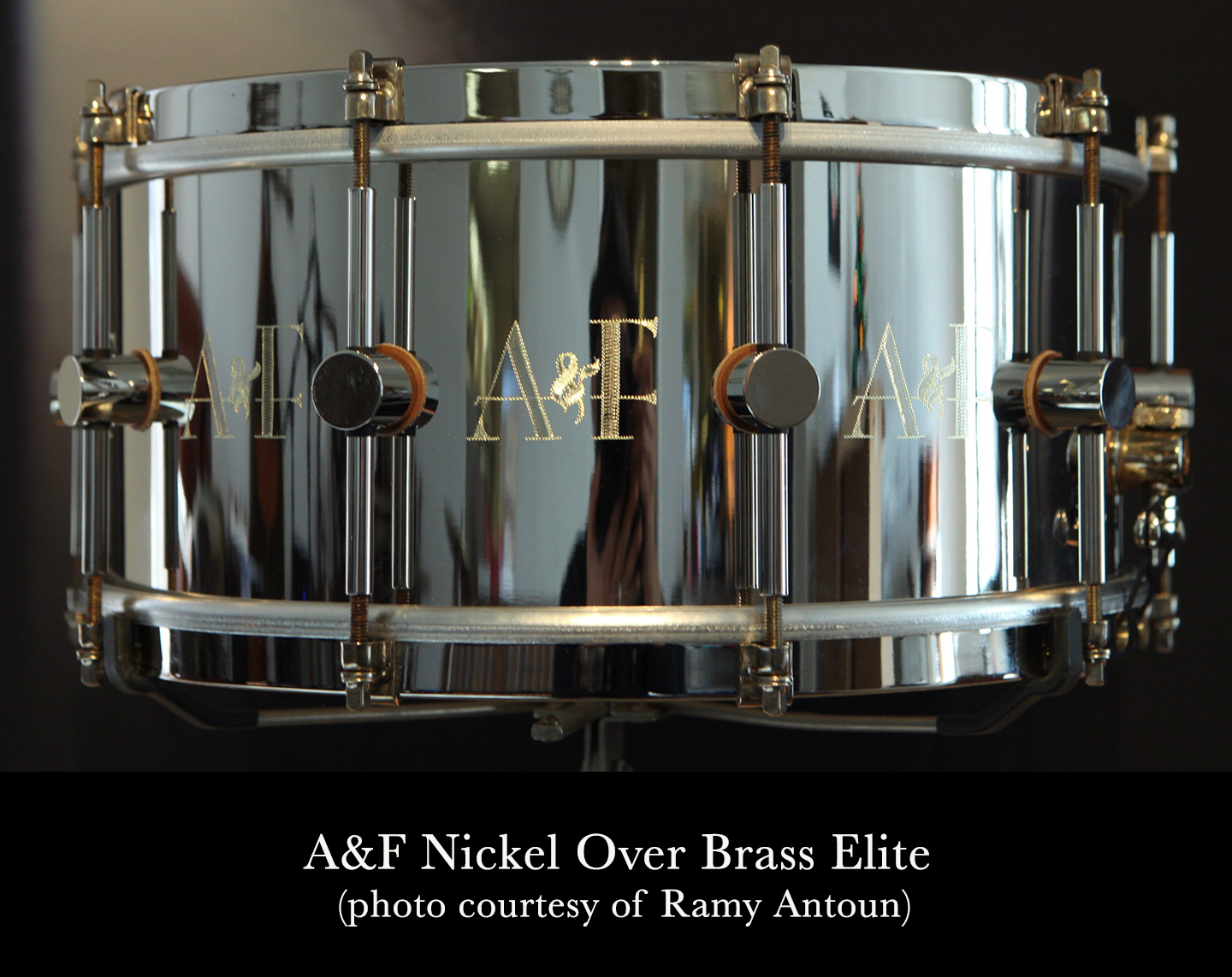
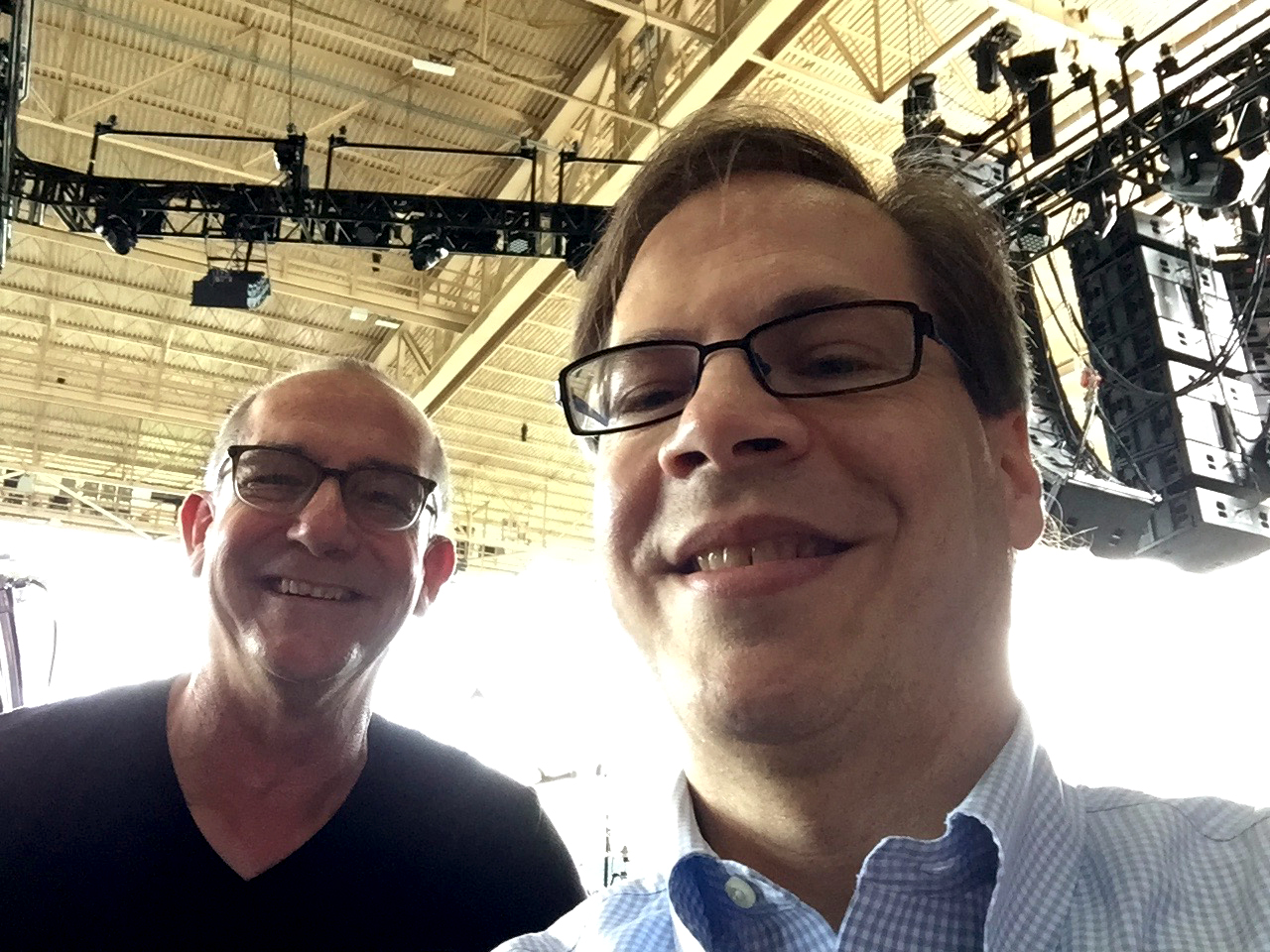
The first of these is the best-known drum engraver of our time, John Aldridge. Some years ago, John Aldridge wanted a hand engraved drum. When he discovered he couldn't afford it, John learned how to do it himself, and brought this lost art form back to the drum industry.
Read moreBook Review: The Tommy Thomas Percussion Library"
Tommy Thomas is a classic example of “the most famous drummer you probably never heard of”.
Read more1970s Ludwig Standard S-330 drum set finished in bronze strata
Standards have their own unique triangular shaped badge. The interiors of the bass and toms are coated with grey speckled paint, but some Standards have white painted interiors. Standards usually have smooth low mass lugs. If your Standard kit has Classic lugs that might also be correct. Ludwig would use the Classic lugs if they were low on Standard lugs.
Read moreBuilding a Stanbridge/Sucherman Empyrean Snare Drum: The Director’s Cut
By Bob Campbell, with Pete Stanbridge and Todd Sucherman
As a collector and player of custom and vintage snare drums, I’m always on the lookout for a drum that speaks to me in a unique way. I believe each great snare drum can evoke a different wavelength of creativity. That’s why drummers should have multiple snare drums in their arsenal (at least that’s what I tell my wife). I like to think that I’m not alone in this respect. In addition, I’ve become enamored of the whole process of drum construction and drum restoration; there is a level of artistry and perfection in the work of the master craftsman that gets my heart racing. A drum that possesses the attributes of fine construction, distinct sound and visual appeal is the best of all worlds (practicality, personality and fine art). The absolute pinnacle would be to document the entire process from conception, to build out, to my hands. This would be heavenly, or perhaps described as “empyrean” (def. “the highest heaven”).
That “ahhhhhh” (imagine angels singing) moment came to me a few years ago when I had the pleasure of chatting with Todd Sucherman after a fabulous STYX show in Indy. When we first arrived, Todd had this strange twinkle is his eye; something clearly had him excited. He waved me over and said, “Look at this!” On his cell phone was a picture of a segment shell snare made of various exotic woods, dark wood hoops and beautiful gold-plated hardware. I had never seen anything like it but it did remind me of Pete Stanbridge’s work (I have the ProMark/Stanbridge 50th Anniversary and Stanbridge Ancient Kauri snares). Indeed it was from Pete. This was a prototype for the planned Todd Sucherman signature snare drum, later to be known as the Empyrean. I felt quite privileged to get an early look, but on the condition that I keep it hush-hush until the public release. Todd described how it was intended to be the most personalized and unique drum ever made, with pictures of the construction along the way, hand-signing and testing of each drum by Todd (including a video to that effect), hand-made walnut case, several signed CD’s and DVDs (Methods & Mechanics I & II!) from Todd, and assorted “toys” made from the exotic wood offcuts. Subsequently, this started an email string between Todd, Pete and me which tells the story of how my Stanbridge/Sucherman Empyrean (#1) came to be. While I have been completely thrilled with this drum in all of its perfection, much enjoyment came from the periodic emails describing each step of the Empyrean’s construction from Pete. It was like a great story where you read each chapter, waiting for a climactic ending, but in the end, disappointed when it’s finally over. Not so much because you didn’t like the ending, but because you enjoyed the story and wanted another. So I’d like to share this “Empyrean biography” with you in hopes that there are also drum geeks in the crowd who will enjoy reading the tale as much as I did.
Introduction:
[My note to Todd] “Todd, it was great to see you in Indy last night. My wife (Helen) and I thoroughly enjoyed the show. I don't know how you play with such intensity in that heat! Musicians like yourself who despite busy tours give exceptional performances night after night always impress me… I enjoy your playing a great deal. While I will never be a drummer like you, I am inspired by your playing and always seek to improve my skills (hopefully with the help of your videos :).
Thanks for showing me the pics of your new signature snare. I will contact Pete Stanbridge today about obtaining one. Knowing your taste in drums, this design looks to be superb.
Wishing you the best.”
---------
After submitting a ton of questions to Pete Stanbridge essentially asking him to justify the cost of an Empyrean (including asking for a second top hoop, i.e., one for playing and the other for display), I received this email:
[Pete S.] “Hi Bob! Thanks very much for your thoughtful and detailed reply - we really appreciate the feedback, and your comments.
I believe that the whole nature of this offering makes it a very difficult comparison with anything that has come before. The 100+ hours I budget for each completed piece is a real number, and that doesn't include Todd's time commitment, or any of the significant material costs of creating this instrument and package.
It remains to be seen what kind of audience there is out there for this instrument. I am sure, however, that neither Todd nor I want to compromise on the package we have created, because we both feel that it really does represent excellent value, and sets a new benchmark in terms of creativity and quality in a percussion offering.
I realize that we are going to take some shots on the forums for a few days, and I have no doubt that there will be people who will become very passionate in voicing their opinions. But, I am exceedingly happy with the work, and if I ever start feeling beaten up by the forum crowd, I know that watching and hearing Todd play this drum will make me feel better.”
[Todd S.] “It's my belief that a drum of such personal detail and care has never been offered in a package so unique. The fact that it comes with a book detailing the manufacturing alone has never been offered to my knowledge. That coupled with it being sent directly to me for playing, tuning, approval, signing, and pics/video detailing that process as well is beyond what has ever been offered. Then getting tickets and backstage passes to a show…I think that takes the package over the top.
I know Pete spends 100+ hours on the drum with materials so expensive and rare that they've never donned a drum before. All these things combined... I can't see any drum out performing it, or out pricing it. Hence, the price reflects the work, materials and package.
A Bugati is a Bugati, and a Fazioli piano is a Fazioli. A Patek Phillipe is a Patek Phillipe, and this is what we set out to do, and I believe we have accomplished just that. Something unparalleled.
Thanks again for sharing your valuable thoughts with us both. It means a lot, and it's fun to have had the opportunity to share with you and only you-- our vision before it becomes reality.
Hope to see you soon, Bob!”
---------
I then decided to be the first to order an Empyrean snare drum…
[Todd S.] “Hey Bob, First off, thanks for the well wishes. My deepest thanks in trusting me along with Pete. I'm happy and proud to have you be our #1! I have no doubt you will be beyond thrilled. I just went and spent about 30 minutes playing in the studio, and on the Empy, and she sings, and has a soul. Everyone of my drummer pals that have played it just melt.
If you haven't seen clips from the new Methods & Mechanics II DVD, here are 2---I use it on the "Melodic" clip and it's of course peppered through the big trailer.
Melodic Song Form: http://www.youtube.com/watch?v=REqodfjCY8Y
14 minute performance trailer: http://www.youtube.com/watch?v=uV_hO2kZixU
Thanks, Bob…”
And so the story begins (each email will be referred to as a chapter).
Chapter 1: The Tease
[Pete S.] “I took a few pictures of the stock for your Empyrean this afternoon, although there has not been a lot of progress beyond sourcing materials thus far. I have a few projects closing by the end of this month, and will be able to dedicate some more time to roughing out your shell blocks in order to get them down to moisture equilibrium soon. I'll shoot some more pictures of all of the wood for your instrument and send them along then. After the Christmas holidays, I will start doing some very gentle microwave drying to stabilize the burl segments, and then I would anticipate beginning construction in earnest in the Spring. I am budgeting one full month of shop time for your drum and accoutrements, although if I need more time then I will take it to make this one perfect.
For now, I thought you might enjoy a mock-up of the basic shell design patterned on Todd's drum, as well as a detail which illustrates the difference between the Amboyna and Afzelia burl eyes (and color). I don't know about you, but this stock gives me chills up and down my spine.”
Chapter 2: As the Drum Turns
[Pete S.] “Hi Bob - Hope you have been having a great summer, and that all is well with you and your family.
As we approach the one-year anniversary of the Empy project, I thought it was high time for an update of your drum. The pictures below illustrate some of the progress to date.
As I may have mentioned earlier, one of the most ticklish aspects of working with this wood is its varying density, which makes drying it without cracking and checking difficult and time consuming. I have had your wood wrapped in brown paper for many months (the paper mitigates the speed at which moisture can leave the wood cells), but in order to make sure that we have reached moisture equilibrium, I prefer to use a microwave drying technique. I stack up the rough cut blocks with small oak stickers between them, and then run each package through the microwave on a very low power cycle a few times each day for about a month. As the water leaves the wood cells, the weight of the package decreases, and when it beings to rebound quickly (within a day or two) I know that we have achieved equilibrium with the surrounding air. If there are no checks present at this stage it is very unlikely the piece will ever develop them.
I also measured an overall weight for just the drum shell wood just so that we can track the amount which ends up as waste through offcuts and shavings.
In image 5485 you can see just how little wood remains as offcuts after the mitering process, although to be fair this does not include the initial rough cutting of the material as it came in from the supplier. With wood this dear, I keep every singles scrap though, and much of it will reappear in some other form later in the project.
I have included a couple of beauty shots to give you an idea of the massive amount of figure in these blocks - every single one has burl eyes and grain swirl in it, and the interlocking effects take on a much more dazzling 3D sort of effect once the shells is turned on the lathe.
Finally, we have a shot with the rings glued up and under clamp pressure, and then after the clamps are removed. Although there doesn't appear to be a lot of colour contrast between the Amboyna Burl rings (1, 2, 4 & 5 from bottom) and the Afzelia Burl, once the finish starts to take hold, it should become much more apparent. I spent a lot of time making sure that the joinery for these rings was first class, and the seams are as fine as I can make them.
The next step is to leave the rings for a few more days, and then flatten them and glue them into the shell blank form, with a faceplate and sacrificial maple ring on one end. I will take lots of photos as we proceed, and now that things are rolling you can expect far more frequent updates.
More soon, Bob - all the best…”
Chapter 3: So Far, So Good
[Pete S.] “Things are good on my end, and I will have another Empy photo update for you in a week or so, but there have been no drying or checking issues with your shell or hoops, and the figure and colours in this drum are going to be really spectacular. I have been using some of the shell offcuts for handles and other elements of your accessories kit, and there are a couple of items that will definitely be one-offs due to the time and complexity of their design. I will shoot a few pictures of that stuff too, although I don't want to give away all of the juice in advance.
All best Bob - photos and commentary will be in your inbox by next Friday.”
Chapter 4: Wood Blocks are not Just for Kids
[Pete S.] “Hi Bob; Congratulations on the Ludwig Triumphal score (note: I had recently purchased a 4 X 14 Ludwig Wild Rose Triumphal from Bun E Carlos) - I know you play your pieces, but you must be spending lots of time just staring at this one too I bet. I would love to come and ogle your collection at some point - probably not in the cards for this year, but I do want to make a junket some time soon.
For the past while I have been working on your hoops, case and throw-off. I am really enjoying spending the time to make every part of this instrument special, and to make sure that I do justice to you, Todd, and the supremely exotic materials. Sorry if that sounds precious.
As I got to thinking about it, I realized that with this drum it only makes sense to include a 'Players Hoop' right from the outset. I did think about having it follow along in a separate carton, but then that didn't seem very Empyrean, so I have redrawn the case so that I can squeeze it in there (I hope). As you will see from the photos following, I am building three hoops for each drum, with each hoop consisting of 25 individual pieces of wood (12 finger-jointed Bubinga blocks, 12 finger-jointed African Blackwood blocks, and one solid inlay stripe of hot iron bent Blackwood). By contrast, most of the hoops I build would use just 10 blocks.
Anyway, here are some photos of your hoops in progress with a little descriptive text below...
6055 - One dandy plank of perfectly seasoned quarter-sawn African Bubinga with a nice Beeswing pattern.
6057 - I cut the plank down into 1.5” strips and then split each of these down the middle to provide a book-matched set of hoop segments. Not a whole lot of this material will show in the finished hoop, but I want to make what is visible as interesting as possible.
6060 - Hoop segments cut to size and resting prior to finger-jointing. Hope you don't mind that I called you Rob - I actually started writing Robert but remembered that you used to only hear that when you were in trouble with your Mom. Notice how vertical the grain is running in this wood - this is called quarter-sawn stock, which contributes greatly to the stiffness and durability of the hoops.
6065 - Badass joinery being dry fitted with the balance of your Bubinga hoop blocks looking on.
6070 - I generally use a number 2 grade African Blackwood for my projects and cut around flaws and checks. With the Empys I sought out a beautiful premium grade Blackwood which has almost zero defects and a much more consistent color and grain pattern than the stock I am used to. Here I am re-sawing a block for your hoop blanks using a couple of gnarly old push sticks on the band saw. You can see from the scars their necessity.
6083 – Finger-jointed and ready for the big glue-up. I love working with this material - African Blackwood fills my shop with the most amazing sweet Rose-like scent.
6102 - Blackwood and Bubinga hoop rings glued up and ready to be flattened, sanded and then glued together in pairs. As an added precaution against potential woes in the distant future, I am using an epoxy to bond these layers together, so I need to get them lined up properly the first time or it is all over.
More to follow very soon Bob!”
Chapter 5: One Piece at a Time
[Pete S.] “Hope you are doing well. Here are some more photos of your drum in progress.
5594 - For most of my drums, I will use a thin strip of wood inlaid into the outer shell surface if I want a contrast stripe. With the Empy’s, that seemed like cheating, so the stripes are made of solid African Blackwood which go completely through the shell. This is a lot more work though. Here are the Blackwood shorts being sanded to precise thickness.
5598 - the center section of Afzelia Burl has been flattened and sanded top and bottom, and the Blackwood segments are glued and clamped in place individually.
5603 - More Blackwood segments glued in place. The nice thing about doing these one-half at a time is that I can 'tune' the final block to fit perfectly with no gaps at all. The downside is - it takes a whole lot of time!
5612 - Rings 1&2 and 6&7 get glued up in pairs. Again, in one of my traditional snare drums, I would glue the rings together all at once in a custom built vacuum press. With the amount of money and time sunk into these blocks though, I feel way more comfortable using the much slower but more controllable clamp approach.
5613 - The center section (centerpiece?) of Afzelia and Blackwood glued up and sanded to silky perfection. All that remains is to flatten the Amboyna ring pairs and glue the whole shell blank up into...
5625 - ... a very lovely pineapple. I'll start coring the inside in the morning, and very soon this shell will be ready for the beginning of the finishing process.
More soon Bob - I have also been working on a bunch of your goodies in the background, and have a couple of pretty cool items that I think you are going to love.”
Chapter 6: Exploring the Woods
[Pete S.] “Please find attached some progress photos of your Empyrean. Working with Amboyna burl is a bit of a double-edged sword - the material is beautiful and utterly unique, while also being extremely finicky due to the many voids and bark inclusions that produce its amazing figure.
I can honestly say though, that this is one of the finest drum shells I have ever built. The joinery is exactly what I was shooting for, and the wild grain and colour in both the Amboyna and Afzelia burl are off the chart. I want the shell to be perfectly flat across its depth so that the gloss reflections are dead straight, and this takes a great deal of care due to the different densities of the African Blackwood and Burl woods, but I feel great about the way this one has turned out. It is also really important that the sanding prep before the pore filling and high gloss stages is done right and that all of the sanding scratches are removed before I change to a higher grit sandpaper. This takes a lot of sandpaper, good lighting and an eye loupe, but most of all patience.
Here are some progress photos with narrative from the last couple of months...
5633 - The outside of the shell is rough turned oversize to reduce the weight and provide a round exterior surface for the next step.
5638 - In order to minimize harmonic vibration and chatter while the shell is spinning, I dampen the free end of the shell with a shop made steady-rest built from a pair of inline skate wheels (retracted in foreground). This reduces chatter and makes for a much better interior surface finish directly off the tool.
5877 - Gorgeous grain swirl and burl eyes a plenty. Although the white balance was wrong in these two pictures, I think you can see why this is the most expensive and prized wood in the world. The shell is still about 1/64th of an inch proud here, but will come down to exact OD with a few long sanding sessions. To get this piece ready for pore filling, I hand sanded with 120, 150, 180, 220 and 320 grit sandpaper before moving to a Random Orbit sander to get rid of any radial scratch pattern. Total time sanding was about 8 hours over three days.
5880 - This is the interior surface directly off the tool - it looks pretty good, but there are still some small radial grooves visible. In order to make the inside smooth and ready for sealing, I spent 3 hours with a sanding block to bring it into perfect focus. The inside is sealed with a few very thin coats of shellac.
5884 - Into the finishing shop. Here a sealer coat has been applied, and the first application of pore filler has been squeegeed onto the surface and baked in my UV oven. This material dries rock hard and must be sanded flat so that it only remains in the pores and voids of the shell. Normally I would use two coats to completely fill the grain - with this wood I am using four. Each cycle takes about half a day to apply, cure and sand back.
5898 - The pore filler is clear so it doesn't alter the appearance of the wood. I use an eye loupe to check for sink-outs in the finish - it is hard to tell from the picture, but this shell is completely filled and just about ready for high gloss. Just a little more... sanding.
5931 - This is the Black Walnut for your drum case. I will re-saw this one plank (12 inches wide by 1.5 inches thick by 72 inches long) to produce a four corner matched case. Still haven't decided on all of the interior fittings, but I will be working on this over the next few weeks, and I will send you some pictures as we proceed.
More soon…”
Chapter 7: Getting on my Case
[Pete S.] “Hope your summer has been going well and that you had a good time with Todd the other night. Please find following some more pictures and commentary regarding your project. I am still on schedule to ship your drum to Todd during this break from Styx dates, so I am hopeful that you will be seeing her in early October as I mentioned in my last message. More to follow as we get closer to a ship date.
Hope you are well Bob - thanks again for your patience and support.
All the best…
6234 - Here are the Black Walnut planks I have chosen for your drum case after being re-sawn. By splitting the boards and book matching them, I can create a 4 corner grain match that flows around the drum case.
6260 - I don't want to give away all of the bells and whistles, but here is the plywood mock-up for your case. It has a bunch of cool features and the inside is going to look dynamite as I am working with a very talented local textile artist on the plush interior.
6336 - One again, here is your sealed and pore filled drum shell prepped for the spray booth and my tried and true UV cure high gloss.
6350 - A final scuff sand prior to applying the Todd signature, and shooting the first three coats of high gloss. The quality of this burl is astounding - every segment is like a little painting.
6365 - Three coats down, another 5 to go. This picture is from a couple of weeks back and the shell is now complete and ready to be finish sanded and buffed.
6394 - In the meantime, I have been working on your hoops. Here I am truing up the hoop blanks in preparation for drilling the tension rod holes. I built a super cool measuring jig (using a laser pointer) to indicate some of the major diameters, but all of this work is done by hand.
6396 - Next, the hoops are locked into a rotary indexing fixture I designed, which allows me to drill any number of equally spaced, accurate holes in hoops from 6 to 26 inches.
6403 - Turning African Blackwood is both a challenge and a joy. It is necessary to re-sharpen my chisels and gouges after only a few moments of contact with this incredibly hard and resinous wood. But - the finished surface really is incomparable.
Chapter 8: Can You Box That To Go, Please?
[Pete S.] “Hope you are doing well and getting into that Fall kind of groove. We have been having some beautiful days recently, including a number of high temp records and a bearable amount of rain, so no complaints about the weather (for the moment). I did just make my appointment to get the tires swapped over to our winter studs however.
Here are some photos of the progress of your Empy over the last few weeks. I have spent a great deal of time on the case and interior, as well as all of the little amenities that will be nestled on board. At present, the cases are with the artist who is doing the interior fabric and foam. We have done a bunch of different hand dyed textile samples and I think the finished effect is going to be great.
6427 - I'm making an African Blackwood pen here - at over 2,000 pounds, this is perhaps the largest lathe ever used to turn a 2 oz. pen.
6430 - I tried a few different designs for drum key handles before I settled on one I really liked. This is an 'also ran' in Afzelia Burl.
6434 - In order to achieve the best 4 corner grain match, the walnut for the drum cases needs to be book matched and laid out properly. I really didn't want to mix up any of the parts after all of this work.
6436 - Here I am cutting the box joints for the case joinery on my table saw. It takes a good number of test fits before the jig is dialed in to run the actual parts.
6437 - Woot! - didn't mess up and the boxes fit together with a satisfying amount of persuasion.
6440a - Much sanding is required to prep the boards for finishing. I used three coats of Danish Oil followed by paste wax for a baby's bum smooth surface.
6441a - Another of those operations that could go horribly wrong (but didn't). After they are glued up and the finish is applied, the lids are cut off the cases on the table saw.
6444 - The spare 'Player's Hoop' rides along in the lid of the case, along with a pair of Todd's signature PM 330s.
6446 - I decided to build a sweet little Rosewood box to hold some of the luxury items accompanying the drum.
6447 - Still not sure how I will hinge the lid, but something will suggest itself I'm sure. They kind of have a baby grand feel to them I think. Holy Faziloi!
6451 - Of course the primary purpose of the case is to protect your Empyrean, so the structure of the insert and surround is very important.
6453 - These babies are ready to ship out for the interior fabric install. I don't do a lot of flat work (as the wood-turners would call this), but it is satisfying despite being excruciatingly slow.
I'm back to finishing up hoops and shells, along with all of the million other little details that these drums require. We're very close to a ship date now - I have been keeping in touch with Todd regarding his schedule so that we connect during a break from touring. Hopefully I'll be able to have these in the air in the next couple of weeks. I will keep you posted.
All the best”
Chapter 9: Exotic Toys for Drummer Boys
[Pete S.] “Here are some pictures and commentary from the past few weeks. I have been working through the last details for your project, and we will soon be ready to ship her off for Todd's shakedown, but I want to make sure I am happy with every aspect of the instrument and package before it moves on. Its almost complete and I am pretty sure that you are going to love it. As you can see, I tend to make a number of variations for each item in the extras box - let me know if there is something that you really love, but otherwise I will just make sure there is a nice variety of wood species.
Here are some photos and commentary…
6466 - A few of the pens I have completed - from L to R we have Big Leaf Maple Burl, African Blackwood and Cocobolo.
6468 - Some keychains in (clockwise from the top) Roasted Birdseye Maple, Curly Maple, Amboyna Burl, Ebony and Snakewood.
6471 - Drumkeys (clockwise from top) in Maple Burl (w/ chrome), Cocobolo, Amboyna Burl, Curly Koa, Cocobolo (w/ chrome), Figured Cocobolo.
6482 - Here is the case lid. Local textile artist Kumi Stoddart dyed the fabric using fern leaves as a resist to create the patterns, and hand-stitched the lining and foam cushioning. I'm really pleased with the overall effect of the textile, and each case will be completely unique.
6494 - Here's a shot of your throw off handle (prior to Swarovski’s). I used 3 pieces of Amboyna Burl with 2 sections of African Blackwood for strength and stability, and epoxy to hold it all together for the long haul.
6506 - Each hoop receives an African Blackwood pinstripe made from solid stock. I carefully cut the Blackwood on the bandsaw and sand it to precisely .124 of an inch to press fit into a .126-inch groove. I pre-bend the inlays using a heat gun to avoid cracking them while installing, and scarf joint the ends so the seams are invisible.
6510 - The inlay is glued into the groove and clamped up overnight, then the hoops are sanded perfectly flush and the finish is applied.
6513 - These are solid wood badges with gold foil embossed on Amboyna Burl and African Blackwood - let me know which one you would like on your instrument.
6514 - Here is the seam in the Blackwood pinstripe after sanding - it is dead centre in the photo. Not bad, eh?
6519 - And finally, the case with almost all of the bells and whistles in place. Hope you like it - I think it does the drum justice nicely
All Best - more news soon…”
Chapter 10: All Lacquered Up and Giddy
[Pete S.] “Great speaking with you just now, and I forgot to ask if winter had overtaken you yet. We got a few inches last night, but hopefully that is the end of it for a while.
Here are a few more shots of your instrument in progress. I didn't include any pictures of your hoops, but they are completed as well, so we are really getting down to the final few details now. I'll keep you updated on the shipping status to Todd over the next week or so.
6558 - The final wet sanding stage, after many hours of power and hand sanding. To bring the lacquer up to a high gloss, I start by machine sanding through 800-grit, and then wet sanding by hand to 2000.
6561 - This jig allows me to spin the shell (slowly) and hand cut, sand and polish the bearing edges to any profile. I use this jig to rotate the shell while I hand cut the bearing edges with lathe chisels. Notice my little shop-made steady rest reducing vibrations in the foreground. Sadly, my daughter can't find her inline skates these days.
6564 - After the edges are finished I use a stationary buffing machine and a number of ultra-fine compounds to bring out the gloss in the body of the shell. The completed shell after polishing. The burl looks like it is buried under glass.
6565 - Looks pretty darn shiny I think. The wildly interlocking grain in the burl is kind of mesmerizing.
6579 - More green tape. Remember the old adage - measure 4000 times, drill once. It still freaks me out to map and drill holes for the hardware - nowhere to hide if I screw up here. She's mapped out and drilled and now I can exhale.
6580 - My heart rate returns to normal after the tape is gone and I have verified that the results are perfect – Wowza! The way light shimmers and refracts when you look at some woods from different angles is called chatoyance. Yep - this baby's got that in spades.
Hardware tomorrow. I'll let you know how we are doing very soon.”
Chapter 11: An Empy is Sighted in Canada – News at Eleven
[Pete S.] “Happy New Year! We left Newfoundland to travel to Ontario to see the extended family on Dec. 18th - just in time for a major ice storm that brought down about 25% of the trees in my parent's community, and knocked the power out for the better part of a day. Their place escaped major damage but the neighbours took a direct hit from a Maple tree and lost their brand new deck. After lots more snow and cold conditions in and around Toronto, we flew back home on New Year's Eve to find that St. John's had been buried under 120 cms of snow over the time we were away. On January 2nd the power utility started rolling blackouts in an effort to stave off a major outage because of the increased electrical demand from the cold temps. Unfortunately, this didn't work, and January 3rd our power went out for 30 hours during a blizzard with the temperature at minus 19 and wind speeds of 120 kph. Another 40 cms of snow and a half dozen more blackouts over the next few days kept things frosty and uncertain, so schools remained closed for three days until the grid was stabilized. We have a generator to keep our well pumping and the fridge and freezer running, along with one room heated, but once my stockpile of gas started running low we discovered that every station in town was out of fuel. Fortunately it has started to warm up a little today, and we are looking at a fairly mild stretch for the weekend at least.
So, it has been quite a start to 2014. Needless to say, I haven't spent much time in the shop up until now.
Your drum however is done, and I am just working on a few additional details with the case and accoutrements. The drum is amazing - I am very proud of this one, and can't wait for both Todd and you to have a chance to shake it down. My plan is to have it out to Todd in the next couple of weeks so that it is waiting for him after this run of shows, and then we'll bring together the final elements to the package. I'm including some progress pics and will be shooting the 'catalogue shots' in a few days - I'll forward these once they are done.
Hope you had a great Christmas holiday Bob, and all the best for 2014.
Photo details are as follows...
6582 - Case is almost complete - I have only a few little details left on the exterior (like a Todd signature).
6585 - Custom fitting the accessory box is time consuming but very fun for a wood nerd like me.
6600 - Yowza! She's a total babe, and I think you are going to be floored by this one.
More soon”
Chapter 12: One Step Forward, One Drop-kick Back
[Pete S.] “Some troubling news from Todd today. He arrived home this morning and discovered that the Empy case had sustained some shipping damage sometime during its long journey from me to him. He suspects that it was dropped on one corner with enough force to split the 5/8th-inch solid Walnut panel in the lid section. I had sent it via Canadapost Expresspost, as I have had very good luck with them - this being only the second piece they have ever damaged. The carton I used to ship was the biggest they allow, and despite a healthy amount of bubble wrap, it didn't stand up to their abuse I guess.
The bright sides are as follows…
The drum itself is perfect - there is not a scuff or any damage whatsoever. I have another identical case that I will have complete by Friday - I just need to add a couple more embellishments and get the accoutrement insert done and she will be ready to go.
This time I will be shipping via UPS - it is considerably more money, but they will take a larger carton so I will do a double box thing and we will be fine.
As you can imagine Todd and I are both supremely bummed out by this and can appreciate how you must feel about it too. I'm including a couple of pictures to tide you over until you have the drum and case in hand. I'll let you know when the replacement box goes out and the ETA to Austin.
All the best…”
Chapter 13: In God We Trust; the Postal Service Will Take More Prayer
[Pete S.] “The new case and accessories are on the way to Texas and are guaranteed by next Thursday. I am using Purolator this time around, so hopefully they will be more gentle than the nasty Posties, although I have packaged this baby up like… well… a baby, so I am expecting a safe trip.
More soon - all the best…”
Chapter 14: And in the Beginning, There was an Empyrean
[Todd] “Hi Bob, I bring good news!
The box arrived safely today. I have spent part of the day in the studio tuning it up and taking pics and vids. Pete and I feel that we should send the luxury accouterments and other special things in a separate box than the one that contains the drum. While this takes away a bit of the "wow" factor when opening the box, it creates a "safe" factor that will stand a greater chance of everything arriving in a pristine state. So that notion wins the day. All the luxury items fit inside the case, there a space for a pair of sticks, all this will be obvious and of course as shown in the picture book that Pete is sending you directly.
I was hoping to ship this out tomorrow but Monday looks like a greater reality, as my mother is in for a visit and it's evening time late on Thursday. I know my UPS guy so I can set something up for a Monday pick up with swift ease. Sorry to add a couple extra days, but it will all be worth it.
I will send you tracking info and please let us know when the eagle lands. We await your feedback, and we hope you are as thrilled as we are. You are #1 in the most personalized signature instrument ever offered before in history. From my home to yours (originating at Pete's of course!)
Thanks, congratulations, and I will email you on Monday
Cheers, Todd
PS. Here's a teaser...”
Chapter 15: The End and The Beginning
Note: I had surgery on my thumb (tendonitis, a.k.a., Trigger Finger) the day my Empyrean arrived.
[Pete S.] “Thanks for the message and I hope your hand will heal perfectly and quickly.
I'll admit that I have been holding my breath for the past few days, as the prospect of the drum or this case being damaged would have been a little bit much for me after all of this. I am including a couple of shots of the interior of the case, just so that we are on the same page about how things fit together, even though I'm not sure if you have the time or mobility to put it all together yet. You will notice the little spiral bound photo album in the photos - this was for the first case and accouterments package, so I redid it with the new gear and it is on the way to you by mail - should be there very soon. The idea is that this fits in the little padded pocket with the Styx CDs and DVDs.
Thanks for your stoic patience throughout this project. It obviously took some twists and turns that none of us were expecting, and I have to admit that I seriously underestimated the complexity of some of the elements of this whole concept. However, I am extremely happy and quite proud of your instrument and all of the accompanying bells and whistles, and I do feel like we have created something completely different and special here. I look forward to chatting with you soon, and hope for a speedy recovery for your paw.”
[Bob email to Pete & Todd] “Well, my dream snare drum has arrived. My wife helped me unpack the drum today - truly stunning! The case is really wonderful (and heavy). Well worth the wait. Thanks so much. I only wish I could play it. It will have to wait. Todd - thanks for the vids! Very nice collection of exotic wood toys and cool stuff to add to my shrine of Todd/Taylor/STYX. The pics of the drum in progress are particularly special to me.
That’s the limit of typing for today…hurting a bit now the anesthetic’s worn off…
Thank you Pete for your meticulous attention to detail. It really pisses me off though that I can’t play it! When my hand deals, it will definitely be the first drum I play!”
Chapter 16: Epilogue
[Bob to Todd] “Doing much better - thanks! Can play only a limited time and nothing with any great dexterity. Just happy that it only hurts a little... Loving my Empy!!!”
[Bob to Todd] “Had a good time playing the drum today. My hand is much better since the surgery. Glad to have my thumb functional again! BTW, this drum sounds as good as it looks – phenomenal!”
So was it worth it? Did the drum speak to me (without alcohol or drugs)? Indeed, it is one of the most breath-taking wood shell snare drums I’ve ever seen or heard. I continue to enjoy the way it sings when I play (and exponentially more so when Todd plays!). The wood hoops warm the tone, add some punch and produce wonderful, articulate cross-sticking and rim-shots. The sensitivity is to die for. I’ve had friends come over and play, and they’ve been equally impressed.
Richie Jarvis (freelance drummer, Australia) was the recipient of Empyrean #2 and was equally blown away by the sound, look, and build quality.
"Just after NAMM 2015 I took delivery of of my Stanbridge/Sucherman Empyrean (Build No 2 ) and from the first opening of the case I was in love with this fine piece of art but I wasn’t able to really to give the drum a proper shake down until my return.
Once home I soaked up what I would call the ultimate collectors snare drum down to the finest details like the Swarovski crystal in the snare drum lever, then came the fun part. The tonal range of this hand made drum was phenomenal with an overtone was dark and very chocolaty tuning from the low “baseball bat to a pie” all the way to “crank city” it was simply breathtaking but no matter where the drum was tuned it never lost its personality.
One major test I have with any drum is the rim click and I was not disappointed with a rather potent but very pleasing woody crack, The Empyrean from the rim click, ghost notes to a full blown shotgun like crack has a refinement of pure class at any volume and volume this drum defiantly has.
Recently my Empyrean was on loan to Todd himself on the Melbourne leg of the Drumscene live tour and he made the drum sing, from a medium tuning point this got the entire backline staff's attention and started to draw in a small crowd to not only see Todd’s playing but to see the beauty of The Sucherman Empyrean. I think what really amazed me about the drum after that weekend having seen it being played by the man himself at full force, no holes bared hard hitting playing was the wood hoops…….not a single mark was left, simply one of the most amazing pieces of drum art ever to be created."
This drum is one for the history books. I hope that someday 100 years from now, this drum will have been passed down to another, and that owner will value not only its beauty and character, but also the pedigreed history that it embodies. In each Empyrean, there is the spirit of both Todd and Pete, an essence that lives as long as we remember this drum’s story. An Empyrean is born; long live the Empyrean.
---
Empyrean Specs: 6.5X14” segment shell drum (5/16” thickness) with high gloss finish, consisting of rare exotic woods: figured Amboyna Burl, Afzelia Burl and African Blackwood; African Blackwood and Bubinga wood hoops. Fitted with a modified Dunnett throw-off with Amboyna Burl handle and Swarovski crystals. All hardware is 24K gold-plated: 10 Stanbridge brass tube lugs, tension rods, throw-off, butt plate and air vent. Each drum has Todd Sucherman’s signature in gold on the outside and a paper tag on the inside with the serial number, date and hand-written signatures of Todd Sucherman and Pete Stanbridge. Each drum comes with a unique Black walnut presentation case lined with foam and velvet.
IN MEMORIUM: Ralph Morris Penland
IN MEMORIUMRalph Morris Penland (1953 – 2014)(Including a previously unpublished interview with Ralph)
by Bob Campbell & Paul Mason
It is with great sadness that we share the news that Ralph Penland, an amazing teacher and performer, passed away on March 13, 2014, at the age of 61. Ralph was one of unsung heroes of the music community; a kind and modest drummer whose accomplishments spanned several decades. He started out in Cincinnati, Ohio where at age 9, he took up an interest in music and drums. At age 15, he bought his first drum kit, and within two years, he was playing as featured percussionist for the Cincinnati Symphony. By age 19, he began playing with the great Freddie Hubbard and his career took off. From 1973-2013, AllMusic (http://www.allmusic.com/artist/ralph-penland-mn0000388206/credits) listed 164 credits for Ralph Penland in roles as drummer, percussion, arranger, producer and/or composer. He played with some of the most influential artists of our time, such as Chet Baker, Natalie Cole, Miles Davis, Herbie Hancock, Freddy Hubbard, Hubert Laws, Etta James, K.D. Lang, Buddy Montgomery, Carlos Santana, Frank Sinatra, and Nancy Wilson just to name a few. Ralph was also an educator, having taught at the New England Conservatory early in his career and then more recently in the Jazz Department at Pasadena City College. He also led his own band, the Penland Polygon.
We each had the opportunity to speak with Ralph at various times in his career – Paul Mason as the owner of Tempus Drums (whose drums Ralph played) and Bob Campbell as an aspiring writer. It seemed altogether fitting to share our personal experiences with Ralph, including a previously unpublished interview from 2002. Please note that the interview was for a book on snare drums, so there are many snare drum-focused questions.
Paul Mason:
I met Ralph when he visited my booth at the January 1986 Winter NAMM Show in Anaheim, California. To my discredit, I did not at the time know who he was, although that changed quickly as I got to know him personally and learned of his already impressive résumé.
Ralph and I kept in touch during the following months and years, a time during which I was always happy to see his career very deservedly taking him farther afield and putting him into musical settings with an ever-expanding circle of brilliant and diverse artists. And yet, for all that he seemed always to be playing/recording with a literal Who's Who of jazz greats (not to mention his performing with such widely disparate musical giants Santana and Frank Sinatra and rehearsing with Allan Holdsworth), Ralph somehow never became one of “The Names” in a way that I felt he'd earned.
The man, quite simply, could play. He was an absolute natural, genuinely gifted in the truest sense of the word. And he had a boundless enthusiasm for music, something which was apparent from our very first meeting when I got to watch him sit and play as part of a spontaneous percussion improvisation with Billy Cobham, who was trying out the exquisite metal instruments of Pete Engelhart at the booth right next door to mine, as well as a conga player who joined the fun at the booth beyond that.
Or, to put it another way, Tony Williams once described Ralph Penland as his favorite drummer.
Ralph seemed to love my work. He'd visit at every trade show, purely so that he could sit down at a set and play. He eventually had me build him a custom set which he went on to use in a variety of musical settings, both live and on record. And I made a point of hearing him play wherever I could, whenever we both happened to be in close enough proximity for that to happen. Between those times he'd call from various places around the globe, always on tour with some other luminary; this week perhaps just back from Japan with Pharaoh Sanders, next into the studio with Dianne Reeves. One project about which Ralph was extremely excited was a proposed recording with Allan Holdsworth; he called me one day just to play me an answering machine message which Allan had left at his home number, Holdsworth phoning to set up rehearsals for what would become the ‘None Too Soon’ album on which, unfortunately, Ralph did not end up playing.
We became friends, at least as much as two people can do when they live 1200 miles apart and see each other perhaps once or twice a year. His then wife, Linda Lawrence, was a lovely woman, and I watched Linda's son Trevor grow from a young boy into a successful artist in his own right, inspired early on by Ralph's encouragement and input. Conversely, in late 1989 my wife, Shelley, and I took our newborn son Taylor to see Ralph play with Freddie Hubbard and George Cables; just a couple of pals hanging out.
And although he occasionally voiced his frustrations with the constant struggle of being a jazz drummer, Ralph never complained about his life; he was genuinely appreciative of the opportunities he'd earned through his formidable talents. Those of us who knew him and admired his accomplishments were perhaps in the minority but I always firmly believed that, one day, he would be awarded at least some greater degree of acclaim from the larger drumming community.
I miss him. Fortunately, I'll always have his music.
Bob Campbell:
I was introduced to Ralph Penland by Paul Mason (Tempus Drums) around 2002 as I was doing some research for a book. We did an interview over the phone that, for various reasons, was never published. He came across as quite knowledgeable, personable and passionate about music and drums. It was a privilege to speak with him.
An Interview with Ralph Penland, drummer extraordinaire (2002)
Ralph, could you tell me a little bit about your musical background?
I went to Boston after graduating. I wound up in a program teaching at the New England Conservatory, in the early 1970’s. They had a special program where they were opening up music to the community, to the inner city students, and I was on the faculty and was teaching. Also, in Boston I had the pleasure of hanging out with a lot of great musicians that were up there. I never studied formally with Alan Dawson, but we did kind of hang out. In my second year at Boston, I had the pleasure of sitting in with Freddy Hubbard. That actually starting my playing with him. From the age of 19, I was on the road playing with Freddy Hubbard. We started working almost immediately. I started playing and recording. We did a record on the CTI label called “Keep Your Soul Together” (1973). There was another one on Columbia called “High Energy” (1974). It was kind of off to the races. Things kind of came along quickly for me. So it was awesome; I was very honored and fortunate.
So of all of the work you’ve done over the years, what are you most proud of?
That’s kind of hard because I did a lot of things. In addition to joining very early with Freddy Hubbard, I can mention a few names. I had the pleasure of working with Amad Jamal, Charles Lloyd, Nancy Wilson, Stan Getz, Toots Thielemans, Sara Vaughan, and Ron Carter. I played with Herbie Hancock, Pharoah Sanders, Joshua Redmond, Wynton and Bradford Marsalis, Harry Connick, Jr., Wallace Roney. I’ve done commercial music. I worked with the Supremes briefly, Marvin Gaye. It covers the board. Steve Vai, Brian Auger, Robben Ford, George Benson and Frank Sinatra, Carlos Santana. I’ve played blues with Etta James. I did her last two albums. Music soundtracks, a couple of comedies…’Throw Mama From the Train’, ‘When Harry Met Sally’, a documentary of Chet Baker, Sean Connery’s ‘The Russia House’, ‘Midnight in the Garden of Good and Evil’…I did that. So there’s a lot of music I’ve had the pleasure of touching on that’s helped me, helped my life and my career to be versatile. That’s very important to be versatile in music…oh, and I have my own record out. I started my own record label called Polygon Records. My record is entitled “To Journey a Dream”. There’s many all-stars on this record. I’ve been working on my own music for the last 20 years and each time I had songs I would go into the studio and record them. On the record, there’s some great musicians…some names you know and some names you may not know. My current band… my trumpet player is Charles Moore, bassist Tony Dumas, young saxophone player named Gerald Pinter, a keyboard player named Greg Kurstin, which is the current band. They are on the record as well as Patrice Rushen, pianist, saxophonist Carter Jefferson, the vocal sound of Minneapolis native, Roberta Davis. Also there was jazz harpist, Dorothy Ashby, pianist Victor Feldman is on this record as is vocalist Bobby McFerrin. I’ve got Steve Hall, another tenor player Wallace Roney. So it’s kind of a collage of the music that I had been writing and recording.
So as I am a snare drum collector, I hope you don’t mind if I ask you a couple question about snares you’ve used. Do you remember the first professional snare that you owned?
That would have been a Gretsch drum. Coming up in the jazz world and having all these guys as famous and mentors, having met them, like Elvin and Tony, they were all playing the Gretsch drums a the time. So my first professional drum set was a Gretsch set. Those Gretsch drums would have been on the Freddie Hubbard records, ‘Keep Your Soul Together’ on CTI and also ‘High Energy’ which was on Columbia. That’s my original Gretsch kit on those recordings. I still have it and record with it. It’s a custom-made 3 piece with a 16”X16” bass drum, and 8”x12”, 14”x14” toms, with a 5-1/2 x 14 chrome (over brass) snare. That snare had die-cast hoops and the wide 42 (strand) snare wires. I was always curious about that. Why some drummers had these wide snares…and I kind of became accustomed to that. Once you get into the sound and it gets into your head and you’re recording with it…that kind of became a basis for all the other snares that I’ve played and that I own.
Back in the day of Tony Williams when he was doing the Tony Williams Lifetime, he was playing Gretsch drums so he made the Gretsch sound applicable to any setting. When I met Charlie Watts, he told me he’s a great lover of jazz drums. I’ve got a picture with him, Billy Higgins, Elvin Jones, and myself. Charlie Watts, in his whole career with Mick Jagger, he had a Gretsch kit and was inspired by Max Roach and Tony Williams and those guys. He’s playing on a jazz kit basically tuned to what he plays with the Stones. I’m saying that because Tony Williams actually pioneered a lot of things as far as jazz-rock or fusion or whatever they’re calling it now.
Could you describe some of the other snares you’ve played and you’ve owned?
I own a set of Tempus drums that is made by a gentleman, Paul Mason in Canada. He custom made a snare drum which was very unique for me, and a whole set actually made out of fiberglass, but it’s not fiberglass the way the old Fibes drums were. The fiberglass that you could see through. He had a process of doing layers of this fiberglass material and he kind of layered them like layers of wood. Mine has a special finish on the outside of mine. It’s like a black-gray swirled. So it was a different way of doing something and I used those drums with Carlos Santana when I played with him, as well as with Frank Sinatra.
What size was the snare drum on that Tempus kit?
It was a 5” x 13” snare. I think it was standard with die-cast hoops. Die-cast does give a little more focused attack. Maybe a warmer attack; it could be brighter. To me, the die-cast can work in any setting.
And you picked that?
Yeah, I chose that. I was trying something different. I thought it was great. The snare drum had a nice sound to it. It was a nice solid sound, more compact than the 5” x 14”. It was a little tighter sound. So I was able to cut through and get some different colors. I kind of tuned it high. I used to love drummers like Stewart Copland from the Police. You’d get a nice kick to it, a nice sound. I still play it. I even had a mic put inside of the drum, the May EA system. I put in the snare drum and also in the bass drum. I had 2 bass drums, a 20” and a 22”.
How would you compare it to your Gretsch COB snare?
It had a brighter sound. Definitely a snap to it where you could definitely hear it. One of the drums I could play with more volume. With Carlos Santana, of course, it would cut through the music, and with Frank Sinatra where we were playing with a full 30-piece orchestra. Yes, it was very good live and I’ve definitely recorded with it. Good drum.
Are there any other snare drums you have or played that come to mind?
Yes, I’ve been recently playing several. Premier put out a high-end maple kit called the Signia. They have a die-cast hoop on the snare drums and I was really impressed by that drum (a maple 5 ½” X 14”). I’m almost exclusively playing that drum now. That kind of became my favorite drum. It really had a nice warm sound, very close to Gretsch, maybe a little more projection. All drum companies try to modernize. They put in a reinforcing ring in there. Some drums have it and some don’t, but it seems to give it an extra bounce. A little extra snap. Then with that, I decided to try the wide 42 strand snares on it. And it’s even closer to the Gretsch sound. So that’s kind of been my influence. And even on the 13” Tempus snare drum, I put some wide snares on it. Gave it even more of a “snarey” sound as well as the brilliantness of it. I have about 3 or 4 different snares, but the sounds are similar, but they’re also varied enough that they can stretch over into rock or R&B or something soft.
Didn’t they also make the Signia drum also with wood hoops?
Yeah, they had some with wood hoops, but not many. They were metal hoops and it was an unusual die-cast hoop on the top. It was a little heavier and, it really was very close to Gretsch drums. So that’s the reason I like it. I think it’s inspired by Gretsch.
Do you think the die-cast hoops make the drums easier to tune?
I think so. As a matter of fact on my Premier Signia kit, they had the die-cast only on the snare drum. Then I put die-cast on all of the tom-toms because again it sounded so close to Gretsch and I wanted to go that way even further. So I had die-cast put on the Premier Signia drums.
Do you bring all your snares when you’re not sure what you’re going to cut?
I usually bring 2 or 3 and I usually ask in advance what kind of music do you want me to play. If they tell me it’s all streety and jazz, then I’ll know what to take, or if it has rock guitars and pop. I’ll take the snares accordingly. Sometimes I may bring a jazz snare to a pop gig just to see if it will cut. I can play all of the drums on any of the sessions, but it it’s a rock session, I may use my 13” Tempus or maybe a little 12” Fever drum (which is wood and Formica). If it’s jazz I’ll use my Signia Premier snare.
So is the idea to be as versatile using the drums that you have or is it just whatever seems to sound good to you at the time?
A little of both. I’m definitely trying to be versatile. If I have a little jazz kit and then a giant Tempus rock and roll kit, 22” bass drum, 3 mounted toms, 3 giant floor toms, so it is the application of the music, but then sometimes, maybe the warmer drum will work in a rock setting.
It’s great that you are open to the different things that are out there.
Definitely. Plus, what the older guys all said to me, like Max and Blakey and Elvin, they say ‘if you’ve got a drum and know how to play it, and you know about the tuning and choosing the right heads and playing it properly, you can make any drum sound good’. So I kind of kept that in my mind.
Do you remember specifically any recent recording cuts, what snares you might have?
Well, in the last 2 Etta James records that I did, she was doing the music of Billy Holiday, some blues type songs. I probably had the Premier Signia snare drum with the die-cast hoop on it. That seems to me my general all around favorite drum that can work in any application. Her last 2 records Etta James on Private Music is the record label - I’m very proud of that. I also used that same snare on a Natalie Cole record. It was called ‘Stardust’ on Electra. Also when I did that music soundtrack with Clint Eastwood, ‘Midnight in the Garden of Good and Evil’, they did a whole jazz sound track so I remember the recording I did. Clint Eastwood loves jazz. KD Lang was on the session so I got to record with her.
Do you have any interest in vintage stuff, like an old Radio King or old Gretsch? Has that ever attracted you?
It has. I’m really good friends with trumpet player Wallace Roney, who is not only a great trumpet player, but he loves drums. He had a couple of drum sets that he got from Tony Williams and Tony got him into Gretsch drums. Wallace has a couple of vintage Round Badge Gretsch drums, so he would talk a lot about those and the vintage sound going back to the old 3-ply as opposed to 6-ply.
Is there anything else you’d like to say, perhaps what you think is the role of the snare drum in a drum kit? Why have more than one snare drum?
I think it’s very important to see that the snare drum is kind of the focal point that the drummer is dealing with. They way you’re sitting, you’re two legs are encompassing the snare drum. Everything is built around that. The way you set your snare, you’ve got your high hat on this side, the bass drum on that side, the cymbals around you. Both of your hands, your legs, everything is centered around the snare drum. So it could be the most important piece of the kit. It’s a good subject to have. We’ve touched on everything else, the drum sets, books on cymbals, so yes, the snare is very important. I highly recommend having a good snare and having a foundation.
I would say as far as snare drums, all the drums seem to be in a general category because everybody is trying to improve on the product. Just like carmakers. Everything is improved and everything is kind of generally great if you think about it. You can customize anything. You and customize a Ludwig snare or Yamaha snare. All of these little independent companies are branching out - they really seem to be into detail and sound, and checking out the hoops and the bearing edges. So I just basically love all types of snare drums. It just depends on the application.
Do you tune your drum to the song or to the drum? What makes the drum sound good?
I tune it to the drum. I have a general sound, some general pitches. I even have some general notes. I will tune my snare to a G. G has been a general tuning note for me. I build everything around that G. It seems to have worked. They’re all in these different musics and styles that I’ve had the pleasure of playing with. So some tune in keys. Tony Williams tuned his drums in pitches and I deal with pitches too.
I would encourage everyone to check out jazz drummers because in jazz music there seems to be a great flexibility and a lot of rhythms that you can play as opposed to if you’re playing a pop song. You’re kind of limited. So jazz drummers really open my head up to the world of rhythm. I encourage people to check out jazz drummers and their snare drums and what they’re doing. With all the work that I’ve done, playing with a lot of people, I’m personally trying to concentrate on my own group, my own sound, my own recording. My group is called the Penland Polygon. Polygon means a many sided figure or having various angles and in my music I’m trying to play jazz and R&B and fusion and incorporate all of that out of the jazz tradition. So I’m going to be concentrating on doing that, my record, my music as well as free-lancing and playing with as many people as I can.”
Thank you for taking the time to share your insights and experiences. I look forward to hearing more from the ‘Penland Polygon”!
My pleasure.
Ralph will be remembered as the talented man who loved being behind the drums - a man with a huge smile, warm heart, and a gentle touch; forever being one with the music, never over-shadowing. Rest in peace and know that your legacy lives on.