It all started at George’s Drum Shop, my retail store in Jackson Mississippi from 1985 - 1987. Joe Partridge was my right hand man there, doing minor repair and refurbishing jobs like taking the old wrap off of drums and re-wrapping them (actually burning the wrap off of the old volatile pre-OSHA drums - the more sadistic customers wanted to be called when we did that so they could come watch!) We didn’t actually build any drums at that store, just sold typical name brand drums and repaired then. Joe and I would start building drums separately in the years after that first shop closed. But, I had some foil stickers made that looked like drum badges with the name of the store and a cool looking drum. We would put those sticker badges on drums that we sold, kind of like car dealership stickers (good idea? bad idea?). Anyway, those stickers would become the badges that I would put on the drums that I started building a little later. I still have some of them. So that was as far as I got with the drum building in those first years - badges!
A shell that Joe Partridge cut, wrapped and drilled at George’s Drum Shop for Jeff Barnett. The used hardware was from Jeff’s Pearl snare.
A Pearl set that Joe Partridge re-wrapped and modified with beefier hardware. The set belongs to Jeff Barnes who was a regular customer at George’s Drum Shop in Jackson MS. The set is still in use today.
1987 - 1993
My first foray into “assembling” drums to sell was shortly after the first George’s Drum Shop closed. In the late eighties and early nineties I had a separate workshop building behind my house in Jackson where I taught lessons and repaired, built and sold drums to my students. I would buy the parts and Keller shells already drilled and wrapped from a distributor, Universal Percussion. One of those kits was installed at Malaco Records Recording Studio in Jackson.
2002
I didn’t get serious about drum building and repairing until the early 2000s when I opened the second George’s Drum Shop in Akron, Ohio. I was in my mid-forties then. I was doing typical light woodwork on plywood shells I bought from Keller: drilling holes to mount hardware, cutting the bearing edges on the ends of the drums, cutting snare beds, etc. I bought the metal parts from WorldMax, Precision Drum and Universal Percussion. Most of these drums were wrapped with Delmar vinyl wrap finishes from Precision Drum. I had a basic wood shop with a tall drill press, a router mounted in a table, a table saw, a layout mat on a lazy Susan and various hand tools and sanding devices.
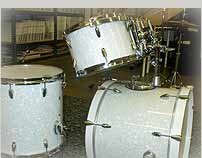
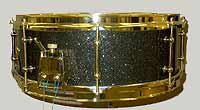
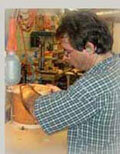
Not great pictures but this was the first kit and first snare drum I built in 2002 shortly after I opened George’s Drum Shop #2 in Akron.
Some of the first drum sets I built in the early 2000s at George’s Drum Shop #2 after we moved to a building in Cuyahoga Falls. Notice the sticker badges and the inlays on the inside of the hoops.
I did a lot of re-wrapping of customer’s drums too. This is when I went looking for a machine for wrapping drums. I knew that it made the process much faster and more efficient. I had seen several at drum shops I worked at in the past, but couldn’t find any for sale, new or used. I knew that Don Corder of Corder Drums had made some in the past but he was not interested at all in building them anymore. So I found a man in Joplin Missouri who built me one. He was a drummer, a machinist and a newspaper press worker. I still use that first machine to this day. He made around twelve to fifteen of these machines that I sold to drum shops, repairmen and drum manufacturers. Even Keller Wood products bought one!
above: The original DrumWrapper machine #1.
Lawrence Drums
I started having drums painted in the mid 2000s and had plans to start a full blown drum manufacturing company called “Lawrence Drums”. I was having the shells painted by Tony Hillhouse in Lincoln Nebraska. Tony had been doing custom paint jobs for Sonor drums for their endorsing artists. I came up with the idea of very thick paint with way more small sparkles than had been used in drum finishes before and had names for them like “Baby Blue Too Much Sparkle” and “Fool’s Gold Too Much Sparkle”, etc. Tony painted three sets of shells for me for the catalog I was developing. He also painted a Harley Davidson design on a floor tom shell that I planned on marketing to Harley dealers and online sales. I had some very nice pro photos made of the shells and built out those three sets. Then, a major kink in the works happened. Tony’s building was a victim of eminent domain by the city of Lincoln. He decided not to re-locate and got out of the painting business. I had no other painters I trusted so I dropped the whole project and continued to make wrapped drums for the drum shop customers.
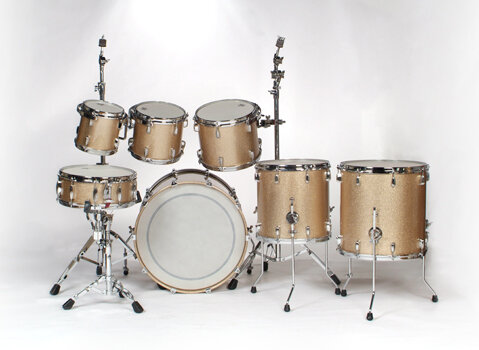
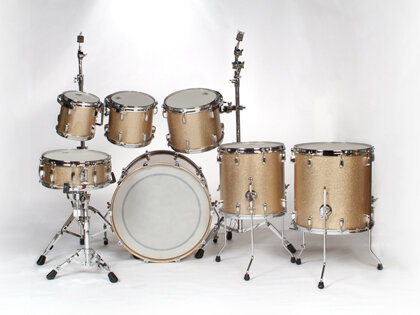
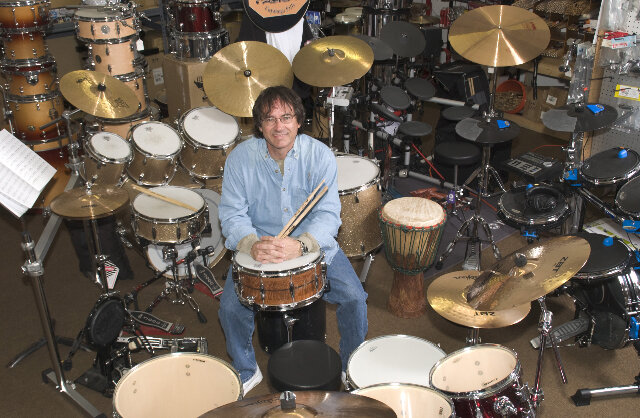
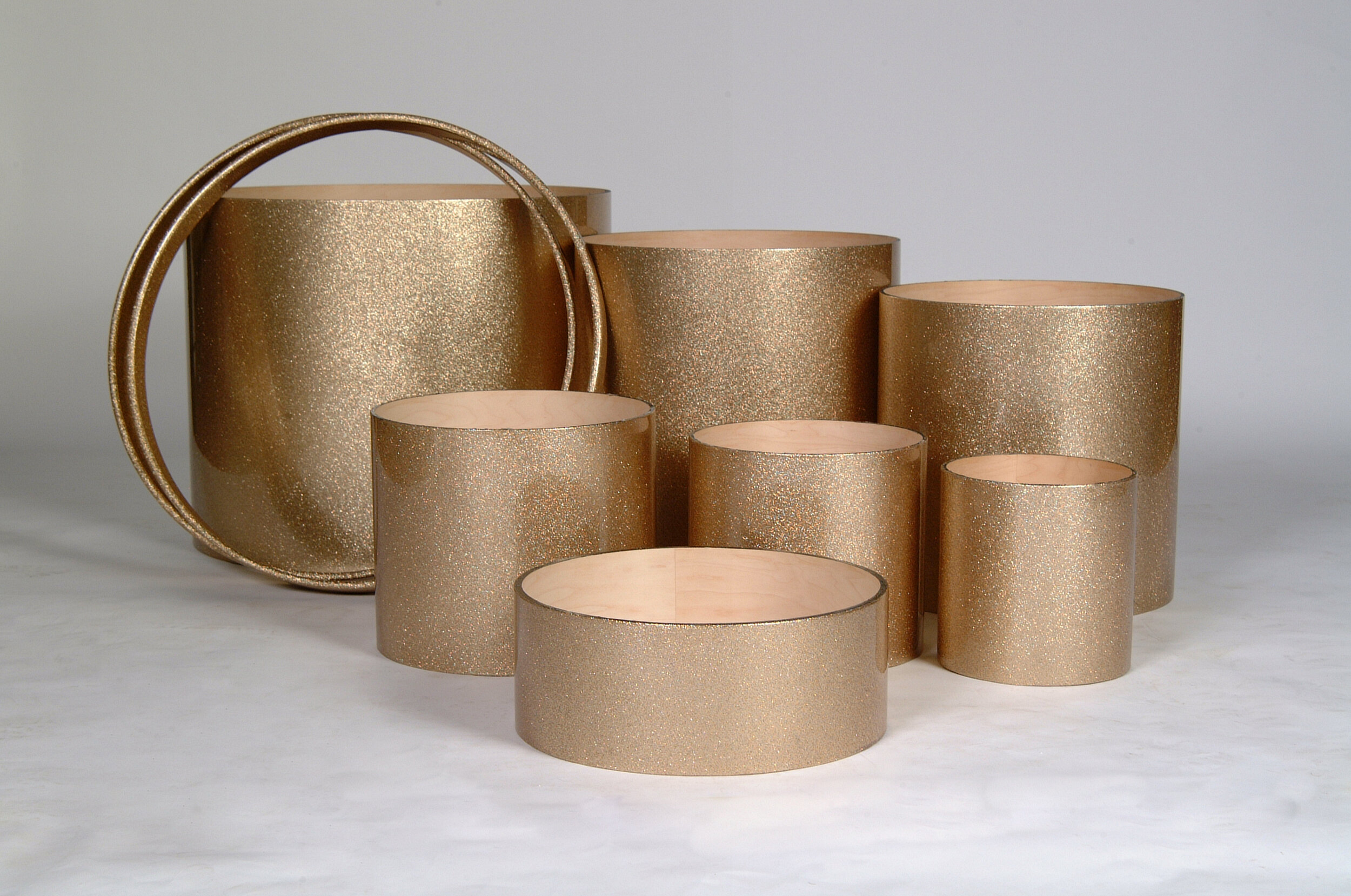
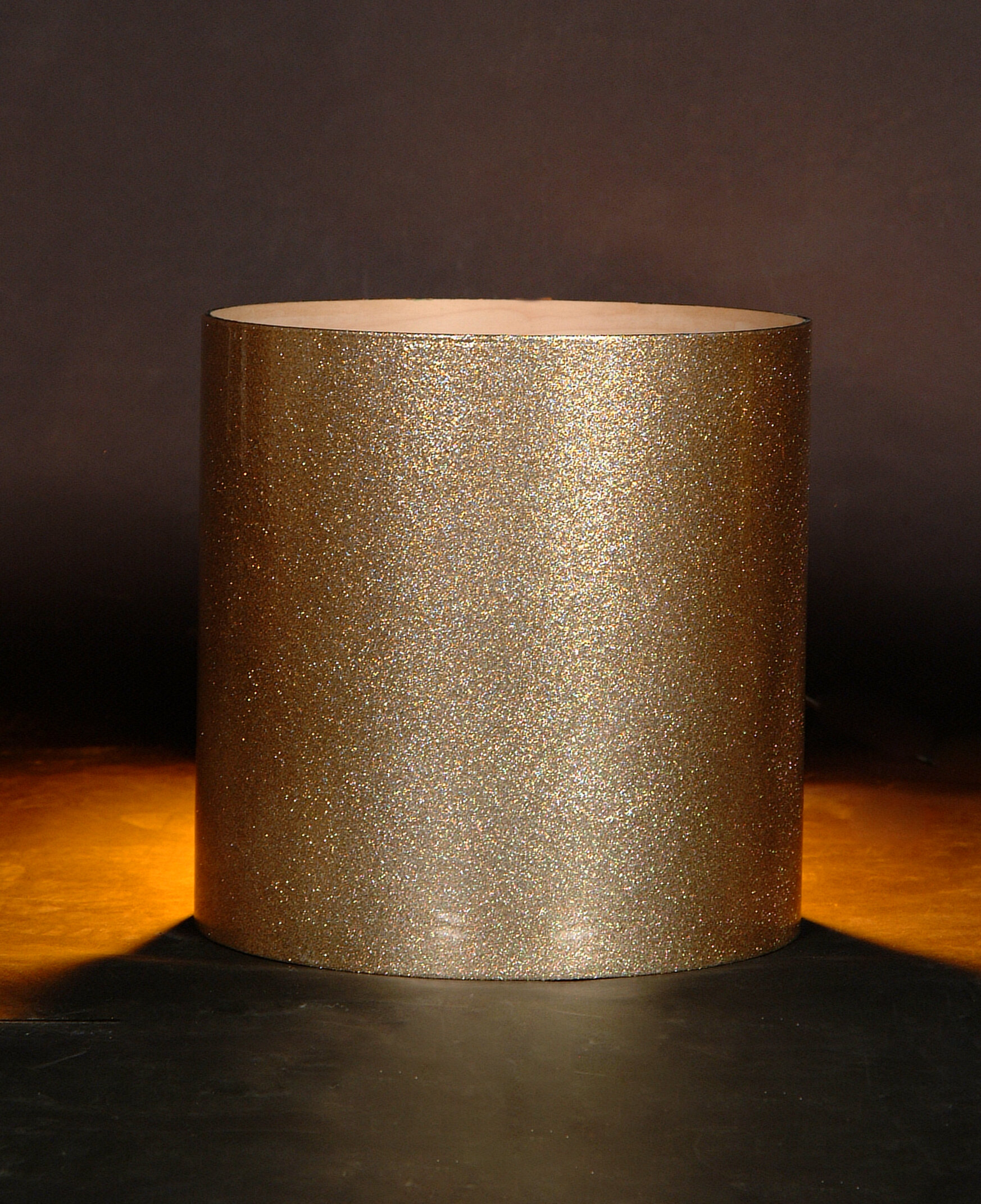
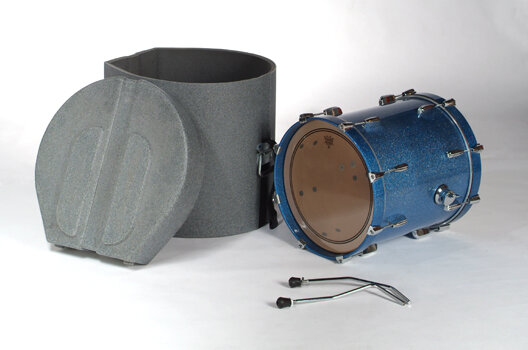
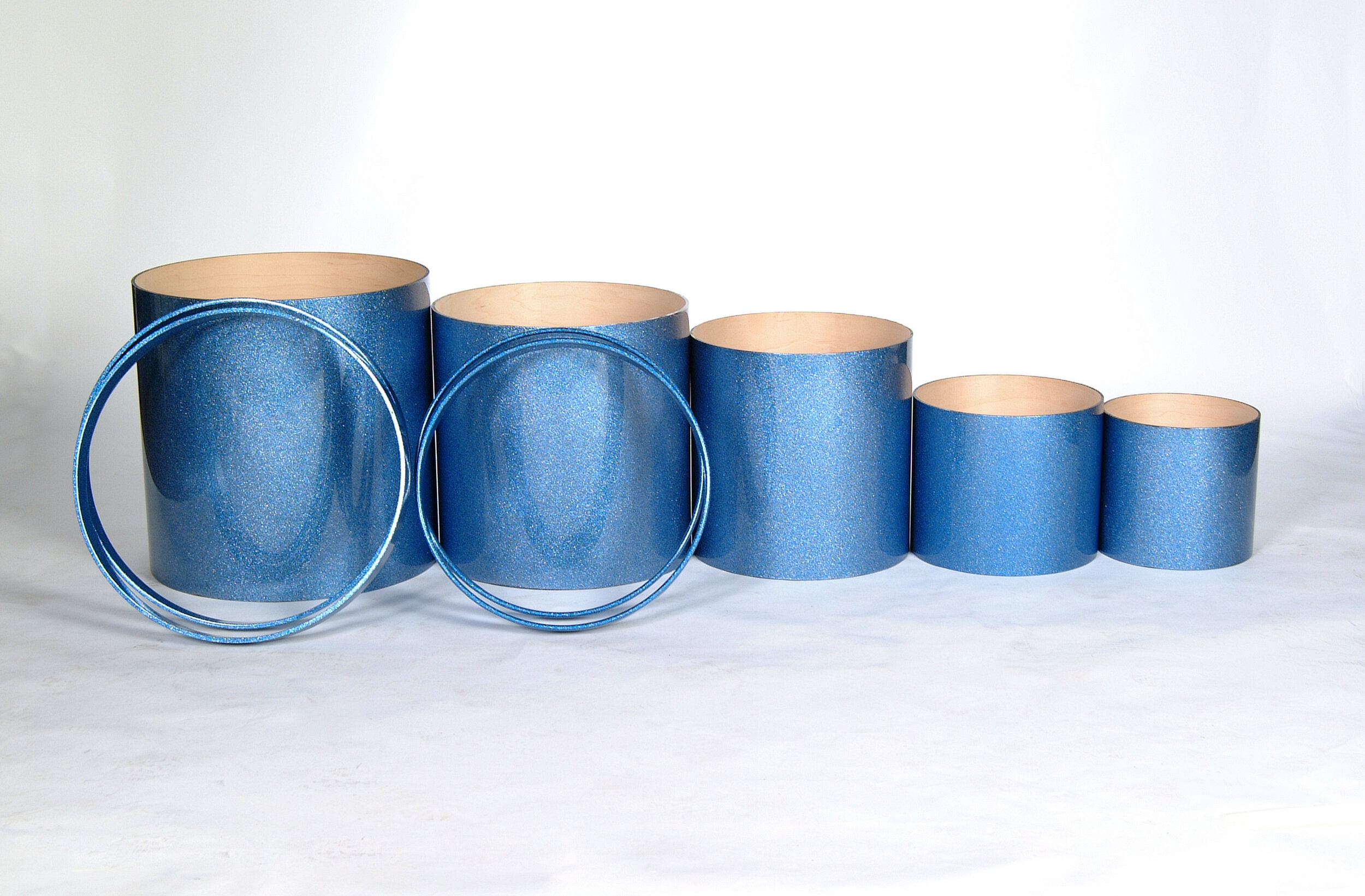
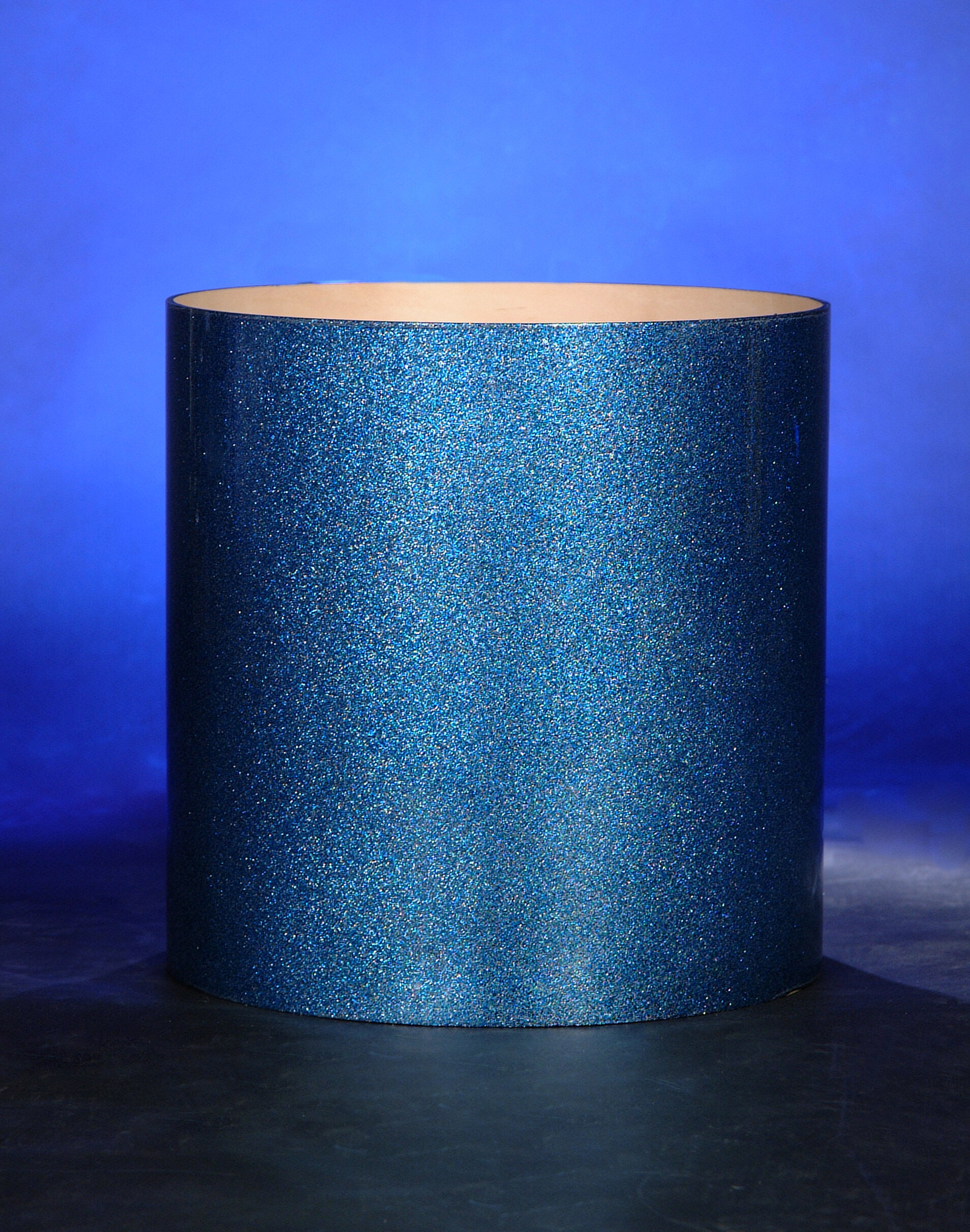

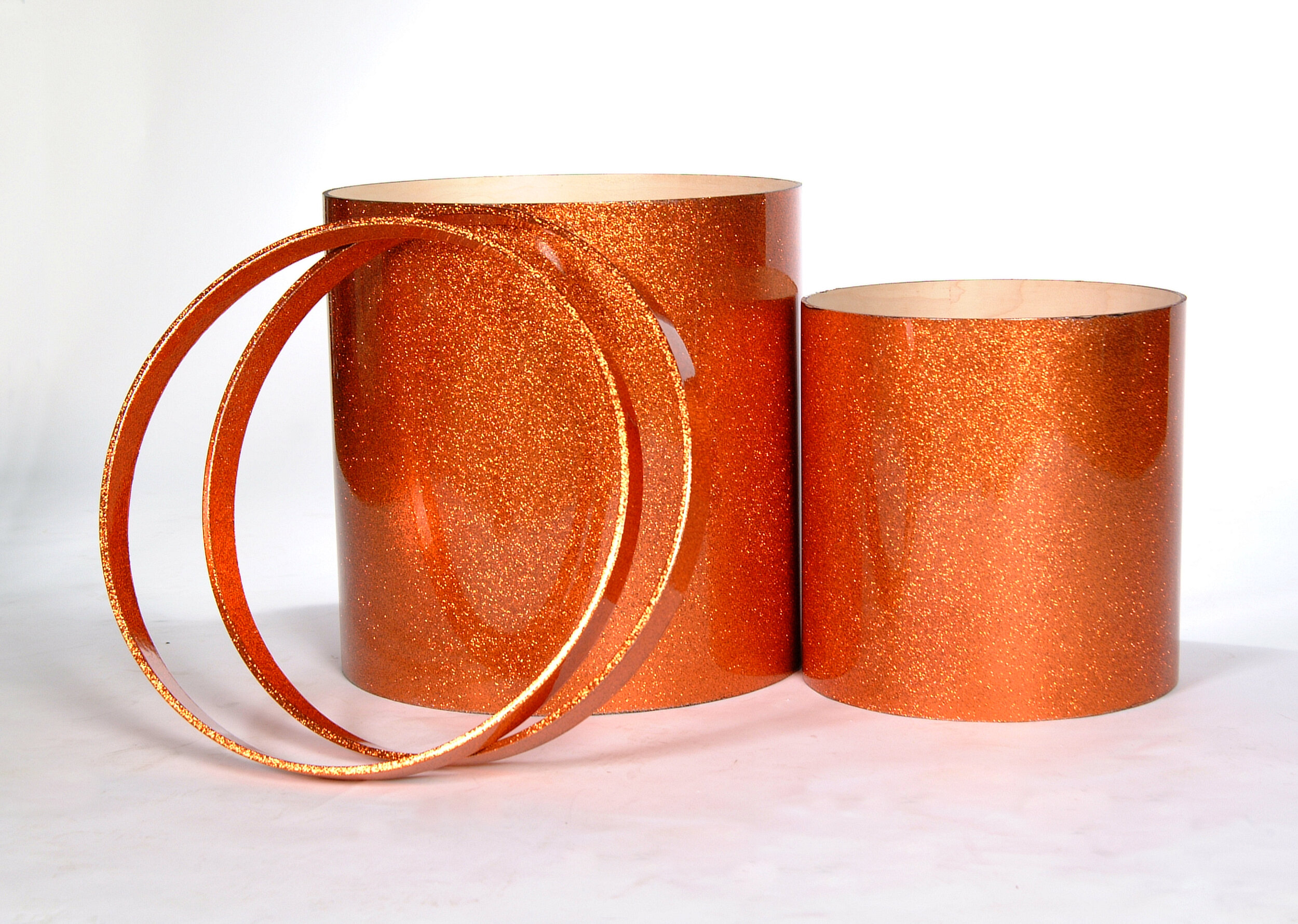
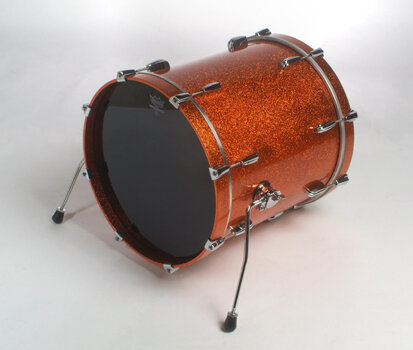
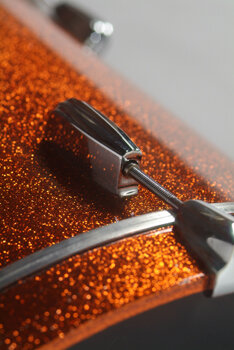
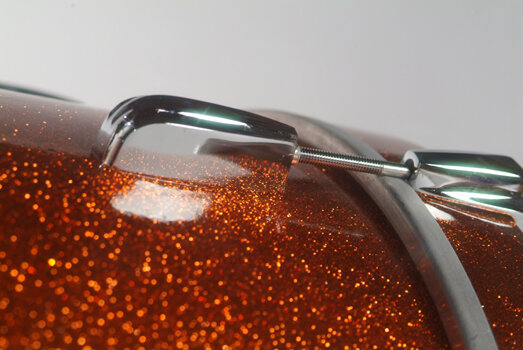
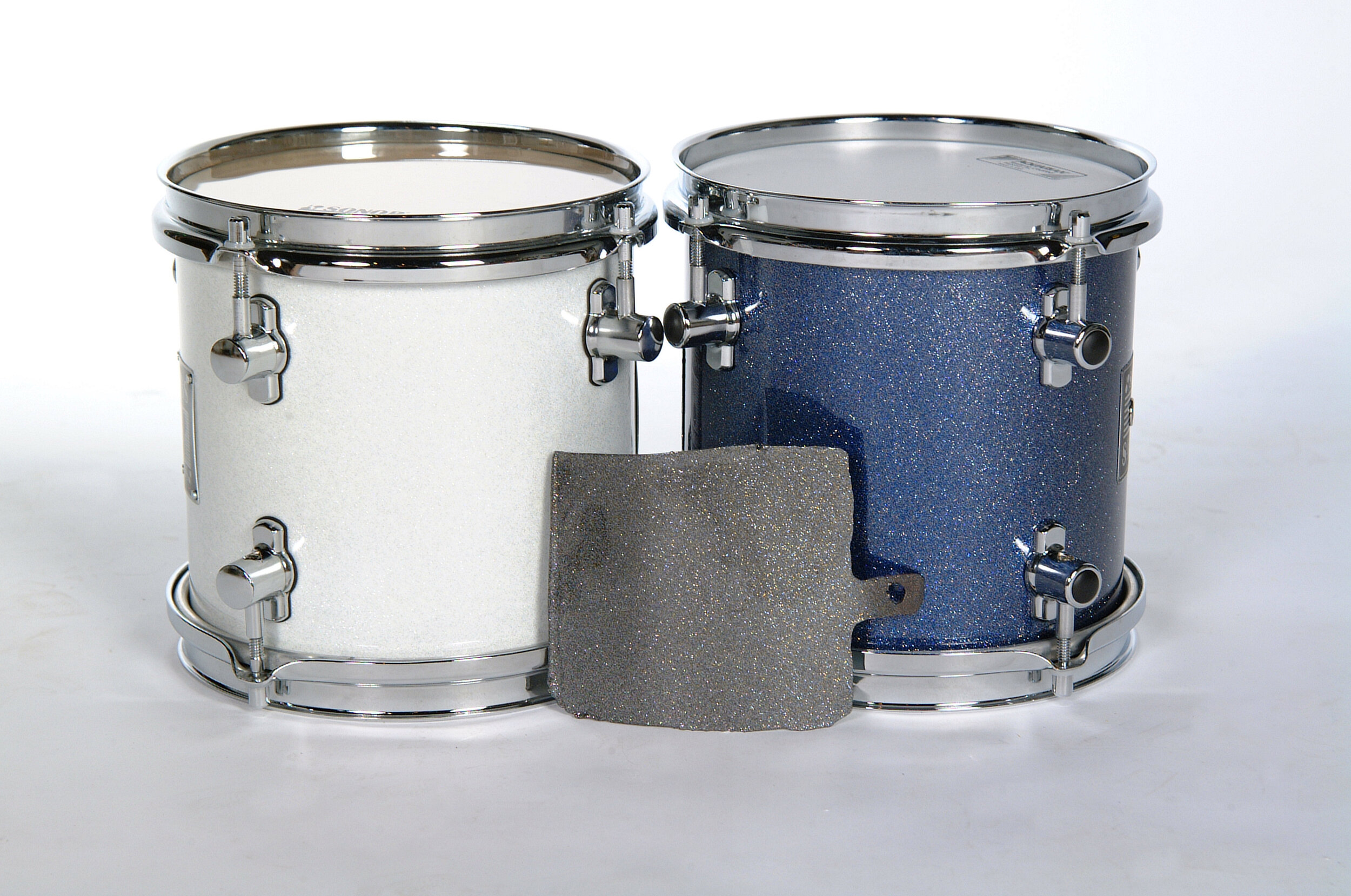
Lawrence Drums above, painted by Tony Hillhouse. I just recently acquired the “too much baby blue sparkle” set from customer/student Keith McFerrin who bought it from my shop shortly after it was built.
Mojoe Drums
Meanwhile, back at the ranch, Joe Partridge had been busy since 1993 making his own line of Mojoe drums in Jackson MS. Here are a few pics of Joe’s work (if you have pics of your Mojoe drums, please email them to me and I’ll post them in this article).
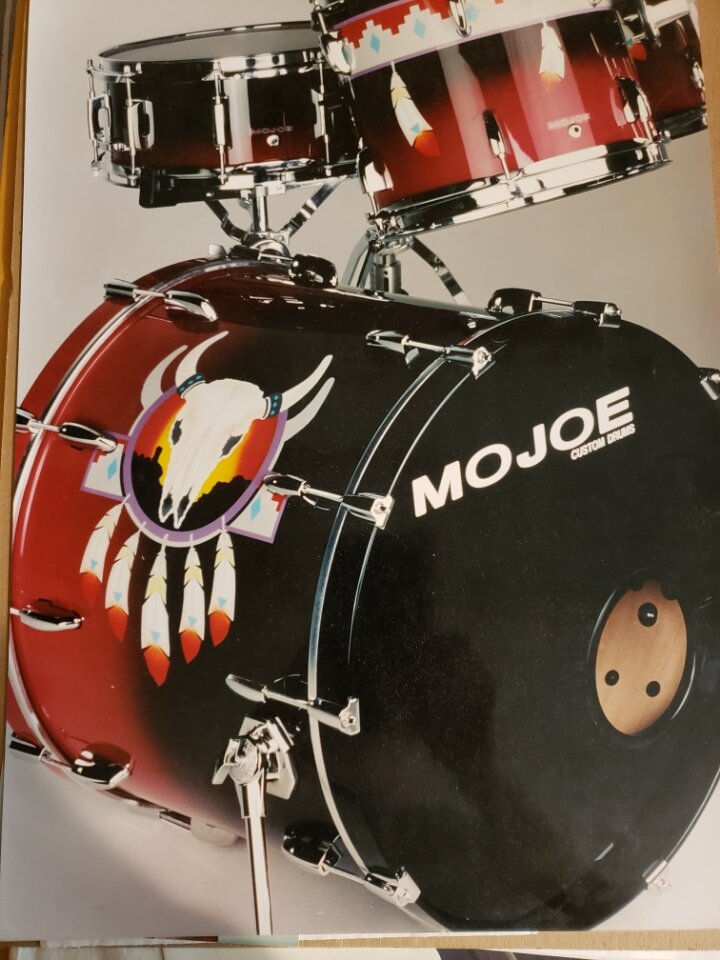
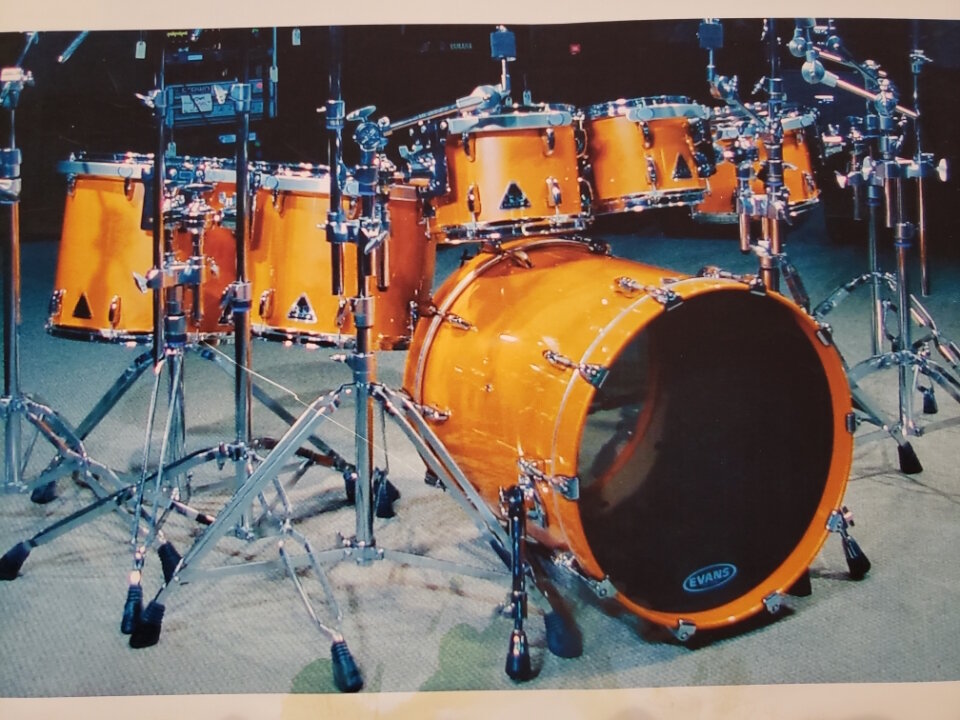
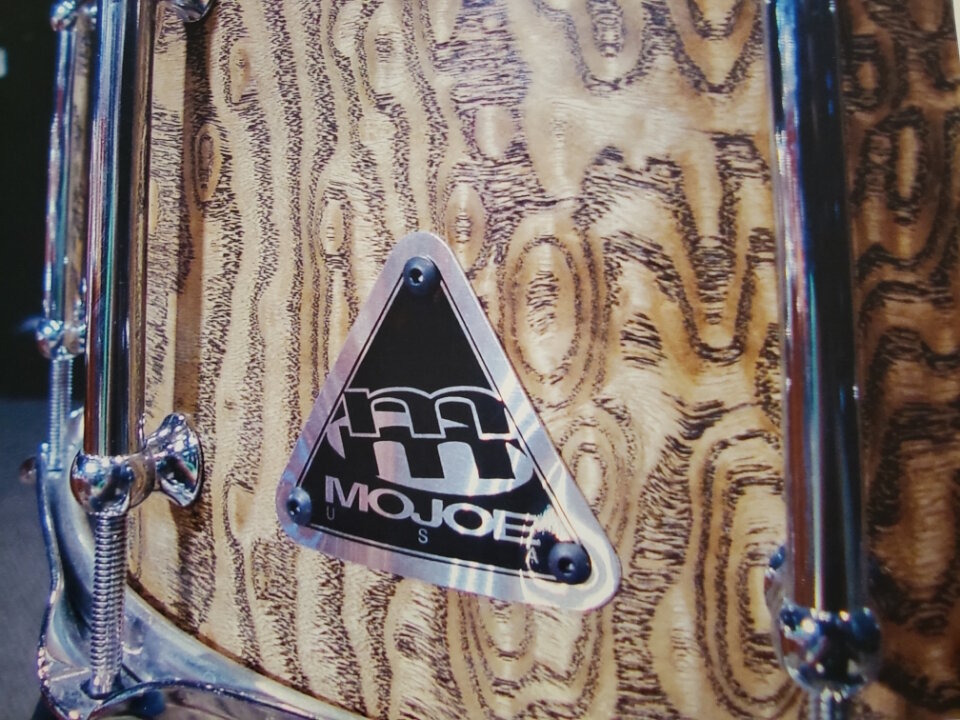
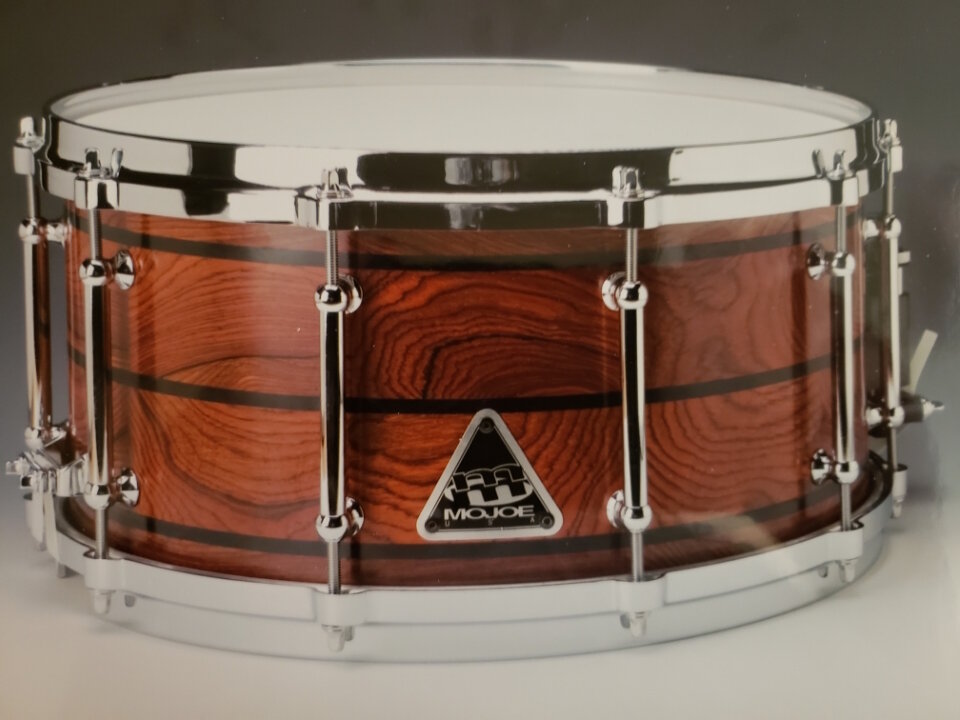
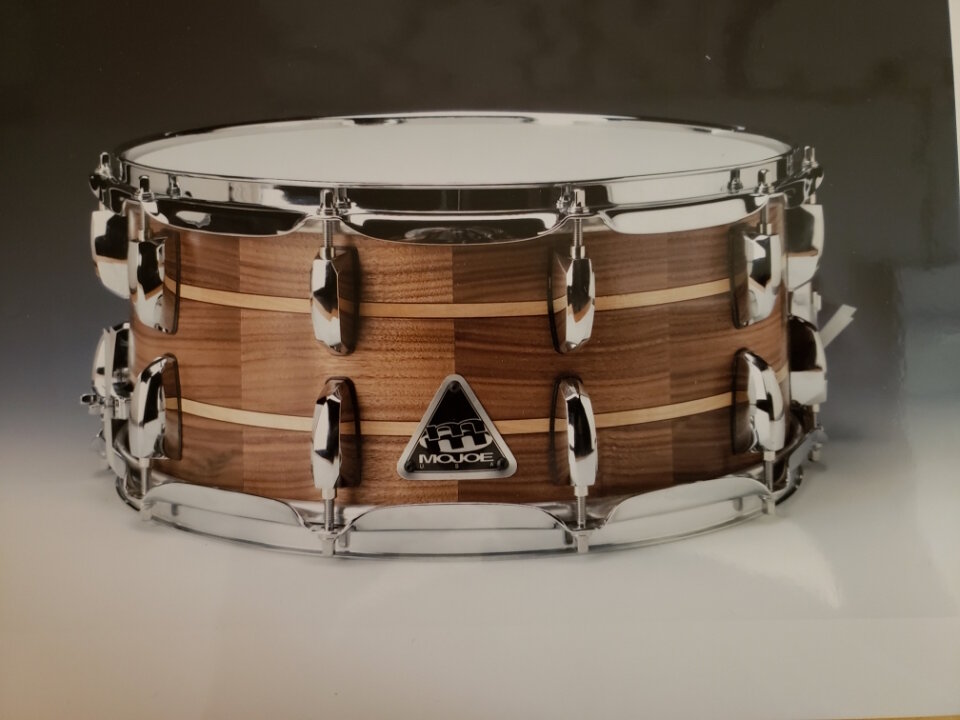
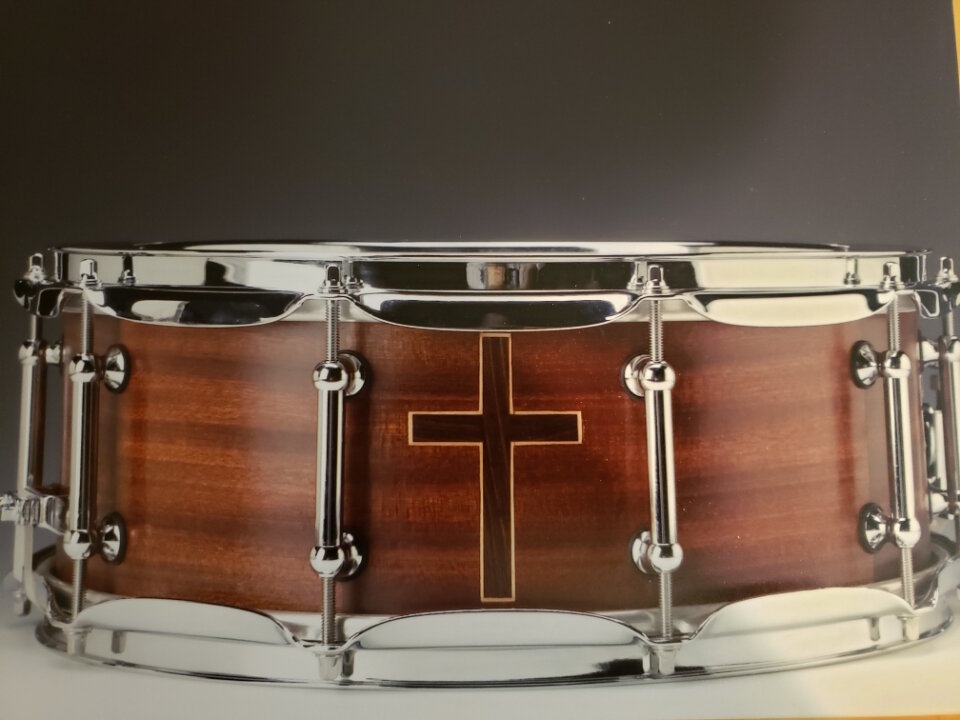
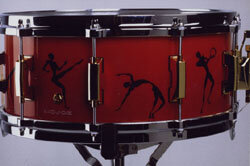
The Famous Drum Company
Joe Partridge and I joined forces again in 2005. We hadn’t talked in a long time, but he called me because he had seen a picture of me and my staff posing for an article about my Cuyahoga Falls drum shop in the Drum Business Magazine that was published by Modern Drummer. He sent me a paper form, the George’s Drum Shop Directory, that Keith Carlock had filled out when he was 15. Joe had been building custom Mojoe Drums at Morrison Brothers Music in Jackson Mississippi for a while. Joe is one of my favorite people. Joe was always a much better wood worker than I was and had done some extremely professional and artistic work with his instruments. He is now a renowned Mississippi wood artist building exotic furniture and commissioned wood sculptures. We gabbed about drum building on that long call and he mentioned that he had made a block shell out of two by fours as an experiment. I asked him what it sounded like and he said. “I don’t know, man, I don’t play them, I just build them”. My curiosity was piqued, so I asked him to put hardware on it and send it to me. Lo and behold, it was a great sounding drum. Very unique. Very loud. It sounded very similar to John Bonham’s snare drum sound, even though it was a wood drum unlike Bonham’s metal Ludwig Supraphonic snares. Uncanny. We decided to market the 2x4 drums for the simple fact that it was different from anything else on the market, which is a big factor in selling drums: “new” and “different”. Joe made a healthy number of them, we distributed them ourselves and through several known drum accessory distributors. We bought ads in Modern Drummer Magazine and even got a “cease and desist” email from DW for using the words “timber matched” in our ad. That was the start of the Famous Drum Company era. The name Famous Drum Company was Joe’s idea and I loved it: “You must have heard of us…we’re famous!”. Shad Gross was our graphic artist who composed the logo badge based on Joe’s basic sketches. Check out the MD ad below and the Famous Catalog page for the 2x4.

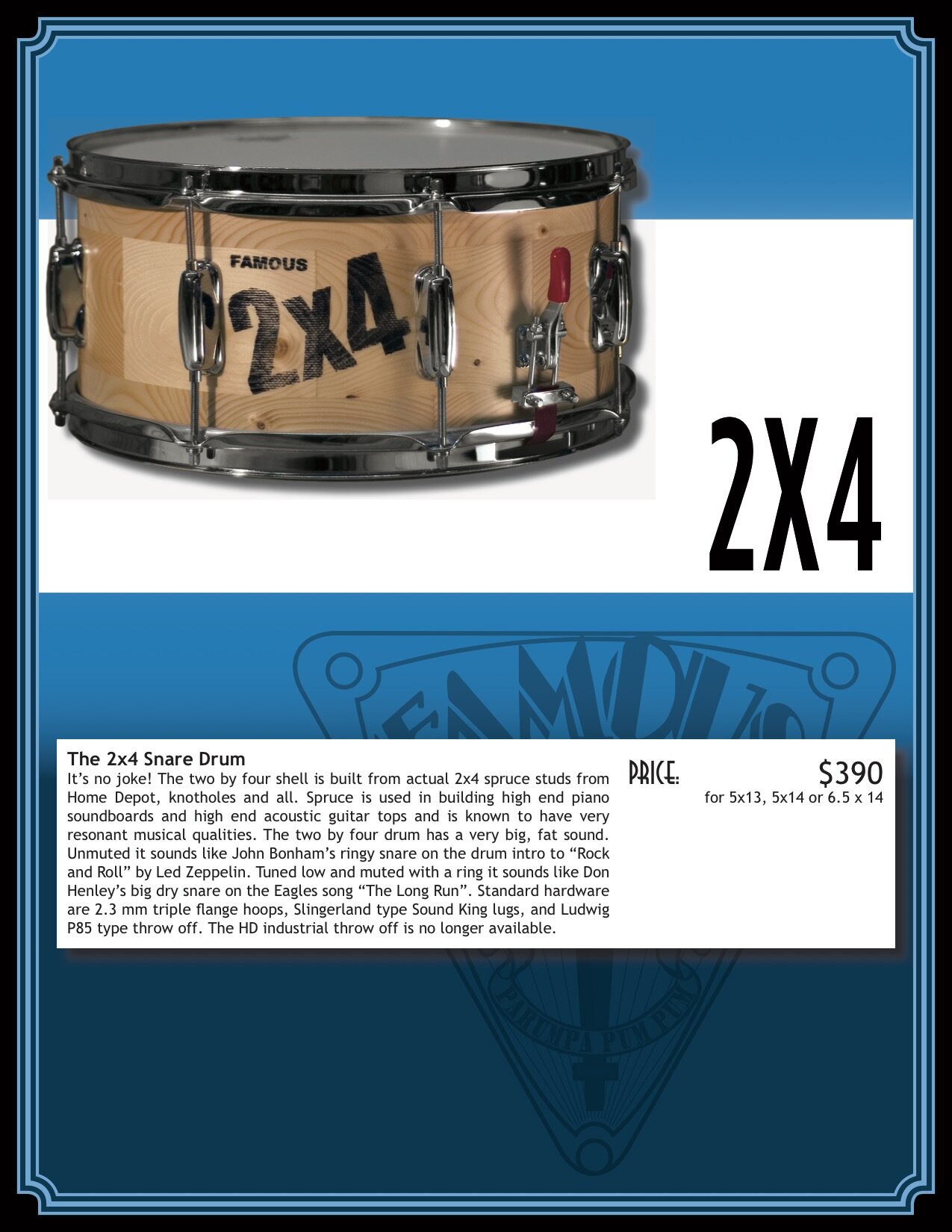
The video below was made by fellow Jacksonian and George’s Drum Shop customer, Bill Ray, who is a world class player and teacher now based in Seattle. Bill was Ike Turner’s drummer for many years.
“Joe Partridge built this drum. I've known Joe since about 1985, when I was a kid going into George's Drum Shop in Jackson, MS. So many great players and drums.” - Bill Ray
Joe and I had several other drum innovation ideas that we collaborated on. One I proposed to him was based on the old Slingerland Tone Flange from the 1920s which resembled a hubcap shaped metal ring that sat on top of the shell, underneath the head . The head rested on the bearing edge of the tone flange and the thing muted the ringing in the head from underneath. A modern plastic ring on top of the head has a similar effect. I proposed that we recreate the tone flange but as part of the wooden shell; a wooden ring built into the shell just underneath the head. Joe said, “That’s cool, but I’ve got an idea for a design that is sexier!” This is how we came up with the Turbine drum, which is pretty zowie. It worked well. We sold a few of them. Modern Drummer gave it a good review along with several other of our drums. We took drums to NAMM. We worked with a plastics company about making a universal tone ring that would fit on the inside of any drum, but didn’t get very far with that. Below see the different types of drums we made and some of the prototype drawings. I have an idea for incorporating the tone flange into the single ply shells that Evan Thomas is now building for Famous Drums.
See the MD review, and online catalog images below. The black and white paper flyer was the result of my wanting to incorporate all of the products into one drum company catalog. The specialized Famous snare drums, the Lawrence plywood wrapped and painted drums, the DrumWrapper machine AND, yes, single ply steam bent shells which were being made close by in Ohio by a local builder, Ian Witt.
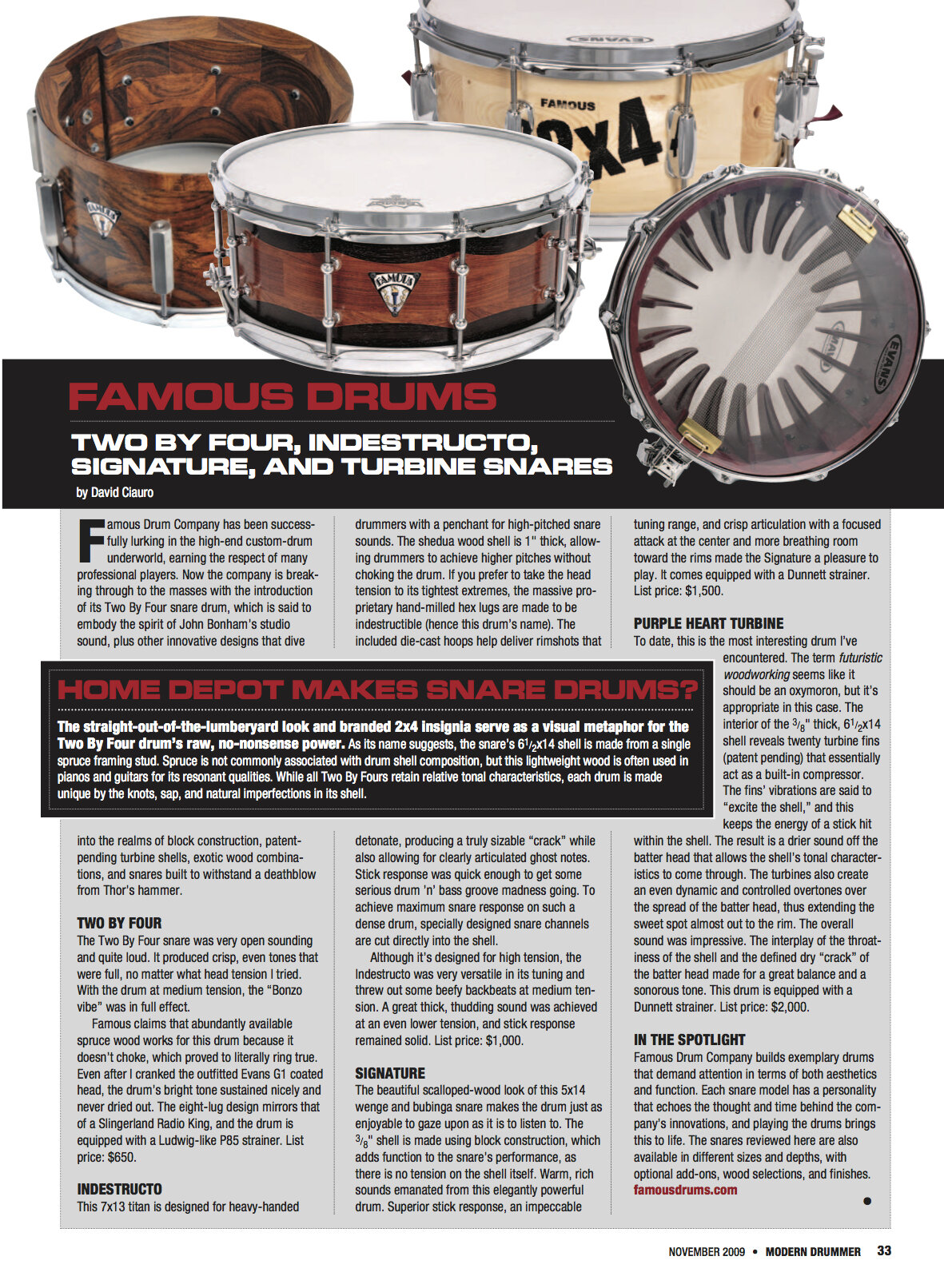
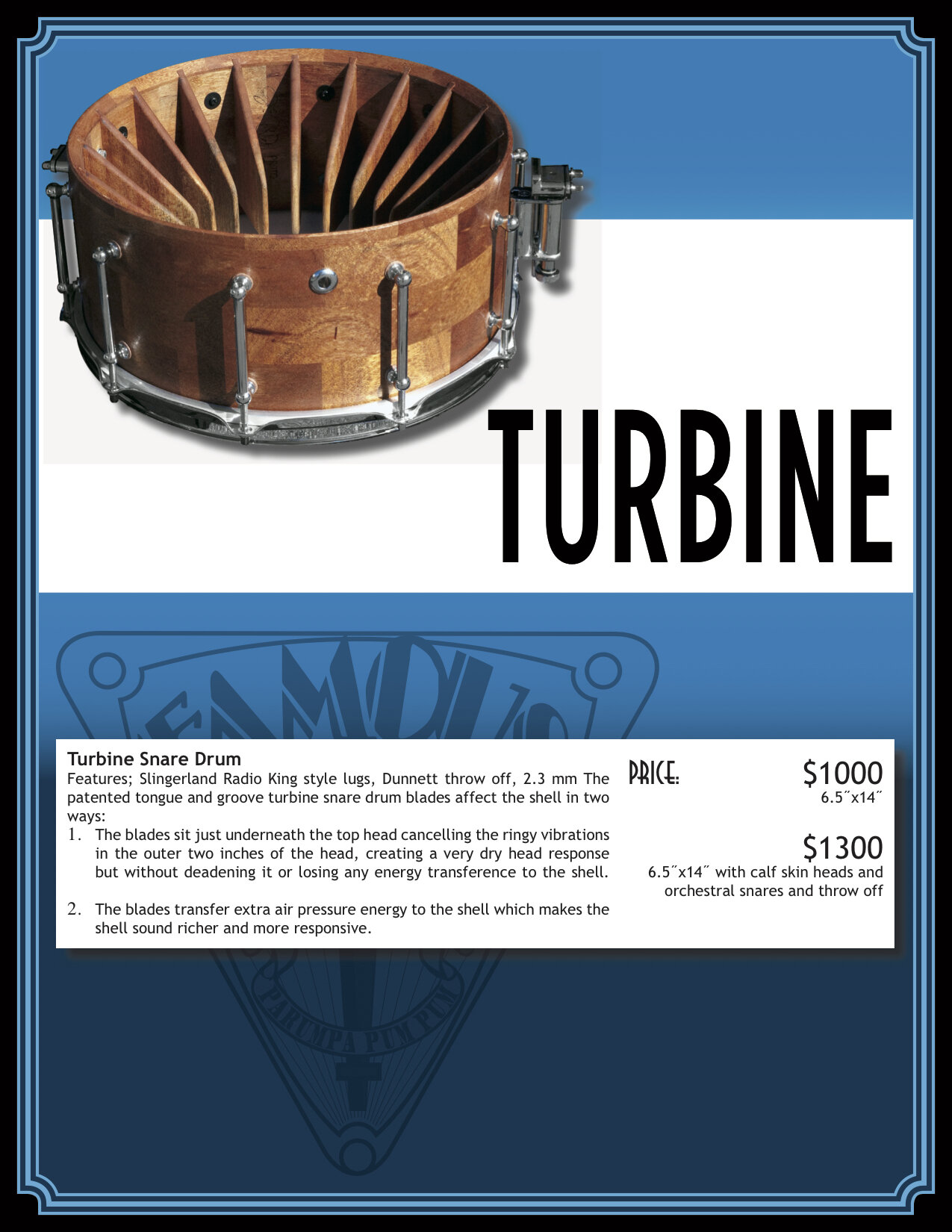
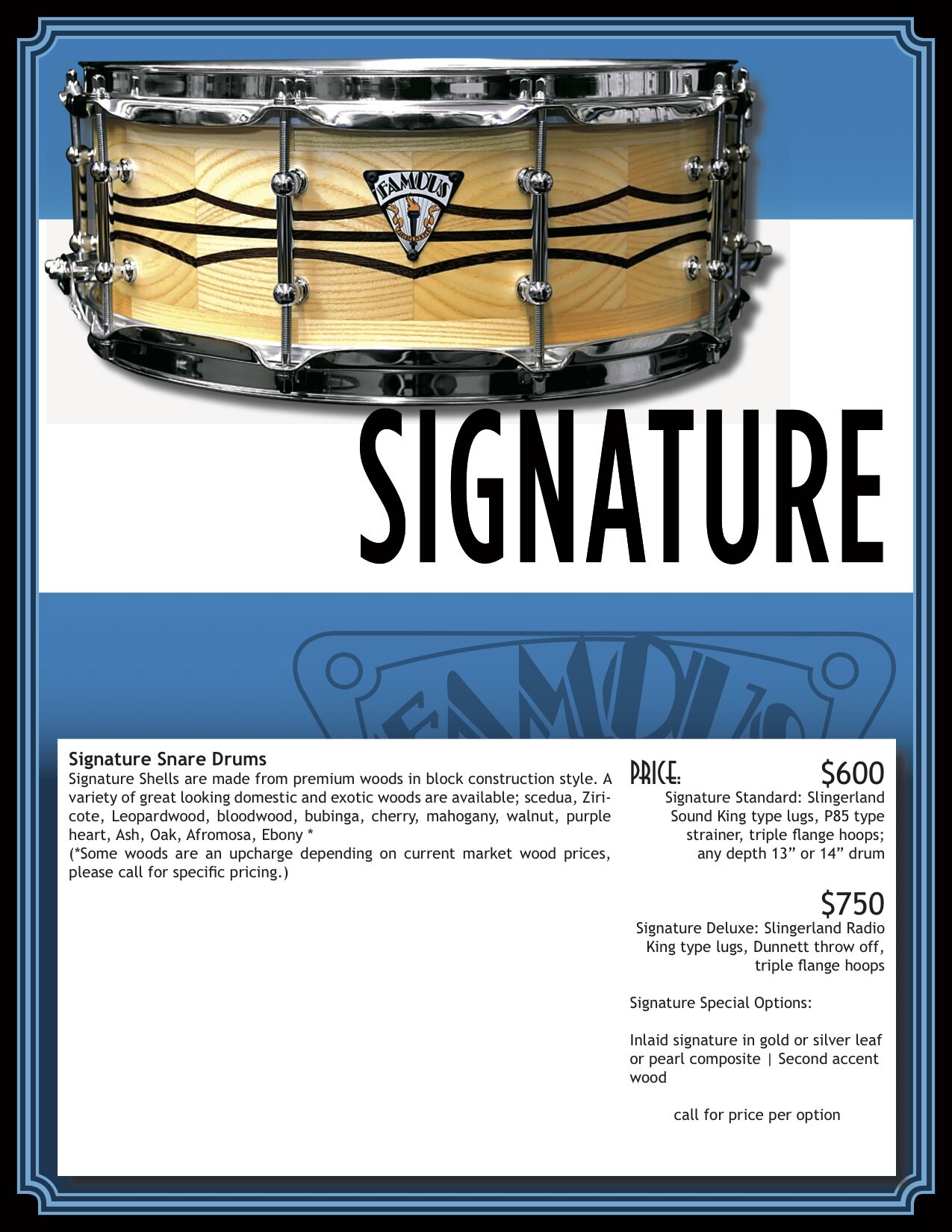
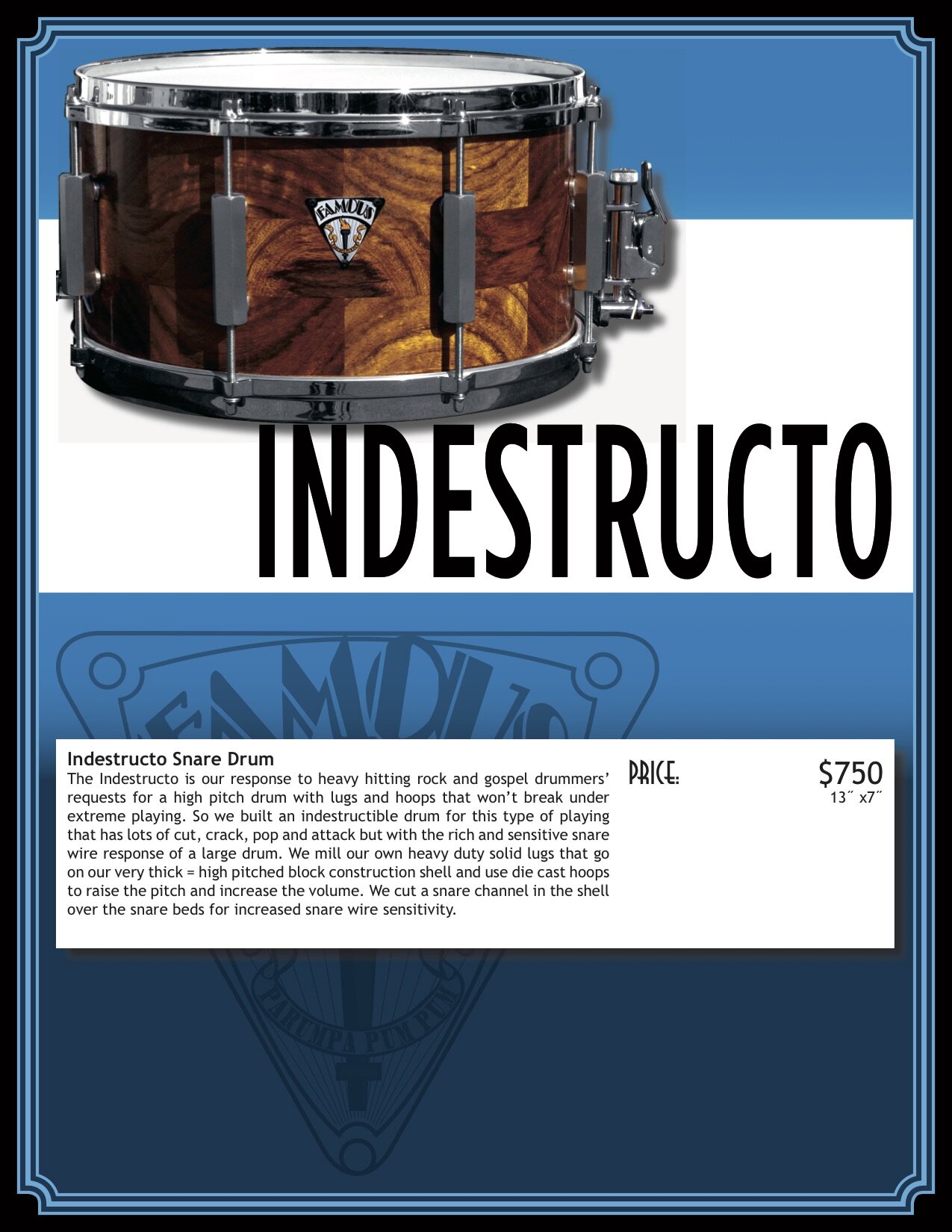
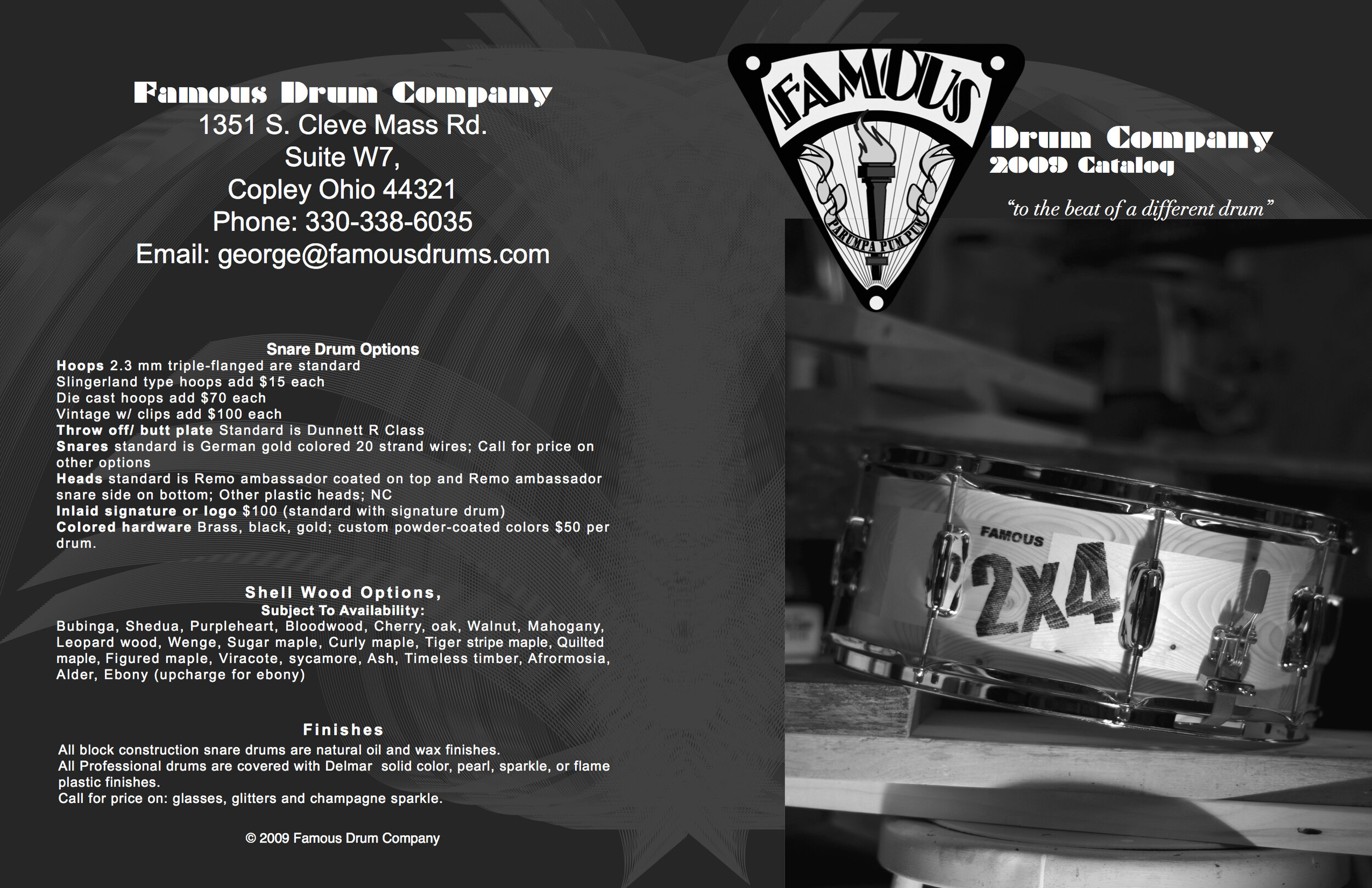
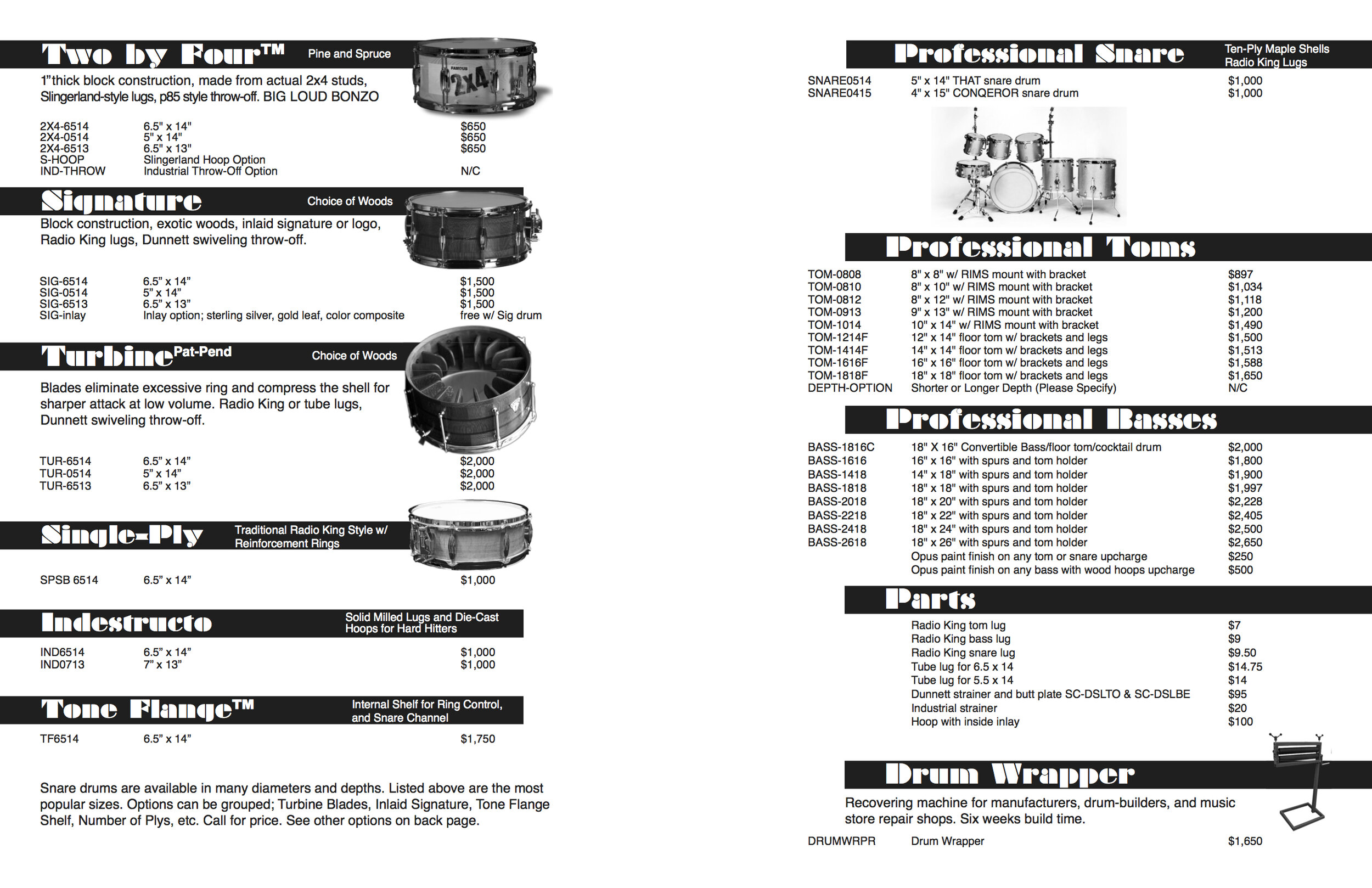
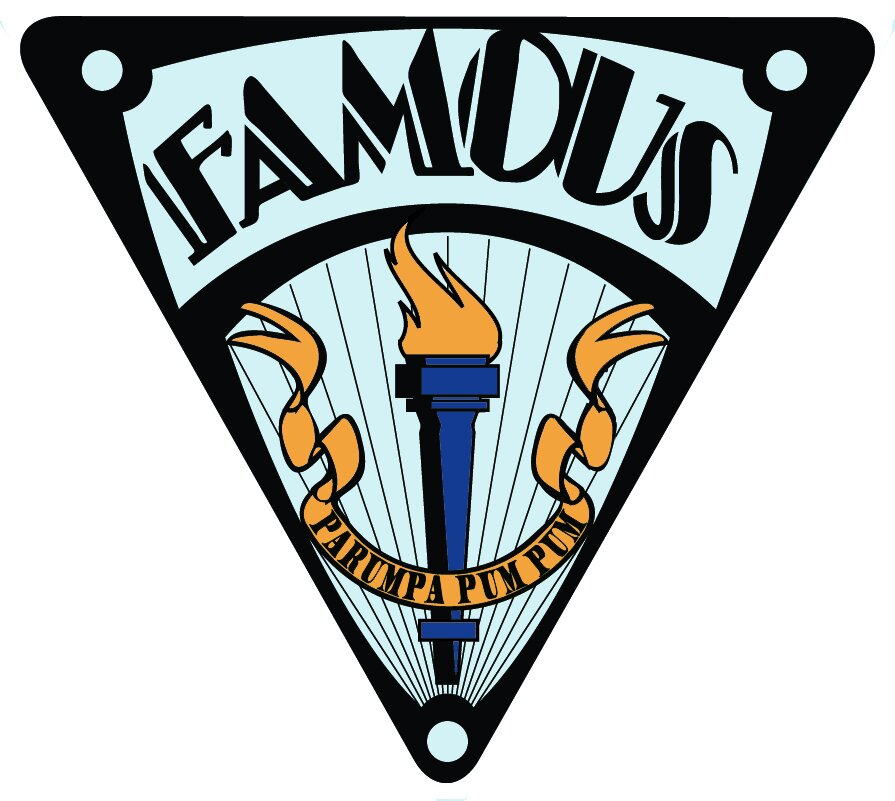
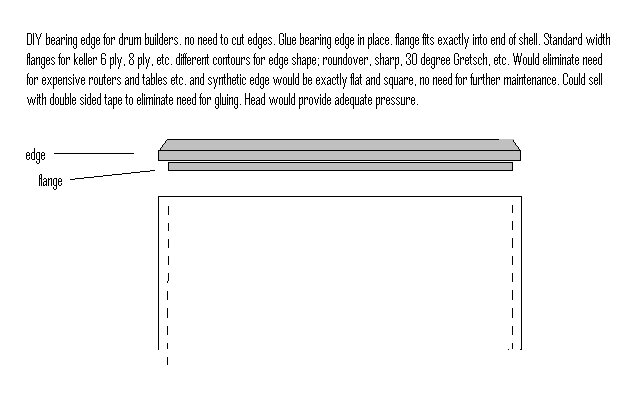
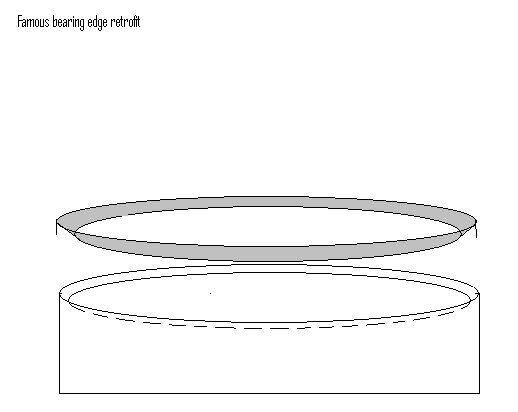
Above; the first prototype Turbine Snare Drum. Owner Jeffrey Bergen modified it with wood hoops, tube lugs and Rhythm Tech snares.
2011 - Drummus Interruptus
So what happened at this point? The Great Recession of 2007 - 2009 happened! The drum shop hung in through 2010 but I wasn’t selling any Famous Drums or much else. No one had any money - especially drummers. I closed the shop down once I was $100,000 down, went through a divorce at the same time, sold off the inventory, paid off the shop debt to the drum suppliers, and moved what was left of Famous Drum Company and George’s Drum Shop back to Nashville, in a 26’ UHaul truck, in February of 2011, in the snow. Needless to say, the winter of 2010 - 2011 was a low point in my life. But success is built upon failures.
I tinkered with drum building and repairs in Nashville from 2011 through 2017 but I became excited again about drum building in 2018 when I learned that my new son-in-law Evan Thomas knew how to build steam bent single ply shells. Evan had been a customer in my Akron Ohio drum shop in the late 2000s and, unbeknownst to me, had worked at age 18 for Ian Witt of Witt Percussion, my supplier for steam bent shells in the mid 2000s. Ian knew how to make a great single ply shell and Evan learned everything about the process. I owned a drum that Ian had made for me and it was one of the best sounding single ply drums I’ve ever heard. I regret selling it.
Evan and I decided to join forces under the revived Famous banner and produce single ply steam bent shells for snares, toms and basses to sell to drum builders. He builds the shells and I design and sell the raw shells and completed drums. I also do some of the drilling and assembling, and wrapping. Evan set up his workshop in a suburb of Phoenix Arizona where the dry air, heat and relatively low rainfall means we can cure/dry the wood to the proper low moisture content very quickly. We also have an excellent source of high grade common and exotic wood boards from a big commercial distributor in Phoenix. Evan’s work shop is mostly outside - protected, but outside. He’s an outside kind of guy! Here he is installing the reinforcing rings into a shell and making a finished drum.
from the Famous website literature:
“Famous Drum Company single ply steam bent shells are built the old fashioned way, by hand, in the tradition of the venerable Slingerland Radio Kings and other historic major drum companies. We don’t have a bunch of fancy computerized machinery, so these are not mass produced. We don’t claim that single ply steam bent shells are better than other types of shells, per se, but it has been proven over time that they have a unique throaty tone that is full and resonant, and an extremely wide tuning range. These characteristics cannot be achieved with typical plywood shells. If you have ever played a Slingerland Radio King, Leedy, Craviotto, Noble & Cooley, Solid, DW or other brand single ply drum then you understand what that sound is and why it has been so sought after for decades. The hand made process is very labor intensive, which is why the shells typically cost twice as much as plywood shells from mass manufacturers. Watch the videos of the process below.
We sell raw shells to consumers, drum builders, and drum manufacturers. All shells are 100% dry, with no moisture content, thanks to Arizona’s hot and dry environment. Raw shells are sanded to a fine degree inside and out. Raw shells are not badged, but we do usually wood-burn the build date and the builder’s initials into the interior of the drum in small letters and numbers in an inconspicuous place for warranty and inventory tracking purposes. We also will do any woodwork that is required, including bearing edges, snare beds, drilling holes for hardware, vents, etc., for a very reasonable extra charge. We can also finish shells in stain and clear finishes, as well as wraps. We can provide shells without the re-inforcing rings to builders who want to do that themselves. Shells can be ordered in any size from 8” to 26” in most depths using a large variety of common and exotic wood types.
We also sell completed custom drums to consumers that are labelled with the badge you see above. The first video on this page is of the first Famous Drum Company snare single ply drum.”
Our basic single ply drum model: 5x14 curly maple with 2.3 mm steel hoops, piccolo strainer, Gretsch style lugs, brass 20 strand snares. $500
If you have any images or info pertaining to the drums that Joe, Evan and I have built. Please contact me about including it in this history. thanks, George Lawrence.